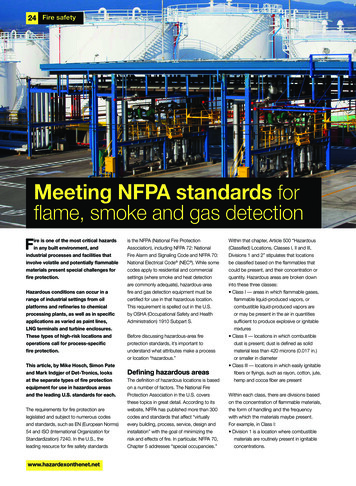
Transcription
24 Fire safetyMeeting NFPA standards forflame, smoke and gas detectionFire is one of the most critical hazardsin any built environment, andindustrial processes and facilities thatinvolve volatile and potentially flammablematerials present special challenges forfire protection.Hazardous conditions can occur in arange of industrial settings from oilplatforms and refineries to chemicalprocessing plants, as well as in specificapplications as varied as paint lines,LNG terminals and turbine enclosures.These types of high-risk locations andoperations call for process-specificfire protection.This article, by Mike Hosch, Simon Pateand Mark Indgjer of Det-Tronics, looksat the separate types of fire protectionequipment for use in hazardous areasand the leading U.S. standards for each.The requirements for fire protection arelegislated and subject to numerous codesand standards, such as EN (European Norms)54 and ISO (International Organization forStandardization) 7240. In the U.S., theleading resource for fire safety standardswww.hazardexonthenet.netis the NFPA (National Fire ProtectionAssociation), including NFPA 72: NationalFire Alarm and Signaling Code and NFPA 70:National Electrical Code (NEC ). While somecodes apply to residential and commercialsettings (where smoke and heat detectionare commonly adequate), hazardous-areafire and gas detection equipment must becertified for use in that hazardous location.This requirement is spelled out in the U.S.by OSHA (Occupational Safety and HealthAdministration) 1910 Subpart S.Before discussing hazardous-area fireprotection standards, it’s important tounderstand what attributes make a processor location “hazardous.”Defining hazardous areasThe definition of hazardous locations is basedon a number of factors. The National FireProtection Association in the U.S. coversthese topics in great detail. According to itswebsite, NFPA has published more than 300codes and standards that affect “virtuallyevery building, process, service, design andinstallation” with the goal of minimizing therisk and effects of fire. In particular, NFPA 70,Chapter 5 addresses “special occupancies.”Within that chapter, Article 500 “Hazardous(Classified) Locations, Classes I, II and III,Divisions 1 and 2” stipulates that locationsbe classified based on the flammables thatcould be present, and their concentration orquantity. Hazardous areas are broken downinto these three classes: Class I — areas in which flammable gases,flammable liquid-produced vapors, orcombustible liquid-produced vapors areor may be present in the air in quantitiessufficient to produce explosive or ignitablemixtures Class II — locations in which combustibledust is present; dust is defined as solidmaterial less than 420 microns (0.017 in.)or smaller in diameter Class III — locations in which easily ignitablefibers or flyings, such as rayon, cotton, jute,hemp and cocoa fiber are presentWithin each class, there are divisions basedon the concentration of flammable materials,the form of handling and the frequencywith which the materials maybe present.For example, in Class I: Division 1 is a location where combustiblematerials are routinely present in ignitableconcentrations.
Fire safety 25 Division 2 is one in which the samematerials are handled, processed, or used,but in which the materials are normallyconfined and can escape only in caseof accident or breakdown or failure of3. Ignition source (i.e., heat) — which,depending on the fuel and conditions,can be as minimal as the spark of anelectric switch or electric motor, or ahot surfaceventilation equipment.Within Class I, locations are also defined byzones (0, 1 or 2) per Article 505 of NFPA 70.For example, in a Class I, Zone 0 location,ignitable concentrations of flammable gasesor vapors are present continuously or for longperiods of time.How to control fire risk inhazardous areasIn order to control fire risk, it’s important tounderstand the components needed for afire to start. Commonly referred to as the “firetriangle,” the essential elements are:1. Oxygen — which can be a constituent oroutcome of various industrial processes,though its primary source is the ambient air2. Fuel — which is present in structures andused in processes of all kinds, but is ofgreater concern in locations defined ashazardousTo control the risk of fire, one of theelements of the fire triangle must beeliminated. When possible, flammablematerials must be contained andkept away from oxygen, as well asignition sources such as sparks or hotsurfaces. The primary goal should becontainment of the fuel source, i.e.,preventing leakage. The next step is toeliminate or minimize the risk of ignition.Because oxygen is ever-present in theatmosphere, it is difficult to eliminatethis element from the fire triangle.Success in containing or reducing theconcentration of fuel determines theDivision level of a hazardous area. Anyhazardous area, by definition, has somedegree of risk due to the presence offlammable materials at combustiblelevels.Controlling ignition riskfrom equipmentMany industrial locations in which hazardousmaterials may