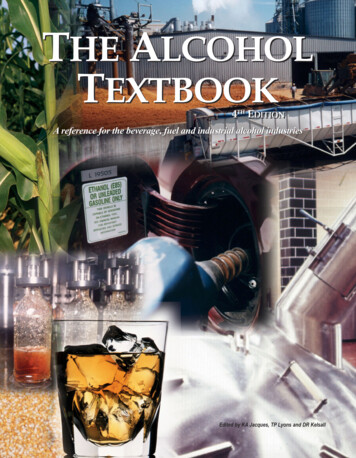
Transcription
THE ALCOHOLTEXTBOOKTH44THEEDITIONDITIONA reference for the beverage, fuel and industrial alcohol industriesEdited by KA Jacques, TP Lyons and DR Kelsall
Foreword iiiThe Alcohol Textbook4th EditionA reference for the beverage, fuel and industrial alcohol industriesK.A. Jacques, PhDT.P. Lyons, PhDD.R. Kelsall
iv T.P. LyonsNottingham University PressManor Farm, Main Street, ThrumptonNottingham, NG11 0AX, United KingdomNOTTINGHAMPublished by Nottingham University Press (2nd Edition) 1995Third edition published 1999Fourth edition published 2003 Alltech Inc 2003All rights reserved. No part of this publicationmay be reproduced in any material form(including photocopying or storing in anymedium by electronic means and whether or nottransiently or incidentally to some other use ofthis publication) without the written permissionof the copyright holder except in accordance withthe provisions of the Copyright, Designs andPatents Act 1988. Applications for the copyrightholder’s written permission to reproduce any partof this publication should be addressed to the publishers.ISBN 1-897676-13-1Page layout and design by Nottingham University Press, NottinghamPrinted and bound by Bath Press, Bath, England
Foreword vContentsForewordT. Pearse LyonsPresient, Alltech Inc., Nicholasville, Kentucky, USAixEthanol industry today1Ethanol around the world: rapid growth in policies, technology and productionT. Pearse LyonsAlltech Inc., Nicholasville, Kentucky, USA1Raw material handling and processing2Grain dry milling and cooking procedures: extracting sugars in preparation forfermentationDave R. Kelsall and T. Pearse LyonsAlltech Inc., Nicholasville, Kentucky, USA93Enzymatic conversion of starch to fermentable sugarsRonan F. PowerNorth American Biosciences Center, Alltech Inc., Nicholasville, Kentucky, USA234Grain handling: a critical aspect of distillery operationDavid J. RadzanowskiAlltech Inc., Nicholasville, Kentucky, USA33Substrates for ethanol production5Lignocellulosics to ethanol: meeting ethanol demand in the futureCharles A. AbbasArcher Daniels Midland, Decatur, Illinois, USA416Ethanol production from cassavaNguyen T.T. VinhThe Research Institute of Brewing, Hanoi, Vietnam597Whey alcohol - a viable outlet for whey?Jack O’SheaAlltech Inc., Dunboyne, County Meath, Ireland658Treatment and fermentation of molasses when making rum-type spiritsRobert PiggotAlltech Inc., Nicholasville, Kentucky, USA75
vi T.P. LyonsYeast and management of fermentation9Understanding yeast fundamentalsInge RussellInternational Centre for Brewing and Distilling, School of Life Sciences,Heriot-Watt University, Edinburgh, UK10Practical management of yeast: conversion of sugars to ethanolDave R. Kelsall and T. Pearse LyonsAlltech Inc., Nicholasville, Kentucky, USA11Continuous fermentation in the fuel alcohol industry:How does the technology affect yeast?W. M. IngledewUniversity of Saskatchewan, Saskatoon, Saskatchewan, Canada12Understanding near infrared spectroscopy and its applications in the distilleryDon Livermore1, Qian Wang 2 and Richard S. Jackson21Hiram Walker & Sons Ltd., Walkerville, Ontario, Canada2Bruker Optics Inc., Billerica, Massachusetts, USA13Emerging biorefineries and biotechnological applications of nonconventionalyeast: now and in the futureCharles A. AbbasArcher Daniels Midland, Decatur, Illinois, USA85121135145171Beverage alcohol production14Production of Scotch and Irish whiskies: their history and evolutionT. Pearse LyonsAlltech Inc., Nicholasville, Kentucky, USA19315Tequila production from agave: historical influences