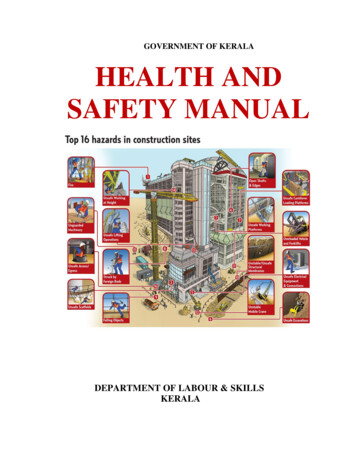
Transcription
GOVERNMENT OF KERALAHEALTH ANDSAFETY MANUALDEPARTMENT OF LABOUR & SKILLSKERALA
HEALTH AND SAFETY ent Prevention ProgrammeHealth & Safety PolicyStatutory RequirementsSafety OrganizationE.a Site Safety Officer/Safety Engineer/ManagerE.b Qualifications of Safety OfficerE.c Safety CommitteeHS ResponsibilitiesF.1 Project ManagerF.2 Construction ManagerF.3 Engineers/Supervisors/ForemenF.4 Store KeepersF.5 WorkforceF.6 Sub-ContractorsActions RequiredG.a Before ImplementationG.b During ImplementationSafety Training ProgrammesH.a Safety Induction Training for new employeesH.b Safety In-house trainingH.c Refresher TrainingH.d External Safety Training (Specialised H.S. Training)H.e Tool Box TalksHS Inspections & AuditsI.1 HS InspectionsI.2 HS AuditsI.2.a Internal HS AuditsI.2.b External HS AuditsHouse KeepingFire Prevention & ControlK.a Prevention of FiresK.b Control of l SafetyUse of Hand Tools & Electric Power ToolsWork at HeightsHandling of Hazardous ChemicalsSafe Erection of Steel StructuresSafety In Demolition WorkSafe Procedures For Excavation WorkSafe Material Handling Operations1112131414151616
TUVWXYZS.a Lifting OperationsS.b Safety Requirement for Vehicles, Equipment & MachineryS.c Manual Handling of MaterialsSafe Practices For Welding and Cutting OperationsPersonal Protective EquipmentHealth & Welfare RequirementsV.1 Health RequirementsV.2 Welfare facilitiesEmergency Response ProceduresEnvironmental ProtectionPermit –To-WorkReporting of Near Misses/Accidents/ Dangerous -1A Typical HS Policy23Annexure-IIGeneral Site H.S. Rules & Regulations23Annexure-IIINear Miss Incident Report24Annexure-IVForm XIV-Report of Accidents and Dangerous Occurrences25Annexure-VAccident Investigation Report28Annexure-VIMonthly HS Statistics28Annexure-VIISite Safety (HS) Inspection Checklist29Annexure-VIIIHazards & Mitigation/Control Measures of High Risk Activities32
A.INTRODUCTIONSAFETY in construction is of paramount importance as any fatal accident will cause irreparable lossof human life, money and progress of work leading to reduction in morale and de-motivation of thework force. In order to prevent occurrence of an accident, every organization should follow thesafety norms and ensure that they are effectively implemented.The primary objective of this manual is to ensure non-occurrence of accidents in work places. Thesignificance for safety starts from the stage of design and continues during the full life cycle of aproject including maintenance. The designers, consultants, contractors, clients and workers sharejoint responsibility for safety which should be built into their work culture and systems.Every personnel at site have to contribute their maximum effort towards safety promotionalactivities. They have to give adequate care for their safety as well as fellow personnel. Safety is tobe treated as a part of work and safe methods are to be practiced by every individual till it becomesa habit and is voluntary. People should be pro-active and no one should wait for an incident oraccident to do something, instead, they have to take all precautionary measures before anythinghappens.This manual specifies the basic fundamentals which will address mainly about the potential hazardsand unsafe practices leading to serious accidents. The emphasis here is to ‘prevent than cure’. Atpresent, the minimum and general safety requirements are given in this manual and it will be revisedon the need basis. If these procedures and code of practices are religiously followed the objectiveof having ‘zero accident’ can eventually be achieved. This safety manual is prepared with dueconsideration of construction safety requirement and for the benefits of all concerned organizationespecially for the Builders, Developers and Contractors for the formulation of safety manual(company wise) and project safety plans (project wise). All of them are requested to read this manualcarefully and utilize the given provisions accordingly. If Organizations working in the constructionindustry have any doubts or needs more information about the construction safety matters, they canapproach the office of the Labour Commissioner, Govt. of Kerala, Thiruvananthapuram to clarifytheir doubts.B.ACCIDENT PREVENTION PROGRAMMEPrevention is always better than cure. The ultimate objective is to reduce accidents by planning anaccident prevention programme and its effective implementation. Safety shall not be viewed as aseparate entity. It should be integrated with all activities right from design, estimate, planning andexecution stages. This programme requires effective and efficient monitoring and controlling.Certain important tips for an effective accident prevention programmes are given below: Ensure an effective safety organization to look after safety matters. Recruit the right personnel in the right places. All personnel at the site shall express and exercise their own safety role & responsibilities. Provide Information, Instruction and Training to all personnel at site regarding hazards,risks and the control measures. Establish & maintain good housekeeping practice throughout the site premises. Ensure effective supervision for all constructional activities. Provide safe access and egress at the site premises. Provide adequate lighting /illumination throughout the site premises on the need basis.
