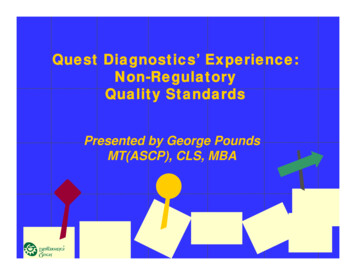
Transcription
Quest Diagnostics’ Experience:Non-RegulatoryQuality StandardsPresented by George PoundsMT(ASCP), CLS, MBA
Presentation ObjectivesThe presentation will answer the questions Why ISO 9001 & Six Sigma?How did Quest Diagnostics do it?What did we learn?What were the benefits?What’s the difference between all thesestandards and how do they relate toQuality?2
Why Non-RegulatoryStandards?While Regulatory standards are essential and provide anecessary foundation, compliance to Regulatory Standards werenot helping the business; meetcustomer needs the best laboratory services possible drive productivity and quality improvement industry competition improve employee hiring and retention employee market competition provide assay design standards industry leadership3
Quest DiagnosticsNon-Regulatory History19971998200020012003Pilot ISO 9001 at Nichols Institute as a Quality frameworkExpanded certification to other clinical and non-clinicalfacilities.Initiated Six Sigma as a Quality improvement program withinISO 9001 framework. Maintained ISO certification for currently certified labs Replicate ISO learnings to the remaining labs through SixSigma and Corporate Medical Quality.10 facilities Certified (5 clinical labs and 5 non-clinical)Fully implemented Six Sigma programthroughout Quest Diagnostics4
How was ISO implemented? Identified a corporate ISO leader.Identified an on-site ISO project leader.Identified an on-site project team (20 – 40 staff)Implemented a standard project plan(approximately 52 steps)Performed staff training (just-in-time method).First lab took 15 months, subsequent labs took10 months.Cost of Certification: 10,000 - 15,000Ongoing annual costs: 8,000 - 12,0005
What did we learn from ISO? ISO represents a cultural change to the organization.Resistance to change is normal must establish &communicate clear need and benefits.Key integrated components for success Clear and visible management participation is required. Solid tools for process management at all levels of theorganization. Solid document management at all levels of theorganization. Solid measurement system to know how you are doing. Solid training and competency for all staff. Solid supplier management process. Solid design control processMinimal recognition of ISO by Hospital andPhysician clients6
What are the Benefits from ISO? Management Participation!Setting clear organizational goals and alignmentaround those goals. Quality Planning!Places customer defined outcomes as the goalof the organization! Process Management!This is where most errors and problems occur!Removes department barriers!7
What are the Benefits from ISO? Document Management System!Controls document and records at all levels. not just SOPs. Measurement and Improvement System!Process and customer measures areembedded in the lab operation.Plan, Do, Check, Act! Supplier Management System!Supplier performance is monitored and they areaccountable to meet quality measures. Design Control System!8
Example: Quality PlanningProcess FlowBusiness Quality Council, MeetingProcess Flow / Input - OutputProcess InputsProcess OutputsReview NicholsOperating PlanOperating Plan &Champion ResponsibleFocus on MeetingOperating Plan ObjectivesReview Nichols Metrics(By Core Process / VOCReview / Customer Trends& Data / Internal VOC)Metrics Based onBalanced BU ScorecardCurrent & YTD MetricStatus for BU Targets &Performance; New IssuesReview Status of AllProjects Against thePlan(Green/Yellow/Red)Review NicholsSelected Projects andInitiativesIdentify Gaps Against OpPlan & Assign or ModifyResourcesProject Status SummaryFocus on ProjectProgressing TowardMeeting Op Plan & BUResource AllocationSelected ProjectReviewsDrives Project Progress,Focus on AchievingProject Desired ResultsParking Lot and IssuesIdentified During ReviewMeet Business UnitTargets; QualityImprovement Plans9
Example: Process ManagementPr. Owner: Dr. Raj PandianDevelop New Products/ServicesCore Process AlignmentNichols-Pr. Owner: Dave PauluzziAcquireThe CustomerPr. Owner: CarlBurgessPr. Owner: CarlBurgessPr. Owner: essSpecimenPr. Owner: KatieBisharTestSpecimenManageCustomer RelationshipEnabling ProcessesQuality/Six Sigma, HR, Finance, Materials, ITPr. Owner: Dr.Richard ReitzReportResultsPr. Owner: JohnBesserBill &CollectPr. Owner Carl BurgessPr. Owner: Marianne Weinell/ Lee Lavi/Karen Dow / John Besser/ Marc Gray10
