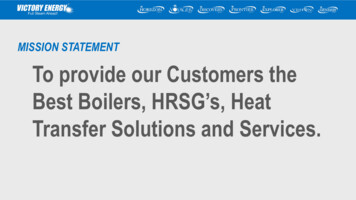
Transcription
MISSION STATEMENTTo provide our Customers theBest Boilers, HRSG’s, HeatTransfer Solutions and Services.
212 PRINCIPLEAt 211 degrees, water is hot.At 212 degrees, it boils.And with boiling water, comes steam.And with steam, we power the progress of change.The power of one extra degree.
COMPANY OVERVIEW Two Locations:- Collinsville, OK- Cushing, OK 200 Employees
IT TAKES ALL KINDSWithout question, ourgreatest asset is ourPEOPLE.They are the meaningfuldifference between goodand great.
COLLINSVILLE FACILITY
CUSHING FACILITY
CONCEPT TO COMPLETION SalesProject stallation / Start-UpAfter-market Services
WORLD CLASS CUSTOMERSUniversity ofColorado
MANUFACTURING
FACILITY EXPANSION 35,000 square foot expansion New height of 41 feet Second dedicated rail spurfor easy access toexisting rail line Significant upgradesto manufacturingequipment
FACILITY EXPANSION – CNC HORIZONTAL BORING MILL
FACILITY EXPANSION – CNC HORIZONTAL BORING MILL Featuring laser alignmentcapability which bringsunprecedented precisionto the drilling process
FACILITY EXPANSION – STEAM TEST FACILITY 6,500 SquareFeet WaterPurificationSystem Control Room EmissionTesting
LEAN PRACTICES5S Manufacturing1 . SORT2. STRAIGHTEN3. SHINE4. STANDARDIZE5. SUSTAIN
VERTICAL INTEGRATIONVictory Energy isequipped to designand manufacture thelargest and highestpressure shells inthe industry.
VERTICAL INTEGRATIONState-of-the-artautomated cuttingprocess for industrialgrade materials.
VERTICAL INTEGRATIONState-of-the-art CNCHigh DefinitionPlasma-arc cutting.
VERTICAL INTEGRATIONState-of-the-art multi-bendtube bending station.
VERTICAL INTEGRATIONIndustrial size plate rollingcells at both facilities.
VERTICAL INTEGRATIONState-of-the-art automatedtube to membrane weldingstation.
VERTICAL INTEGRATIONSub-arc welding cellfor industrial-size vesselfabrication.
VERTICAL INTEGRATIONOrbital TIG weldingincreases efficiencies andconsistent qualityof welds.
QUALITY CONTROLEach project is trackedand managed by an ITP(Inspection Test Plan). More than 100 checkpoints are in placefor quality assurance.
QUALITY CONTROL AWS Certified WeldingInspectors Level II Certified NDETechnicians Weld maps Pre-flight check list
PRODUCTSAND SERVICES
PRODUCTS AND SERVICESHeat Recovery SteamGenerators (HRSGs)Waste Heat BoilersO-style PackagedWatertube BoilersD-style packagedWatertube Boilers
PRODUCTS AND SERVICESWet-BackFiretube BoilersDry-BackFiretube BoilersLow NOx BurnersEconomizers
PRODUCTS AND SERVICESEnhanced HeatRecoveryHigh TemperatureFluid Generators
STANDARD Robust furnace design Membrane designeliminates by-passingof furnace gas
STANDARD Minimum tube wallthickness far exceedsASME requirements.
STANDARD Membrane headerwalls design Improves circulation Eliminates refractory Minimizes complextube bends
STANDARD Insulated drum headsare assembled withceramic insulation andcovered with carbonsteel.
STANDARD Gas outlets are insulatedwith high density mineralwool for improvedefficiencies and safety
STANDARD Vibration-DampeningTrim Pipe Clamps Designed to reducevibration, noise andshock
STANDARD Over-size entrywaydoors allow easyaccess
STANDARD All units are shrinkwrapped with a heavyduty material forprotection duringtransport
BRANDS
Utility HRSG Modular design Multiple flow andpressure configurations Patented Technology
Utility HRSG Customengineering Shop assemblymaximized
HRSGAdvanced flow modelingis utilized to analyzetemperature profiles andflow distribution.