and contemporary processes223Miguel Cedeño CruzTequila Herradura, S.A. de C.V. Ex-Hda San Jose del Refugio Amatitán, Jalisco, México16Production of heavy and light rums: fermentation and maturationRobert PiggotAlltech Inc., Nicholasville, Kentucky, USA24717From pot stills to continuous stills: flavor modification by distillationRobert PiggotAlltech Inc., Nicholasville, Kentucky, USA25518From liqueurs to ‘malternatives’: the art of flavoring and compounding alcoholAndy Head and Becky TimmonsNorth American Biosciences Center, Alltech Inc., Nicholasville, Kentucky, USA265
Foreword vii19Production of American whiskies: bourbon, corn, rye and TennesseeRon RalphRon Ralph & Associates Inc., Louisville, Kentucky, USA275Contamination and hygiene20Bacterial contamination and control in ethanol productionN.V. NarendranathNorth American Biosciences Center, Alltech Inc., Nicholasville, Kentucky, USA21Managing the four Ts of cleaning and sanitizing: time, temperature, titration andturbulenceJim Larson and Joe PowerNorth American Biosciences Center, Alltech Inc., Nicholasville, Kentucky, USA287299Recovery22Ethanol distillation: the fundamentalsP. W. MadsonKATZEN International, Inc., Cincinnati, Ohio, USA31923Development and operation of the molecular sieve: an industry standardR. L. Bibb SwainDelta-T Corporation, Williamsburg, Virginia, USA337Engineering ethanol fermentations2425Water reuse in fuel alcohol plants: effect on fermentationIs a ‘zero discharge’ concept attainable?W. M. IngledewUniversity of Saskatchewan, Saskatoon, Saskatchewan, CanadaUnderstanding energy use and energy users in contemporary ethanol plantsJohn MeredithRo-Tech, Inc., Louisville, Kentucky, USA343355The dryhouse, co-products and the future26Dryhouse design: focusing on reliability and return on investmentJohn MeredithRo-Tech, Inc., Louisville, Kentucky, USA27Ethanol production and the modern livestock feed industry: a relationshipcontinuing to growKate A. JacquesNorth American Biosciences Center, Alltech Inc., Nicholasville, Kentucky, USA363377
viii T.P. Lyons28Biorefineries: the versatile fermentation plants of the futureKarl A. DawsonNorth American Biosciences Center, Alltech Inc., Nicholasville, Kentucky, USA387The Alcohol AlphabetA glossary of terms used in the ethanol-producing industries399Index441
Foreword ixForewordAlcohol production: a traditional process changing rapidlyT. PEARSE LYONSPresident, Alltech Inc., Nicholasville, Kentucky, USAIn its simplest form, alcohol production is theprocess of preparing starch- or sugar-containingraw materials for fermentation by yeast, whichis currently the only microorganism used forconverting sugar into alcohol. The ethanol isthen concentrated and recovered in a processcalled distillation. Though essentially a simpleprocess, making it happen with maximumefficiency on a very large scale is a remarkablecombination of microbiology and engineering.Over the past 25 years progress has been madein virtually all aspects of the process, but whatare the challenges facing alcohol in the future?Beginning with raw material processing, hereare the areas that we feel need to be addressed:Raw material reception and processingDespite many declarations to the contrary, it isvirtually impossible for a distillery to accuratelycalculate true yields. A sampling of grains iseither done in very cursory fashion or not at all.The distiller must see himself first as a processorof grain rather than a producer of alcohol. Hemust know accurately how much starch ispresent in his raw material and he must be ableto measure that immediately. NIR spectroscopyhas much to