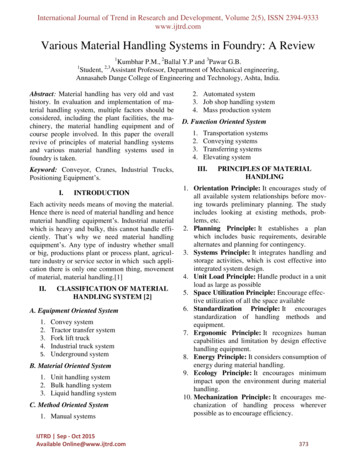
Transcription
International Journal of Trend in Research and Development, Volume 2(5), ISSN 2394-9333www.ijtrd.comVarious Material Handling Systems in Foundry: A Review1Kumbhar P.M., 2Ballal Y.P and 3Pawar G.B.Student, Assistant Professor, Department of Mechanical engineering,Annasaheb Dange College of Engineering and Technology, Ashta, India.12,3Abstract: Material handling has very old and vasthistory. In evaluation and implementation of material handling system, multiple factors should beconsidered, including the plant facilities, the machinery, the material handling equipment and ofcourse people involved. In this paper the overallrevive of principles of material handling systemsand various material handling systems used infoundry is taken.Keyword: Conveyor, Cranes, Industrial Trucks,Positioning Equipment’s.I.INTRODUCTIONEach activity needs means of moving the material.Hence there is need of material handling and hencematerial handling equipment’s. Industrial materialwhich is heavy and bulky, this cannot handle efficiently. That’s why we need material handlingequipment’s. Any type of industry whether smallor big, productions plant or process plant, agriculture industry or service sector in which such application there is only one common thing, movementof material, material handling.[1]II.CLASSIFICATION OF MATERIALHANDLING SYSTEM [2]A. Equipment Oriented System1.2.3.4.Convey systemTractor transfer systemFork lift truckIndustrial truck system5. Underground systemB. Material Oriented System1. Unit handling system2. Bulk handling system3. Liquid handling systemC. Method Oriented System1. Manual systemsIJTRD Sep - Oct 2015Available Online@www.ijtrd.com2. Automated system3. Job shop handling system4. Mass production systemD. Function Oriented System1.2.3.4.Transportation systemsConveying systemsTransferring systemsElevating systemIII.PRINCIPLES OF MATERIALHANDLING1. Orientation Principle: It encourages study ofall available system relationships before moving towards preliminary planning. The studyincludes looking at existing methods, problems, etc.2. Planning Principle: It establishes a planwhich includes basic requirements, desirablealternates and planning for contingency.3. Systems Principle: It integrates handling andstorage activities, which is cost effective intointegrated system design.4. Unit Load Principle: Handle product in a unitload as large as possible5. Space Utilization Principle: Encourage effective utilization of all the space available6. Standardization Principle: It encouragesstandardization of handling methods andequipment.7. Ergonomic Principle: It recognizes humancapabilities and limitation by design effectivehandling equipment.8. Energy Principle: It considers consumption ofenergy during material handling.9. Ecology Principle: It encourages minimumimpact upon the environment during materialhandling.10. Mechanization Principle: It encourages mechanization of handling process whereverpossible as to encourage efficiency.373
International Journal of Trend in Research and Development, Volume 2(5), ISSN 2394-9333www.ijtrd.com11. Flexibility Principle: Encourages of methodsand equipment which are possible to utilize inall types of condition.12. Simplification Principle: Encourage simplification of methods and process by removingunnecessary movements13. Gravity Principle: Encourages usage of gravity principle in movement of goods.14. Safety Principle: Encourages provision forsafe handling equipment according to safetyrules and regulation15. Computerization Principle: Encourages ofcomputerization of material handling and storage systems16. System Flow Principle: Encourages integration of data flow with physical material flow17. Layout Principle: Encourages preparation ofoperational sequence of all systems available18. Cost Principle: Encourages cost benefit analysis of all solutions available19. Maintenance Principle: Encourages preparation of plan for preventive maintenance andscheduled repairs20. Obsolescence Principle: Encourage preparation of equipment policy as to enjoy appropriate economic advantage.