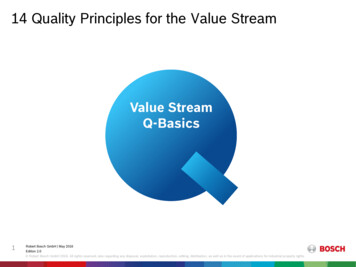
Transcription
14 Quality Principles for the Value StreamValue StreamQ-Basics1Robert Bosch GmbH May 2016Edition 2.0 Robert Bosch GmbH 2016. All rights reserved, also regarding any disposal, exploitation, reproduction, editing, distribution, as well as in the event of applications for industrial property rights.
Value Stream Q-BasicsWe wantour customersto be satisfied!2Robert Bosch GmbH May 2016Edition 2.0 Robert Bosch GmbH 2016. All rights reserved, also regarding any disposal, exploitation, reproduction, editing, distribution, as well as in the event of applications for industrial property rights.
Principle 1Stop SignCustomer complaints are communicatedwithin the production site and, if possible,displayed directly at the station in question.Using problem-solving techniques, they areprocessed in a fast and systematic manner.The supply chain is promptly informed.3Robert Bosch GmbH May 2016Edition 2.0 Robert Bosch GmbH 2016. All rights reserved, also regarding any disposal, exploitation, reproduction, editing, distribution, as well as in the event of applications for industrial property rights.
Principle 1Stop SignA STOP sign process with all of the 8D elements isdisplayed on the shop floor.A standard review process involving theproduction/logistics management and qualitymanagement takes place.The decision to end the STOP sign process is taken byproduction/logistics management after a review of themeasures’ effectiveness.It is necessary to ensure that customer complaints arecommunicated quickly over the entire supply chain fromsupplier to customer.4Robert Bosch GmbH May 2016Edition 2.0 Robert Bosch GmbH 2016. All rights reserved, also regarding any disposal, exploitation, reproduction, editing, distribution, as well as in the event of applications for industrial property rights.
Principle 2Andon CordIn the event of deviations in quality or ifcontrol limits are exceeded in the valuestream (source, make, deliver), the employeeneeds to stop the process or escalate.5Robert Bosch GmbH May 2016Edition 2.0 Robert Bosch GmbH 2016. All rights reserved, also regarding any disposal, exploitation, reproduction, editing, distribution, as well as in the event of applications for industrial property rights.
Principle 2Andon CordThere is a systematics (e.g. Andon cord, blocking/escalation process, reaction plan) in place that allowsthe operator, if he notices deviations, to choose toprevent the passing-on / further processing of parts (bystopping/blocking) and to escalate immediately.Deviations can occur if control limits are exceeded, andalso based on subjective observations (for example, thepower screwdriver is not running smoothly, material hasbeen funneled into the incorrect chute, or the associateis not working to the standards set, label badly readableor incomplete).After stopping the system there needs to be a welldefined process governing the restarting and release ofthe system by shop floor management.6Robert Bosch GmbH May 2016Edition 2.0 Robert Bosch GmbH 2016. All rights reserved, also regarding any disposal, exploitation, reproduction, editing, distribution, as well as in the event of applications for industrial property rights.
Principle 3InstructionsSafety, health, production, and inspectioninstructions are complied with.5S standards are put in place and observed.7Robert Bosch GmbH May 2016Edition 2.0 Robert Bosch GmbH 2016. All rights reserved, also regarding any disposal, exploitation, reproduction, editing, distribution, as well as in the event of applications for industrial property rights.
Principle 3InstructionsThe work, production and inspection instructions areclearly visible at every work place. A consistent set ofsymbols is available. If appropriate, the right/left handmovement becomes evident from the instruction. Thefailure modes from the FMEA and special characteristicsfrom the control plan are taken into account. Detailedphotos support the process.There is a feedback loop in place that ensures theconsistency of the control plan, FMEA, and directions.Health and safety instructions are carried out accordingto the plan. Participation is compulsory and will bedocumented.All deviations regarding safety, work, production andinspection instructions or safety and health briefingsshall be resolved using the 8D method.8Robert Bosch GmbH May 2016Edition 2.0 Robert Bosch GmbH 2016. All rights reserved, also regarding any disposal, exploitation, reproduction, editing, distribution, as well as in the event of applications for industrial property rights.