Display the relevant safety sign boards and safety instructions at the prominent locations. All personnel at the site should observe and obey the safety signs & symbols and safetyinstructions displayed at the site premises. Establish and maintain a proper system for safely using the electric power. Ensure appropriate fire prevention & control measures. Report, investigate and take the relevant corrective measures for all cases of near misses. Report and investigate accidents and communicate the lessons learnedto all employees. Also take the relevant precautionary measures to avoid similaroccurrences in future. Wear the relevant Personal Protective Equipment (PPE) at the site premises and otherareas on the need basis.In short, formulate and adopt PROJECT SAFETY PLAN and implement the provisions given in theplan accordingly.C.HEALTH & SAFETY POLICYSafe and healthy working conditions do not happen by chance. Employers need to have a writtensafety policy for their enterprise setting out the safety and health standards which it is theirobjective to achieve. As per the statutory requirement, every establishment employing 50 or morebuilding workers shall prepare a written statement of his policy in respect of safety and health atwork. The employer shall revise the safety policy as often as necessary. The policy shall be signedand dated by the senior executive (preferably by the chief executive) who is responsible for seeingthat the standards are achieved, and who has authority to allocate responsibilities to managementand supervisors at all levels and to see they are carried out. A typical HS Policy is given theAnnexure-ID.STATUTORY REQUIREMENTSImportant Act & Rules “Buildings and Other Construction Workers (Regulation of Employment and Conditions ofService) Act, 1996”. This is a Central Act, it extends to the whole of India, the Actpromulgated in 1996 and it has 64 Sections and XI Chapters. According to Section-44, Anemployer shall be responsible for providing constant and adequate supervision of anybuilding or other construction work in his establishment as to ensure compliance with theprovisions of this Act relating to safety and for taking all practical steps necessary toprevent accidents. This clause itself is self explanatory to point out the responsibility ofthe employer. “Buildings and Other Construction Workers (Regulation of Employment and Conditions ofService) Kerala Rules, 1998”. The Rules are framed as per the provisions given in “ THEBUILDING AND OTHER CONSTRUCTION WORKERS (REGULATION OF EMPLOYMENTAND CONDITIONS OF SERVICE) ACT,1996”. It has 317 Rules, 8 Schedules and 46 Forms Inter State Migrant Workmen (Regulation of Employment & Conditions of Service) Act,1979. According to this Act, Contractors must pay timely wages equal or higher than theminimum wage, provide suitable residential accommodation, prescribed medical facilities,protective clothing, notify accidents and causalities to specified authorities and kin. The
Act provides right to raise Industrial Disputes in the provincial jurisdiction where theywork or in their home province. The act sets penalties including imprisonment for noncompliance. In addition to the above, the rules & regulations of concerned Traffic Department,Municipalities, Electricity Board, Civil Aviations, Fire Force Department; and provisionsgiven in the Codes of practices (IS) etc., also shall be effectively implemented by theemployer wherever and wherever it is applicable.In addition to the above, it is the responsibility of the employer to display the site safety rules ®ulations at the entrance. A typical copy of the site HSE rules & regulations are given in theAnnexure-IINon-compliance of Statutes & Regulations.The project manager at the site is bound to take appropriate disciplinary actions on any violations ofstatutory requirements, rules & regulations, and non-compliance of company’s HS policy. Allpersonnel at the site should get the rights to point out the violation of rules & regulations.E.SAFETY ORGANIZATIONThe organization of safety on the construction site will be determined by the size of the work site,the system of employment, rating of the potential risks, and the way in which the project is beingorganized. Safety and health records should be kept which facilitate the identification andresolution of safety and health problems on the site.a)Site Safety Officer/Safety Engineer/ManagerIn every establishment