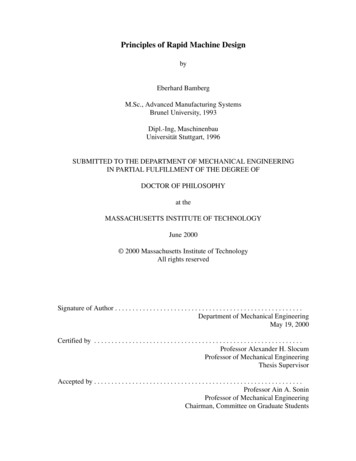
Transcription
Principles of Rapid Machine DesignbyEberhard BambergM.Sc., Advanced Manufacturing SystemsBrunel University, 1993Dipl.-Ing, MaschinenbauUniversität Stuttgart, 1996SUBMITTED TO THE DEPARTMENT OF MECHANICAL ENGINEERINGIN PARTIAL FULFILLMENT OF THE DEGREE OFDOCTOR OF PHILOSOPHYat theMASSACHUSETTS INSTITUTE OF TECHNOLOGYJune 2000 2000 Massachusetts Institute of TechnologyAll rights reservedSignature of Author . . . . . . . . . . . . . . . . . . . . . . . . . . . . . . . . . . . . . . . . . . . . . . . . . . . . . .Department of Mechanical EngineeringMay 19, 2000Certified by . . . . . . . . . . . . . . . . . . . . . . . . . . . . . . . . . . . . . . . . . . . . . . . . . . . . . . . . . . . .Professor Alexander H. SlocumProfessor of Mechanical EngineeringThesis SupervisorAccepted by . . . . . . . . . . . . . . . . . . . . . . . . . . . . . . . . . . . . . . . . . . . . . . . . . . . . . . . . . . . .Professor Ain A. SoninProfessor of Mechanical EngineeringChairman, Committee on Graduate Students
2
3Abstract . . . . . . . . . . . . . . . . . . . . . . . . . . . . . . . . . . . . . . . . . 7AcknowledgmentsChapter 1. . . . . . . . . . . . . . . . . . . . . . . . . . . . . . . . . . . 9Introduction . . . . . . . . . . . . . . . . . . . . . . . . . . . . . .1.1 Overview. . . . . . . . . . . . . . . . . . . . . . . . . . . . . . . . . . .1.2 Summary of ContributionsChapter 2.Design Principles1111. . . . . . . . . . . . . . . . . . . . . . . . . .13. . . . . . . . . . . . . . . . . . . . . . . . . . .152.1 Computer Aided Concept Generation2.1.1 Background . . . . . . . . .2.1.2 Overview . . . . . . . . . . .2.1.3 Concept Generation . . . . .2.1.4 CAD Component Libraries .16161717202.2 Component Selection Process . . . . . . . . .2.2.1 Stiffness Budget . . . . . . . . . . . .2.2.2 First Pass Selection . . . . . . . . . .2.2.3 Second Pass Selection . . . . . . . . .2.2.4 Bearing Calculations . . . . . . . . . .2.2.5 Ballscrew and Drive Motor Calculations.2525272830342.3 Concept Selection Process . . . . . . . . . . . . . . . . . . . . . . . .2.3.1 First Round Elimination - Fulfillment of Functional Requirements2.3.2 Second Round Elimination - Visual Inspection . . . . . . . . . .2.3.3 Third Round Elimination - Analytical Analysis . . . . . . . . . .2.3.4 Fourth Round Elimination - FEA Analysis . . . . . . . . . . . .39424344482.4 Finite Element Modeling Techniques2.4.1 Basic Facts About FEA . . .2.4.2 Basic FEA Elements . . . . .2.4.3 Modeling Bearings . . . . . .2.4.4 Modeling Plates as Shells . .2.4.5 Constraints . . . . . . . . . .2.4.6 Performance and Accuracy .515253566465662.5 Conclusion . . . . . . . . . . . . . . . . . . . . . . . . . . . . . . . . . . .71Chapter 3.Manufacturing Principles . . . . . . . . . . . . . . . . . . . . . . .3.1 Fabricated Structures. . . . . . . . . . . . . . . . . . . . . . . . . . . . .3.2 Kinematically Defined Machine Supports7373. . . . . . . . . . . . . . . . . .783.3 Standard Machine Elements . . . . . . . . . . . . . . . . . . . . . . . . . .79
43.3.1 Linear Rails . . . . . . . . . . . . . . . . . . . . . . . . . . . . . .3.3.2 Ballscrews . . . . . . . . . . . . . . . . . . . . . . . . . . . . . . .79813.4 Replication . . . . . . . . . . . . . . . . . . . . . . . . . . . . . . . . . .3.4.1 Reference Edge . . . . . . . . . . . . . . . . . . . . . . . . . . . .3.4.2 Replicated Joints . . . . . . . . . . . . . . . . . . . . . . . . . . . .828383Chapter 4.Damping . . . . . . . . . . . . . . . . . . . . . . . . . . . . . . . .854.1 Mathematical Models . . . . . . . . . . . . . . . . . . . . . . . . . . . . .854.2 Material Damping . . . . . . . . . . . . . . . . . . . . . . . . . . . . . . .884.3 Damping in Bolted Joints and Bearings . . . . . . . . . . . . . . . . . . . .894.4 Active Damping . . . . . . . . . . . . . . . . . . . . . . . . . . . . . . . .894.5 Constrained Layer Damping . . . . . . . . . . . . . . . . . .4.5.1 Background . . . . . . . . . . . . . . . . . . . . . . .4.5.2 Principle of Constrained Layer Damping . . . . . . . .4.5.3 The Split Tube Design . . . . . . . . . . . . . . . . . .4.5.4 Concrete Cast Damper . . . . . . . . . . . . . . . . . .4.5.5 Reinforced Concrete Cast Damper Design . . . . . . .4.5.6 Round Core Concrete Cast with Multiple Reinforcement4.5.7 Concrete Cast with Interlocking Constraining Layers . .Chapter 5.Damping Experiments. 90. 90. 91. 94. 96. 99. 103. 106. . . . . . . . . . . . . . . . . . . . . . . . 