offer in terms of raw materialapplications; and this topic is detailed in thisvolume. However, if we control the process anduse the appropriate enzymes from solid statefermentation, such as Rhizozyme andAllzyme SSF, which are capable of releasingnot just bound starch but also hemicellulose andcellulose, we can and indeed some plants do,get 2.9 gallons per bushel (116 gallons or 420liters/tonne. In fact, we predict yields of 3.2gallons in the near future. For molasses, theadvent of detranases can ensure maximumyields. Every aspect of cooking and fermentationmust be controlled, however.The cooking processMuch debate exists at the moment regarding thecooking process. It is a sad reflection perhapson our industry that since the pioneering PhDwork by Dr. John Murtagh in 1972 no furtherscientific thesis has been published on cooking.Should grain be finely ground? Should cookinginvolve high temperature α-amylase or shouldan entirely different type of enzyme be used?Often the enzyme selected is one developedbased on experience in the corn wet millingsector, which may be far from ideal for dry millalcohol production.Our industry needs a new enzyme, one tailoredto our specific needs: converting grain tofermentable sugar. Raw materials contain notonly starch, but also hemicellulose (a polymerof 5-carbon sugars) and cellulose. The cookingprocess must be designed to loosen thesematerials such that they release bound starch andalso become available in turn for fermentation.Yeast and fermentationDespite all we know about it, yeast remainsunderrated and misunderstood. It is theworkhorse of the distillery, yet ‘economies’ onquality and quantity of yeast are made; and we
x T.P. ilo RSugarcaneSugarbeetsCO-PRODUCTSWheyCO2DDGSWet cakeSolublesYeastPRIMARY ALCOHOLPOT STILLIrishWhiskeyValue-addedco-productsCONTINUOUS olFuelAlcoholTequilaBourbonBlended WhiskyScotch WhiskyGinVodkaWHITE SPIRITSMATURATION SPIRITSoften force it to grow and operate underunsuitable conditions. As Professor MikeIngledew has pointed out many times, thefermentor is not a garbage can! We must makesure that conditions in fermentation are optimumfor yeast.Like our need for appropriate enzymes, ethanolproduction also requires yeast with higherethanol and temperature tolerance if we are tokeep progressing to higher levels of alcohol inthe fermentor. Today, 17-20% abv is becomingstandard in our industry as we move to hightemperature Thermosacc TM -like yeast. Whenused in combination with enzymes capable ofextracting increasing amounts of sugar, such asthose produced by surface culture fermentation,yeast can bring us to a whole new level.While 23% ethanol by volume in the fermentorwithout loss of performance is possible giventhe right yeast and enzyme combination, it canonly be done by careful management of the socalled stress factors. Factors which, if leftuncontrolled, will prevent the yeast fromperforming. Operating a fermentation at 23%ethanol is totally different than operating adistillery at 8% ethanol. Any minor change,whether in mycotoxin level, salt level or nutrientlevel can have a major impact on performance.Microbial contaminationA distillery is never going to be a sterilefermentation and even those of us who have hadthe good fortune to operate in sterile fermentationconditions know how easily infection can takehold. Since the yeast is a relatively slow-growingmicroorganism compared to most of theinfectious microorganisms (Lactobacillus, etc.),it is critical that we have an arsenal ofantimicrobial agents and effective cleaningproducts and programs ready to protect thefermentor environment.