wherein 500 or more workers are ordinarily employed, the employershall employ the safety officers. The position of such safety officers shall be notified by theChief Inspector. The Labour Commissioner, Govt. of Kerala). Whoever is appointed shouldhave direct access to an executive director of the company. The position and status of thesafety officer shall be clearly marked on the organization chart of the project.b)Qualifications of Safety Officer A person shall not be eligible for appointment as a safety officer unless he possesses a recognized degree in any branch of engineering to technology andhad a practical experience with construction work in a supervisory capacity fora period of not less than 2 years; or possesses a recognized diploma in anybranch of engineering or technology and has had practical experience ofconstruction work in a supervisory capacity for a period of not less than 5years; or possesses a degree or diploma in industrial safety with at least onepaper in construction safety (as elective) and recognized by the CentralGovernment in this behalf; or possesses a recognized degree or diploma inengineering or technology and has had experience of not less than 5 years inthe department of Central Government which deals with the administration oflabour legislations pertaining to safety; or possesses a recognized degree ordiploma in engineering or technology and has had experience of not less than 5years in training & education or research in the field of accident prevention inindustry or construction work. The ultimate authority for notifying the safety officer falls on the Chief Inspector. Though the employer is not required to appoint a safety officer as per thestatutory requirement or the number of employees at site, there shall be acompetent safety officer or a safety representative who have acquired adequateknowledge on site safety standards and requirements. If a responsible safetyperson is not available at the site, the employer cannot exercise the theirresponsibility for taking precautionary measures to prevent accidents.
The duties and responsibilities of the site safety officer/engineer/manager should include, butnot limited to the following: identify the hazard & conduct risk assessment for all activities from the mobilization todemobilization ( see Annexure- VIII); Acquire the knowledge on statutory provisions pertaining to construction safety; Ensure that the relevant safety sign boards, safety posters, cautionary instructions,general site safety rules& regulations, emergency procedures with contact telephonenumbers, and emergency assembly points etc., are displayed at the prominentlocations. All of them shall be in English and other language(s) understandable by themajority of workers; conduct safety induction training to all new entrants coming to the site irrespective oftheirlevel of status and also conduct the safety in-house trainings on the need basis; conduct regular site inspection and advise the concerned person(s) to take correctivemeasures immediately to eradicate the dangerous situations; investigate near misses, accidents, dangerous occurrences, and occupational diseasesand communicate the lessons learned to all employees. Also informed to the concernedpersonnel to take corrective and preventive measures to be taken to avoid suchoccurrences; acting as a secretary and technical adviser to the safety committee; ensure that implementing safety management system as per the safety budgetingfor the project;c) ensure that pre-job meeting is conducted just before starting the job; keep the copies of the license for the operators of vehicle/equipment/machinery; thirdparty test certificates for the lifts, hoists & cranes; third party certificates for thescaffolding crew, first-aider/male nurse; competency of welders & electricians; andMaterial Safety Data Sheets (MSDS) for chemicals etc., at the site safety office; prepare, maintain and update all safety reports and records; ensure that necessary personal protective equipment is available and used; and ensure that the provisions given in the project safety plan is effectively implemented.Safety CommitteeEvery establishment wherein 500 or more building workers are ordinarily employed, there shall bea safety committee constituted by the employer which shall be represented by equal number ofrepresentatives of employer and building workers/ representative of the recognized trade unions.
