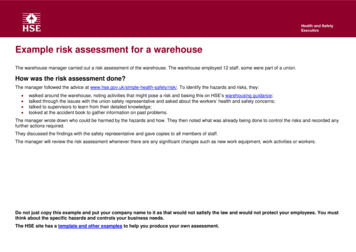
Transcription
Example risk assessment for a warehouseThe warehouse manager carried out a risk assessment of the warehouse. The warehouse employed 12 staff, some were part of a union.How was the risk assessment done?The manager followed the advice at www.hse.gov.uk/simple-health-safety/risk/. To identify the hazards and risks, they: walked around the warehouse, noting activities that might pose a risk and basing this on HSE’s warehousing guidance;talked through the issues with the union safety representative and asked about the workers’ health and safety concerns;talked to supervisors to learn from their detailed knowledge;looked at the accident book to gather information on past problems.The manager wrote down who could be harmed by the hazards and how. They then noted what was already being done to control the risks and recorded anyfurther actions required.They discussed the findings with the safety representative and gave copies to all members of staff.The manager will review the risk assessment whenever there are any significant changes such as new work equipment, work activities or workers.Do not just copy this example and put your company name to it as that would not satisfy the law and would not protect your employees. You mustthink about the specific hazards and controls your business needs.The HSE site has a template and other examples to help you produce your own assessment.
Risk assessmentCompany name: GHI LogisticsAssessment carried out by: JH ReynoldsDate assessment carried out: 3/10/19What are thehazards?Who might beharmed andhow?What are you already doing tocontrol the risks?What further action doyou need to take tocontrol the risks?Who needs to When is thecarry out the actionaction?needed by?DoneFalls from heightStaff could suffersevere or fatalinjuries if they fellwhile climbingracking.All staff are given strict instructionsnever to climb racking – monitored bysupervisors.Share this riskManagerassessment with regularcontractors. Check theirawareness of health andsafety issues and ensurethey give health and safetyinformation to any staffnew to the site.30/10/1930/10/19Staff could suffersevere or fatalinjuries if they fellwhile changinglight bulbs in thehigh ceiling.Proprietary forklift cage used bymaintenance worker for changingbulbs. Cage supplier’s informationshows it is manufactured to standard.Train maintenance workerto check cage is in goodcondition and properlysecured before each use.Manager andmaintenanceworker15/10/1914/10/19Staff or contractorcould suffer severeor fatal injuriesfalling throughNo controls in place.Agree with maintenanceworker that a contractorwill be used for anyaccess to the roof.Manager andmaintenanceworker14/10/1914/10/19
What are thehazards?Who might beharmed andhow?What are you already doing tocontrol the risks?fragile roof lightswhen looking forleaks or repairingthem.Worker falling fromroof of internalwarehouse officeused for storage.Slips, trips andfallsThe internal warehouse roof is loadbearing, has full rails and boardsaround its edge. It has adequatelighting and access is by permanentsteps with a handrail.All staff may suffer Flooring kept dry and qualitysprains ormaintained.fractures if they trip All staff trained to maintain goodover debris or sliphousekeeping standards andon spillages.ensure stock does not project intogangways. Cleaner empties bins and removesloose debris daily. Pallets stored safely in designatedarea. Protective non-slip footwearsupplied and worn.What further action doyou need to take tocontrol the risks?Who needs to When is thecarry out the actionaction?needed by?DoneRequire contractor toprovide an assessmentbefore access is allowed ifany roof work is required.MaintenanceworkerFrom now onPut up ‘fragile roof’ signs,one on each side of thebuilding and at accesspoints to roof.Maintenanceworker17/10/1917/10/19Suitable absorber to bemade available for liquidspills.Supervisor15/10/1914/10/19Staff to be trained to cleanand dry any ra bins to be providedfor waste material nearloading bays.Manager28/10/1928/10/19No further action required.
What are thehazards?Who might beharmed andhow?What are you already doing tocontrol the risks?What further action doyou need to take tocontrol the risks?Who needs to When is thecarry out the actionaction?needed by?Operation of lifttrucksSerious injuries orfatalities can becaused by: All operators trained and competentto use lift truck. Trucks serviced regularly andexamined by suppliers every sixmonths. Drivers instructed to keep keys withthem at all times. System in place for refreshertraining of drivers. Gangways and aisles big enoughfor lift trucks to load and unloadfrom the racking safely. System in place to separatevehicles and pedestrians. Access to warehouse restricted tostaff. Floor condition maintained on aregular basis, housekeepingstandards maintained by cleanerand workforce. Warning signs located around thetraffic route. Trucks have seat belts and rollcages.Supervisor to ensure truckdrivers check trucks eachday before starting.SupervisorFrom now onSeparate pedestrianentrance(s) with protectivebarrier rail to be providednext to roller-shutterdoors.Supervisor7/11/19Housekeeping standardsand floor condition to becovered by a monthlyinspection by managerand brief record kept.ManagerFrom now onStrict requirement thatonly competent driversmay operate lift trucks tobe explained to all staff.Disciplinary action to betaken against anyoneinvolved in breaking thisrule.Manager4/11/19 the vehiclecrashing intoother vehiclesand/or otherobjects; staff and visitorsbeing hit by lifttrucks; objects fallingfrom lift trucksonto staff andvisitors; lift trucks topplingover; people fallingfrom the vehicleor parts of thevehicle; and being crushed bythe mast.Done5/11/194/11/19
