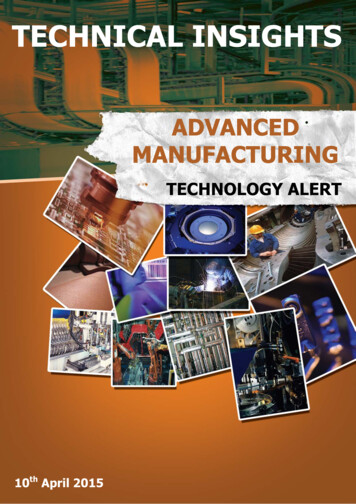
Transcription
TECHNICAL INSIGHTSTECHNOLOGY ALERT10th April 2015
Advanced Manufacturing Technology Alert1. COLLABORATIVE ROBOTS FOR INDUSTRIAL APPLICATIONS2. NOVEL METHOD TO PRODUCE MORE EFFICIENT THERMOELECTRICMATERIALS3. INNOVATIVE PROCESS TO PRODUCE LESS EXPENSIVE GALLIUMARSENIDE ELECTRONIC DEVICES4. PATENT ANALYSIS OF SINTERING TECHNOLOGIES1. COLLABORATIVE ROBOTS FOR INDUSTRIAL tiesinmanufacturingandautomation applications. However, one of the major challenges associated withthese robots is that they cannot always be used for high precision tasks. Whilecollaborative robots have facilitated high performance automation and interactiveuser experience, they still are not used for a wide range of adaptive tasks.Another challenge is that they may not be effectively used for a wide range oftasks, while maintaining the requisite critical flexibility and safety. Many researchand developmental efforts across the globe are focused on extending theapplications of collaborative robots.One such effort has resulted in the development of a flexible collaborativerobot by Rethink Robotics, USA. The robot, commercialized under the name,Sawyer , is a single-arm, high-performance robot. Mainly intended for machinetending, circuit board testing, and other precise tasks, the developed robot can beused in automation tasks for which common industrial robots are not fit, as wellas for precise repetitive tasks.The lightweight nature of the robot helps in easy maneuverability in tightspaces. The robot also features a 4kg (8.8 lb) payload, with around 7 degrees offreedom and a 1-meter reach. One of the distinctive features of the robot is thatit possesses high-resolution force sensing embedded at each joint. This helps incompliant motion control, enabling Sawyer to “feel” its way through obstacles andfixtures in machines and allows it to function in semi-structured environments.This feature of adaptive precision can be considered unique in robotics industry.Furthermore, elastic actuators used in Sawyer use S-shaped springs made of 2015 Frost & Sullivan1
Advanced Manufacturing Technology Alerttitanium. Sawyer’s arm was made smaller, due to the spring design and havingcables run through the joint).The robot also possesses an embedded vision system, including a camerain its head; this facilitates easy performance of tasks that require a wide view. Itis also equipped with a Cognex camera with a built-in light source for precisionvision applications. This also facilitates the Robot Positioning System for dynamicre-orientation and can help in supporting advanced features and upgrades, suchas, barcode scanning, and object recognition, over a period of time. The robotruns on the ROS-based software platform called Intera and features an interactivecontrol system that will help in programming the robot, only once, for effectiveoperations.The company has partnered with Jabil, an electronics product company, forfield testing and early adoption of the developed robot. The company believesthat Sawyer can help in leveraging the best of both humans and machines tooptimize productivity. The robot has been undergoing field testing in NorthAmerica, Europe, China, and Japan. Sawyer is slated for limited availabilityrelease during this summer, and will be targeted for general customer availabilitylater in MA,Marketing02210.Officer,Phone:RethinkRobotics, m. URL: www.rethinkrobotics.comScott Eckert, President and CEO, Rethink Robotics, Inc., 27-43 -mail:seckert@rethinkrobotics.com.2. NOVEL METHOD TO PRODUCE MORE EFFICIENT THERMOELECTRICMATERIALSSince the discovery of the thermoelectric effect, there has been keyimprovement in electricity generation and distribution, in terms of efficiency andin harnessing heat. Over the years, many thermoelectric materials and processeshave been developed to efficiently convert heat to electricity, and the research forachieving higher efficiency in new thermoelectric (TE) materials and theirproduction methods still takes the center stage. 2015 Frost & Sullivan2
Advanced Manufacturing Technology AlertThe initial foundation for development of TE devices was laid in 1834,when Jean Charles Athanase Peltier, a French physicist, found out an essentialconcept for TE temperature control. Since then, TE devices are known as Peltierdevices. Although there has been a constant evolution of TE devices, theirefficiency is less in comparison with classic compressor/ evaporation cooling.During 1960s, alloys of bismuth telluride (Bi 2Te3) or antimony telluride(Sb2Te3) were used to make Peltier devices. These devices had peak efficiency(zT) of 1.1. The alloy technology has seen cumulative growth since then forapplication in Peltier devices.A research team consisting of members from research institutes in SouthKorea and USA has established a new