Safety committee meetings shall be held at least once in a month at site. The committee shalldiscuss every aspect of safety, its adequacy with respect to the work, implementation, awarenesslevels, training, effectiveness of communication related to safety, detailed analysis of accident ornear miss that has occurred, further improvement required etc. The entire proceedings of themeeting shall be recorded. Action taken and compliance report shall be placed before the SafetyCommittee in the next safety committee meeting. Recommendations of the safety committee shallbe submitted to the management (Project Manager) for review and its proper implementation.If there is no safety committee constituted in the construction project as per the statutoryrequirement, it does not mean that there is no need for safety meeting. Weekly or monthly safetymeetings shall be conducted to discuss the current safety problems and future course of action toeradicate the dangerous situations. All key personnel at the site shall sit together and the meetingshall be chaired by the Project Manager. The implementation of the safety meetings will be one ofthe effective accident prevention programmes and it will be one of the important tools to exercisethe responsibilities of the employer towards safety promotional activities according to the section44 of the BOC Act,1996.F.HS RESPONSIBILITIESThe employer ( builders/developers/contractors) is fully responsible for taking all precautionarymeasures to avoid accidents in the construction project. Generally, the main/principal contractorwho is responsible for the construction from the mobilization to de-mobilization will be theemployer.An employer shall be responsible for providing constant and adequate supervision of any buildingor other construction work in his establishment as to ensure compliance with the provisions of thisact relating to safety and for taking all practical steps necessary to prevent accidents.Officially, on behalf of the principal contractor, the project manager is responsible for dealingsafety matters in his project. The major responsibilities of certain personnel/organizations at thesite are given below:1)Project Manager Ensure that H.S. Policy and procedures of the company is effectively implemented inthe project.Actively participate in the safety meetings and implement all outcomes of thosemeeting in the project.Acquire knowledge in statutory obligations and ensure its compliance in the project.Visit the work place frequently and monitor safety aspects during the visit.Investigate accidents with the help of a Safety Officer and establish causes andremedial measures to prevent re-occurrenceRecommend suitable incentive schemes to increase the safety awareness/performanceamong the employeesEvaluate the Safety performance of the employees and recommend for proper incentivefor best performance.Give strong instructions and delegate the responsibilities to the sub-ordinates toimplement the provisions given in the project safety plans.Actively participate in H.S internal audit and follow-up of audit recommendations.In short, effectively implemented the provision given in the project safety planthroughout the project activities.
2) Construction Manager3) Exercise the safety responsibilities of the project manager in implementing the safetymanagement system at the work site Ensure that H.S. Plan for the project is effectively implemented Give instructions to all sub-ordinates in implementing safety standards andprovisions at the workplace.Engineers/Supervisors/ForemenGood planning and organization at each work site and the assignment of clear responsibility toEngineers/Supervisors/Foremen are fundamental to safety in construction.” Each supervisorrequires direct support of project manager/construction manager. Engineers and supervisorsare directly supervising the workplace and workers. Therefore, they have a vital role toimplement safety provisions and standards in their own areas of activities. They should:4) Ensure effective supervision at the workplace. In addition to the supervision of thework, inspecting the work spot for on the spot corrections of unsafe acts of theworkmen & unsafe working conditions. Conduct pre-job meeting just before starting the work. Ensure that good housekeeping practice is established and maintained at theworkplace. Ensure that the relevant safety, health and environmental system &facilities arearranged at the workplace. Ensure that workers have been adequately trained for the job they are expected to do;workplace safety measures are implemented as per the project safety plan; andnecessary personal protective equipment is available and used.Store keepers Ensure that no smoking boards, relevant safety instructions, signs & symbols etc., aredisplayed in the store premises. Implement good housekeeping practice inside and outside the store building. Ensure that adequate lighting is always available in and outside the store. Implement the relevant material codification standards while storing the materials. Ensure that relevant ventilation facility is provided in the storage areas. Segregate the combustible materials, non-combustible materials, hazardous chemicals,non-hazardous chemicals etc., with tags in the proper way and give adequate access toreach the materials easily. Ensure that MSDS is readily available for all hazardous chemicals. Read andunderstand the details given in MSDS and pass the information to the sub-ordinatesand the personnel who are supposed to handle these materials. Copy of all MSDS shallbe given to the site HS Officer/Engineer Ensure that fire prevention & control measures in the store area are very effective.