Foreword xiRecovery and utilization of co-productsAs we review our overall process, it is obviouslycritical that we maximize utilization of coproducts. Assuming the feedstock is corn, themajor cost factors are the raw material, energy,enzymes, processing chemical cost (watertreatment, etc.) and labor. Much of these costscan be offset with 17 lbs of distillers grainscoming from each bushel of corn; but we mustmaximize the return on this essential product.Distillers grains with solubles (DDGS) arecurrently (July 2003) selling for around 80/tonand corn for 2.20 per bushel. At 0.04 per lb( 80/ton), 17 lbs of DDGS gives us a credit of 0.68. This is set against the 2.20 bushel ofcorn or the 0.03-0.04 for enzymes. If on theother hand, new or novel products could bemade from distillers grains, (i.e. improved bypass proteins for cattle, pre-hydrolyzed DDGSfor human foods), the financial impact could besubstantial. The future will see many newproducts built around DDGS. This is the subjectof a separate chapter in this volume.As dry mills shift toward biorefining, insteadof simply grinding, corn, yield of ethanolbecomes only one part of the economicequation. Perhaps in the future, furtherprocessing of distillers grains will create productsthat make spent grains the single most importantraw material from a distillery. After all, they arerich and valuable protein sources, a commodityin very short supply across the world.EducationPerhaps the biggest surprise, as one surveys theprogress that has been made in the last 20 yearsis how little progress has been made in the areaof education. Unlike the brewing industry, whichseems to have an abundance of professionalswith PhD and masters degrees, our industry hasvery few. Unlike the brewing industry, whichhas no less than five brewing schools aroundthe world, the annual Alltech Alcohol Schoolremains the only venue for industry-widetraining.The Alltech Institute of Brewing and Distilling,established in 2000, set out to address thisshortfall by working in conjunction with theHeriot-Watt University in Scotland. Perhaps ourindustry should use the brewing industry as amodel. Scholarships should be funded andperhaps a bioscience center concept established.Bioscience centers bridge the gap betweenuniversity and industry by creating anenvironment where students are encouraged tocomplete higher degrees while doing industryfocused research.ConclusionsThe alcohol industry, therefore, is alive and well,and we have been given an opportunity toachieve something that many of us thoughtwould have been achieved by the mid-1980s.We have a superb oxygenate that will helpreduce global warming and at the same timeenable us to add value to our grains. The worldis not short of starch and sugar, the world is shortof protein. The fuel alcohol industry andbeverage alcohol industries therefore are in factgenerators of protein; it only remains for us tomake sure the proteins we generate are the mostadvantageous possible to man and beast.The chapters in this book we hope will helpthe reader realize the complexity and at the sametime the simplicity of the process of convertingsugars to ethanol. If we make your search forinformation just a little easier, we will haveachieved our objective. If we can encouragemore research, then we will be well-rewarded.
Ethanol industry today
Ethanol around the world: rapid growth in policies, technology and production 1Chapter 1Ethanol around the world: rapid growth in policies, technology andproductionT. Pearse LyonsPresident, Alltech Inc., Nicholasville, Kentucky, USAFuel ethanol industry history: how didtoday’s ethanol ‘boom’ happen?The amazing expansion of the past few years ishappening in a wholly different industry thanwhen the first ‘boom’ occurred. In the late 1970sand early 1980s an embryonic ethanol industrywas heralded as the renewable answer toworldwide shortages of fossil fuels. Farmers inAmerica’s heartland had abundant raw materialsin the form of cereal grain; and it seemed at onestage as if every farm would have its own‘gasohol’ plant. Small-scale operations with amyriad of new technologies emerged withunique names like ‘OPEC Killer’ or ‘A Step toIndependence’.Few of the early fuel ethanol plants were reallybig, as it seemed the beverage plant size wastaken as an example. Many were only capableof producing hundreds of gallons per day, butothers were well-engineered plants withcapacities up to 15-20 million liters per annum.Competitions were held at state fairs in order toenable farmers to determine which design wasbest. Enthusiasm, regardless of expertise, wasthe order of the day. The industry was cryingout for training and technology; and during thistime Alltech Inc. emerged, with its philosophyof marketing through education. Here alsoemerged the concept of the ‘Alcohol Textbook’,and the annual Alcohol School, which is now inits 23rd year.Figure 1. The alcohol industry reference books byAlltech Inc.By the mid-1980s, the smaller plants werebeginning to run into typical start-up problems,many associated with poor design, little capital,and relatively high labor costs. Perhaps theywere doomed to fail from the beginning, withor without government support. Production was
