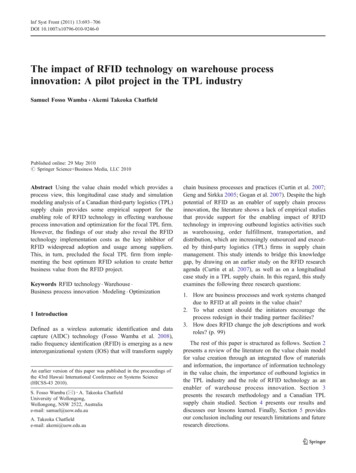
Transcription
Inf Syst Front (2011) 13:693–706DOI 10.1007/s10796-010-9246-0The impact of RFID technology on warehouse processinnovation: A pilot project in the TPL industrySamuel Fosso Wamba & Akemi Takeoka ChatfieldPublished online: 29 May 2010# Springer Science Business Media, LLC 2010Abstract Using the value chain model which provides aprocess view, this longitudinal case study and simulationmodeling analysis of a Canadian third-party logistics (TPL)supply chain provides some empirical support for theenabling role of RFID technology in effecting warehouseprocess innovation and optimization for the focal TPL firm.However, the findings of our study also reveal the RFIDtechnology implementation costs as the key inhibitor ofRFID widespread adoption and usage among suppliers.This, in turn, precluded the focal TPL firm from implementing the best optimum RFID solution to create betterbusiness value from the RFID project.Keywords RFID technology . Warehouse .Business process innovation . Modeling . Optimization1 IntroductionDefined as a wireless automatic identification and datacapture (AIDC) technology (Fosso Wamba et al. 2008),radio frequency identification (RFID) is emerging as a newinterorganizational system (IOS) that will transform supplyAn earlier version of this paper was published in the proceedings ofthe 43rd Hawaii International Conference on Systems Science(HICSS-43 2010).S. Fosso Wamba (*) : A. Takeoka ChatfieldUniversity of Wollongong,Wollongong, NSW 2522, Australiae-mail: samuel@uow.edu.auA. Takeoka Chatfielde-mail: akemi@uow.edu.auchain business processes and practices (Curtin et al. 2007;Geng and Sirkka 2005; Gogan et al. 2007). Despite the highpotential of RFID as an enabler of supply chain processinnovation, the literature shows a lack of empirical studiesthat provide support for the enabling impact of RFIDtechnology in improving outbound logistics activities suchas warehousing, order fulfillment, transportation, anddistribution, which are increasingly outsourced and executed by third-party logistics (TPL) firms in supply chainmanagement. This study intends to bridge this knowledgegap, by drawing on an earlier study on the RFID researchagenda (Curtin et al. 2007), as well as on a longitudinalcase study in a TPL supply chain. In this regard, this studyexamines the following three research questions:1. How are business processes and work systems changeddue to RFID at all points in the value chain?2. To what extent should the initiators encourage theprocess redesign in their trading partner facilities?3. How does RFID change the job descriptions and workroles? (p. 99)The rest of this paper is structured as follows. Section 2presents a review of the literature on the value chain modelfor value creation through an integrated flow of materialsand information, the importance of information technologyin the value chain, the importance of outbound logistics inthe TPL industry and the role of RFID technology as anenabler of warehouse process innovation. Section 3presents the research methodology and a Canadian TPLsupply chain studied. Section 4 presents our results anddiscusses our lessons learned. Finally, Section 5 providesour conclusion including our research limitations and futureresearch directions.
