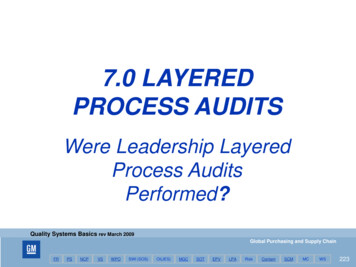
Transcription
7.0 LAYEREDPROCESS AUDITSWere Leadership LayeredProcess AuditsPerformed?Quality Systems Basics rev March 2009Global Purchasing and Supply ChainFRPSNCPVSWPOSWI (SOS)OI(JES)MGCSOTEPVLPARiskContamSCMMCWS223
LAYERED PROCESS AUDITSOutline7.0) Introduction page: Purpose, Scope, Responsibility7.1) Benefits7.2) Process explanation7.2.1) Schedule and tracking7.2.2) Develop high risk items for auditing7.2.3) Layered Process Audit Check sheet Concept7.2.4) Layered Process Audit Check sheet Evaluation7.2.5) Countermeasure sheet7.2.6) Management Review Requirements7.3) Summary, ShallsQuality Systems Basics rev March 2009Global Purchasing and Supply ChainFRPSNCPVSWPOSWI (SOS)OI(JES)MGCSOTEPVLPARiskContamSCMMCWS224
LAYERED PROCESS AUDITS7.0 IntroductionPURPOSE: SCOPE: Ensure consistent applicationand execution of standards.Improve built-in-quality andincrease operator/leadershipawareness facilitated bycoaching/teaching interactionbetween leadership &operatorsAssembly AreaManufacturing OperationsShipping / ReceivingAll OperationsOther Support FunctionsRESPONSIBILITY: Ownership Plant / Operations Mgr Contingency Plan for AllSituationsQuality Systems Basics rev March 2009Global Purchasing and Supply ChainFRPSNCPVSWPOSWI (SOS)OI(JES)MGCSOTEPVLPARiskContamSCMMCWS225
LAYERED PROCESS AUDITS7.1 - Benefits Layered Process Audits provide a system to:– verify compliance to the documented process.– instill discipline.– improve communication.– improve overall quality. Ensures a high level of process control by identifying &controlling high risk / significant process elements. Maintains proper application of standards as defined & achievedthrough operational readiness process. Identify opportunities for improvement & provide a process foreffective follow up.Quality Systems Basics rev March 2009Global Purchasing and Supply ChainFRPSNCPVSWPOSWI (SOS)OI(JES)MGCSOTEPVLPARiskContamSCMMCWS226
LAYERED PROCESS AUDITS7.2 - Process explanation Layered Process Audit (LPA) is a standardized audit performed ona regular, frequent basis by all layers of the organization to verifyadherence to operational standards. LPA‟s are an industry standard. LPA‟s supplement ongoing control plan and job instruction checks. LPA‟s shall be owned by manufacturing leadership(Team Leader – Plant / Operations Manager). Quality and other functions will participate and support the LPAsystem.Quality Systems Basics rev March 2009Global Purchasing and Supply ChainFRPSNCPVSWPOSWI (SOS)OI(JES)MGCSOTEPVLPARiskContamSCMMCWS227
LAYERED PROCESS AUDITS7.2 - Process explanation (continued) The Layered Process Audit system includes:– Schedule and tracking of audits.– Identifying high risk items for the LPA.– A LPA Checklist that evaluates current processes toestablished standards.– Identification of corrective action requirements andcountermeasures.– Regular review process by senior management of the auditresults and corrective actions.Quality Systems Basics rev March 2009Global Purchasing and Supply ChainFRPSNCPVSWPOSWI (SOS)OI(JES)MGCSOTEPVLPARiskContamSCMMCWS228
LAYERED PROCESS AUDITS7.2 - Process explanation (continued) Pick the station to be audited based on theLPA scheduleChoose theWorkstation Follow LPA Check sheetConduct the Audit Immediately inform all Team membersabout the audit results. Record all deviations on LPA Check sheetand Countermeasure sheet. Assign target close date & champion Implement suggested countermeasuresas soon as possible. Follow-up on open items, make sure to closeby target close date. Elevate problem to higher level after targetClose date. Perform Management review.Give feedback &document resultsFollow-upQuality Systems Basics rev March 2009Global Purchasing and Supply ChainFRPSNCPVSWPOSWI (SOS)OI(JES)MGCSOTEPVLPARiskContamSCMMCWS229
LAYERED PROCESS AUDITS7.2.1 - Scheduling and tracking Define the organization levels to perform audits. Define audits frequency for each level of the organization.Layered Process Audits levels & frequency: Daily, the manufacturing supervisor shall perform audits. Weekly, the manufacturing area manager shall audit & verify thatsupervisor verification is being completed. Monthly, the site leadership shall conduct Layered Process Auditsand review audit results and corrective actions.Quality Systems Basics rev March 2009Global Purchasing and Supply ChainFRPSNCPVSWPOSWI (SOS)OI(JES)MGCSOTEPVLPARiskContamSCMMCWS230
