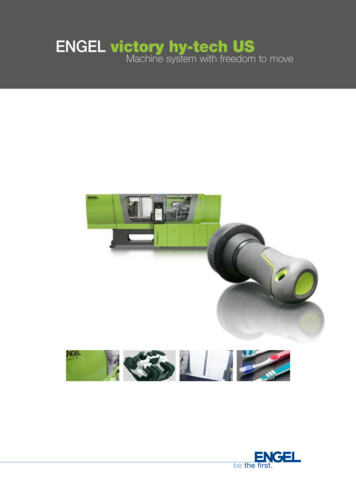
Transcription
ENGEL victory hy-tech USMachine system with freedom to movebe the first.
Multi-color applications I Page 24Customized solutions I Page 26Automation I Page 22Tie-bar-less I Page 4Control unit I Page 20Clamping unit I Page 12Injection unit I Page 14Machine series I Page 8Drive technology I Page 163ENGEL victory hy-tech US
Machine systems withSpace4 ENGEL victory hy-tech USSpace in every sense of the word.No tie-bars. Maximum scope.The unique tie-bar-less technologyof the ENGEL victory improvesefficiency and economy in injectionmolding production.5ENGEL victory hy-tech US
ENGEL victory– a success story in figuresmore than.25 years10,000 satisfied customersTie-bar-less.Flexible. ENGEL.60,000 machines on the marketMold dimensions – unbeatableImproved use of the barrier-free mold space. Large molds or bulkycorepulls. The generously designed mold fixing platens can be usedright up to their limits – and often beyond.Machine availability – excellentFaster mold changes thanks to shorter tooling times – also for talland bulky molds. Less maintenance overhead thanks to a robust,low-friction design.Automation – ideal conditionsFast part take-off, smaller plant footprint, lower shop heights due tofree access to the mold area for robots and handling equipment.Minimum mold wearUnrivalled platen parallelism guaranteed by the patented ENGEL FlexLink system and the factory standard platen parallelism setting.Outstanding energy efficiencyLow friction and closing pressure lock-in ensure low energy consumption. And the ENGEL ecodrive raises energy efficiency to a newlevel hitherto only achieved by fully electric machines.6 ENGEL victory hy-tech USProduction with machines whichare one or two clamping forceclasses smallerThe mold size, rather than the maximumclamping force, is often the key to optimizingmachine design. An exact calculation of therequired clamping force pays off. The tie-bar-lessmachine has a smaller footprint and requires lessinvestment costs, particularly with: Technical parts and thick-wallinjection moldingWith its tie-bar-less benefits, the ENGEL victory isthe optimum machine for technical and thick-walledparts.Molds with multiple cavitiesNon-full-surface molded partsFoammelt applicationsMulti-color applications7ENGEL victory hy-tech US
Tie-bar-less. Modular. ENGEL.The versatile ENGEL victory machine series.The construction kit for cost-effective injection molding production.The tie-bar-less ENGEL victory covers the clamping force range from 280 to 5000 kN. In fact, the rangeof appli cations is considerably broader, as the molded part to be produced is not limited by the clampingforce but by the platen size. Large mold fixing platens and the wide delivery chute of the ENGEL victoryguarantee low machine investments, because with the ENGEL victory a machine with a lower clamping force will do the job just as well. Particularly when using large and bulky molds, substantially lowerinvestments are required for machines.ENGEL victory6015ENGEL victory 30 US280 kNENGEL victory 45 US400 kNENGEL victory 55 US500 kNENGEL victory 65 US600 kNENGEL victory 75 US700 kNENGEL victory 85 US800 kNENGEL victory 100 US900 kNENGEL victory 120 US1100 kNENGEL victory 130 US1200 kNENGEL victory 160 US1400 kNENGEL victory 180 US1600 kNENGEL victory 200 US1800 kNENGEL victory 220 US2000 kNENGEL victory 240 US2200 kNENGEL victory 290 US2600 kNENGEL victory 340 US3000 kNENGEL victory 400 US3500 kNENGEL victory 450 US4000 kNENGEL victory 500 US4500 kNENGEL victory 560 US5000 kNENGEL victory hy-tech8 ENGEL victory hy-tech US18200202530330353035ENGEL victory hy-spex & 9055501058090705010590105 120Subject to change!9ENGEL victory hy-tech US