HRSGFin tubes beingTIG welded toheader assembly.
HRSGHarp assemblygoing throughQuality Controlexamination.
HRSGCompletedHRSG module.
HRSGModule leavingthe facility,ready for railshipment.
HRSGField erectionof modules.
HRSGHP and LPsteam drums
HRSG CROSSDRUMUpper DrumBeing Jigged
HRSG CROSSDRUMDowncomersexternal to the fluegas path
HRSG CROSSDRUMReady for ShrinkWrap
HRSG CROSS DRUM SYSTEM
HRSG CROSS DRUM SYSTEM
HRSG – Natural Circulation Vertical tube horizontal gas flow Steam capacityup to 200K PPH Steam pressure to 750 PSIG Duct burner firing to 1,700 F Option for Superheat
HRSG Patented Technology All welded design,no rolled tube joints Platen (header) design Compact footprint
HRSG O-Style Symmetrical Design Rolled tube joints Modular Design Compact Footprint
HRSG A-Style Symmetrical Design Rolled tube joints Modular Design Compact Footprint
HRSG A-Style Symmetrical Design Rolled tube joints Modular Design Compact Footprint
HRSG – WHB Solid Fuel Municipal SolidWaste (MSW)
Firetube HRSGCapacities range from 15 to700 PSIG design pressures.
O-style WatertubeBoiler assembly beginswith drums mounted in aproprietary JIG for precisealignment.
O-style Watertube Custom designsCapacities up to 500K PPHin a single unit.Pressures up to 2,000 PSIGModular designs
O-style Watertube Industry’s highest steamproduction efficiencies Quick ramp rates Easy to lift due to centralplacement of drums
O-style WatertubeHigh capacity, fullymembrane boilerreduces CO emissions.
O-style WatertubePackaged boilers comefactory installed withfuel efficient integralLow NOx burners.
O-style Watertube - Superheater
D-style Watertube Capacitiesrange from10K PPH to over 500KPPH in a single layout.
D-style Watertube Large furnace promoteslower emissions. Engineered for long-term reliability
D-style Watertube Pressures up to2,000 PSIG
D-style Watertube Modular & field-erectedsizes are available. Well suited for high-pressure superheatedsteam applications.
Elevated D-style Boiler Maximizes shop assembledcontent while minimizingfield labor costs. Multiple burnersconfiguration available.
Long Heavy Haul “D” boiler
Modularized Boiler Systems91. Furnace7. FD (Forced Draft) Fan2. Convection Bank8. Combustion AirPreheaterSteam Drum9. Stack4. Economizer5. Low NOx Burner6. Combustion Air Heater3. Elevated14328756
ModularizationInstalling completeBoiler system on apre-fabricated baseprior to shipment
ModularizationTwo System Designwith a common stack
Enhanced Heat RecoveryRectangular Economizer: Custom engineered forboiler sizes rangingfrom 100 BHP to greaterthan 500K PPH.
Enhanced Heat RecoveryAir Pre-heaters: Custom designed to fitplant layout Flue gas temperaturesup to 1,750 F
Enhanced Heat RecoveryWaste heat recovery: Inlet gas temperaturesup to 2,000 F Well suited for powergeneration applications
Enhanced Heat Recovery ROI expectedwithin monthsnot years. Decreasefuel usage.
VEO
GENESISHigh TemperatureFluid Generators Custom engineered to heatthermal oil, glycol-watermixture or water with outputranging from 5 MMbtu/hr to200 MMbtu/hr
GENESISHigh TemperatureFluid Generators
END-MARKETSOLUTIONS
Rental Boiler FleetTrailer-mounted boilers range from 20K PPH to 150K PPH.
Rental Boiler FleetOperatingpressures rangefrom 100 PSIGto 750 PSIG.
Rental Boiler FleetQuick-release“Drop-n-Go”delivery system.
Mobile Water Treatment SystemsPre-piped,pre-wired andready to roll.
Victory Energy is equipped to design and manufacture the largest and highest pressure shells in the industry. VERTICAL INTEGRATION . State-of-the-art automated cutting process for industrial grade materials. . boiler