694Inf Syst Front (2011) 13:693–7062 Background and context of the study2.1 The value chain modelThe value chain model was proposed by Michael Porter inhis book, Competitive advantage: Creating and sustainingsuperior performance, as a means to analyze and describeall activities conducted within a company to create thevalue and competitive advantage that will support itscompetitive position in the industry (Porter 1985). Themodel’s process view shows the existing task interdependency and implies that an integrated flow of materials andinformation is the key to value creation within theenterprise value chain.The model identifies five primary activities: inboundlogistics, operations, outbound logistics, marketing andsales, and service, as well as four supporting activities:corporate infrastructure (i.e., leadership), human resourcesmanagement (i.e., education and training), technologydevelopment (i.e., IT to support the value chain activities),and procurement (Fig. 1).The focus of our paper -warehousing- is an integralpart of Outbound Logistics, which performs essentialactivities such as inventory management, order fulfillmentand transportation that are required to get the finishedproduct -an output of Operations- to the end customers.Primary activities are thought to contribute directly to thecreation or delivery of a product or service, and hence tobusiness value creation, while secondary activities aremainly used to support and enhance effectiveness andefficiency of the primary activities (Porter 1985). To thefirm, the costs of realizing the product or service, and,therefore, profits, depend on the activities to be carried outwithin the value chain (Porter 1985). More importantly,realizing a profit margin and a competitive advantage willdepend on the level of optimization and coordination of allSupport activitiesCorporate Infrastructure (e.g. leadership)Human resources management (e.g. education & training)Technology development (e.g. RFID deployment)ProcurementServiceFig. 1 The value chain modelMarketing and SalesOutbound LogisticsOperationsInbound LogisticsKey activitiesinterdependent activities in the value chain (Porter 1985).In the literature, it is commonly assumed that the use ofnetwork information technologies, such as electronic datainterchange (EDI) and RFID, can help the firms achievethese value chain objectives. However, the literaturefails to provide empirical support for the commonly heldassumptions.2.2 The value chain model and information technologyThe value chain model is a useful tool that allows managersnot only to analyze, redesign intra- and inter-organizationalbusiness processes to improve firm efficiency and effectiveness (Papazoglou and Ribbers 2006), but also to understandhow Information Technology (IT) may affect the firm’scompetitiveness (Karakostas et al. 2005). To Porter (1985)“technology is embodied in every value activity in a firm,and technological change can affect competition through itsimpact on virtually any activity” (p. 166).Several ITs have been used to support value chainprimary and supporting activities and linkages with externalsuppliers and buyers. For example, e-commerce technologies are used as a means for integrating the value chain inorder to reduce costs and to respond more rapidly tochanges in an unstable market (Dedrick and Kraemer2005), to facilitate intra- and inter-organizational businessprocess reengineering, and thus improving informationsharing (Wu and Wu 2006), the coordination of decisionmaking (Asoo 2002), and enhancing the organization’scomparative efficiency (Johnston and Vitale 1988) andbenefits (Curtin et al. 2007). However, the level of ITadoption and usage within the value chain depends onvarious factors such as IT characteristics (e.g., technologicalcomplexity, relative advantage), firm characteristics (e.g.,firm size and readiness) and environmental characteristics(e.g., competitive pressure) (Rogers 1995; Zhu et al. 2006),the level of organizational change to leverage the ITcapabilities (Riggins and Mukhopadhyay 1994) and thelevel of intra- and inter-organizational business processesreengineering, standardization and alignment with the IT(Brousseau 1994; Riggins and Mukhopadhyay 1994).With regard to RFID technology, its characteristics, suchas multiple tags items reading, more data storage capability,and data read/write capabilities, and no line of sight, mayserve as facilitators of its widespread adoption and usage,while its perceived complexity and actual cost mayconstitute inhibitors (Fosso Wamba and Chatfield 2009).2.3 Outbound logistics and TPL industryA TPL service provision is defined as “a relationshipbetween a shipper and a third party which, compared withthe basic services, has more customized offerings, encom-