What are thehazards?Who might beharmed andhow?What are you already doing tocontrol the risks?What further action doyou need to take tocontrol the risks?Who needs to When is thecarry out the actionaction?needed by?Trafficmovements(deliveries etc)Injuries such asfractures or evenfatalities can becaused by: Floor and traffic routes suitable forthe vehicles using them. Vehicle routes kept free ofobstructions (with spillages beingcleaned up promptly). Parking of cars and vans onlyallowed in marked spaces, wellaway from externaldelivery/dispatch area. Outside area gritted when frosty,snow cleared. Sensible speed limits imposed andkept to. Adequate signage to warn ofhazards. Reversing of delivery vehiclesavoided unless absolutelynecessary. Any reversing that is necessaryshould be overseen by a trainedreversing assistant (banksman).Anyone working in thevicinity of moving vehiclesshould be given trainingand high-visibility clothing.Supervisor staff and visitorsbeing hit byvehicle; people fallingfrom a vehicle orparts of avehicle; and objects fallingfrom vehicle ontostaff and visitors.From now onDone
What are thehazards?Who might beharmed andhow?What are you already doing tocontrol the risks?What further action doyou need to take tocontrol the risks?Who needs to When is thecarry out the actionaction?needed by?Stretch-wrapmachineStaff using themachine. Movingparts can trapfingers, hands,arms etc, causingcrush injuries. Thewhole body mayalso get trappedbetween movingpallet load andfixed structure. Machine is relatively new andinstructions show it meets therelevant guarding standard. Only standard palletised loadswrapped. Emergency stop button provided. Fixed guards on moving parts. Mechanical parts maintainedregularly. Staff trained to use correctly.Keep area aroundmachine unobstructed atall times.MachineoperatorsFrom now onIndicate area aroundmachine using markings influorescent orange-red.MachineoperatorsFrom now onWeekly check on guardingand condition of machine.MachineoperatorsFrom now onDoneStaff can also becut by sharp edgesor scalded by hotparts.Conveyor belt forunloading fromlorriesAs above,particularly wherethe belt meetsrollers. Guards provided for moving parts. Conveyor instructions show itmeets guarding standards. Emergency stop button provided. Regular maintenance.Weekly check on guardingand condition of conveyor.SupervisorFrom now onPortableelectricalequipmentAll staff couldreceive potentiallyfatal electricalshocks or burns ifthey use faultyelectricalequipment. Fixed electrical installations aremaintained to a suitable standardand inspected every five years.Manager to arrange andrecord the six-monthlyinspection and testing ofportable equipment.ManagerFrom now onInstruct staff to reportfaults immediately.Manager andsupervisor15/10/19Rest area:industrial cleaner,kettle and heater15/10/19
What are thehazards?Who might beharmed andhow?What are you already doing tocontrol the risks?What further action doyou need to take tocontrol the risks?Who needs to When is thecarry out the actionaction?needed by?DoneFireIf trapped in thewarehouse, allstaff and visitorscould suffer fromsmoke inhalationor burns whichcould potentiallykill. Building designed with fire-resistingmaterials. Exits/fire exits marked and keptclear. Fire extinguishers well located. Clear access kept at all times to allexits and fire extinguishers. Fire detection and alarm system. Each fire alarm point displaysevacuation procedures. Maintenance contracts forextinguishers and detection/alarmsystem. Annual fire drill and training incorrect use of extinguisher. Cleaner ensures no debris left. Staff trained in good housekeeping.Talk to insurer aboutproviding automaticallyclosing, roller-shutterdoors linked to the firealarm.Manager16/10/19Fumes may irritateeyes, causerespiratoryirritation. Only few vehicles delivering soexposure is limited, which preventsbuild-up of fumes. Drivers not allowed to leaveengines running. Roller-shutter doors and windowskept open, to assist ventilation.No further action required. Cleaner told safe procedures.Rubber gloves used. First-aid facilities (including eyewash) are readily available.Investigate availability ofsafer alternatives forcleaner.Supervisor Batteries charged in designatedbay that is well ventilated. Safesystem of work used whichincludes provision and use ofSupervisor to monitor andensure protectiveequipment is being worn.Supervisor Bulk storage ofeasily burntmaterials Ignited throughelectrical fault,batteryrecharging etcHazardoussubstancesVehicle exhaustfumesBleach andcleaning fluidsRecharging offorklift truckbatteries –potential explosionthrough release ofMay irritatecleaner’s skin, orvapour cause eyeirritation breathingdifficulties.Burns or fracturesfrom materialejected couldaffect any worker16/10/19
What are thehazards?Who might beharmed andhow?What are you already doing tocontrol the risks?What further action doyou need to take tocontrol the risks?hydrogen, spillageof acidnearby.LightingPoor lighting islikely to result inhigher levels ofwork error andaccidents. Good quality lighting providedthroughout the warehouse. Stacking of materials in warehouseon top of racking is restricted toavoid blocking light and creatingshadows. Cleaner checks that light units areoperating and are replaced byelectrician when necessary. Floodlighting in the external area.No further action required.Hygiene/comfortAll staff couldsuffer varieddiscomfort, egbeing too hot/cold. Heated rest area provided with hotand cold water. Area kept clean. Lockers availablefor staff members’ belongings. Toilets a short walk away, cleaneddaily.No further action required.goggles and gloves. Potentialsources of ignition controlled.Published by the Health and Safety Executive 11/19Who needs to When is thecarry out the actionaction?needed by?Done
machine instructions show it meets the Staff using the machine. Moving parts can trap fingers, hands, arms etc, causing crush injuries. The whole body may also get trapped between moving pallet load and fixed structure. Staff can also be cut by sharp edges or scalded by hot parts. Machine is relatively new and relevant guarding standard.