ENGEL victory hy-spexthe flexible tie-bar-less machine with perfect ergonomics selected machine modelssequential machine movementsefficient ENGEL ecodrive systema variety of practical optionssmart ENGEL CC300 machine controlsoptimal price/performance ratioPerfectly complementing the ENGEL victory hy-techand ENGEL victory combi. Special process technologies or applications also necessitate specialequipment on the injection molding machine. Standard machines become custom machines.ENGEL victory hy-techrubberScrew injection unit adapted to rubber processingthe die versatile tie-bar-less machine that leaves no wishes opencomprehensive range of modelsefficient ENGEL ecodrive systemcomprehensive range of optionsperfect for individual solutionssmart ENGEL CC300 machine controlsENGEL victory combithe compact tie-bar-less machine for multi-color applications additional compact injection units (W, V and L positions) flexible layout plenty of room for a rotary table or index plate increased mold installation height optional rotary table (hydraulic or servo-electric) efficient ENGEL ecodrive system (standard from 290 tons) comprehensive range of options perfect for individual solutions smart ENGEL CC300 machine control units10 ENGEL victory hy-tech USLIMEquipment package for liquid silicone processing,with a screw or barrel injection unit depending onthe application.ENGEL technology modules HTVPlasticizing unit and process software for processingsolid silicone. Stuffing device optionally available.HARD PVCEquipment package and plasticizing unit for processing hard PVC.duroplastPlasticizing unit and process software for processing duroplast.cleanroomAdaptation of the complete machine in several s tages for production under clean room conditions.foammeltEquipment package and plasticizing unit for preparation for parts production with micro-foam structure.gasmeltGas injection technology for creating cavities inmolded parts.watermeltWater-injection technology for creating cavities inmolded parts.11ENGEL victory hy-tech US
High-precision mold parallelism[The most innovative clamping unitof the past decades.]With the tie-bar-less ENGEL -victory, platen parallelism –and thus mold wear – is not left to the individual components‘ sum total of production tolerances. Each tie-barless clamping unit is precisely set prior to delivery usingthe standard, highly sensitive platen parallelism setting.Later adjustment is possible, of course, thus guaranteeing a long service life of the machine and the molds.During clamping force build-up the platen parallelismautomatically adjusts to mold parallelism. This unique benefitis ensured by the patented Flex-Link system.Heavy moldsHeavy molds are no problem for the tie-bar-lessclamping unit. The high-precision platen parallelism isadequately ensured by the pre-tension of the patentedFlex-Link system and support through the solidC frame. And thanks to the use of additional guide shoesto support the moving mold half, the mold weight can beincreased almost without limits.Ergonomic operationThe ENGEL tie-bar-less- technology allows easy access andergonomic working within the mold area. All necessary operations like cleaning or spraying can be done comfortablyfrom every angle.Large mold dimensionsThe standard version of the ENGEL victory tie-bar-lessclamping unit already offers greater freedom for the moldthan other clamping units. Wider mold fixing platens andgreater platen spacing are available as options if necessary. This allows the mold area to be adapted to match thenext biggest size without changing the clamping force.Outstanding energy efficiencyWhen it comes to saving resources, the tie-bar-less concept possesses clear advantages: in particular, the bearing-mounted precision guide rails, the absence of tie-barfriction, and the clamping force lock-in increase energy efficiency significantly. The extra bonus: the hydraulicENGEL ecodrive as standard equipment means that youwill achieve the maximum energy savings with everyENGEL victory machine.13ENGEL victory hy-tech US
Excellent injection process controlThe hydraulic ENGEL injection units score extra pointswith reliable control of the injection molding process.Compared with common injection controllers, the„clamped system“ of the injection pistons in connectionwith the highly sensitive eletronic controllers, respondsextremely quickly to disturbances and any processdriven changes of the injection process. This ensures excellent mold part quality and reproductionaccuracy.As a further optimization for very low injectionspeeds, a servo-valve is available as an optionalextra (included in the factury standard with the ecodriveoption).Accumulator for high injectionperformanceExtremely thin-walled parts need very high injectionspeeds to achieve the required molded part