Principle 4Process ParametersThe target values/tolerances for allstated process parameters are observed.9Robert Bosch GmbH May 2016Edition 2.0 Robert Bosch GmbH 2016. All rights reserved, also regarding any disposal, exploitation, reproduction, editing, distribution, as well as in the event of applications for industrial property rights.
Principle 4Process ParametersAll process parameters (e.g. press-in force, maximumstorage time) that affect product quality are clearlydefined and systematically checked on basis of thecontrol plan. All required inspection criteria areimplemented according to specification.Process validations are performed to determine whethertarget values/tolerances of the defined parameters havebeen observed. Deviations are systematically recordedand eliminated permanently.10Robert Bosch GmbH May 2016Edition 2.0 Robert Bosch GmbH 2016. All rights reserved, also regarding any disposal, exploitation, reproduction, editing, distribution, as well as in the event of applications for industrial property rights.
Principle 5Measurement/Test EquipmentMeasuring and test equipment is defined,and monitoring intervals are observed.11Robert Bosch GmbH May 2016Edition 2.0 Robert Bosch GmbH 2016. All rights reserved, also regarding any disposal, exploitation, reproduction, editing, distribution, as well as in the event of applications for industrial property rights.
Principle 5Measurement/Test EquipmentThe type of measuring and test equipment (e.g. gages,scanners) incl. auxiliary means and its uses is definedfor all processes in the control plans.All measuring and test equipment is calibrated and onlyutilized within the permissible inspection interval.The inspection status of the measuring and testequipment is recognizable at its place of usage (e.g.marked by inspection certificate sticker, tag).In case of suspected malfunctions/damages this has tobe notified.12Robert Bosch GmbH May 2016Edition 2.0 Robert Bosch GmbH 2016. All rights reserved, also regarding any disposal, exploitation, reproduction, editing, distribution, as well as in the event of applications for industrial property rights.
Principle 6Check the CheckerThe “check the checker” principle is applied,and the “checker’s” suitability is ensured.13Robert Bosch GmbH May 2016Edition 2.0 Robert Bosch GmbH 2016. All rights reserved, also regarding any disposal, exploitation, reproduction, editing, distribution, as well as in the event of applications for industrial property rights.
Principle 6Check the CheckerThe suitability of processes used to prevent or detecterrors (e.g. camera-monitored processes, sensor-basedmeasurements, inspection processes, scanning oflabels) needs to be checked according to a predefinedstandard.Possible errors, such as loading the incorrect camerasoftware/testing program or incorrect MAE softwareversions/updates, entry of wrong inspection parameters,or improper sensor calibration, need to be prevented bycarrying out the inspection. These inspection processes,need to be evaluated using appropriate methods (e.g.FMEA).Check-the-Checker-parts are included in the control ofinspection measurement and test equipment.Generally speaking, mistake-proofing is alwayspreferable to error detection (e.g. Poka Yoke).14Robert Bosch GmbH May 2016Edition 2.0 Robert Bosch GmbH 2016. All rights reserved, also regarding any disposal, exploitation, reproduction, editing, distribution, as well as in the event of applications for industrial property rights.
Principle 7Total Productive MaintenanceA maintenance standard is installed andobserved at every station.15Robert Bosch GmbH May 2016Edition 2.0 Robert Bosch GmbH 2016. All rights reserved, also regarding any disposal, exploitation, reproduction, editing, distribution, as well as in the event of applications for industrial property rights.
Principle 7Total Productive MaintenanceThe four-pillar TPM model, particularly the autonomousand preventative maintenance, is instituted at everymachine, device, facility. This contains both the rolesand responsibilities for production and the supportingareas.Systematic damage and dirt built-up on machinery anddevice components (e.g. workpiece carriers, storagefacilities, stackers) need to be consistently analyzed,recognized, and remedied.The restart after maintenance (see principle 9), has toconsider potential influences on product quality.16Robert Bosch GmbH May 2016Edition 2.0 Robert Bosch GmbH 2016. All rights reserved, also regarding any disposal, exploitation, reproduction, editing, distribution, as well as in the event of applications for industrial property rights.
