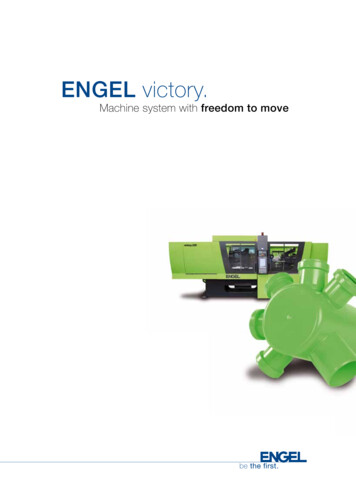
Transcription
ENGEL victory.Machine system with freedom to movebe the first.1
Automation I Page 22Control unit I Page 20Tie-bar-less I Page 4Injection unit I Page 14Clamping unit I Page 12Machine series I Page 8Drive technology I Page 16Multi-colour applications I Page 24Customised solutions I Page 2623
Machine system with lots ofSpaceFreedom in every respect.No tie-bars. Lots of space. The unique tie-bar-less technology of the ENGEL victoryimproves efficiency and economy in injection moulding production.45
Tie-bar-less. Flexible. ENGEL.ENGEL victoryAutomation – ideal conditions Faster part take-off, smaller footprint and lower ceiling heights thanks to free access to the mouldarea for robots and automation equipment.Machine availability – excellent Faster mould changing due to shorter set-up times – even for high and bulky moulds.Lower maintenance costs due to robust, low-friction design.Mould dimensions – unbeatable Better utilisation of the barrier-free mould area.Large moulds or bulky core pulls. The generously dimensioned mould fixing platens can be used tothe limit – and often beyond.successThe infiguresmore than. 20 years . 10,000 satisfied customers . 55,000 machines on the marketProduction with machines which are one or two clamping forceclasses smallerThe mould size and not the maximum clamping force is often the keyto optimum machine dimensioning. An exact calculation of the requiredclamping force pays off. The tie-bar-less machine has a smaller footprint andrequires less investment costs, particularly with:6Minimum mould wearOutstanding energy efficiencyThe patented ENGEL Flex-Link system and standard platen parallelism setting ensure unbeatable platen parallelism.Low friction, closing pressure lock-in and electrohydraulic variable capacity pumps ensure low energy consumption. And the optional drive system,the ENGEL ecodrive, raises energy efficiency toa new level hitherto only achieved by fully electricmachines. Moulds with multiple cavities Non-full-surface moulded parts Multiple colour applicationsTechnical parts and thick-wall injection mouldingWith its tie-bar-less advantages the ENGEL victory is the optimum machine fortechnical and thick-walled parts.7
Tie-bar-less. Modular. ENGEL.The tie-bar-less ENGEL victory covers the clamping force range from 280 to 5000kN. In fact, the range of applications is considerably broader, as the moulded part to be produced is not limited by the clamping force but by the platen size.Large mould fixing platens and the wide delivery chute of the ENGEL victory guarantee low machine investments, because with the ENGEL victory a machine witha lower clamping force will do the job just as well. Particularly when using large andbulky moulds, substantially lower investments are required for machines.The versatile ENGEL victory machine series. The construction kit forcost-effective injection moulding production.ENGEL victory8018ENGEL victory 2830 US280 kNENGEL victory 4045 US400 kNENGEL victory 5055 US500 kNENGEL victory 6065 US600 kNENGEL victory 7075 US700 kNENGEL victory 8085 US800 kNENGEL victory 90100 US900 kN1100 kNENGEL victory 110120 USENGEL victory 120130 US1200 kNENGEL victory 140160 US1400 kNENGEL victory 160180 US1600 kNENGEL victory 180200 US1800 kNENGEL victory 200220 US2000 kNENGEL victory 220240 US2200 kNENGEL victory 260285 US2600 kNENGEL victory 300330 US3000 kNENGEL victory 350400 US3500 kNENGEL victory 400440 US4000 kNENGEL victory 450500 US4500 kNENGEL victory 500550 US5000 kN22200252530 9080905550105 80907050105 90105 120Subject to change!ENGEL victory tech8ENGEL victory spex & tech9
ENGEL victory spex The special series to mark the 20th anniversaryof tie-bar-less machines. Selected models Sequential machine movements EHV hydraulics (alternatively ENGEL ecodrive) Practice-oriented option pool ENGEL CC 200 control unit Best price/performance ratioENGEL technology modulesThe optimum supplement to the ENGEL victory tech and ENGEL victory combi.Special process technologies or applications also call for special equipment on injection mouldingmachines. Making special machines from standard machines.ENGEL victory tech The tie-bar-less machine for all applications. Extensive range of models Wide range of EHV hydraulic versions(alternatively ENGEL ecodrive) Comprehensive range of options,including customised solutions ENGEL CC 200 control unitrubberScrew injection unit adapted to rubberprocessingENGEL victory combi The optimum machine for multi-colour applications Additional compact injection units in W, V and L position High degree of flexibility and plenty of space fora rotary table or index plate Increased mould installation height Rotary table optionally with hydraulic