quality. Therequired injection performance is provided by optionalhydraulic accumulators. The injection process is controlled by a servovalve.More efficient plasticizing driveHigh injection performance and excellent process stability.HydraulicENGEL injection unit14 ENGEL victory hy-tech USThe plasticizing drive is powered by a hydro-motor.These hydro-motors are available in three sizes for eachinjection unit. Besides the standard hydro-motor, amotor for higher speeds or higher torques is availableas an option in each case. This means that the drivecan be adapted to match the plasticizing unit and theinjected material to be processed, thus ensuring goodenergy efficiency. With the right choice of hydraulicvariant, the plasticizing drive can be operated parallel tothe mold movements.Matching plasticizing unitTo adapt plasticizing perfectly with the applicationin question, various barrels and screw types are available. The barrel is mounted on the injection unit via aquick-release coupling.The plasticizing unit is pressed torque-free againstthe mold, whereby the required force is set on themachine control unit.15ENGEL victory hy-tech US
Drive unit.Energy efficiency.Efficient ENGEL hydraulics. Control of all machine movements:fast, reproducible and energy-efficientENGEL is a pioneer in energy-efficient hydraulic concepts.Even more important than efficiency of the hydraulic drivecomponents is the basic hydraulic concept of an injection molding machine. Since the introduction of the tie-bar-less injectionmolding machine ENGEL has had a concept that guaranteesin itself very low energy requirements for the central hydraulicsystem of the respective machine.Besides the highly energy efficient basic concept of themachine, ENGEL has relied for many years on particularlyefficient hydraulic drive units. When the PQ hydraulics werereplaced more than 20 years ago by the modern EHV hydraulics, ENGEL already set standards in terms of energy efficiencyand control quality.And thanks to the new servohydraulic ecodrive, ENGELnow combines the benefits of hydraulics with the benefits of servodrives. ENGEL ecodrive offers additionallyenhanced control accuracy, and is - above all - a further milestone in energy efficiency.Flexibility thanks to modularhydraulic variantsHydraulic variablecapacity pumpEnergy consumptionFixed displacementpumpPQElectric variable capacity pumpFixed displacement pump ServomotorEHVENGEL ecodriveWhether easily de-molded parts with a low shotweight, or complex molds with parallel motion, oruse cases that require high injection performance, asophisticated hydraulics variant is available forevery requirements profile.„Lock-in“ closing pressureAll movements and pressures for the individualmachine movements are, of course, regulatedhydraulically. But where it makes sense – whenholding the clamping force and the nozzle contactforce – the required pressure is upheld hydraulically,thus reducing the pressure holding energy to zero.With increasing cycle time, the energy savingsgrow to a sustantial level. S ingle pump system for sequential movements. pump systems for parallel movements. More powerful drives for improved injection andplasticizing performance Accumulators for extremely high injection performance ENGEL ecodrive for maximum energy efficiencyEvolution of hydraulic drive technology16 ENGEL victory hy-tech US17ENGEL victory hy-tech US
The "new" hydraulics - ENGEL ecodriveUp to 70% energy savings compared to conventional hydraulic drive systemsUp to 100% cooling water savings for the oil coolerENGEL ecodrive - a revolutionary hydraulic concept with decisive advantages: Excellent energy efficiency Extremely low noise level Optimum for clean room applications On-board hydraulics for operating core-pullsNo or substantially lower cooling water requirements"On-board" hydraulicsENGEL ecodrive offers all the prerequisites forenergy-efficient and space-saving productionwith hydraulic core pulls. For parallel movementsof the ejector, core pulls, nozzle, and plasticizingecodrive can also have two completely independentdrive units.ENGEL ecodrive reduces energy losses to such ahigh extent that – with the exception of high performance applications – only minimal heating of the hydraulic oil occurs. Cooling water