Inf Syst Front (2011) 13:693–706passes a broad number of service functions and ischaracterized by a long-term, more mutually beneficialrelationship” (p. 35) (Murphy and Poist 1998). Today theTPL industry appears as a viable solution to the marketglobalization, increased competition, cost pressures and anincreasing use of outsourcing (Power et al. 2007). Thegrowing importance of the TPL industry is highlighted bythe results of multiple survey studies. Langley et al. (2005)found that, among more than 1,500 logistics and supplychain executives, almost 82% of the respondents wereusing TPL services. Similarly, in a more recent study,Langley (2008) found that 70% of firms in North America,73% of firms in Europe, and 75% of firms in Asia Pacificwere using TPL services for their warehousing activities. Inaddition, TPL is increasingly considered as a strategic toolfor the IT-enabled supply chain to reduce environmentaluncertainty and improve logistics management efficiency.Indeed, IT capabilities play a vital role in achieving theintegration of logistics services provided by TPLs. Forexample, Langley (2008) found that 91% of TPL users willoutsource their web-enabled communications and visibilitytools, while 83% of them will do the same with regard towarehouse/distribution center management (p. 14). Finally,the TPL industry is considered as a lead user of RFIDtechnology (Gartner 2008).2.4 Warehousing processes and RFID technology potentialIn an economic context where the growing development ofinformation technologies has been generating unprecedented repercussions on the management of activities withinwarehouses, it goes without saying that the use of acentralized inventory management, for example, could leadto an increased productivity and short response times of thewarehousing systems, and that “shorter product life cycleswill impose a financial risk on high inventories and,therefore, on the purchase of capital intensive highperformance warehousing systems” (p. 519) (Van Den Bergand Zijm 1999).To categorize warehouses, there are three main perspectives to be considered: the processes, the resources, and theorganization (Rouwenhorst et al. 2000, p. 516). Theprocesses are the different steps through which a productwill pass through in the warehouse; they can be divided infour distinct phases: (i) the receiving process, which is thefirst step the products go through in a warehouse. Thisstage usually involve the checking and/or the repackagingof the products in the various storage units before they aremoved to the next process; (ii) the put-away process, whichconsists in moving and placing the products into theirspecific storage location so as to make it easy for thepicking clerk to retrieve them; (iii) the picking process,which involves the retrieval of the products from their695storage locations in order to consolidate a customer order.This process is considered as the most “labour-intensiveand costly activity for almost every warehouse” and couldaccount for up to 55% of the total warehouse operating cost(De Koster et al. 2007); (iv) the shipping process, whichinvolves the checking, packing and loading of the productsin the transportation unit in order to bring them to thecustomer facilities. The effectiveness and efficiency ofthese processes will heavily depend on both the bettermanagement of the interdependency between them, theavailable resources, and the organization of the warehouse.More precisely, the resources involve all means, that is,equipment such as the storage unit (e.g., pallets, boxes), thestorage system (e.g., simple shelves, automated systems,automated cranes or conveyors, pick equipment), a warehouse management system (WMS) (for control of theprocesses within the warehouse), a material handlingequipment to prepare the retrieved items (e.g., sortersystems), and the personnel needed to operate the warehouse. Finally, the warehouse organization involves all theplanning and control procedures that are used to run thesystem. For example, during the picking process, a routingpolicy may describe the sequence of retrievals and the roadto visit the retrieval locations within the warehouse(Rouwenhorst et al. 2000).Recently, researchers have increasingly demonstratedthat RFID could have important impacts on the fourwarehouse processes than any other technology. Forexample, Capone et al. (2004) argued that RFID technologycould reduce the put-away labor cost by 20 to 30% and thepicking labor cost by some 30 to 50%. Lefebvre et al.(2005), through a pilot study, also demonstrated that RFIDcould transform the warehouse processes—which may, inturn, facilitate collaboration practices in the supply chainsuch as collaborative planning, forecasting and replenishment and vendor managed inventory. In other words, RFIDtechnology may automate the verification activities involved in the shipping process, thus reducing potentialerrors. Fosso Wamba et al. (2006) argued that the impactsof RFID on the warehouse processes would facilitate an“intelligent supply chain management” through the emergence of the so-called “intelligent processes”—processesthat can be automatically triggered without any humanintervention. Finally, García et al. (2007) showed that RFIDenables the automatic input of receipt in the supply chainsystem during the receiving process, allowing real-timechecking of bin availability during the put-away andpicking processes and reduces the process time. Despitethe high potential of the RFID demonstrated in thesestudies, however, the literature is yet to provide real-worldlongitudinal studies to test these assumptions. The RFIDliterature shows that there is a knowledge gap to bridge andthat this research is urgently required.