[2][3]IV.VARIOUS MATERIAL HANDLINGEQUIPMENTSA. Conveyers1. Wheel ConveyorUnit On-Floor AccumulateUses a series of skate wheels mounted on a shaft(or axle)Spacing of the wheels is dependent on the load being transportedSlope for gravity movement depends on loadweightMore economical than the roller conveyor Forlight-duty applications Flexible, expandable mobileversions availableFigure 1: Wheel Conveyor2. Roller ConveyorUnit On-Floor AccumulateMay be powered (or live) or non powered (or gravity)Materials must have a rigid riding surfaceMinimum of three rollers must support smallestloads at all timesTapered rollers on curves used to maintain loadorientation.Conveyors are used:1. When material is to be moved frequentlybetween specific points2. To move materials over a fixed path3. When there is a sufficient flow volume tojustify the fixed conveyor investmentConveyors can be classified in different ways:1. Type of product being handled: unitload orbulkload2. Location of the conveyor: in-floor, onfloor, or overhead3. Whether loads can accumulation the conveyor or no accumulations possibleFigure 2: Roller Conveyor3. Chain ConveyorUnit In-/On-Floor No AccumulationIJTRD Sep - Oct 2015Available Online@www.ijtrd.com374
International Journal of Trend in Research and Development, Volume 2(5), ISSN 2394-9333www.ijtrd.comUses one or more endless chains on which loadsare carried directlyParallel chain configuration used as (chain) palletconveyoror as a pop-up device for sortation (seeSortation conveyor: Pop-up devices)Vertical chain conveyorused for continuous highfrequency vertical transfers, where material on horizontal platforms attached to chain link (cf. vertical conveyor used for low-frequency intermittenttransfers)5. Trolley conveyorUnit Overhead No AccumulationUses a series of trolleys supported from or withinan overhead trackTrolleys are equally spaced in a closed loop pathand are suspended from a chainCarriers are used to carry multiple units of productDoes not provide for accumulationIt is commonly used in processing, assembly,packaging, and storage operations. [5]Figure 3: Chain Conveyor4. Magnetic belt conveyorBulk On-FloorA steel belt and either a magnetic slider bed or amagnetic pulley is usedTo transport ferrous materials vertically, upsidedown, and around cornersFigure 5: Trolley ConveyorB. CranesGeneral characteristics of cranes:1. Used to move loads over variable (horizontaland vertical) paths within a restricted area2. Used when there is insufficient (or intermittent) flow volume such that the use of a conveyor cannot be justified3. Provide more flexibility in movement thanconveyors4. Provide less flexibility in movement than industrial trucks5. Loads handled are more varied with respect totheir shape and weight than those handled by aconveyor6. Most cranes utilize hoists for vertical movement, although manipulators can be used ifprecise positioning of the load is required1. Jib CraneHorizontal boom (jib) supported from a stationaryvertical supportFigure 4: Magnetic Belt ConveyorIJTRD Sep - Oct 2015Available Online@www.ijtrd.com375
International Journal of Trend in Research and Development, Volume 2(5), ISSN 2394-9333www.ijtrd.comHoist can move along the jib and can be used forliftingOperates like an arm in a work area, where it canfunction as a manipulator for positioning tasksJib can also be mounted on the wallArm can rotate up to 360Used to span a smaller portion of the work area ascompared to a bridge crane. The supports can befixed in position or they can travel on runways. Itcan be used outdoors when “floor” supported atboth ends. [2]Figure 8: Gantry CraneC. Industrial Trucks1. Two-Wheeled Hand TruckLoad tilted during travelGood for moving a load up or down stairwaysFigure 6: Jib Crane2. Bridge CraneBridge mounted on tracks that are located on opposite walls of the facilityEnables three-dimensional handlingTop riding (heavier loads) or under hung (moreversatile) versions of the craneUnder hung crane can transfer loads and interfacewith other MHS (e.g., monorail systems)Figure 9: Two Wheeled Hand Truck2. Powered Pallet JackPallet Walk No Stack PoweredPowered lifting and/or travelPowered pallet jack is sometimes referred to as a“(walkie) pallet truck”Figure 7: Bridge Crane3. Gantry CraneSingle leg, double leg, and mobile types of gantrycranes Similar to a bridge crane except that it isfloor supported at one or both ends instead ofoverhead (wall) supportedIJTRD Sep - Oct 2015Available Online@www.ijtrd.comFigure 10: Powered Pallet Jack376