production method for producing anadvanced alloy to be used in thermoelectric devices. The new method is scalableand produces thermoelectric materials two times more efficient than the currentlyavailable materials. This new improved efficiency promises an array of frigeration,andtransportation.This new method of producing highly efficient thermoelectric materials wasdeveloped by researchers from the IBS Center for Integrated NanostructurePhysics, Samsung Advanced Institute of Technology, the department of nanoapplied engineering at Kangwon National University, the department of energyscience at Sungkyunkwan University, all from South Korea, and the materialsscience department at the California Institute of Technology, USA.The metals used in making TE alloys usually have extremely high meltingpoints, which makes it difficult to create alloys by melting the metals. Instead,small metal granules are joined together using pressure by a process known assintering. The research team used a similar process to create an alloy ofantimony, bismuth, and telluride. The team used a specialized sintering processcalled liquid-flow assisted sintering to create the alloy (Bi0.5Sb1.5 Te3) and theconstituent metal granules were held together by melted tellurium.Normally, when Bi0.5Sb1.5 Te3 is fused using traditional sinteringtechnique, the joints between the metal granules, known as grain boundaries, arecoarse and bulky and lower the alloy’s thermal and electrical conductivity.However, the novel liquid-phase sintering technique renders organized andcoordinated grain boundaries. Interestingly, the new aligned grain boundaries or 2015 Frost & Sullivan3
Advanced Manufacturing Technology Alertdislocation array, as the researchers term it, largely increased the thermoelectricconversion efficiency by reducing the thermal conduction in the alloy.Efficiency testingof the Bi0.5Sb1.5 Te3alloy was conducted andoverwhelming results were observed. The efficiency (zT) was nearly double thatof the industry standard and reached 2.01 at 320K. Similarly, compelling resultswere observed when Bi0.5Sb1.5 Te3 was used in Peltier cooler, where the alloysustained a change in temperature of 81K at 300K (26.85 degrees C).The increasing usage of electric vehicles, smart devices, and personalelectronic items demands more efficient systems equipped with self-powergenerating and competent cooling mechanisms. This new process to produce TEmaterials with greater efficiency can open up possibilities to develop moreefficient TE devices. Also, when this process is scaled up, the traditionalrefrigeration systems could be easily replaced by Peltier cooling devices that aremore efficient and robust.Details: Shi Bo Shim, Head of Department of Communications, Institute forBasic Science, 70, Yuseong-daero 1689-gil, Yuseong-gu, Daejeon, Korea, 305811. Phone: 82-42-878-8189. E-mail: sibo@ibs.re.kr3. INNOVATIVE PROCESS TO PRODUCE LESS EXPENSIVE GALLIUMARSENIDE ELECTRONIC DEVICESAlthough many semiconductors have been developed and used since thediscovery of silicon, such devices continue to takecenter stage for variousreasons. One of the main reasons for this is that silicon is available in abundance,which makes it inexpensive and feasible for commercial mass production ofelectronics. But, silicon has shortcomings in certain niche application areas whereother semiconductor materials become prominent. In certain applications, galliumarsenide is preferred for its unique capabilities and is far more superior inefficiency than silicon. In solar cells for instance, gallium arsenide gives a greaterefficiency as its ability to convert light into electricity is much higher than that ofsilicon’. The exclusive properties of gallium arsenide explain its cost, which isgenerally 1000 times that of silicon.Hence, its usage tends to be restricted tospecialized applications. Using gallium arsenide as a substitute for silicon couldhelp change the face of electronics by creating a class of electronic devicessuperior in performance than the existing ones. 2015 Frost & Sullivan4
Advanced Manufacturing Technology AlertWith the aim of creating less expensive and highly-efficient electronics, aresearch team from Stanford University has devised a manufacturing process toproduce gallium arsenide electronic devices, which will drastically bring down thecost of such devices.The circuit manufacturing process, as described by the researchers, beginsby molding the semiconductor into a flat and round-platter, usually called ‘wafer’by the electronic manufacturers. Then, electronic devices are created on top ofthe wafer for various purposes, for example, computer chips, and solar cells.Typically, the circuit-on-wafer is created by flowing gallium arsenide along withother materials on the wafer and condensing them on the wafer.The wafer used for