696Inf Syst Front (2011) 13:693–7063 MethodologyThis paper is part of a larger study conducted in Canada toimprove our understanding of the impacts of integratingRFID technology in a TPL supply chain. A value chainperspective (Porter 1985) is adopted since RFID adoptionand usage is mainly product-driven (Bendavid et al. 2009)and involves the study of the impacts of RFID on theinterdependent activities related to the management oftelecommunications stationary batteries of a specific TPLsupply chain (Fig. 2).3.1 Research design and data collection methodsAs the main objective of this study is to improve ourtheoretical and practical understanding of the impact ofRFID technology in real-life contexts over a period of time,the appropriate research design requires a longitudinal casestudy. Eisenhardt (1989) defined the case study as “aresearch strategy which focuses on understanding thedynamics present within single settings” (p. 534). Thisresearch strategy allows to focus on emerging phenomenaand eventually induce theories (Benbasat et al. 1987). It isrecognized by many researchers as a suitable approach toanswer research questions such as “why” and “how” thingsare done (Yin 1994), and is therefore appropriate to studythe impact of RFID technology on the warehouse processesof a TPL industry, where research and theory are at theirearly and formative stages (Benbasat et al. 1987).A longitudinal case study was conducted betweenSeptember 2007 and April 2008 in a TPL supply chain,which consists of two main phases. In the first phase,which is to explore RFID technology opportunities, bothqualitative and quantitative data were collected throughmultiple sources such as several interviews, three focusgroups, multiple on-site observations, RFID workshops,organizational documents and RFID technical papers inorder to understand the dynamics within the supply chain.For example, on-site observations allowed us to mapexisting processes. Interviews with operational staff andmanagers on “how and why things are done?” providedmore comprehensive information that can help to solvepossible inaccuracies in our mapping. Furthermore, abusiness process modeling and analysis tool called “ARISTools”, which is based on the Event-driven Process Chains(EPC) formalism (Dreiling et al. 2006; Scheer et al. 2002),was used to understand, represent, and “map” the existingintra- and inter-organizational processes into a currentmodel (as-is). The modeling of the current processes,therefore, enables us to identify bottlenecks and areas ofopportunities when using RFID technology. Using thiscurrent model as a guide, we worked together with keystakeholders involved in the warehouse project to performan analysis of business and technological informationrequirements.In addition, the business process analysis tool was veryeffective in enabling the managers to make better decisionsabout the management of RFID-enabled business processes,by exploring and evaluating the impact of RFID on resourceutilization, IS integration, and information flows. The overallanalysis enabled us to generate various plausible scenariosfor business process innovation. These optimization scenarios were discussed with the stakeholders during RFIDworkshops. In fact, “ARIS Toolset” allows a globaldefinition, mapping, analysis, optimization and implementation of business processes. This formalism offers a logicrepresentation of activities in a network of multiple organizations through the alternative use of events, functions andconnectors to specify the routing logic based on the requireddecision rule (Dreiling et al. 2006) (Table 1).Fig. 2 TPL supply chainTPL firmSuppliersRemote sites(Focal firm)(s1, s2,., sn)(rs1, rs2,., rsn)(c1, c2, c3)ServiceServiceOnly informaton flowProduct flow and information flowEquipmentMinister ofInstallation firm ceivingServiceOperationsOutbound logisticsCustomersRecycling firm
Inf Syst Front (2011) 13:693–706Table 1 Elements of EPC model (Bevilacqua et al. 2009)ElementDescriptionAn “event” describes the situationEventbefore and/or after a function isexecuted, and may correspond to thepost-condition of one function and actas a pre-condition of another function.A function corresponds to an activity697In this project, the “Living Laboratory” was mainly used tosimulate the impact of RFID technology on intra- and interorganizational processes, intra- and inter-organizational ISintegration, and information flow between the key supplychain players. The simulation enabled them to consider, forexample, the best location in the supply chain where RFIDtagging should be done, the level of tagging (e.g., singlebattery vs. case of batteries), and the level of inter-firminformation sharing.Function(e.g., task and process step), which3.2 A Canadian TPL supply chainneeds to be executed.The “AND” connector allows (i) theflow of the process branches into twoor more parallel paths; and (ii) all theevents must occur in order to triggerthe following function.With the “OR” connector (i) one ormore paths may be followed as aresult of the decision; (ii) each event,or combination of events, will giverise to the function.With the “XOR” connector (i) one, andonly one, of the possible paths will befollowed; (ii) one, and only one, of thepossible events will give rise to thefunctionMoreover, the EPC formalism is considered as a viablemeans to study a collaborative e-business process (Hoyer etal. 2008), open source online shopping solutions (Saka2008), and