2 T.P. Lyonsnowhere near the forecasted 7 billion liters (1.85billion gallons), and instead languished around1.5 billion liters (0.4 billion gallons). Beverageethanol remained the dominant ethanol product.To most, it looked like the gasohol boom wasover.While smaller operations disappeared, otherlarger companies, well funded and with welldesigned plants, continued to grow. Corporationssuch as Cargill, Staleys and ADM becameindustry leaders. Today, one of these (ADM) isresponsible for processing 45% of the corn thatis converted into ethanol in the US. Thiscompany and others of this size knew the ethanolindustry had long term prospects and theyplanned survival strategies accordingly.Meanwhile in Brazil during the 1970s and1980s, a similar revolution was occurring. In1975 the so-called ‘Proalcohol’ program waslaunched, with massive support by thegovernment. Initially, the program focused onthe production of anhydrous ethanol, which wasblended with gasoline to produce the Braziliangasohol. The emphasis quickly changed tohydrous ethanol (95% ethanol/5% water), whichcould be used in its pure form in cars withspecially designed engines. By the mid-1980s,such cars represented the vast majority of themarketplace and it seemed the Proalcoholproduct was going to replace gasoline on a 1:1basis.The system, however, was very inflexible.When ethanol became difficult to get in the late1980s, consumers began to switch back toconventional cars in which gasoline (stillblended with a minimum level of ethanol) couldbe used. Was the fuel ethanol program alsogoing to falter in Brazil?Growing interest in fuel ethanol aroundthe worldAgainst such a background of declining interestin ethanol in the early 1990s, what brought aboutthe resurrection of the ethanol boom in the USand elsewhere? The first driving factor was aninternational agreement called the KyotoProtocol, in which most industrial nations agreedto improve the environment and lessen thegreenhouse effect by burning less fossil fuel ordoing so more efficiently. It was agreed to rollback carbon dioxide emissions to a given year.The impact was to be enormous.UNPRECEDENTED GROWTH IN THE USIn the United States, domestic events have giventhe industry a big push. The US Clean Air Actmandated an average of 2% oxygen be presentin what was called ‘reformulated gasoline’(RFG). Representing some 30% of the vast USgasoline market (100 billion gallons), it createda clear demand for an oxygenate. MTBE (methyltertiary butyl ether), with approximately 18%oxygen, and ethanol with 30% oxygen werechosen. Both were excellent oxygen boosters.MTBE, a petroleum derivative, was the earlychoice, but a series of scares regarding itspossible carcinogenic nature and its detectionin groundwater led to its planned phaseout. Thealcohol industry, meanwhile, was beginning toemerge, particularly in the Corn Belt (Nebraska,Iowa, Minnesota and Illinois). Its capacity hadreached 10 billion liters (2.7 billion gallons) by2003 (Figure 2) and in anticipation of thephaseout of MTBE (not just in California, butaround the country) some 73 plants had beenbuilt. At the time we are going to press, these 73plants, located in 20 states, have the capacity of11 billion liters (Figure 3). A further 13 plantsare under construction, which will add some 2billion liters (500 million gallons) of capacity.The ethanol industry also continues its streakof monthly production records. An all-timemonthly production record of 181,000 barrelsper day (b/d) was set in June of 2003, accordingto the US Energy Information Administration(Figure 4). The previous all-time record was179,000 b/d, set in April of this year.Driving industry growth: Farmer-owned ethanolplantsUnlike the earlier plants, which were dominatedby the large corporations, most of the new plantsare farmer-owned projects, as farmers seek toadd value to the commodities they grow andparticipate in profit sharing when the plantprospers. These plants have a typical size of 150million liters and a construction cost per liter of 0.40- 0.50. The predominant raw material islocally-grown corn (maize); and ethanolproduction is the third largest and fastest growingmarket for US corn (Figure 5). In 2002, over800 million bushels of corn were processed intoethanol and valuable feed co-products. The USDepartment of Agriculture estimates that morethan one billion bushels of corn will be
Ethanol around the world: rapid growth in policies, technology and production 198419821980019Millions of gallons2500Figure 2. Historic US fuel ethanol production.Ethanol production facilityBegan productionn in 2002Under constructioonSource: Renewable Fueels AssociationFigure 3. Fuel ethanol plants in the US (source: RFA).