creating the circuit is only a support. The electronics isusually the circuit layer that is formed on the expensive wafer. Hence, reusing thegallium arsenide wafer would reduce the cost of circuits made on them. In itionstothemanufacturing process.In the new process,the wafer is coated with a layer of disposablematerial. Then, the circuit of gallium arsenide is grown on top of the disposablelayer using the typical process of depositing gas. Once the circuit is formed, thedisposable layer is eliminated using laser that leaves the circuitry behind. Later,the circuit is mounted on a stronger support and the gallium arsenide wafer isprepared for making the next batch of circuits by cleaning its surface.The research team reckons that this new process of reusing the waferwould curtail the prices of gallium arsenide circuits to 50 to 100 times than thatof silicon. This value is significantly less expensive than the existing cost. This willattract more interest for further research in gallium arsenide electronics.Silicon became an inevitable choice for the electronics industry, in largepart, because it is available at an inexpensive cost. The cost of silicon was notjust driven by its abundant availability but also by the competition among variouselectronics manufacturers, who wanted to capture the electronics market. Thisnew process of producing less expensive gallium arsenide electronics will paveway for more research and development in this space. Clearly, gallium arsenideelectronics has more dominance in terms of performance and efficiency,especially in solar energy generation sector. 2015 Frost & Sullivan5
Advanced Manufacturing Technology AlertDetails: Dr. Bruce Clemens, Walter B. Reinhold Professor in the School ofEngineering and Professor of Photon Science, Stanford University, 450 Serra Mall,Stanford, CA 94305. Phone: 1-650-725-7455. E-mail: bmc@stanford.edu4. PATENT ANALYSIS OF SINTERING TECHNOLOGIESSintering is a process by which materials are joined or compacted to forma solid mass by heating the materials. Usually, in sintering, materials suchplastics, metals, and ceramic are taken in powdered form. Generally, thematerials are heated in temperatures less than their melting points with orwithout applied pressure. Sintering, in comparison to many other joiningtechniques, has many advantages. Since the materials are taken in powder form,the joints are usually less porous. Also, sintering boosts some properties of thefinal product such as its strength, thermal and electrical conductivity, ductility,and so on. This process is highly desired in ceramic manufacturing. Withadvances in technology, sintering of various forms has been developed, such as,electric current assisted sintering, spark plasma sintering, pressure-less sinteringand many more.On-going research in the sintering domain seems to be focused moretoward ceramic sintering. A careful look at the latest developments and patents insintering in 2015--from January 2015 to March 2015--reveals that new sinteringmethods are invented to join new materials, particularly in the ceramics industry.The patents also reveal that more intricate techniques are being incorporated intosintering technology to achieve higher precision in the sintered product.Indicative of key trends,a patent assigned toFujian Jiamei GroupCorporation,Sintering Process For Ceramic Sheets (WO/2015/043388), pertains toa new sintering process for ceramic sheets involving controlled kiln temperature.A patent assigned to Nitto Denko Corp., Method and Apparatus For Sintering FlatCeramics (EP/2838867), refers to a process and apparatus for sintering flatceramics using a mesh or lattice.Another interesting invention is shown in apatent assigned to WDT Wolz Dental Technik GMBH, Sintered Insert For ASintering Furnace For The Oxygen-Free(EP/2844412), pertains toSintering of Metal or Ceramic Materiala method of sintering metal or ceramic material,particularly for use in dental technology. 2015 Frost & Sullivan6
Advanced Manufacturing Technology Alert 2015 Frost & Sullivan7
Advanced Manufacturing Technology AlertExhibit 1 illustrates patents related to sintering technologies.Picture Credit: Frost & SullivanBack to TOCTo find out more about Technical Insights and our Alerts, Newsletters,and Research Services, access http://ti.frost.com/To comment on these articles, write to us at tiresearch@frost.comYou can call us at: North America: 1-843.795.8059, London: 44 207 3438352, Chennai: 91-44-42005820, Singapore: 65.6890.0275 2015 Frost & Sullivan8
efficiency is less in comparison with classic compressor/ evaporation cooling. During 1960s, alloys of bismuth telluride (Bi 2 Te 3) or antimony telluride (Sb 2 Te 3) were used to make Peltier devices. These devices had peak efficiency (zT) of 1.1. The alloy technology has seen cumulative growth since then for