1095.1 Building the Dampers . . . . . . . . . . . . .5.1.1 Split Tube . . . . . . . . . . . . . . .5.1.2 Concrete Core Damper . . . . . . . . .5.1.3 Concrete Core Cast with Reinforcement5.1.4 Concrete Mixture . . . . . . . . . . .5.1.5 Material Cost . . . . . . . . . . . . . .1101101111131141155.2 Experimental Setup . . . . . . . . . . . . . . . . . . . . . . . . . . . . . . 1165.3 Damping Calculations . . . . . . . . . . . . . . . . . . . . . . . . . . . . . 1175.4 Experimental Data . . . . . . . . . . . . . . . . . . . . . . . . . . . . . . . 1195.5 Test Results . . . . . . . . . . . . . . . . . . . . . . . . . . . . . . . . . . 1225.6 Conclusion . . . . . . . . . . . . . . . . . . . . . . . . . . . . . . . . . . . 123Chapter 6.Case Study - STG . . . . . . . . . . . . . . . . . . . . . . . . . . . 1256.1 STG . . . . . . . . . . . . . . . . . . . . . . . . . . . . . . . . . . . . . . 1276.1.1 Overall Machine Concepts . . . . . . . . . . . . . . . . . . . . . . . 1286.1.2 First Round Elimination - Fulfillment of Functional Requirements . . 131
56.1.36.1.46.1.56.1.6Second Round Elimination - Visual InspectionResult of First and Second Round EliminationThird Round Elimination - FEA Analysis . . .Final Round Elimination - Team Discussion .1311351351396.2 STG Base . . . . . . . . . . . . . . . . . . . . . . . . . . . . . . . . . . . 1396.2.1 STG Base Concepts . . . . . . . . . . . . . . . . . . . . . . . . . . 1396.2.2 Design Optimization . . . . . . . . . . . . . . . . . . . . . . . . . . 1456.3 STG Gantry . . . . . . . . . . . . . . . . . . . . . . . . . . . . . . . . . . 1496.3.1 STG Gantry Concepts . . . . . . . . . . . . . . . . . . . . . . . . . 1496.4 STG Modal Analysis . .6.4.1 Rigid Body Modes6.4.2 Actual Modes . .6.4.3 RecommendationsChapter 7.Case Study - TubeMill.154155157162. . . . . . . . . . . . . . . . . . . . . . . . 1637.1 Error Budget . . . . . . . . . . . . . . . . . . . . . . . . . . . . . . . . . . 1647.2 Overall Machine Concepts. . . . . . . . . . . . . . . . . . . . . . . . . . 1677.3 Base Concepts . . . . . . . . . . . . . . . . . . . . . . . . . . . . . . . . . 1687.3.1 First Round Elimination - FEA Analysis . . . . . . . . . . . . . . . 1697.3.2 Second Pass Elimination - Global Sensitivity Study . . . . . . . . . 1737.4 TubeMill Gantry Concepts. . . . . . . . . . . . . . . . . . . . . . . . . . 1757.5 Design Optimization of Gantry . . . . . . . . . . . . . . . . . . . . . . . . 181Nomenclature . . . . . . . . . . . . . . . . . . . . . . . . . . . . . . . . . . . . . 183References . . . . . . . . . . . . . . . . . . . . . . . . . . . . . . . . . . . . . . . 185
6
Principles of Rapid Machine DesignbyEberhard BambergSubmitted to the Department of Mechanical Engineeringon May 19, 2000 in Partial Fulfillment of theRequirements for the Degree of Doctor of Philosophyat the Massachusetts Institute of TechnologyABSTRACTFollowing a continuing industry wide trend that began many years ago, design-to-manufacturing times for all kinds of products are getting increasingly shorter. The productionequipment industry is no exception to this development and needs to respond accordingly.This thesis presents a novel approach to conceptual design as part of a rapid machinedesign initiative. Solid model CAD systems and advanced engineering tools are used during the early design phase to generate realistic concepts of designs for manufacturingequipment. Concept evaluation is done very effectively through use of advanced analysistools such as Finite Element Analysis. Core elements of this initiative are: create reasonably detailed concepts with 3D CAD systems, analyze concepts analytically if possible orthrough use of finite element methods if necessary, and build designs from fabricatedstructures so there are no tooling times or costs, resulting in short design-to-manufacturetimes. In addition, to enable this methodology to be realizable, a new design for structuraldamping is presented which helps to reduce design uncertainty caused by vibration. Thenovel constrained layer damping design achieves the same or better levels of damping at afraction of the cost of existing designs.Case studies of two fabricated machine tool structures are used to illustrate this new FEAbased concept evaluation technique. The first study illustrates this design process in whichthe new approach to conceptual design led to a fundamentally new way of designingmachine tool structures. A second study presents an optimization process where FEA isused to select, size and position structural members of a truss-like machine base.Thesis Committee:Prof. Alexander H. Slocum (Chair)Prof. Sanjay SarmaProf. Samir NayfehDept. of Mechanical Engineering, Massachusetts Institute of Technology