ProcessProcess ManagementManagementExample: Process ManagementMANAGE ACCOUNTSTEST & REPORTRESULTSACQUIRE SPECIMENSAND ENTER ORDERSAcquire PatientSamples2.0Transport PatientSamples3.0Process PatientSamples4.0Test & ReportPatient Results5.0BILL &COLLECT6.0CUSTOMER NEEDSServe EMENT10.09.0INFORMATIONRESEARCH &MEDICALTECHNOLOGYDEVELOPMENT12.014.013.0QUALITY PLANNINGHUMAN RESOURCES8.0FINANCE11.0CUSTOMER SATISFACTIONACQUIRECUSTOMERS1.0Vision, Mission, Values, Roadmap 2000, Six Sigma, ISO, Ops Excellence, Document Control, Quality Metrics, Training, Internal AuditsMACRO MAP11
Example: Process ManagementA deeper dive!ACQUIREPATIENTSAMPLESMap 2.0 &2.1ACQUIRECUSTOMERSMap 1.0ProcessProcess ManagementManagementClient SOPPSC /ClientVisitSOPRecord SampleInformationAre thereany Sample orInformationProblems?ProcessPatientSamplesMap 4.0NoCheck withDispatch forMessagesDeliverSamples toProcessingSOPReturn to TestingLab or CourierHubPrepareSamples forShipmentSOPPost RouteDutiesSOPAll Other NonSampleDeliveriesSOPAreThere RT PATIENT SAMPLECourier ServiceMap 3.0September 2, 1999NoDocumentStoragePost RouteProblemResolutionSOP12
Example: Document ManagementDocument ManagementDocument StructurePoliciesProcessesABWhat to doHow it HappensProceduresCHow to do itRecordsDEvidence of Compliance13
Document Management(Quality Manual)Example: Document ManagementDocument StructureActualLEVEL UALLEVEL TIONMATERIALSMANAGEMENTMANUALLEVEL C18 LAB DEPT.MANUALSRESEARCH &DEVELOPMENTMANUALLEVEL DQAMANUALOTHERDEPT.MANUALSSHIPPING &RECEIVINGMANUALRECORDS14
Example:Management Responsibilityand MeasurementManagement ResponsibilitiesManagement ReviewQuality Measures include results of: all audits, internal or external customer feedback including surveys and complaints employee surveys key process measuresThen provide for corrective and preventive actions &follow-up actions from previous management reviews15
Example: MeasurementClient Retention TeamClient Retention Team in place. Service Solutions Specialists assess Clients AtRisk. Top 25 Tests TAT, SF and TNP activity for prior month. Contact SalesRep and summarize findings.Team members assign action items for improvedretention. In addition, will evaluate early intervention data.Test DescriptionExpectedRelease toFinalUnderExpected450Hepatitis B Surface Antigen021:23008:073701Hepatitis C Antibody, EIA033:39014:162%145558Hepatitis B Core Antibody (IgM)025:53006:210%038:22143478Hepatitis A (IgM), Acute Status025:54006:22068:261086960HIV-1/HIV-2 Antibody Screen017:06028:11944362T4, Free, Non-Dialysis049:59Draw :3247409CA 125, MEIA049:45021:480%027:2347983CA 27.29052:27039:190%026:45023:05404360LEAD, BLOOD 514Alpha-Fetoprotein, eine (Cardiovascular), Serum, FPIA056:27038:2510%031:24319199MATERNAL SERUM SCREEN 4071:45030:186%035:2029475CA 19-9, Serum021:50009:47036:0325910Hepatitis B Surface Antibody Quantitation030:57026:0821562PTH, Intact and Calcium052:57027:590%031:56216732Methylmalonic Acid115:10:00053:455%034:0418295Thyroid Peroxidase Antibody (Anti-TPO)051:39037:21041:20184210Vitamin B1, 5216218ANCA l, Ultra 90%038:2914404Thyroglobulin 45042:300%006:158%0%026:05039:0661%13%8%Average TAT 8%16
Example: MeasurementClient Retention TeamService Event Summary ReportService Event AnalysisClient 52572From 01 MAY 2004 to 31 MAY 2004Origin DescCause DescriptionCountCLIENTNO SAMPLE RECEIVED11Total %24%STEROIDSDELAY920%CLIENTSPILT ORDER PRIMARY SAMPLE RECEIVED716%CLIENTTEST NOT ACCESSIONED37%CLIENTBATCH NOT CROSSED37%CLIENTADDITIONAL INFORMATION REQUESTED TO REPORT TEST24%CLIENTTEST ADD HOLD12%CLIENTINCORRECT SAMPLE TYPE SUBMITTED12%CLIENTSTABILITY SAMPLE12%CLIENTTEST CANCELED BY CLIENT1CLIENTPATIENT VERIFY1SEROLOGYDELAY1SEROLOGYMISSING SPECIMEN1TEST SEND OUTSCOMMUNICATION COMPLAINT1ENDOCRINE PEPTIDESMISSING SPECIMEN1IMMUNOCHEMISTRYDELAY1Total 45Test Not Performed(TNP) AnalysisTNP Comment Description2%TNP-INTERFERING SUBSTANCE PRESENT. UNABLE TO2%QUANTITATE. Count12%TNP-Specimenexceeds Quest Diagnostics, Nichols