orservo-electric drive unit Wide range of EHV hydraulic versions(alternatively ENGEL ecodrive) Comprehensive range of options, includingcustomised solutions ENGEL CC 200 control unit10LIMEquipment package for liquid siliconeprocessing, depending on the case in question with screw or plunger injection unit.cleanroomAdaptation of the complete machine in several stages for production under clean roomconditions.foammeltEquipment package and plasticizing unit forpreparation for parts production with microfoam structure.HTVPlasticizing unit and process software forprocessing solid silicone. Stuffing unit optionally available.gasmeltGas injection technology for creating cavitiesin moulded parts.HART-PVCEquipment package and plasticizing unit forprocessing hard PVC.watermeltWater injection technology for creating cavities in moulded parts.duroplastPlasticizing unit and process software forprocessing Duroplast.11
The most innovative clamping unitof the past decades.A symbiosis of flexibility, precision and customer orientation.High-precision mould parallelismPlaten parallelism – and thus mould wear – in thetie-bar-less ENGEL victory is not left to the sum ofmanufacturing tolerances of the single components.Each tie-bar-less clamping unit is precisely set priorto delivery using the standard, highly sensitive platenparallelism setting. Subsequent fine adjustment is,of course, possible and guarantees a long servicelife of machine and moulds. During clamping forcebuild-up the platen parallelism automatically adjuststo mould parallelism. This unique advantage is implemented through the patented Flex-Link system.Heavy moulds[]Heavy moulds are no problem for the tie-bar-lessclamping unit. The high-precision platen parallelism isadequately ensured by the pre-tension of the patented Flex-Link system and support through the massive C frame. And by using additional guide shoes tosupport the movable mould halves, mould weightcan be increased virtually without limit.Large mould dimensionsThe standard version of the ENGEL victory tie-barless clamping unit already offers greater freedom forthe mould than other clamping units. Wider mould fixing platens and greater platen spacing are availableas options if necessary. The mould area can thus beset to the next size with the same clamping force.Outstanding energy efficiencyThe basic concept of the tie-bar-less machine already guarantees maximum energy savings. In particularly the bearing-mounted precision guide rails, theabsence of tie-bar friction and the closing pressurelock-in significantly increase energy-efficiency. A widerange of configurations for energy saving are possible in combination with different hydraulic drivesfrom EHV to ecodrive.1213
Excellent injection process controlEfficient plasticizing driveThe hydraulic ENGEL injection units score extra pointswith reliable control of the injection moulding process.Compared to conventional injection controllers, the„clamped system“ of injection plungers included in thestandard version with the highly sensitive electronic controllers reacts extremely quickly to disturbing influencesand any process-related changes. This guaranteesexcellent injection moulded parts and a high degree of reproduction accuracy. Control accuracy iseven further improved by the electro-hydraulic variablecapacity pumps included in the standard version.The plasticizing drive is powered by a hydro-motor. These hydro-motors are available in three sizes for each injection unit. Besides the standard hydro-motor, a motorfor higher speeds or higher torques is available as anoption in each case. This enables the drive unit to betuned with the respective plasticizing unit and mouldingmaterial to be processed, guaranteeing a high levelof energy efficiency. With the selection of the corresponding hydraulic versions, the plasticizing drive canbe operated parallel to the mould movements.A servo-valve is available as an option (standard featurein the ecodrive option) for further optimisation of extremely low injection speeds.Accumulator for high injection performanceExtremely high injection speeds of up to 600 mm/sare necessary to achieve the required quality of mouldedparts with extremely thin walls. The required injectionperformance is provided by optional hydraulic accumulators. The injection process is controlled by a servo-valve.Tuned plasticizing unitA range of barrel and screw configurations is availablefor optimal tuning of plasticizing with the respective application. The barrel is mounted on the injectionunit by means of a quick coupling.The plasticizing unit is pressed torque-free against themould; the required force can be set on the machinecontrol unit.Hydraulic ENGEL injection unitHigh injection performance and excellent process stability.1415