International Journal of Trend in Research and Development, Volume 2(5), ISSN 2394-9333www.ijtrd.com3. Counterbalanced (CB) Lift TruckPallet Ride StackSometimes referred to as a “fork truck” (but otherattachments besides forks can be used)Weight of vehicle (and operator) behind the frontwheels of truck counterbalances weight of the load(and weight of vehicle beyond front wheel s); frontwheels act as fulcrum or pivot pointRated capacity reduced for load centers greaterthan 24 in. and lift heights greater than 13 ft.Workhorses of material handling because of theirflexibility: indoor/outdoor operation over a varietyof different surfaces; variety of load capacitiesavailable; and variety of attachments available—fork attachments can replace the forks (e.g., cartonclamps) or enhance the capabilities of the forks(e.g., blades for slip-sheet’s)Figure 12: Hoist2. ManipulatorUsed for vertical and horizontal translation and rotation of loadsActing as “muscle multipliers,” manipulators counterbalance the weight of a load so that an operatorlifts a small portion (1%) of the load’s weight Canbe powered manually, electrically, or pneumatically. Manipulator’s end-effectors’ can be equippedwith mechanical grippers, vacuum grippers, electromechanical grippers, or other toolingManipulators fill the gap between hoists and industrial robots: they can be used for a wider range ofpositioning tasks than hoists and are more flexiblethan industrial robots due to their use of manualcontrolFigure 11: Counterbalance Lift TruckD. Positioning Equipments1. HoistUsed for vertical translation (i.e., lifting and lowering) of loads, Frequently attached to cranes andmonorails to provide vertical translation capabilityCan be operated manually, electrically, or pneumatically, Uses chain or wire rope as its liftingmedium.Hoists are categorized into duty classes: H1—infrequent, standby duty uses (1 or 2 lifts permonth); H2—light duty (avg. 75 start/stops perhour); H3—medium (max. 250 start/stops perhour); H4—heavy, and H5—severe duty.IJTRD Sep - Oct 2015Available Online@www.ijtrd.comFigure 13: Manipulator377
International Journal of Trend in Research and Development, Volume 2(5), ISSN 2394-9333www.ijtrd.com3. Industrial RobotUsed in positioning to provide variable programmed motions of loads“Intelligent” industrial robots utilize sensory information for complex control actions, as opposedto simple repetitive “pick-and-place” motionsIndustrial robots also used for parts fabrication,inspection, and assembly tasksConsists of a chain of several rigid links connectedin series by revolute or prismatic joints with oneend of the chain attached to a supporting base andthe other end free and equipped with an end effectorRobot’s end effector can be equipped with mechanical grippers, vacuum grippers, electromechanical grippers, welding heads, paint sprayheads, or any other toolingAlthough similar in construction, an industrial robot is distinguished from a manipulator by the useof programmed control logic as opposed manualcontrolPick-and-place industrial robots can be used as automatic palletizersMobile robots similar in construction to freeranging AGVsCan be powered manually, electrically, or pneumatically [4]CONCLUSIONDifferent MHSs were considered and discussed.They were mentioned as theoretical, ultimate, andtechnologically workable. However, the suggestionwas that companies should focus on and implementa MHS that is cost effective and is able to functionat the present time without any obstacle and failureThere are various principles and factors on whichSelection material handling system depends. Bystudying these parameters, selection of proper material handling system can done.References1. Keshava Chanda Arora, “Aspects of MaterialHandling” Firewall Media,2007,Page no 1-202. Mikell P.Groover, “Automation, ProductionSystems and Computer Integrated Manufacturing”, Page no.359-3993. Mayank Dev Singh,” Overall Productivity Improvement in Casting Industry by Using Various Industrial Engineering Techniques”, International Journal of Innovative Research inScience,EngineeringandTechnology,Vol.4,Issue 1, January 20154. B.Ramana,” Quantitative Analysis of AGVSystem in FMS Cell Layout”, Defense ScienceJournal, Vol 47, January 19975. Vivek A. Bandebuche,” Parts Handling Systems for Machine Shops of Small and MediumEnterprises”, International Journal of Engineering Research and General Science Volume1, Issue 2, December 2013Figure 14: Industrial RobotIJTRD Sep - Oct 2015Available Online@www.ijtrd.com378
Hence there is need of material handling and hence material handling equipment's. Industrial material which is heavy and bulky, this cannot handle effi-ciently. That's why we need material handling equipment's. Any type of industry whether small or big, productions plant or process plant, agricul-ture industry or service sector in which .