consumption at theoil cooler is reduced to a minimum, in many casesto zero.The "noiseless" machine.The elimination of permanently running hydraulicpumps considerably reduces noise emissions.PUKonstantPumpeReduction in energy dissipationENGEL ecodrive boosts energy efficiency byradically reducing the energy losses common toconventional hydraulic machines. The portion ofsupplied energy that is not applied as movementenergy for individual machine movements istransformed into heat. The majority of this heat istransferred to the hydraulic oil and via the standardoil cooler to the external cooling water processingplant.Ideal for clean room applicationsThe ENGEL victory is extremely suitable for cleanrooms alone due to the tie-bar-less technology andelimination of friction. An additional advantage isoffered by the ENGEL ecodrive. The servomotorsused do not have motor cooling fans, and thus thereis no air turbulence resulting in a higher particleconcentration.ServoControllerMSUOil temperature indicator of energy efficiencyENGEL ecodrive: The system.The ecodrive system in the ENGEL victory consists of aservomotor with fixed displacement pump (insteadof a permanently running asynchronous motor withvariable capacity pump). Energy efficiency depends onvarious criteria, of which two should be highlighted here:No control valvesEach control valve causes energy losses due to thepressure differential. The ENGEL ecodrive controlsspeed and pressure without control valves, whichproduces considerable efficiency gains. Thespeed is controlled via the fixed displacement pumpspeed without additional pressure and energy loss.A unique feature is the closed loop pressure control bymeans of completely new control algorithms directly via18 ENGEL victory hy-tech USthe speed of the pump and no longer via a pressurecontrol valve.Drive standstill when operations stopWhen at a standstill, the ENGEL ecodrive eliminatesidling and purging energy consumption as occursin conventional hydraulic systems. An idle pumpconsumes no energy. This is substantially supported by the energy-efficient machine concept (e.g.clamp pressure lock-in).19ENGEL victory hy-tech US
Intuitive. ENGEL. Operation.The control unit of the ENGEL victory is the perfect interfacebetween operator and machine. Besides the clearcut designof the basic functions, the CC300 also impresses with otherelements that make it easier for the user to meet the requirementsplaced on injection molding production today.Machine and robotsequences at a glanceQuality monitoringThe freely configurable machine sequence supportssimple, individual configuration of sequences throughout the injection molding cycle. Complex programsequences including robots can be easily andreliably visualized and edited.A wide range of modules for monitoring the quality of injection molded parts are available in standardversions and as optional extras. Both the directgraphic monitoring of all key parameters of theinjection molding process and the recording andstatistical evaluation of the same are displayed in asimple and clear manner.The machine sequence can be set up in advanceon the PC with the supplied ‚virtual machine‘. Fastermold changes, less risk of mold damage, andoptimum training options for the operator are the majorbenefits here.This data can also be centrally collated andevaluated via an interface to external productionplanning and monitoring systems.Energy efficiency withENGEL ecographThe standard ENGEL victory control unit incorporatesENGEL ecograph, an energy analysis tool. This toolenables the operator to check the machine‘s energyconsumption and to optimise the energy efficiencyof the injection molding sequence.20 ENGEL victory hy-tech US21ENGEL victory hy-tech US