more recently, the impacts of RFID technologyon supply chain-enabled business process transformation(Fosso Wamba and Bendavid 2008).In the second phase, two most plausible scenarios ofRFID-enabled supply chain were being chosen andassessed in the RFID solution provider laboratory throughthe “Living Laboratory” approach. In this approach a givenscenario is retained to be implemented and monitoredduring a pilot project in the focal firm warehouse. In fact,“Living Laboratory” approach was intended to supportdiverse research settings, including the simulation ofbusiness experiments and the use of the laboratory over aprolonged period by all key RFID project stakeholders for“self-trial” learning (Loeh 2005), joint problem solving,interaction, knowledge generation and exchange among allkey project stakeholders (Bergvall-Kareborn et al. 2009;Eriksson et al. 2007; Følstad 2008).The TPL supply chain studied in Canada is involved in themanagement of telecommunications stationary batteries(Fig. 2). The focal firm is a Canadian owned medium-sizeTPL service provider, with annual revenue of nearly US 23million and 52 full-time employees and owns a largedistribution centre in Canada and warehouse facilities in theUnited States of America (USA).The company provides a variety of services such asstorage, transport and customs clearance fees. Its Canadabased distribution centre, where the study was conducted, isused to store telecommunications batteries from varioussuppliers. The TPL has three major customers for this valuechain: a telecommunication company, a communicationprovider, and a utility company. The company is in chargeof (i) shipping new batteries to different customers’ remotesites based on their needs, (ii) collecting used batteries, and(iii) bringing them to the recycling plant. It relies on set of ITsystems to conduct its intra- and inter-organizational businessprocesses—which range from the very basic practices (e-mail,fax, and paper-based system) to the sophisticated ones (barcode systems, in-house warehouse management system,RFID-enabled transport management system, B2B Webportal). In addition, the firm often uses the Canadian postalservices to communicate with its supply chain stakeholders.Importantly, however, the firm primarily uses its paper basedsystem to track and trace batteries analyzed in this study.Nevertheless, the TLP firm is already using RFID technologyin other areas. Indeed, in 2005, the firm had its first experiencewith the RFID technology when it started providing a “Slap &Ship” RFID solution service to its customers in order to meetRFID mandates from their trading partners. Later in the sameyear, the firm started deploying a RFID-enabled trucktracking solution so as to have better visibility on its “truckin transit”. Therefore, this TPL organization can be considered as an early adopter of RFID technology. Indeed, in arecent study Langley (2008) found that only 13% of 3PLservice providers were using RFID technology. Furthermore,according to the management board of the TPL Company,the use of RFID technology as an enabler of telecommunications stationary batteries management is a “logical nextstep” in their IT innovation process for value creation.
698Inf Syst Front (2011) 13:693–7064 ResultsWe now present and discuss the results of the RFIDimplementation in relation to the TPL warehouse processinnovation and the future RFID-enabled warehouse optimization that is plausible, but has not been implementedlargely because of the lack of stakeholder investment.4.1 RFID-enabled warehouse process innovationThe first scenario of the RFID-enabled warehouse processinnovation (Section 4.1.1) required the RFID tagging ofproducts in the TPL warehouse. As for the next phase, itassumes that this tagging activity is conducted in eachsupplier’s facilities, and represents, from the TPL firmperspective, the best scenario of RFID adoption in the TPLsupply chain (Section 4.1.2). However, the suppliers wereunwilling to make the initial RFID investment required. Inconsequence, the best scenario for the warehouse processinnovation and radical transformation could not be chosenfor implementation. Instead, the second scenario forincremental change was implemented and monitored inthe pilot project at the TPL warehouse.4.1.1 Current RFID implementation focus: RFIDas enabler of incremental change on the pickingand shipping processes (s1)Figure 3 presents the current picking process (“as-is”),while Fig. 4 presents the incremental redesign process ofthe same process when using RFID technology (“to-be”).Figure 5 presents the current (“as-is”) shipping process andFig. 6 the incremental redesign of the shipping processintegrating RFID technology (“to-be”).p-Pick receivedPicking order sentusing email (e-Pick)Automaticallyreceive e-PickGo to thededicated rackfor pickingPicking order (e-Picking)Internetemail-InboxForkliftArrived at theracke-Pick receivedPick the quantityof battery on thep-PickManually openthe email-Inboxp-PickPicking-clerk-2Battery pickedPicking-clerk-1Email-InboxopenedStandard printerManually printthe e-Pick(p-Pick)p-PickMove loaded forklift tothe shipping stagingareaForkliftForklift moved to theshipping staging areap-Pick printedWMSGenerate the shippingmanifest s-ManifTake the p-PickS-Manif generatedp-Pick takenBring the p-Pickto the secondpicking clerkManually print thes-ManifS-Manif printedp-Pick broughtEnd of pickingPicking-clerk-2Receive thep-PickFig. 3 The current picking processStandard prints-Manif
