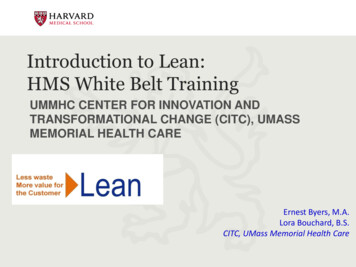
Transcription
Introduction to Lean:HMS White Belt TrainingUMMHC CENTER FOR INNOVATION ANDTRANSFORMATIONAL CHANGE (CITC), UMASSMEMORIAL HEALTH CARESUBTITLEErnest Byers, M.A.Lora Bouchard, B.S.CITC, UMass Memorial Health Care
Learning Objectives Define ‘Value’ for the customer at eachstep Develop eyes for ‘Waste’ Stop Firefighting and get to the root cause Learn Lean tools, countermeasures andthinking to eliminate ‘Waste’ Practice Respect for People & ContinuousImprovementLEAN Community2
Agenda Introduction to LeanºMr. Potato Head Game Round 1 Foundation– Value, Waste Break Intro to Problem Solving, Root Cause Analysisº5S, Visual Management Error Proofing Standard Work & Exercise Cellular Layout, Flow, Pull, A3 Problem SolvingºMr. Potato Head Game Round 4 Value Stream Mapping – Large Projects Idea Systems Break People Pillar – Culture, Respect, Leadership Next StepsMr. Potato Head Game Round 2 º Mr. Potato Head Game Round 3Process Mapping vs. Value Streams Single-piece flow & Balancing Work Lunch (12:00 to 12:30)LEAN Community3
Introduction Ground rules Introductions. Please discuss at your tables ingroups of 2 or 3ºAn opportunity for improvement within your departmentLEAN Community4
“Going Lean in Healthcare” Discuss pre-class reading (IHI, 2005)1.What is meant by “Lean Thinking” and where can Lean be applied?2.What must leaders do for Lean principles to take root?3.What influences behavior?4.What are some challenges to becoming Lean?5.What’s the best way to ensure a clear vision and understanding?LEAN Community5
What is Lean?“Lean” is both an approach to work & anorganizational philosophy A set of methodologies designed to solve organizationalproblems and improve results. Culture of continuous improvement, and peopledevelopment.Lean MeanOr downsizing, or outsourcing, or working faster or just commonsenseLEAN Community6
Why Lean?ºQualityººººººEfficiencyReduces customer wait timesSatisfactionReduces errorsStandardizes workflowReduces unnecessary workload, duplicative work and/orreworkImproves hand-offs“At Toyota we get brilliant resultsIncreases productivityfrom average people managing aReduces inventorybrilliant process.Others get average results frombrilliant people managing brokenprocesses.”--The Toyota Motor CompanyPeople are not the cause of problems, bad processes are.LEAN Community7
Discussion How might Lean fit with organizational initiatives atHMS? Think, pair, share – 1 min, 5mins, 10minsLEAN Community8
5 Guiding Principles of LeanSpecify value from the perspectiveof the customerAlways competeagainst perfectionnot just yourcurrent competitionVALUEPERFECTIONA system in whichnothing is produced by asupplier until thecustomer signals a needCharacterize the ValueStream (set of activities)for each product /process while removingwaste.PULLVALUESTREAMFLOWProgressive achievementof value creating steps withminimal queues and nostoppages or backflows ofproduct, information orservicesLEAN Community9
Where did Lean come from?And how did we get from automobiles to all industries?LEAN Community10
Where did “Lean” come from?1920s - 30s1940sTime & MotionF. TaylorInterchang-ablePartsE. WhitneyMass production World War IIAmericanSupermarkets (A&P)Industries: Manufacturing Services Retail Healthcare Others“Lean”90s - presentJ. Womack1980s – 90s11“Just intime”Toyota Production System(TPS)1940sLEAN Community11
Exercise Mr. Potato Head GameLEAN Community12
Mr. Potato Head - The Plan-Do-Study-Act GameºYour team is the DNA Sequencing Research TeamºThe goal of the game is to accurately assemble asmany Potato Heads (mini genomes) as possible in 4minutesºExplain the metricsLEAN Community13
Game RulesOnly 2 people from each team can put the PotatoºHead body parts on the Potato HeadAll other team members will give the correct piecesºto the “Assemblers”One person on the team will be the “Inspector” andºcheck Does the Potato Head match the picture? How many Mr. Potato Heads are completed?LEAN Community14
ASSEMBLE YOUR TEAMSºChoose your 2 “Assemblers”ºChoose your InspectorºWhen we start: Open the bag, find the photos, fix your“genomes”ºWhen we end: Inspect your “genomes”LEAN Community15
4 een-stopwatch/ºWhy did we pick 4 minutes? If it takes 20-30 seconds to correctly assemble one PotatoHead with no waste in the system, it should take maximumof 5 minutes to assemble all 9 if only 1 assembler. Youhave an entire team!ºGuinness Book of World Records’ fastest assembly of a Mr.Potato Head: Samet Durmaz of Turkey.6.62 seconds!LEAN Community16