4 T.P. LyonsThousands of barrels/day190180170160150140130120110JunJulAug SepOct Nov Dec Jan Feb Mar Apr MayJunFigure 4. Monthly US ethanol production, 2002-2003 (1 barrel 42 US gallons or 159 liters).Millions of 9881986198419821919800Figure 5. Corn utilized in US ethanol production.processed into ethanol in 2003, or about 10%of the total US harvest. Since 1999, farmerowned ethanol plants have increased theirpercentage of total production capacity from20% to nearly 35%. As a whole, farmer-ownedethanol plants are the largest ethanol producerin the US.New marketplace ination with MTBE, the state of Californiapassed landmark legislation phasing out the useof MTBE in the state’s motor fuel supply. Whilethe original deadline was delayed by one yearto December 31, 2003, all major refinersvoluntarily switched to ethanol in early 2003,resulting in a new market for more than 600million gallons. In 2004, with the MTBE ban inplace, California’s ethanol consumption willincrease to 750-800 million gallons annually.MTBE bans in New York and Connecticut arealso scheduled to take effect on January 1, 2004.These two states combined represent a marketfor more than 500 million gallons of ethanol. Ifall of the northeast were to replace current MTBEuse with ethanol, a market for more than a billiongallons of ethanol would be created. In total, 17states have passed legislation to phase out MTBEuse; and the future for ethanol looks bright.
Ethanol around the world: rapid growth in policies, technology and production 5Comprehensive energy legislation offersopportunities for ethanolThe nation’s increasing reliance on importedenergy, particularly from unstable regions of theworld, combined with erratic natural gas andworld oil markets has prompted theadministration and US Congress to debatecomprehensive energy policy legislation. As partof this legislation, an historic fuels agreementsupported by an unprecedented coalition ofagriculture, oil and environmental interestswould provide a growing market for renewablefuels while addressing concerns regardingMTBE water contamination and providingneeded flexibility in the fuels marketplace. Thisagreement would establish a Renewable FuelStandard (RFS), which would set an annual andincreasing minimum level of renewable fuelssuch as ethanol and biodiesel permitted in themarketplace, growing to 5 billion gallons by2012.New uses for ethanolWhile ethanol today is largely used as a blendingcomponent with gasoline to add octane andoxygen, opportunities abound for ethanol toplay a role in advanced vehicle technology andalternative fuels markets. For example, as arenewable fuel with an established fuelinginfrastructure in the US, ethanol is an attractivefuel option for the fuel cell market in both powergeneration and transportation. Research is alsounderway on E dieselTM, a mixture of ethanol,diesel and a blending agent. And there is alargely untapped market for E85, a blend of 85%ethanol and 15% gasoline, to power the growingnumber of available flexible fuel vehicles.Valuable feed co-product production increasingRecord ethanol production means recordproduction of valuable feed co-products forlivestock. In 2002, US dry mill ethanol facilities,which account for approximately 65% of ethanolproduction, produced about four million shorttons of distillers dried grains with solubles(DDGS). Ethanol wet mills producedapproximately 450,000 US tons of corn glutenmeal, 2.5 million tons of corn gluten feed andgerm meal, and 530 million pounds of corn oil.With estimates for 2003 production nearly 30%higher than 2002, we can anticipate a parallelincrease in production of feed co-products. Awaiting market exists in the world’s animal feedindustry ( 600 million tonnes) wheretraditionally used sources of protein such asanimal by-products and fish meal have beeneither eliminated due to concern surroundingMad Cow Disease (BSE) or reduced availabilityand higher prices. The combined protein andenergy value of ethanol by-products gives themtremendous potential in animal feeds across theworld.BRAZIL AND SOUTH AMERICAThe US, however, is not the only countryexperiencing an increase in alcohol production.In Brazil, new initiatives are underway and theinflexible Proalcohol program has been changed.Flex-fuel engines, which run equally well oneither pure hydrous alcohol or gasoline, havebeen launched. This technology can cope withanything from 100% hydrous ethanol to agasohol mix of 80% gasoline and 20%anhydrous ethanol, adjusting to any changewithin a fraction of a second. This compares veryfavorably to the engines in the US, which