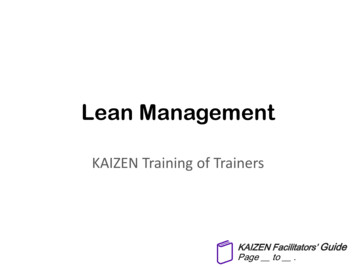
Transcription
Lean ManagementKAIZEN Training of TrainersKAIZEN Facilitators’ GuidePage to .
Objectives of the sessionAt the end of the session, trainees are able to:1) Understand the philosophy on leanmanagement2) Describe the relation between 5S-KAIZENand Lean management3) Describe what is lean tools4) Describe the importance of thinking andacting in lean management for health careimprovement in Tanzania1
Environment surroundinghealth services in TZ Although Tanzanian health sector has madesignificant progress over the last several years,there are many significant challenges that stillneed to be addressed, including:– Health resources (HRH, financial, commodities )shortage– Low quality of health services– Low reliability of the public health facilityHowever, we cannot stop providinghealth services to the community2
What should we do forimprovement of the situation?3
Think “out of box” andbreak through4
Answer is “Lean Management”5
What is the difference betweenKaizen and Lean?KAIZENLean ManagementSix SigmaOriginJapanese TQC and ToyotaProduction systemmanagement philosophydeveloped from ToyotaProduction System (TPS)set of techniques and toolsfor process improvement.Developed by Motorola in1986.DefinitionA problem solving process.focuses on eliminating waste,improving productivity, andachieving sustained continualimprovement in targetedactivities and processes of anorganization.focused on improvingprocess speed and qualitythrough reduction ofprocess wastes.a disciplined, data-drivenapproach andmethodology foreliminating defectsProgram/activitiesdriven byBottom to top(Bottom up approach)Top to bottom(Top down approach)Top to bottom(Top down approach)ImplementationstructureSmall group activities (QCcircle / QIT / WIT)Lean TeamsBlack, Green, Yellow beltsTools used for theapproachUse QC 7 tools and New QC7 toolsLean Tools (5S, Kanban,Andon, JIT, TPM, etc.)DMAIC, StatisticalapproachDeveloped/Conceptualized byMasaaki Imai and ToyotaMotorsWomack, Jones and Roos, Bill Smith at MotorolaMITProblem-Solving and SelfDirected Work Teams are themost common types6
Two ways communication andimprove organizationKAIZEN approachFrom bottom to topWorkers should havepositive mindset, andtrying to makeworkplace andservices better(“KAIZEN mind”)Lean ManagementFrom top to bottomManagers need toknow“Lean management”to guide workers forImprovement of workflow and productivity7
What is “Lean thinking”?Basic concept for Lean management A business methodology which aims to provide anew way to think about how to organize humanactivities to deliver more benefits to society andvalue to individuals while eliminating waste.Simple definition is:“Becoming ‘lean’ is a process of eliminatingwaste with the goal of creating value.”8
How can we eliminate “wastes”?Different types of waste in your organization9
7 types of wastes in work placeOverproductionOverprocessingProcessingbeyond thestandardCreating morematerial or informationor tests or treatmentthan neededInventoryMore material orinformation thanneededWaitingReworkPeople or itemsthat wait for awork cycle to becompletedRepetition orcorrection of ocessesMotionUnnecessarymovement with aprocess10
“Muri”, “Mura”, adsMudaAny forms ofWaste in theprocessAny activity asking unreasonable stress or effort from personnel,material or equipment. In short: OVERBURDENFor people, Muri means: a too heavy mental- or physical burden.For machinery Muri means: expecting a machine to do more thanit is capable of- or has been designed to do.Any variation leading to unbalanced situations. In short:UNEVENNESS, inconsistent, irregular.Mura exists when workflow is out of balance and workload isinconsistent and not incompliance with the standard.any activity in your process that does not add value. MUDA is notcreating value for the customer. In short: WASTEType I muda: Non-value-added tasks which seam to be essential.Business conditions need to be changed to eliminate this type ofwaste.Type II muda: Non-value-added tasks which can be eliminatedimmediately.11