Inf Syst Front (2011) 13:693–706699Fig. 4 The picking processwith incremental change whenusing RFIDPicking ordersent using email(e-Pick)InternetAutomaticallyreceive e-Picke-Pickingemail-Inboxe-Pick receivedManually openthe oxopenedNew activity when using RFIDStandard printerManually print thee-Pick (p-Pick)p-Pick printedTake the p-Pickand n-TagsPicking-clerk-1p-Pickp-Pickp-Pick takenBring the p-Pickto the secondpicking clerkn-b-Tagsp-Pick and n-TagbroughtEnd of pickingBased on the analysis of the current processes (“as-is”picking process in the Fig. 3 and “as-is” shipping processin Fig. 5) and on the incremental change when using RFID(“to-be” picking process in Fig. 4 and “to-be” shippingprocess Fig. 6), the following observations are made: (i)the picking process involves two human resources (HR)and the shipping process one human resource; (ii) themain activities of the HR in the picking process (Pickingclerk-1) include the processing of information (e.g.,manually print the picking order (e-Pick) that is used inthis process, while the second HR deals with physicalactivities in the process (e.g., Picking the quantity ofbattery on the p-Pick), and generates and prints themanifesto (s-Manif) marking the end of the process. This
700Inf Syst Front (2011) 13:693–706s-ManifDrive forklift throughTake the s-Manifthe shipping portalForkliftForklift drived throughS-Manif takenDrive the forklift toshipping portalForkliftPlace forklift into thetruckShipping clerkthe shipping stagingareaShipping clerkForklift drove to theForklift placed into theshipping staging areatruckPick the batteryDrop battery into thetruckBattery pickedBattery dropped into thetruckMove loaded forkliftto shipping dockBring battery to theshipping destinationForklift moved to theBattery brought to theshipping dockshipping destinationTruck driveEnd of shippingFig. 5 The current shipping processmanifesto constitutes the link between the picking processand the shipping process.In the shipping process, a single HR needs to manageall physical activities (e.g., Drop battery into the truck)and informational (e.g., Take the s-Manif) activities in theprocess. In both cases, the information used is mostlypaper-based. On the other hand, there is no means toverify that the type of batteries that is being pickedcorresponds to the one being ordered. The smoothrunning of these processes heavily depends on thejudgment of the HR involved. For example, there is nomechanism to know for sure that that the batteries that arebeing shipped are those specified in the manifesto. Thisoften leads to a shipment mismatch, and thus results in theincreased transportation costs as the truck driver needs tobring back the shipment and reschedule a new one, whichalso affects customer service delivery. Resolving thissituation is one of the goals of RFID technology adoption,by the TPL management board, for more effectivebatteries management.The new picking process with the RFID-enabledincremental change from RFID technology is similar tothe current (“as-is”) picking process. With a new no-valueactivity, which is “manually print the number of RFID tags(n-Tags)”—the first picking clerk (Picking-clerk 1) needs topick the order using a RFID printer. It must be noted thatthe TPL needs to conduct the tagging process because thesuppliers of the TPL firm are not yet involved in the
Inf Syst Front (2011) 13:693–706701Fig. 6 The shipping process with incremental change when using RFIDproject. Now, not only is the second picking clerkresponsible for picking the quantity of battery on the pPick to bring them in the shipping staging area, but he isalso in charge of all shipping activities.The new picking process increased the level of electronicintegration. Indeed, it resulted in the integration of theRFID infrastructure with the firm’s ERP and WMS. Thisallows the automatic validation and generation of themanifesto, and all picking activities related the manifestoare now transferred to the shipping process and areautomated all together, and thus increasing the level ofelectronic integration between the picking and the shippingprocess. One implication of this new level of electronicintegration is that the picking and the shipping processesshould henceforth be carried out when the truck is ready tocarry the shipment to the remote sites. It effectively resultsin the better use of the warehouse staging area.In this scenario, the workflow of the second pickingclerk radically changed as a result of the adoption and useof RFID technology. Now he has to perform not only histraditional responsibilities but also those of the shippingclerk. This resulted in labor cost savings, although a propertraining to update his skills is required to enable himperform his new responsibilities. Moreover, the shippingclerk can now be reassigned to other duties within thewarehouse.In the “as-is” shipping process, the process is triggeredby the shipping manifesto, and followed by the physicalpicking of the batteries from the shipping staging to thetruck by the shipping clerk.
702Inf Syst Front (2011) 13:693–706In the case of the shipping
radio frequency identification (RFID) is emerging as a new interorganizational system (IOS) that will transform supply chain business processes and practices (Curtin et al. 2007; Geng and Sirkka 2005; Gogan et al. 2007). Despite the high potential of RFID as an enabler of supply chain process innovation, the literature shows a lack of empirical .