LAYERED PROCESS AUDITS7.2.1 - Scheduling and ers/ DirectorsDirectorsQuarterlyQuarterly/ timetime/ month/ monthManager/ EngineersManager/ Engineerstime/week1 1time/weekSupervisor/ TeamLeaderLeaderSupervisor/ TeamDailyDaily/ WeeklyQuality Systems Basics rev March 2009Global Purchasing and Supply ChainFRPSNCPVSWPOSWI (SOS)OI(JES)MGCSOTEPVLPARiskContamSCMMCWS231
LAYERED PROCESS AUDITS7.2.1 - Scheduling and tracking(continued)The example at the right isanother way to ensure eachstation within a work area isevaluated at a minimum, on amonthly basis. This chart is usedby all auditors to determine whichstations have not yet been auditedand requires the auditor to writedown their name, date, and shiftfor the stations they chose for theaudit.The goal is to audit each workstation where a team member ispresent one time each month.(Example)Quality Systems Basics rev March 2009Global Purchasing and Supply ChainFRPSNCPVSWPOSWI (SOS)OI(JES)MGCSOTEPVLPARiskContamSCMMCWS232
LAYERED PROCESS AUDITS7.2.1 - Scheduling and tracking(Example)(continued)Identifying Audits to becompleted by theleadership staff isessential to ensure thatall areas on the shopfloor interact with themanagement team. Anexample schedule atthe right addresses boththe required frequencyby manager and thestatus of thisinteraction.Shaded inas Audit isCompletedShaded inRed if NotCompletedQuality Systems Basics rev March 2009Global Purchasing and Supply ChainFRPSNCPVSWPOSWI (SOS)OI(JES)MGCSOTEPVLPARiskContamSCMMCWS233
LAYERED PROCESS AUDITS7.2.2 - Development of high risk items for auditingHigh risk items shall be identified and included in the audit.They should be organized by 3 main sections: Work Station– list of checks, applicable to all work stations Quality Focused – checks are specific to operations anddevelopedby plant, based on quality feedback, processknowledge, and problem solving Manufacturing System – list of system checks that focused oncompliance to plant operationsQuality Systems Basics rev March 2009Global Purchasing and Supply ChainFRPSNCPVSWPOSWI (SOS)OI(JES)MGCSOTEPVLPARiskContamSCMMCWS234
LAYERED PROCESS AUDITS7.2.2 - Development of high risk items for auditingExamples of Work Station issues:(continued) Ensuring proper safety practices and PPE are being followed. Ensuring proper tools, gages and materials are available & used. Ensuring standardized work & quality standards are understood &followed. Ensuring Andon system is functioning properly. Ensuring Workplace Organization & Visual Managementstandards are maintained (e.g. according to the plant WPOstandards and Visual Management policy). Ensuring compliance to Material Processes – FIFO/Min.-Max.levels.Quality Systems Basics rev March 2009Global Purchasing and Supply ChainFRPSNCPVSWPOSWI (SOS)OI(JES)MGCSOTEPVLPARiskContamSCMMCWS235
LAYERED PROCESS AUDITS7.2.2 - Development of high risk items for auditing (continued)Examples of Quality Focused issues : Specific to a Product Line or Area of the plant Specific items regarding corrective action implementation tocustomer concerns. (e.g. error proofing verification, use of fixtureadded to complete standardized work Ensure error proofing is functioning properly and identified highrisk/ significant process elements are controlled to preventknown problems from reoccurring. Ensure required quality inspection and/or documentation is beingcompleted.Quality Systems Basics rev March 2009Global Purchasing and Supply ChainFRPSNCPVSWPOSWI (SOS)OI(JES)MGCSOTEPVLPARiskContamSCMMCWS236
LAYERED PROCESS AUDITS7.2.2 - Development of high risk items for auditing(continued)Examples of Manufacturing System issues : Completion of safety talks & tours Compliance to Process Control Plans Conformance to Workplace Organization standards Proper use of the Andon System Effective Problem solving & countermeasure implementation Effective use of Layered Process Audits process for control andfollow upVerification that special process audits are performed shall be includedas applicable. (e.g. CQI 9, 11, 12, Weld Audit, Chrome Audit, PaintProcess Audit)Quality Systems Basics rev March 2009Global Purchasing and Supply ChainFRPSNCPVSWPOSWI (SOS)OI(JES)MGCSOTEPVLPARiskContamSCMMCWS237