5)6) Check the materials/equipment/machinery/tools etc., carefully while receiving andissuing and don’t issue or receive any defective one. Prepare, maintain and update all records for receiving and issuing of materials Wear the relevant PPE’s while handling and storing the materials and ensure that allsub-ordinates are doing the same.Workforce Beware of your Health & Safety and your fellow-workers. Inform all abnormal situations to the superiors immediately. Ensure the potential hazards of the work are well understood and do the work safelyand in time. Properly wear the P.P.E’s on the nature of the job and the work site. Use the tools/appliances/equipment properly. Report all incidents/accidents immediately to the concerned personnel. Discard the defective PPE’s and Tools safely and replace by the new one. Clean up the work area immediately after finishing the work. Be alert in case of emergencies and act as per the emergency response procedures. Always follow the safety instructions of superiors and safety Officer. Actively attend the TBM and safety awareness programs.Sub-Contractors Identify the hazards of their work, assess the risks, and tell the contractor how theyare to be controlled. Co-operate and co-ordinate with the Contractor, other sub-contractors andsuppliers Comply the relevant provisions mentioned in the project HS Plan Conduct the risk assessment for all activitities and submit the details to theContractor prior to the commencement of any activity at the site. Give the relevant information, instruction and training to the employees. Obtain all information from the contractor about the hazards and risks at the workplace and remedial action to be taken to eliminate/avoid the risk and pass thisinformation to all employees. Immediately report all accidents/incidents/near misses to the contractor. Appoint a suitable and competent Safety Officer or HS co-ordinator and instructhim to co-operate and co-ordinate with the site safety engineer. Submit all HS reports including accidents/incidents/near misses to the contractor Follow the emergency response procedures of the contractor
G.ACTIONS REQUIREDa)Before ImplementationFrom the design and tendering stage onwards, accident prevention requirements should becarefully analyzed by all concerned organizations. Adequate monetary allocations (HSbudgeting) should be made for items such as barricades, safety signs & symbols, portablefire extinguishers, sand buckets, first-aid medicines & equipments, approach platforms,temporary supports, scaffoldings, warning tapes & traffic cones, pipes/re-bars, waste bins,personal protective equipment (like safety helmet, safety harness, safety nets, goggles,gloves, welding shield/glass, safety shoes & gumboots, ear plugs/ear muff and dust masks)etc,. The approximate cost for the placement of safety officer, safety assistants, safetyhelpers, first-aider/male nurse etc., also shall be estimated and included in the safetybudgeting.b)During ImplementationGeneralImmediately at the start of any job, key personnel should discuss about accident preventionprocedures during the pre-job meeting. Job layouts, plans and schedules should be studiedto determine requirements of safety materials, as mentioned in the above paragraph and aprocurement schedule should be prepared.Supervisory personnel assigned to the job should review initial planning, discuss anycondition changes and alter safety plans as required. On the basis of decision taken, a briefsupplemental safety programme is to be developed and distributed to all supervisorypersonnel on the job and to those who may later be assigned. Subsequently, regular safetymeetings shall be conducted to monitor the safety performance.Recorded safety announcement, in relevant different languages, shall be played using PAsystem, just before commencement of the work in the morning and afternoon as well asduring the tea breaks in the morning and evening.Unless there is accurate means of measure, it is virtually impossible to determine progressin any management function and accident prevention is no exception. All accidents shouldbe supplemented with an investigation report for internal purposes. [refer Annexure-IV forspecimen report]H.SAFETY TRAINING PROGRAMSa) Safety Induction Training for new employeesNo employee shall be assigned on job without attending H.S. induction training.Safety Officer should conduct this training and proper record is to be maintained.All concerned personnel should send the new employees to the safety section andensure that the new employees are attended this training before starting their job.b) Safety In-house trainingH.S. In-house training shall be given to the employees on the basis of generalrequirements and training need analysis. Safety professionals will conduct this typeof training programs. Proper records shall be maintained and it will be reviewedperiodically.
