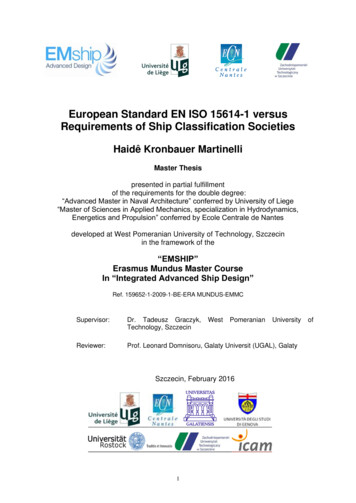
Transcription
European Standard EN ISO 15614-1 versusRequirements of Ship Classification SocietiesHaidê Kronbauer MartinelliMaster Thesispresented in partial fulfillmentof the requirements for the double degree:“Advanced Master in Naval Architecture” conferred by University of Liege“Master of Sciences in Applied Mechanics, specialization in Hydrodynamics,Energetics and Propulsion” conferred by Ecole Centrale de Nantesdeveloped at West Pomeranian University of Technology, Szczecinin the framework of the“EMSHIP”Erasmus Mundus Master CourseIn “Integrated Advanced Ship Design”Ref. 159652-1-2009-1-BE-ERA MUNDUS-EMMCSupervisor:Dr. Tadeusz Graczyk,Technology, SzczecinWestPomeranianReviewer:Prof. Leonard Domnisoru, Galaty Universit (UGAL), GalatySzczecin, February 20161Universityof
P2Haidê Kronbauer MartinelliCONTENTSABSTRACT . 101.INTRODUCTION . 112.LITERATURE REVIEW . 132.1.Classification Societies . 132.2.Welding Procedure Qualifications. 142.2.1.Welding Procedure Specification (WPS) . 162.2.2.Welding Procedure Qualification Record (WPQR) . 182.3.Welding Process . 182.3.1.2.4.Flux Cored Arc Welding (FCAW) . 19Welding Tests . 202.4.1.Non Destructive Test (NDT) . 212.4.1.1.Visual Inspection (VT) . 212.4.1.2.Penetrant Testing (PT) . 222.4.1.3.Magnetic Particle Testing (MT). 232.4.1.4.Radiography Testing (RT) . 242.4.1.5.Ultrasonic Testing (UT) . 272.4.2.Destructive Test (DT). 282.4.2.1.Tensile Test . 282.4.2.2.Impact Test. 292.4.2.3.Bend test. 302.4.2.4.Hardness Test . 322.4.2.5.Etching Test (Macro or micro examination) . 333. WELDING PROCEDURE SPECIFICATION AND WELDING PROCEDUREQUALIFICATION RECORDS ON PRACTICE . 353.1.DIN EN ISO 15614-1:2012-06: A Brief Rereading of the Standard . 363.1.1.Clause 1: Scope . 363.1.2.Clause 6: Test Piece . 363.1.3.Clause 7: Examination and Testing . 383.1.4.Clause 8: Range of Qualification . 453.1.5.Clause 9: Welding Procedure Qualification Record (WPQR) . 523.2.Welding Procedure Qualification Records: The Applied Sample . 53Master Thesis developed at West Pomeranian University of Technology, Szczecin
European Standard EN ISO 15614-1 versus Requirements of Ship Classification Societies3.3.4.3Welding Procedure Specification: The developed Document . 54ANALYSES OF RESULTS . 564.1.Shape and Dimensions of Test Pieces . 564.2.Extend of Testing. 584.3.Location and taking of test specimens . 604.4.Range of Qualification – Related to Material Thickness . 625.CONCLUSIONS AND DISCUSSIONS . 646.ACKNOWLEDGMENTS . 667.REFERENCES . 67APPENDIXES . 69“EMSHIP” Erasmus Mundus Master Course, period of study September 2014 – February 2016
P4Haidê Kronbauer MartinelliLIST OF FIGURESFigure 1: Welding procedure qualification flowchart. Adapted from The BritishConstructional Steelwork Association Ltd. (2009) . 15Figure 2: Self-shielded flux cored arc welding and gas-shielded flux cored arc welding.Available from Hobart Institute of Welding Technology (2012). . 20Figure 3: Optical instruments to visual inspection. Available from Halmshaw (1996). . 22Figure 4: Penetrant testing procedure. Adapted from Canadian Welding Bureau. (2006) . 23Figure 5: Magnetic particle test indicating longitudinal crack in weld. Available fromHalmshaw (1996) . 24Figure 6: Weld with porosity defect. Adapted from Jeffus. (2012) . 25Figure 7: Weld with transverse crack. Adapted from Jeffus. (2012) . 25Figure 8: Weld with tungsten inclusion. Adapted from Jeffus. (2012) . 25Figure 9: Detection of planar discontinuities at various orientations by radiography. Availablefrom American Welding Society. (2009) . 26Figure 10: Basic principle of ultrasonic flaw detection. Available from Halmshaw (1996). . 28Figure 11: Tensile test specimen before and after machined to perform reduced tensile test.Available from Hobart Institute of Welding Technology (2010) . 29Figure 12: Charpy V-notch test specimen. Available from Hobart Institute of WeldingTechnology (2010) . 30Figure 13: Bend test sample specimen. Available from Hobart Institute of WeldingTechnology (2010) . 31Figure 14: Hardness test. Available from Hughes (2009). . 32Figure 15: Etched welding surface specimen. Available from Hobart Institute of WeldingTechnology (2010) . 33Figure 16: Test piece for a butt joint in plate with full penetration. Available from DIN ENISO 15614-1:2012-06 . 38Figure 17: Location of test specimens for a butt joint in plate. Available from DIN EN ISO15614-1:2012-06 . 40Figure 18: EN ISO 15614-1 vs DNVGL: Test piece dimensions comparison. . 57Figure 19: BV vs ABS: Location and taking of test specimens. . 57Figure 20: EN ISO 15614-1 vs DNVGL: Location and taking of test specimens. . 60Figure 21: BV vs ABS: Location and taking of test specimens. . 61Master Thesis developed at West Pomeranian University of Technology, Szczecin