Drive unit.Energy efficiency.Efficient ENGEL hydraulics Control of all machine movements:fast, reproducible and energy-efficientENGEL is a pioneer in energy-efficient hydraulic concepts. Even more important than efficiency ofthe hydraulic drive components is the basic hydraulic concept of an injection moulding machine. Sincethe introduction of the tie-bar-less injection moulding machine ENGEL has had a concept that guarantees in itself very low energy requirements for the central hydraulic system of the respective machine.Besides the particularly energy-efficient basic machine concept, for many years ENGEL has also beencommitted to highly efficient hydraulic drive units. ENGEL already set the standard in energy efficiencyand control quality over 15 years ago with the replacement of PQ hydraulics by smart pump hydraulics(EHV). And with the new optional ecodrive servohydraulics ENGEL is now combining the advantagesof hydraulics with those of servodrives. ecodrive offers even better control accuracy and, most ofall, sets a new milestone in energy efficiency.Smart pump hydraulics (EHV)ENGEL standard hydraulics are based on electro-hydraulic variable capacity pumps. Compared to an old PQ variable capacitypump, an EHV variable capacity pump offers not only a higherlevel of efficiency of the pump itself, it requires no additional flowcontrol valve for closed loop speed control. The closed loopspeed control is activated directly in the pump with a higher degree of accuracy and without the usual pressure or energy loss.This results in energy savings of approx. 20%.Flexibility through modular hydraulic variations.Electricvariable capacitypumpFixed displacementpump Single – pump units for sequential movements. Double – pump units for parallel movements. Stronger drive units for increased injection and meteringperformance Accumulators for extremely high injection performance ENGEL ecodrive for maximum energy efficiencyEfficiencyFixed displacement Hydraulicpumpvariable capacitypump„Lock-in“ closing pressurePQEHVENGEL ecodriveEvolution of hydraulic drive technology16Whether easily removed moulded parts with a low shot weight,complex moulds with parallel movements or high injectionspeeds are required. A sophisticated hydraulic version isavailable for every requirement profile.All movements and pressures for the individual machine movements are, of course, closed-loop regulated hydraulically. Butwhere it makes sense – holding clamping and nozzle contactforce – the required pressure is hydraulically maintained and thusthe holding energy is reduced to zero. With increasing cycletime, the energy savings grow to a respectable level.17
Drive unit. Milestone. ENGEL.The „new“ hydraulics - ENGEL ecodriveUp to 70% energy savings compared to conventional hydraulic machines.Up to 100% cooling water savings for the oil cooler of theOil temperatureENGEL ecodrive - a revolutionary hydraulic concept with decisive advantages:Excellent energy efficiencySubstantially lower cooling water requirementsExtremely low noise levelOptimum for clean room applicationsIncludes „on-board“ hydraulics for operating core pullsindicatorenergy efficiencyof hydraulic machinesENGEL ecodrive. The system:ENGEL ecodrive in the ENGEL victory consists of a servomotor with fixed displacement pump (instead of a permanently running asynchronous motor with variable capacity pump). Energy efficiency depends on various criteria,of which two should be highlighted here:Energy efficiencyIdeal for clean room applicationsNo control valves in the central drive unit forspeed and pressure controlecodrive boosts energy efficiency by radical reduction of the energy dissipation common to conventional hydraulic machines. The portion of supplied energy that is not applied as movement energy for individualmachine movements is transformed into heat. The majority of this heat is transferred to the hydraulic oil and via theoil cooler to the external cooling water processing plant.The ENGEL victory is extremely suitable for clean roomsalone due to the tie-bar-less technology and eliminationof friction. An additional advantage is offered by ecodrive.The servomotors used do not have motor cooling fans,and thus there is no air turbulence resulting in a higherparticle concentration.Each control valve causes energy losses due to the pre
Hydraulic ENGEL injection unit High injection performance and excellent process stability. 16 17 ENGEL is a pioneer in energy-efficient hydraulic concepts. Even more important than efficiency of the hydraulic drive components is the basic hydraulic concept of an injection moulding machine. Since the introduction of the tie-bar-less injection moulding machine ENGEL has had a concept that guaran .