c) Refresher TrainingThe Site Safety Professionals and the immediate Supersvisor of the individualsshould assess the performance of the people . If it is findout any drawbacks fromany individual/groups , suitable training shall be scheduled and conductedaccordingly.d) External Safety Training ( Specialised H.S. Training )In special cases, if it is found that specialised training is required, it can bearranged . But it will be studied and reviewed by the H.S. Manager and after theapproval of Managing Partner, it will be arranged accordingly.e) Tool Box TalksTool box talks will be given to workers on daily basis and records will bemaintained. It will be conducted by the concerned Supervisor –in-Charge and therecords shall be documented by the concerned Project Safety Officer.I. HS INSPECTIONS & AUDITSI.1 HS InspectionsThe Safety Officer/Site Line Management Personnel will conduct frequent HS Inspections(Both Planned and Unplanned) with comprehensive checklist and subject to a written reportof the results of the inspection, completed as soon as practicable after the inspection. It isthe responsibility of all concerned personnel to take corrective actions on inspectionreports. A typical HS Inspection checklist is attached in the Annexure- VII.In addition to the above, specific inspections shall be conducted for certain activities,vehicles, tools, equipment & machinery etc. by the concerned responsible personnel.A register shall be maintained for inspections, but not limited to: Scaffold InspectionExcavation InspectionCranes & Other Lifting Accessories InspectionFire Fighting Equipment InspectionFirst Aid Facilities & Equipment InspectionVehicles & Equipment/Machinery inspectionI .2 HS Auditsa)Internal HSAuditsMonthly internal HS Audits shall be conducted by the project manager and site safetyofficer/engineer and it shall be recorded in the prescribed format. It is the responsibility ofthe project manager to give the information on the adverse comments in the Audit report tothe concerned sub-ordinates for taking the proper corrective as well as preventive measureswithout any delay.a)External HS AuditExternal HS Audit gives the clear picture of safety deficiencies and status of safetyperformance of the construction project. The safety audits shall be done on the basis of thefollowing points:
J. To be done by independent auditors enlisted by the Chief Inspector. Audit to be done once in six months at a reasonable fee to be decided by the above bodies. The observations of the audit team to be classified as major and minor non-conformities.Any major non-conformity shall be corrected within 2 weeks. In case, if the non-conformityis of a very serious /damaging/hazardous nature, such activity/activities shall be stoppedforthwith as per the written instructions/stop memo by the audit team. For major nonconformity, the audit team shall make a second visit to inspect and ensure compliance afterthe corrective measures are undertaken. Minor non-conformities are to be corrected within 2 weeks and compliance report shall besubmitted to the audit tea. A follow up visit is not required in the case of non-conformities.HOUSEKEEPINGGood housekeeping is one of the important elements of accident prevention programmes. Itshould be planned at the beginning of the job and carefully supervised until the final cleanup and handing over of the site.It is recommended to have a regular clean up in all the job sites. However, housekeepingshould be the concern of all workers, supervisors and engineers in their area of workingand not left for the cleanup crew. In any case, housekeeping should be a part of dailyroutine with clean up being continuous procedure. It must be made clear to everyoneincluding the workers that housekeeping and clearing of debris in their area of work is theresponsibility of the workers working in that area.The following guidelines have to be followed for maintaining good housekeeping practice: All materials should be maintained in neat stockpiles with well laid aisles andwalkways for ease of access. There shall not be any projections in the walkways. Debris from the floors shall be removed and collected by suitable chutes and skips.When the skip is full, debris shall be disposed off into the designated dumpingarea. Loose materials, scrap, tools etc. shall not be allowed lying in the working areasespecially in the vicinity of ladders, ramps, stairs etc. This is more important atheights where loose materials are liable to fall down. Spilt oil and grease should beremoved immediately. Protruding nails is wooden pieces is a chronic problem in sites of civil workconstruction. Every worker need to be made aware that such pieces will injure theworkers themselves so that they will not throw such wooden pieces carelesslyaround their work space. Instead they should retrieve protruding nails and stackthe materials in designated place. Wooden scrap yard should be well away from any
Z Reporting of Near Misses/Accidents/ Dangerous Occurrences 22 Annexes Annexure -1 A Typical HS Policy 23 Annexure -II General Site H.S. Rules & Regulations 23 Annexure -III Near Miss Incident Rep ort 24 Annexure -IV Form XIV -Report of Accidents and Dangerous Occurrences 25 Annexure -V Accident Investigation Report 28