European Standard EN ISO 15614-1 versus Requirements of Ship Classification Societies5LIST OF TABLESTable 1: Examination and testing of the test pieces. Adaptation from DIN EN ISO 156141:2012-06 . 39Table 2: Permitted maximum hardness values (HV 10). Available from DIN EN ISO 156141. (2012) . 44Table 3: Range of qualification for steel groups and sub-groups. Available from DIN EN ISO15614-1. (2012) . 47Table 4: Range of qualification for butt welds material thickness and weld deposit thickness.Available from DIN EN ISO 15614-1. (2012) . 48Table 5: Comparison table related to dimensions of test pieces. . 58Table 6: Comparison table related to extent of testing of non-destructive test. . 58Table 7: Comparison table related to extent of testing of destructive test. . 59Table 8: EN ISO 15614-1 vs requirements of ship classification societies: range ofqualification related to material thickness. . 62“EMSHIP” Erasmus Mundus Master Course, period of study September 2014 – February 2016
P6Haidê Kronbauer MartinelliABBREVIATIONSABSAmerican Bureau of ShippingACAlternating currentAWSAmerican Welding SocietyBVBureau VeritasCWBCanadian Welding BureauDCDirect currentDNVDet Norske VeritasDNVGLOrganization under joint between Det Norske Veritas and GermanischerLloydDTDestructive testFCAWFlux cored arc weldingGLGermanischer LloydGMAWGas metal arc weldingHAZHeat affected zoneHBBrinell hardness test unitHRRockwell hardness test unitHVVickers hardness test unitJ-L045Pipe fixed at 45 degrees downwards welding positionMTMagnetic particle testingNDENon-destructive examinationNDTNon-destructive testPCHorizontal welding positionPFVertical upwards progression welding positionPGVertical downwards progression welding positionPTPenetrant testingpWPSPreliminary welding procedure specificationRTRadiography testingSAWSubmerged arc weldingSMAWShield metal arc weldingUTUltrasonic testingMaster Thesis developed at West Pomeranian University of Technology, Szczecin
European Standard EN ISO 15614-1 versus Requirements of Ship Classification Societies7Impact testing specimen type – Charpy V-notch in heat affected zoneVHTthrough the thicknessVTVisual testingVWTImpact testing specimen type – Charpy V-notch in weld metal through thethicknessWPQRWelding procedure qualification recordsWPSWelding procedure specification“EMSHIP” Erasmus Mundus Master Course, period of study September 2014 – February 2016
P8Haidê Kronbauer MartinelliDeclaration of AuthorshipI declare that this thesis and the work presented in it are my own and have been generated byme as the result of my own original research.Where I have consulted the published work of others, this is always clearly attributed.Where I have quoted from the work of others, the source is always given. With the exceptionof such quotations, this thesis is entirely my own work.I have acknowledged all main sources of help.Where the thesis is based on work done by myself jointly with others, I have made clearexactly what was done by others and what I have contributed myself.This thesis contains no material that has been submitted previously, in whole or in part, forthe award of any other academic degree or diploma.I cede copyright of the thesis in favour of the West Pomeranian University of Technology andUniversity of Liège.Date:SignatureMaster Thesis developed at West Pomeranian University of Technology, Szczecin
European Standard EN ISO 15614-1 versus Requirements of Ship Classification Societies9“Don t let your fear of the hazards keep your ship in the harbor. Cast off your lines and sailaway.”Gail Lynne Goodwin“EMSHIP” Erasmus Mundus Master Course, period of study September 2014 – February 2016
P 10Haidê Kronbauer MartinelliABSTRACTThe shipbuilding industry, from its inception to the present day, had evolved, and followingthe needs of the industry, classification societies were founded. They, as non-governmentalorganization, regulate the fabrication of new ships or offshore structures based on their ownestablished codes, rules and standards. As, nowadays, the most widely used joining techniqueon shipbuilding activities is welding, these welded joints must be certified and ensured thataccomplish the quality expected and allow repeatability for the specified materi
European Standard EN ISO 15614-1 versus Requirements of Ship Classification Societies 5 “EMSHIP” Erasmus Mundus Master Course, period of study September 2014 – February 2016 LIST OF TABLES Table 1: Examination and testing of the test pieces. Adaptation from DIN EN ISO 15614-Author: Haide Kronbauer MartinelliPublish Year: 2016