Institute'srecommended;stability range. Please resubmit. Charges have been2%cancelled. Count1TNP-The EDTA blood specimen that we received was too old to yield2%an accurate; white blood cell count. We are unable, therefore, to2% or report; absolute values for the lymphocyte subsets.calculateCount12%TNP-Unable to perform ordered test with sample type submitted.Please contact; Quest Diagnostics Client Services for the samplerequirements for this test,; or if an alternative test is desired. Charges1have been cancelled. CountTNP-Unable to perform ordered test because the specimen wassubmitted in an; incorrect transport medium. Please contact QuestDiagnostics, Nichols; Institute Client Services at (800) 553-5445 forthe transport medium; requirements for this test, or if a1TNP-Duplicate test order. Test has been cancelled. Count5TNP-INTERFERING SUBSTANCE PRESENT. UNABLE TOQUANTITATE.; TNP-Unable to calculate due to interfering substance.Count1TNP-TEST REQUEST CANCELLED - NO CHARGE. Count5TNP-Cancelled per client request. CountTNP-Cancelled per client request.; TNP-NO SAMPLE RECEIVED.Count9Grand Count35117
Example: Training ManagementTraining Management Job Descriptions - describe the qualificationsand tasks for all job titles. Learning & Development - formal instruction toenhance overall knowledge or insight related tocurrent or future job positions for all employees. Training - formal instruction on SOPs or anyother document necessary to perform the tasksin the Job Description for all employees. Competency - periodic assessment of taskperformance for all employees.18
Example: Training ManagementTraining ManagementFILE TRAININGRECORD INDEPARTMENTPERFORM &DOCUMENTTRAININGAre additionaltasks to beperformed ?NONOACTIONCREATE TRAININGCHECKLISTYESIDENTIFY TRAININGNEEDS BASED ONDUTIES ANDPROCEDURES TO BEPERFORMEDYESAre new tasksdocumented in thejob description ?NODOCUMENT JOBREQUIREMENTSAND DUTIES IN JOBDESCRIPTIONTRAINING PROCESS19
Example:Supplier ManagementSUPPLIER NON-CONFORMANCEDATA COLLECTION&DOCUMENTATION PROCESS FLOWLab Identifies SupplierPerformance Deficiency forMaterial or Service ProvidedLab Contacts Supplier forTechnical Assistance &Deficiency ResolutionLab Reports Supplier PerformanceDeficiency at Daily Lab Ops MeetingUsing Applicable DatabaseNon-Conformance CodeLab Ops Database is UpdatedWith Supplier PerformanceDeficiency DataLab Ops Database GeneratesSupplier Root CauseAnalysis/Corrective ActionForm & Cover LetterMaterials Department Edits/IssuesCover Letter & Root CauseAnalysis/Corrective Action FormTo SupplierSupplier Completes/ReturnsRoot Cause Analysis/CorrectiveAction Form to MaterialsManager & DistributionSupplier Root Cause Analysis/Corrective Action Form ResponseEntered into Lab Ops Database20
How does Six Sigmafit into a Non-Regulatoryapproach to Quality?21
How was Six Sigma implemented? Identified a corporate Six Sigma leader.Identified Master Black Belts (BB) as onsite project leaders.Identified and trained on-site Black Belts.Implemented a standard project plan.Identified and initiated Six Sigma projects.Identified and trained Green Belts (GB).2000 – 2003: 330 BB & 1245 GB projectscomplete.22
What are we learning from Six Sigma? A cultural change to the organization. expect resistance!Better Six Sigma results from ISO certifiedfacilities!Management participation required.Project selection and alignment required forsuccess.Sharing of key learnings essential to overallsuccess.Effective and practical statistical and teammanagement tools.Hospital and Physician recognition ofSix Sigma is growing.23
What are the Benefits from Six Sigma? Highly evolved tool (statistical and teammanagement) for improvement! Best results if there is a well definedinfrastructure to support it.Extremely customer focused get the voice of the customer with specificcritical to quality measures!Focus on specific problems! Don’t boil the ocean!Focus on data not opinion! Get the right data in the right format!24