be present are also areaswhere electronic and electrical equipmentcould provide sources of ignition. It istherefore necessary to control ignitionsources, e.g., heat, arcing or sparking. Ifelectrical equipment (including flame and gasdetectors) must be located in a hazardousarea, per NFPA they must be designedto limit or isolate potential sources ofignition. NFPA 70 Section 500.7 “ProtectionTechniques” lists several techniques forprotecting electrical and electronic equipmentused in hazardous (classified) locations. Thethree acceptable protection methods forClass I Division 1 are: Explosion Proof (XP) — sparks orexplosions are contained within thehousing Purged and Pressurized — combustiblegases and vapors are denied entry into theenclosure Intrinsically Safe (IS) — the entire power ofthe system is limitedIn addition to limiting electrical energy as anignition source, the surface temperature ofelectrical equipment must also be controlled.Equipment is marked (T1 – T6) to show theenvironment for which it has been evaluatedand is considered suitableWhat makes up a fireprotection systemFire triangleA fire protection system is comprised of severalsubsystems that can include, but are notlimited to: flame, smoke and gas detection;notification and/or suppression activation;and a controller that receives the inputs fromthe detection devices, makes decisions andinitiates appropriate action or actions.www.hazardexonthenet.net
26 Fire safetyThere is no single solution for fire detectionin hazardous areas. Effective protection isbased on the materials and fuels present, theprocesses involved, the environment, andother control measures present. Based onthese variables, an effective detection andsuppression system may require multipletechnologies to effectively detect the hazards.Regardless of the application, many NFPAcodes and standards for specific processesreference NFPA 72, National Fire Alarm andSignaling Code, including: NFPA 15 Standard for Water SprayFixed Systems for Fire Protection —“The selection, location and spacing ofautomatic fire detectors for the actuationof fixed water spray systems shall meetor exceed the application requirements ofNFPA 72.“ NFPA 30 Flammable and CombustibleLiquids Code references numerous NFPAcodes, including NFPA 15, which in turnreferences NFPA 72. NFPA 59A Standard for the Production,Storage, and Handling of Liquefied NaturalGas (LNG) says, “.the detection systemshall be designed, installed and maintainedin accordance with NFPA 72 National FireAlarm Code.” NFPA 70 National Electrical Code hasmultiple references to NFPA 72. NFPA 409 Standard on Aircraft Hangarssays, “Listed detection systems shallwww.hazardexonthenet.netbe acceptable in lieu of heat detection ifapproved by the authority having jurisdictionand installed in accordance with NFPA 72.”Chapter 17 of NFPA 72 is titled “InitiatingDevices” and it provides requirements for theuse of various types of detectors — radiantenergy-sensing (flame) smoke and gas — thatcan be used to discover or recognize potentialindications of fire. Below is an overview ofeach detector type and some of the NFPAstandards applicable to each.Flame detectorsNFPA 72 describes a flame detector as “aradiant energy-sensing fire detector thatdetects the radiant energy emitted by aflame.” Flame detectors are line-of-sightdevices that can employ several sensingtechnologies: ultraviolet (UV), infrared (IR),ultraviolet/infrared (UV/IR) and multi-spectruminfrared (MSIR).Radiant energy-sensing detectors areincorporated into hazardous-area fireprotection systems particularly when eitheror both of two factors are present in theapplication: 1) when rapid-fire detection andactuation response times are critical; and 2)when the impact of false alarms is potentiallydisastrous in terms of damage, downtimeor both. Flame detectors used in hazardousareas must be hazardous-location-rated andperformance-certified.There are many factors to consider whenselecting the type, quantity, location, andspacing of flame detectors, including: Matching the spectral response of thedetector to the spectral emissions of the fireor fires to be detected. Minimizing the possibility of spuriousnuisance alarms from non-fire sourcesinherent to the hazard area.NFPA 72 addresses these selection factors inChapter 17: 17.8.3.2.1 The location and spacing ofdetectors shall be the result of an engineeringevaluation that includes the following:1) Size of the fire that is to be detected2) Fuel involved3) Sensitivity of the detector4) Field of view (FOV) of the detector5) Distance between the fire and the detector6) Radiant energy absorption of theatmosphere7) Presence of extraneous sources of radiantemissions8) Purpose of the detection system9) Response time requiredSmoke detectorsA smoke detector detects the particlesproduced by combustion using a varietyof technologies. These can includeionization, cloud chamber, photoelectric lightobscuration, photoelectric light scattering andvideo image detection. To be effective, smoke