Metrics ScorecardRound 1Round 2Round 3Round 4# Complete# Errors# CorrectLEAN Community17
Mr. Potato Head - DebriefºTotal Complete, # Errors, # CorrectºWhat did you notice?ºWhy?ºWhat will you try next time? Why?LEAN Community18
5 Guiding Principles of LeanSpecify value from the perspectiveof thecustomerAlways competeagainst perfectionnot just yourcurrent competitionPERFECTIONA system in whichnothing is produced by asupplier until thecustomer signals a needCharacterize the ValueStream (set of activities)for each product /process while sive achievementof value creating steps withminimal queues and nostoppages or backflows ofproduct, information orservicesLEAN Community19
Types of WorkValue-Added WorkActivities that transform material ,information, or people into something thatthe customer cares about ( )o Orientation, approving travelRequired Non-ValueNo value in the customer’s eyes, butcan’t be avoidedoDebarment form, Regulatory tasksPure waste –Non ValueConsumes resources but doesn’t add value.o Looking for data/informationo Staff waitingo Re-work, redundant paperworkValueNon-Value- AddedAdded(Required)Non ValueAdded,Pure wasteLEAN Community20
Pizza – What are you willing to pay for?Yes NoWaste Non-Value-Added Not Willing to Pay For( )DoughSauceToppingsToppings drop on thefloorEnergy for ovensEnergy for ovens left onover nightLabor for the deliverypersonTravel expenses fordeliveryDaily car washes fordelivery person’s carLong distance phonecharges to the cooksbookieLEAN Community21
Eliminate Waste – Increase ValueObserve that 2 Things are ALWAYS Happening. . .Value1. Things that should be doneNon-Value2. Things that should not be doneBeforeReduce wasteAfter OrValue Added WorkIncrease valueLead TimeNon Value Added Work“It” Either Adds Value or Does NotLEAN Community22
DThe “8 Wastes”OWNDefectsOverproductionWaitingNot UtilizingEmployeesErrorsDoing more than neededWaiting or DelaysIdeas and skills not usedWrong coding on requisitions,Incomplete/incorrect info. forGrants submissionExtra reports, Unnecessary info.sent automatically, printing inadvanceWaiting for information, report,answer, approvals, signatures,etc.Not recognizing employees asbest source for fixing ovement of people ormaterialToo much materialMovement by workersRe-dosBuying in bulk, stocking tonerwhen we get next day delivery,more servers than required,supplies, equipmentSearching for supplies, itemsneeded not close by, alwayslooking in shared drivesUnnecessary approvals,rework, same data required inmultiple places or systemsTransport between campuses,hand delivering invoices to A/P,Movement of files to differentlocations
Toast Kaizen, Greater BostonManufacturing Partnership “Eyes for Waste”LEAN Community24
Waste Walk FormWaste WalksDepartment: Names of department or peopleDate of Waste Walk : dateFor a process in your area , identify where waste may exist and think of one or more ways to reduce or eliminate them. Attendeesshould include a lean expert, frontline staff and supervisorType of WasteSpecific Waste5 WhysWays to Reduce(use Fishbone template if needed)(e.g. 5S, error proofing, visual controls)1Defects2Over-Production121Waiting2Not tion2ExtraProcessing12Supervisor Approval for Countermeasures:LEAN Community Date:25
Waste Walk Video Use the Waste Walk form on the next page and in yourhandout to identify waste you find in the following video. On the Waste Walk form, list the waste by category (e.g.Waiting, Transport / Motion, Inventory, Defects, etc.) We’ll discuss your findings after the video.LEAN Community26
ExerciseThink, Pair, Share Identify 3 examples of Waste – 1min Share with those next to you – 2minLEAN Community27
Gemba At the site Where the work is happening The office area The lab workbenchLEAN Community28
Muda, Mura, Muri Muda – Activity or process that does not add value(8 wastes) Mura – Unevenness or inconsistency Muri – Overburden, unneccesary stress toemployee and processes“Without standardsthere can be noKaizen.”-Taiichi OhnoLEAN Community29
BreakBack in10 minutesLEAN Community30
The Toyota WayTrue NorthBest Quality – Low Cost – Shortest Lead TimeBest Safety – Highest MoraleContinuousImprovementRespect forPeoplePDSA Learning CyclesLEAN Community31
Lean House Model:Just in TimeWasteSystem Goal*PeopleBuilt in QualityContinuousFlow(Cells, Balance)Produce onlywhatis needed,when it isneededErrorProofingCultureJidokaPull Systems(WIP Limits)VisualManagementQuickSetupsTotal Productive MaintenanceNever passdefects to nextProcessFlexible,HighlyMotivatedPeopleSPC & 6σStop the Line!(Andon)Design forAssembly & MfgFoundation of Operational StabilityValue Stream MappingWaste EliminationAdapted by UMMHC from J. Liker, 2002 and AltarumProblem Solving5S & Visual ManagementMetricsStandard WorkLEAN Community32