wouldnormally handle up to 85% anhydrous in a blendand cannot use pure hydrous ethanol.Furthermore, since ethanol sells in Brazil for lessthan gasoline at the pumps (50-60% of thegasoline price) even taking into account that 30%more ethanol is required to travel the samedistance, the new cars are bound to be a successand will drive up ethanol demand.It is expected that a million cars with Flex-fuelengines could be sold each year. With an average240 liters (63 gallons) of ethanol per monthconsumption, this could mean an additional 3billion liters would be needed over Brazil’scurrent 12-13 billion liters of production.Table 1. Projected production of ethanol (billion liters)1.2003USABrazilEuropean UnionIndiaThailandAustraliaChina1F.O. Licht, July .42
6 T.P. LyonsWhile few people will say exactly how much itcosts to produce a liter of fuel ethanol in Brazil,it is believed to be between 0.10 and 0.15.This puts the industry in a very favorableposition to export ethanol, since a similar costin the US from corn would be more like 0.20.Fuel ethanol emergence in South America isnot limited to Brazil. In Peru and Colombiainterest is also growing. Colombia estimates anannual need for almost one billion liters and 12production plants.THE EUROPEAN UNIONDriven by the Kyoto Agreement, the EuropeanCommission proposed in 2001 to increase theuse of crop-based, non-polluting renewablefuels. The target was for biofuels to account for2% of all fuels in EU transport by 2005. It wasmandated this would increase to 5.75% by 2010(from 0.3% in 2001).Both ethanol and biodiesel (from canola) areconsidered biofuels. In 2003 the targets weremade voluntary, but a direction on tax relief forrenewable energy was expected to be put intoplace. These would augment the existing taxrelief schemes, which vary from country tocountry. Spain, Germany, and Sweden, forexample, have 100% tax relief on renewablefuels, while France has 60% and Britain 40%.Across Europe, from Poland to Ireland, interestis rising as the new legislation begins to takeeffect.ASIAIndia’s transport sector accounts for over halfof the country’s oil consumption. It is notsurprising, therefore, that interest is growing inreplacing dependence on fossil fuels. By January2003, nine states had mandated at least 5%ethanol (E5) in transport fleets. Local distillerieswith a capacity of some 3.2 billion liters (900million gallons) are currently only operating at50% capacity. The demand for an additional 400million liters under this new mandate is thereforeimmediately being met. Although some politicalmaneuvering is still needed, the fuel ethanolprogram looks sound.In Southeast Asia, Thailand’s government, likemany in the region, had an early interest inbioethanol as a way to reduce oil imports. It wasestimated that 0.7 billion liters of ethanol wouldbe required should they decide to introduce theoxygenate at 10% of gasoline. Both cassava(tapioca) and molasses were suggested as rawmaterials and eight projects were approved. Atthis time only one project is under construction.Two distinct areas for ethanol production existin China: the maize-rich north and the sugarcane rich south. Both will feature in the country’sethanol future. The government sees ethanol aspart of its program to reduce pollution –important with the looming 2004 Olympics –and at the same time encourage ruralemployment. China’s largest fuel ethanolfacility, costing almost 300 million to construct,is in Jilin. With a capacity of some 600 millionliters (165 million gallons), it will use 2 milliontons of maize a year (13% of production in thatprovince). By October 2003, all vehicles in theProvince of Jilin will use fuel containing at least10% ethanol.AUSTRALIAUncertainty also exists in Australia, where atarget of 350 million liters was encouraged withtax exemptions and grants for up to six years.Local governments have tried to boost ethanolconsumption. For example, in Cairns,Queensland’s largest city, government-ownedvehicles were mandated to use E10 (90%gasoline, 10% ethanol). Using some 20,000 litersper day, the government hoped in this way toavoid some of the negative publicity beinggenerated by the anti-ethanol lobby.ConclusionsEthanol, as a global product, is experiencing asignificant jump
Yeast and management of fermentation 9 Understanding yeast fundamentals 85 Inge Russell International Centre for Brewing and Distilling, School of Life Sciences, Heriot-Watt University, Edinburgh, UK 10 Practical management of yeast: conversion of sugars to ethanol 121 Dave R. Kelsall and T. Pearse Lyons Alltech Inc., Nicholasville, Kentucky, USA