8ABSTRACT
ACKNOWLEDGMENTSThis research was supported by Bill Silberhorn and Bud Webber of the Elk Rapids Engineering Corporation, a division of Star Cutter Company. I am grateful to Stan Ruskowskifor his open mind towards new ideas and turning them into an actual machine tool.My special thanks go to my friend and advisor Alex Slocum for his guidance and neverending inspiration. Snowboarding wouldn’t be the same without him. Prof. Sanjay Sarmafor his constructive criticism on writing this thesis and Prof. Samir Nayfeh for sharing hisvast knowledge on machine dynamics with me as well as letting me use his modal analysishard- and software.I could not have completed this work without help from Kripa Varanasi who with greatpatience introduced me to modal analysis, its equipment, and the proper interpretation ofthe results. I would also like to express my gratefulness towards all my colleagues fromthe Precision Engineering Research Group for keeping me on my toes in the past andhopefully the future too.And last but not least Stacy Morris for her understanding during the past months of intensewriting - may the future provide more quality time.And at last a word of wisdom from yet another source of inspiration to all those designersout there that still don’t think analysis is necessary:Do Or Do Not - There Is No TryYoda9
10ACKNOWLEDGMENTS
Chapter 1INTRODUCTION1.1 OverviewThe methodology of rapid machine design attempts to shorten design-to-manufacture timeof production equipment by using advanced engineering tools such as Computer AidedDesign systems (CAD) and Finite Element Analysis (FEA) during the conceptual designphase. It is hypothesized that by identifying the best of all available design concepts, overall development time can be shortened. Further time savings result from building machinecomponents out of fabricated structures instead of casts. This eliminates the need for making molds and other specialized tooling systems, and provides a high degree of flexibilityin terms of changing the design and/or making modifications to design specifications.Special FEA modeling techniques and principles are being presented that allow designersto create models that are optimized for fast computing time at reasonable accuracy. Casestudies of two fabricated machine tool structures are used to illustrate this new FEA basedconcept evaluation technique. The first study illustrates this design process, in which thenew approach to conceptual design led to a fundamentally new way of designing machinetool structures. A second study presents an optimization process where FEA is used toselect, size and position structural members of a truss-like machine base. These resultsassist the designer in the subsequent selection of the best concept.11
12INTRODUCTIONUsing solid models for concept generation has several tremendous advantages: The solid model makes it very easy to visualize the concept. Easy interfaces to mechanical analysis packages allow fast and accurateevaluation of the design. By combining existing concepts, new ideas can be quickly realized. Component libraries allow fast insertion of predefined, standard key components. Upon concept selection, existing models can be used for continuing designwork. Through exchange of files, design teams can effectively communicate witheach other outside meetings. Files are easy to output to rapid prototyping.Welded machine tool structures provide easy scalability in terms of size and outstandingflexibility in terms of fast design and fabrication; however, damping of the structure is avery critical issue. Unlike cast iron or polymer concrete-based components, welded steelplates have virtually no internal damping and are therefore prone to unwanted vibrations.Filling the structure with concrete or sand adds damping but also a great deal of unwantedweight. A better approach is the use of constrained layer damping where a viscoelasticlayer is squeezed between the structure and one or more constraining layers. Kineticenergy from relative motion between the structure and the constraining layer as it oc
the base of a machine from standard, larg e diameter tubes, resulting in devel-opment and implementation of a completely new base design. 4. Component selection tools: development of spreadsheets for rapid selection of machine components that assist designers to very quickly select compo-nents based on functional requirements. 5. Novel .