What should be used forelimination of wastes?12
Lean Principles5. PursuitPerfectionStrive for perfection by continuallyremoving successive layers of waste4. EstablishPull system1. DefineValueOnly make what is pulledby the customer just-in-timeSpecify what creates valuefrom the customers perspectiveLeanPrinciples3. CreateFlowMake those actionsthat create value flow2. Map ValueStreamIdentify all steps acrossthe whole value stream13
Lean PrinciplesMental Model for lean thinkingLean PrinciplesWhat should be done1)Define ValueDefine value from a patient’s perspective.Try to understand their health and non-healthexpectations. How patients’ experience could beimproved.2)Map Value StreamEvaluate how all the steps of a process orprocedure to provide services in the healthfacility. Then, eliminate any steps that do notcontribute to performance, productivity or safetyof the health facility.3)Create FlowEliminate waste between steps of a process andcreate smooth workflow for high efficiency4)Establish Pull systemAllow the patient to receive or request services ifand when need.5)Pursuit PerfectionContinuously adapt to an ever-changingenvironment and patients’ needs in order todeliver high quality of health services.14
An example of Define ValueLong waiting timefor consultancy?Good communicationand explanation oftreatment?15
An example of map value stream“Process of seen patients at OPD”Registration ofpatientsEnteringInformation intoHMSLookingforpatientfile fromshelfHandoverthe file tothepatientAskingthepatient togo andwait atOPDMeasurevital signof thepatientAre all the steps necessary ?Are there any steps can be eliminated or change for better?16
An example of create “flow”Process of seen patients at OPDRegistration ofpatientsEnteringInformation intoHMSLookingforpatientfile fromshelfHandoverthe file tothepatientAskingthepatient togo andwait atOPDMeasurevital signof thepatientRegistration can be divided into 2 lanes:1) Registration of new patients, and2) Registration of returning patients for smooth registration17
How can we apply LeanPrinciples?18
Use “Lean Tools” Lean tools are essential for accelerating thepractice of lean management. There are over 50 lean tools that organizationcan adopt for lean management Lean tools can be selected based on thecharacteristic of organization and servicesprovided It is important to know how to use each leantoolPossible to obtain lots of lean tools 19
Patient focusedEliminatewasteSimplifyeverythingCreate flowContinuous improvementPull system(Kanban)Quick –set upJust In TimeMistake-Proofing(Poka-yoke)Point of use storageBatch size reductionStandardized workTakt TimeProblem solving process(KAIZEN process)Total ProductiveMaintenanceVisual controlStopping the line5S approachValue Stream MappingWorkplace layoutLean toolsNote that tools in the blue box are taught in 5S training20
Wrap up: Lean processIdentify theproblems,needs andexpectationsof patientsReview thecurrentsituation andprocess of theservicesprovidedTry toeliminatewastes andunnecessaryprocedurewith lean toolsEstablishmechanism of“Pull system”(demanddriven)Try to improvethe situationcontinuouslyand maintainhigh quality ofservices21
Lean management and 5S-KAIZEN-TQM ApproachHighly Reliable Organization sitive mindsetfor improvementof quality amongfrontline workersWastesLeadership andcommitment ofhospitalmanagementLeadership and team workLean ManagementQuality of services andmanagementTotal Quality Management22
Achieve “Lean” with “KAIZEN”Continues Quality Improvement and open quality spiralconcepts achieve “Lean management”23
Thank you for listening !any question?
Lean Tools (5S, Kanban, Andon, JIT, TPM, etc.) DMAIC, Statistical approach . Developed/Concept ualized by Masaaki Imai and Toyota Motors; Womack, Jones and Roos, MIT . Bill Smith at Motorola. 6 . Two ways communication and improve organization. KAIZEN approach From bottom to top . Lean Management . From top to bottom . Managers need to know “Lean management” to guide workers