Principle 8ToolsEach tool has a defined service life; thecurrent status must be recognizable.A quality evaluation must be carried outduring installation, removal or disassembly.17Robert Bosch GmbH May 2016Edition 2.0 Robert Bosch GmbH 2016. All rights reserved, also regarding any disposal, exploitation, reproduction, editing, distribution, as well as in the event of applications for industrial property rights.
Principle 8ToolsWear-prone tools with influence on product quality (e.g.processing, assembly, molding tools, workpiecefixtures/carriers) have been recorded and are controlled(e.g. defined service lives, control on basis of productcharacteristics, inspection during maintenance).A warning system promptly displays when tools need tobe replaced or serviced.Each tool needs to be inspected when installed,removed or disassembled to check for recognizableabnormalities (e.g. damage/wear and tear). In case ofdeviations, it is necessary to follow measures to ensureproduct quality is maintained.18Robert Bosch GmbH May 2016Edition 2.0 Robert Bosch GmbH 2016. All rights reserved, also regarding any disposal, exploitation, reproduction, editing, distribution, as well as in the event of applications for industrial property rights.
Principle 9RestartRestart after disruptions is clearly regulatedfor all machinery and equipment.19Robert Bosch GmbH May 2016Edition 2.0 Robert Bosch GmbH 2016. All rights reserved, also regarding any disposal, exploitation, reproduction, editing, distribution, as well as in the event of applications for industrial property rights.
Principle 9RestartEach disruption to the continuous production process(tool change, set-up, break, shift change, maintenance,power failure, upgrade, MAE software update,parameter changes) presents a potential risk to quality.A predefined standard for post-restart is thereforenecessary. This should detail how to deal with productsin the process after a disruption.All devices have been inspected according to a definedstandard for quality risks in connection with disruptions(for example, an unplanned disruption to the weldingprocess, the injection molding process stopsunexpectedly, a product remains in thermal treatment fortoo long, the silicone bead is exposed to the air for toolong). The standard also includes the analysis of criticalwear parts (for example, drill bits or welding electrodes).Following longer disruptions (e.g. station upgrade,control software update), it is necessary to newlyrelease the process.Set-up processes, need to be evaluated usingappropriate methods (e.g. FMEA).20Robert Bosch GmbH May 2016Edition 2.0 Robert Bosch GmbH 2016. All rights reserved, also regarding any disposal, exploitation, reproduction, editing, distribution, as well as in the event of applications for industrial property rights.
Principle 10LabelingProducts and containers are labeledaccording to the set standard.21Robert Bosch GmbH May 2016Edition 2.0 Robert Bosch GmbH 2016. All rights reserved, also regarding any disposal, exploitation, reproduction, editing, distribution, as well as in the event of applications for industrial property rights.
Principle 10LabelingOutside the production flow:White card with a red diagonal stripe: Product blocked;Green card: Product after additional test back inproduction flow and in good condition;Yellow card: Product for rework;Red card: Product is scrap;White card: Product in good condition. Rejected parts in the red box (scrap container). Red boxes must be secured against unintended access(e.g. by locking them, covering, spatial separation,covering during transport).In the entire value stream products must alwayshave a clear status. Therefore, a consistent identification/labeling concept at the production site andadherence to the following rules are necessary.Within the production flow: Filled boxes must always be labeled(e.g. card, sticker, RFID).22 Containers for rejects must be emptied in line withstandards and the parts must be analyzed. Parts at the analysis station are spatially separated fromthe production flow and clearly identified. Only parts with the same status in the same container No good parts in the red box. A blocking process for production and logistics is defined. Products are protected against environmental influences(e.g. contamination) in line with regulations.Robert Bosch GmbH May 2016Edition 2.0 Robert Bosch GmbH 2016. All rights reserved, also regarding any disposal, exploitation, reproduction, editing, distribution, as well as in the event of applications for industrial property rights.
Principle 11Rework / ScrapThe handling of rejected parts and thoseto be reworked is clearly regulated.23Robert Bosch GmbH M
Robert Bosch GmbH May 2016 Edition 2.0 Robert Bosch GmbH 2016. All rights reserved, also regarding any disposal, exploitation, reproduction, editing .