What are the Benefits from Six Sigma? Focus on root cause analysis! Practical use of statistical tools to understandthe root cause of the problem. Focus on sustaining the gain! The process owner participates in solutiondesign, monitoring and correcting future problems. Focus on risk assessment! FMEA tool for anticipating problems andidentifying solutions prior to incident. Proven Results! Customer Satisfaction: improved 20%Savings: Exponential25
/028/19/028/20/028/21/02*Release to Final TAT (Hrs)Example: HIV Genotype TATH IV G enotype A ssay C ycle T im eT arget C ycle T im e 168 H ours700P rocessIm provem ents InP lace6005004003002001000Setup DateKey Tools: VOC, Process Mapping, Time Study, Process Capacity analysisImprovements: Streamlined repeat process & instrument schedules.Implemented IT automation for reviews and reporting26
/19/028/20/028/21/02*0.6LCL 0.439480.30.2Release to Final TAT (Hrs)Human Contact in the Laboratory0.8First Round of Workouts0.7Second Round of WorkoutsUCL 0.57569CEN 0.50759HIV Genotype Assay Cycle TimeTarget Cycle Time 168 Hours53700600400200ProcessImprovements InPlace500UCL 0.36237CEN 0.29497300100LCL 0.227570UCL 0.18202CEN 0.11806Setup Date0LCL 0.05409Key Tools: VOC, Process Mapping, Time Study, Process Capacity analysisKey Learnings: streamline repeat process, instrument schedules,Implementing IT automation for reviews and reporting5/16/00Key Tools: VOC, created a reliable measure and display systemImprovements: wireless head-sets, accurate contact information in theLIS, dedicated staff for answering the phone.27
What are the Overall Benefits?BENEFITSISO Implemented ISO Six Sigma Customer Satisfaction Savings 199719981999200020012002200328
QUALITY EVOLUTIONSTRATEGIC QUALITYMANAGEMENT (1980s) (2000s*)OPERATIONAL QUALITYMANAGEMENT (1950s) (1980s*)WORK FORCE QUALITY CONTROL(1920s) (1950s*)*wide use by clinical lab industry!29
STAGES OF QUALITYNCCLS Guideline GP26 (based on ISO 9000)STAGETotal Quality ManagementACTIVITIES PERFORMEDQuality ImprovementFormal process to achieve significantimprovements and cost savingsQuality System“Comprehensive and Coordinated” systemto meet quality objectivesQuality AssuranceOrganized activities to provide“Confidence” that the organization meetsrequirements for qualityQuality ControlOperational techniques applied to “SpecificTasks” for quality and regulatorycompliance.Total management approach centered around“Customer Satisfaction”30
JURAN AND NCCLSJURANStrategic Quality ManagementNCCLS GP26Total Quality ManagementQuality ImprovementOperational QualityManagementQuality SystemQuality AssuranceWork Force Quality ControlQuality Control31
STAGES OF QUALITYNCCLS Guideline GP26 (based on ISO 9000)STAGEACTIVITIES PERFORMEDTotal Quality ManagementQuality ImprovementQuality ControlISO 9001ISO 15189Quality AssuranceCLIA/CAPQuality SystemNewSIX SIGMATotal management approach centeredaround “Customer Satisfaction”Formal process to achieve significantimprovements and cost savings“Comprehensive and Coordinated”system to meet quality objectivesOrganized activities to provide“Confidence” that the organizationmeets requirements for qualityOperational techniques applied to“Specific Tasks” for quality andregulatory compliance.32
ISO 9001 - 2000 RevisionManagement Responsibility(Clause 5)Plan Do - Check ActResource Management(Clause 6)DesignInputService Realization(Clause 7)ProcessPurchasingOutputCUSTOMER SATISFACTIONCUSTOMER REQUIREMENTSQuality Management System(Clause 4)Measurement, Analysis & Improvement(Clause 8)ISO 15189 does not develop these aspects33
Document ManagementDocument StructurePoliciesAWhat to doCLIA/CAP & ISO 15189 DO NOT DEVELOP THIS LEVELProcessesBHow it HappensProceduresCHow to do itRecordsDEvidence of ComplianceCLIA/CAPISO 15189ISO 900134
Presentation ObjectivesThe presentation will answer the questions Why ISO 9001 & Six Sigma?How did Quest Diagnostics do it?What did we learn?What were the benefits?What’s the difference between all thesestandards and how do they relate toQuality?35
Thank You for YourTime and AttentionQuestions?36
Sample Deliveries SOP TRANSPORT PATIENT SAMPLE Courier Service Map 3.0 Return to Testing Lab or Courier Hub Post Route Duties SOP Are There any Outstanding Issues? Process Patient Samples Map 4.0 ACQUIRE PATIENT SAMPLES Map 2.0 & 2.1 Post Route Problem Resolution SOP Document Storage ACQUIRE CUSTOMERS Map 1.0 Check with Dispatch for Messages No .