Fire safety 27detectors should be located and spacedin anticipation of airflow from sources likelyto present fire risks, but without resulting inunwarranted alarms. NFPA 72 describes therequirement this way:gas detection technology to use, and theplacement of the devices. Combining varioustechnologies and placing them in locationsthat maximize their effectiveness can mitigatethe impact of a hazard.requirements for ensuring fire andgas detection systems are designed,implemented, operated and maintainedto provide the required Safety IntegrityLevel (SIL) for specific hazardous events.Resources1. NFPA 70 National Electrical Codewww.nfpa.org/702. NFPA 72 National Fire Alarm and SignalingExample of disposition of different types of gas detection within a plant 17.7.1.9 The location of smoke detectorsshall be based on an evaluation of potentialambient sources of smoke, moisture, dust,or fumes, and electrical or mechanicalinfluences, to minimize nuisance alarms.Combustible gas detectorsNFPA 72 describes a gas detector as“a device that detects the presence of aspecified gas concentration.” Detectors areintended for specific types of gas or vapor andshould be chosen accordingly, as specified inNFPA 72: 17.10.2.4 The selection and placement ofthe gas detectors shall be based on anengineering evaluation.Gas leak detection technologies can include: Acoustic detection for gas leaks —ultrasonic sensors detect leaks based onnoise patterns Infrared detection along a line of sight —detects gas along a path providing a largearea of detection Point detection of a combustible or toxicgas by electrochemical, catalytic, or infraredtechnologies — gases come into contactwith the detector, causing the detector toactivateA challenge related to gas detection is thatthe origin of gas leaks can often be difficultto predict. Gas leak detection can also bechallenging due to varying environmentalconditions such as wind and rain, andapplication factors such as machinery andpiping. These environmental and situationalfactors, as well as the many potentialsources of gas leaks, play major roles inselecting the type(s) of combustible and toxicFire protection system controllerA safety system controller (SSC) receivesand interprets input from multiple detectorsand makes executive decisions regardingnotification and further activity includingsuppression. While the primary function ofdetectors is to detect a hazard and thensignal to alert that an event has occurred, itis also essential that detectors are capableof maximizing false alarm rejection – so theydo not alarm to non-hazardous events, suchas arc welding. NFPA 72 defines a nuisancealarm this way: “An unwanted activation of asignaling system or an alarm initiating devicein response to a stimulus or condition thatis not the result of a potentially hazardouscondition. In some cases, in order to preventnuisance alarms, the SSC may discountinformation from a single detector if it is notconfirmed by other detectors in the area.As is the case for individual detectors, theSSC, if installed in a hazardous location, mustbe rated for the location. Alternatively, the SSCcan be located outside the hazardous location.Beyond NFPAWhile the NFPA standards are both wideranging and very detailed, they do notaddress detector performance. Otherstandards organizations or NationallyRecognized Testing Laboratories (NRTLs)have metrological standards that supportthe NFPA, such as Factory Mutual (FM) 3010for fire alarm systems and UnderwritersLaboratories (UL) 864.In addition, the International ElectrotechnicalCommission (IEC) 61508 defines theCode www.nfpa.org/723. International Electrotechnical Commissionwww.iec.ch/functionalsafety/4. Factory Mutualwww.fmapprovals.com5. European Normswww.cen.eu6. ISO 7240 Fire detection and alarm systemswww.iso.org7. UL Standards (Underwriters Laboratories)ulstandards.ul.comNFPA 70 , National Electrical Code andNEC are registered trademarks of theNational Fire Protection Association, Quincy,Mass., USA.About the authorsSimon J. Pate is Key Account Managerfor the LNG market at Det-Tronics.Simon has broad experience in theoil and gas industry, having workedin process automation and functionalsafety at EPCs, end users andmanufacturers. He received his BEng(Hons) degree from Kingston University.Michael J. Hosch is the FlameDetection Product Line Manager andhas worked with optical flame detectionfor Det-Tronics for over 25 years.Mark Indgjer joined Det-Tronics as anApplication Engineer in 2017. Prior tojoining Det-Tronics, he held a variety ofroles in his 25 years in the fire industry.www.hazardexonthenet.net
Reprinted with the permission of HazardEx, published by IML Group PLC, online at www.hazardexonthenet.netCorporate Office6901 West 110th StreetMinneapolis, MN 55438 USAwww.det-tronics.com 2018 Detector Electronics Corporation. All rights reserved.AR 1123 January 2018Phone: 952.946.6491Toll-free: 800.765.3473Fax: 952.829.8750det-tronics@det-tronics.com
Alarm Code." NFPA 70 National Electrical Code has multiple references to NFPA 72. NFPA 409 Standard on Aircraft Hangars says, "Listed detection systems shall be acceptable in lieu of heat detection if approved by the authority having jurisdiction and installed in accordance with NFPA 72." Chapter 17 of NFPA 72 is titled "Initiating