Robot. Freedom. ENGEL.The injection molding machine is in many cases only one element of the overall, oftencomplex production cell. Robots and automation components perform a wide range oftasks.They range from insert-placing and take-off actions at the injection mold, including mounting and checkingoperations, to packaging of the finished product. The aspect of cost-effectiveness is usually founded in the overall concept and not its individual components. And it is precisely here that the ENGEL victory offers decisiveadvantages in the overall solution thanks to its tie-bar-less benefits.Smaller footprintIntegrated automationAutomation solutions by ENGELBecause there are no tie-bars in the way, the robotcan move in and out of the mold horizontally whenthe safety gate is open. The automation can thusoften be built closer to the machine, which savesspace.Tie-bar-less machine technology is an ideal prerequisite for machine-integrated automation. The robot always moves within a slightly widened machine safetygate. After short horizontal movements it places theparts onto a conveyor belt directly adjacent to themold fixing platens. Smaller footprints, lower systemheights, smaller robot sizes and the elimination of additional safety guarding for each robot secure lowerinvestment costs and better utilization of the shop floorspace.It goes without saying that ENGEL also supplies automation solutions, true to the motto of „Everything from asingle source“. The ENGEL viper and ENGEL ER-USProbot series are ideal for use in combination with theENGEL victory. Preconfigured automation packagesare available for simple take-off tasks. The ability tocontrol operation using the machine control unit offersspecial benefits. In particular, the creation of a commonmold data set brings substantial benefits to the user.Low ceiling heightProduction can take place without problems and riskof collision in low halls or beneath crane runways,because the robot does not need to move out of themold in an upward direction.Shorter production cycleThe cycle time is shortened due to the direct, horizontal in- and outward movements of the robot,particularly in the case of complex automation.Sprue take-offThe ENGEL victory offers optimum conditions for reliable and fast sprue take-off by the sprue picker.Sprue ejection chutes are available as an option forthe non-operator side safety gate.Robot simple to operateThe new wizard for the robot, and integration with themachine control unit, make this possible!22 ENGEL victory hy-tech US23ENGEL victory hy-tech US
Multi-colors. Combimelt. ENGEL.Market leader and pioneer in multi-color injection molding.ENGEL combimeltInjection unit in „L“ positionMolds for multi-color applications needrelatively little clamping force compared to themold size. This is due to the fact that the sumtotal of the projected area of the cavities istypically relatively small.The right combination of unitsfor each applicationInjection unit in „V“ positionIt is here in particular that the generously designedand barrier-free mold area offers added flexibility in machine design and mold changing. Takingtie-bar-less technology into consideration isparticularly important as early as the concept phaseof a project. This can save time and money.The right technology for everypartInjection unit in „W“ (piggyback) position24 ENGEL victory hy-tech USWhen large shot weights, a small footprint, lowsystem heights or full freedom for automation arecalled for, ENGEL combimelt is the right solutionfor every application. .The ENGEL victory optimally supports all multicolor mold concepts: rotary tables, index plates,slide technology, co-injection or transfer of partsby a robot.25ENGEL victory hy-tech US
Requirements. Solutions. ENGEL.ENGEL has the optimum solution for every requirement. And, above all,the flexibility of the tie-bar-less ENGEL victory series leaves nothing to bedesired.It is the perfect machine for the majority oftechnical parts, thick-wall injection moldingand many standard applications. The extensivestandard features and wide range of options areyour guarantee. Furthermore, our experiencedENGEL technicians are committed on a dailybasis to the satisfaction of special customerrequirements.26 ENGEL victory hy-tech US27ENGEL victory hy-tech US
ENGEL victory hy-tech US en/2-2015ENGEL victory hy-tech USENGEL AUSTRIA GmbH A-4311 Schwertberg tel: 43 (0)50 620 0 fax: 43 (0)50 620 3009e-mail: sales@engel.at www.engelglobal.combe the first.
ENGEL victory hy-tech ENGEL victory hy-spex & hy-tech Subject to change! Tie-bar-less. Modular. ENGEL. The versatile ENGEL victory machine series. The construction kit for cost-effective injection molding production. The tie-bar-less ENGEL victory covers the clamping force range from 280 to 5000 kN. In fact, the range