Introduction to Problem SolvingLEAN Community33
Multiple Problem Solving ause(cause is known or could easily be identified,i.e. 5 why’s)FirefightingA3 Problem SolvingLEAN Community34
What does “Kaizen” mean? “ a system of continuous improvement in quality,technology, processes, company culture, productivity, safetyand leadership that involves every employee and theidentification and elimination of waste.” Literal Translation: “to become good through change” It is a Daily Process of improving at the front line In a kaizen “event”, we know the problems and root causes,but are not sure yet of the best countermeasures. We figurethat out, and implement by the end of the event.LEAN Community35
The Kaizen “Event” Can be 1-4hours,1-2 days, atmost 5 daysLEAN Community36
Lean Problem Solving1.Define the problem clearly. Scope.2.Understand the problem, deeply. Go see.3.Find the root cause(s).4.Only then, design countermeasures, andimplement.I don’t have time 5.Track analyze your results. Measure before andafter.6.Try again, until goal is achieved.LEAN Community37
Is there a Root Cause to Waste? What is meant by “root cause”?ºº Why do we pursue the root cause?ºº Underlying reason, usually not obvious. The “real” problem.Vs. “contributing” cause, or symptoms.Root cause is solvable and will result in fixing the problem byapplying a countermeasureSolving contributing causes or symptoms won’t eliminate theproblem (the Waste).Root Cause Analysis Tool – 5 Why’sºBreaks down each reason or cause until further breakdown isnot possibleLEAN Community38
How to Find the Root Cause? What is the real problem? What is the root cause?––Ask why 5 timesPurpose – to discover the root causeLEAN Community39
“5 Whys” ExampleBASED ON A TRUE STORYHow many of you have been to Washington, DC?How many of you have visited the Jefferson Memorial? Please play along .A few years ago the National Park Service recognized that the marble on the JeffersonMemorial was deteriorating faster than the other memorials.Audience . “Why?”It was from all the power washing they had to do more than on theother monuments.Audience .“Why so much power washing?”LEAN Community40
“5 Whys” ExampleBecause of all the bird droppingsAudience .“Why so many bird droppings?”The birds were being attracted to eat all the spiders Audience .“Why so many spiders?”There were so many spiders, because they were attracted to the littleblack insects.Audience .“Why so many tiny black insects?”LEAN Community41
“5 Whys” ExampleThe little insects were attracted by the lights .Finally .an actionable cause .In fact, they found that for no good reason, the lights at thismemorial were on several hours longer than at other memorials.The park service reduced the time of the lights, the problem gotbetter, and over 200,000 was saved on maintenance expenses.LEAN Community42
Fishbone DiagramDate: date MaterialsMethodMain cause – Why?Sub-Cause 1) - Why?Sub-Cause 1.a) – Why?Main CauseMain cause – Why?Sub-Cause 1.b) – Why?Root CauseSub-Cause 1.b.i) – Why?Root CauseEffectMain Cause – Why?Main Cause – why?Sub-Cause 1) – Why?Root CauseRoot CauseSub-Cause 2) – Why?Main CauseSub-Cause 2.a) – Why?Root CauseMan/PeopleMachineLEAN CommunityCITC Template, UMMMC – UMMS Nov 25, 201443
PROBLEM STATEMENT:IT Purchase requests are taking more than 7 business days to process and approve. Requestsare submitted without the appropriate information resulting in approval delays.LEAN Community44
Exercise Now it’s your turn Pick one identified waste from the Mr. Potato HeadGame and do a root cause analysis using 5 whysLEAN Community45
Mr. Potato Head - The Plan-Do-Study-Act GameºººRound 2Same rulesSwitch bags!LEAN Community46
4 een-stopwatch/ºWhy did we pick 4 minutes? If it takes 20-30 seconds to correctly assemble one PotatoHead with no waste in the system, it should take maximumof 5 minutes to assemble all 9 if only 1 assembler. Youhave an entire team!ºGuinness Book of World Records’ fastest assembly of a Mr.Potato Head: Samet Durmaz of Turkey.6.62 seconds!LEAN Community47
Metrics ScorecardRound 1Round 2Round 3Round 4# Complete# Errors# CorrectLEAN Community48
Mr. Potato Head - DebriefºTotal
LEAN Community 2 Learning Objectives Define ‘Value’ for the customer at each step Develop eyes for ‘Waste’ Stop Firefighting and get to the root cause Learn Lean tools, countermeasures and thinking to eliminate ‘Waste’ Practice Respect for People & Continuous Improvement