LAYERED PROCESS AUDITS7.2.3 - LPA Check sheet LPA results are documented on LPA Check sheet .The intent is to have a single page LPA Check sheet form that ismanually completed on production floor. The back side oftheform is available to write down the noncompliance comments. Establish LPA Check sheet questions from the high risk items.– A LPA Check sheet should have two common sections (Work Stationand Manufacturing System) and one section (Quality Focused), thatis customized to a specific Product Line or Area of the Plant.– Work Station and Quality Focused sections of the LPA Check sheetshall be completed by all auditors. The Manufacturing Systemsection shall be completed by the site leadership only.– A LPA Check sheet should be created for each unique processingareaQuality Systems Basics rev March 2009Global Purchasing and Supply ChainFRPSNCPVSWPOSWI (SOS)OI(JES)MGCSOTEPVLPARiskContamSCMMCWS238
LAYERED PROCESS AUDITS7.2.3 - LPA Check sheet (continued)(Example)HEADER: Enter the System NameProduct line or an area of the Plant1. Molding2. Paint/Coating3. Assembly4. Warehouse/ShippingIn this ExampletheManufacturerwould have (4)four unique onepage auditforms/files, tocover allprocesses.Section #1:COMMON Work Station QuestionsSection #2:UNIQUE Quality FocusedQuestionsSection #3:COMMON Manufacturing SystemQuestionsQuality Systems Basics rev March 2009Global Purchasing and Supply ChainFRPSNCPVSWPOSWI (SOS)OI(JES)MGCSOTEPVLPARiskContamSCMMCWS239
LAYERED PROCESS AUDITS7.2.3 - LPA Check sheet (continued)Header & Work Station Specific(Example)Has the team member been qualified torequirements of the job and is this documented?Quality Systems Basics rev March 2009Global Purchasing and Supply ChainFRPSNCPVSWPOSWI (SOS)OI(JES)MGCSOTEPVLPARiskContamSCMMCWS240
LAYERED PROCESS AUDITS7.2.3 - LPA Check sheet (continued)Quality Focused & Manufacturing System(Example)Quality Systems Basics rev March 2009Global Purchasing and Supply ChainFRPSNCPVSWPOSWI (SOS)OI(JES)MGCSOTEPVLPARiskContamSCMMCWS241
LAYERED PROCESS AUDITS7.2.4 - LPA Check sheetEvaluation There are four results that can come out of each audit question:– Y – No deviation found– N – Deviation found / not corrected during audit– NC – Deviation corrected during audit – drive this behavior – N/A – Not applicable (established at Plant/Shift Leaderlevel)All Deviations shall be recorded on the LPA Check sheet .Describe deviations in the detail section on the back of the LPACheck sheetAny Deviations that can be corrected immediately will have aletter „C‟ next to N.Any Deviations that cannot be immediately corrected shouldhave additional detail written and transferred to aCountermeasure Sheet.Reasons for non-compliance should be understood.Quality Systems Basics rev March 2009Global Purchasing and Supply ChainFRPSNCPVSWPOSWI (SOS)OI(JES)MGCSOTEPVLPARiskContamSCMMCWS242
LAYERED PROCESS AUDITS7.2.4 - LPA Check sheetEvaluation(Example)YNCN Deviation FoundY Meets StandardIf the item is CorrectedImmediatelyQuality Systems Basics rev March 2009Global Purchasing and Supply ChainFRPSNCPVSWPOSWI (SOS)OI(JES)MGCSOTEPVLPARiskContamSCMMCWS243
LAYERED PROCESS AUDITS7.2.5 - Countermeasure SheetAll questions answered “N” on the LPA Checks sheet that cannot beresolved immediately will be entered on the Countermeasure Sheet asan open item. The Countermeasure Sheet tracks the specific open issues onan operation/workstation for each group. All questions answered “N” on the LPA Check Sheet that cannotbe resolved immediately will be entered on the CountermeasureSheet as an open item. The Countermeasure Sheet will be updated and signed off asissues are resolved.Quality Systems Basics rev March 2009Global Purchasing and Supply ChainFRPSNCPVSWPOSWI (SOS)OI(JES)MGCSOTEPVLPARiskContamSCMMCWS244
LAYERED PROCESS AUDITS7.2.5 - Countermeasure Sheet (continued)(Example)Item # Date Location4 7/7/086 7/7/08Problem DescriptionOwnerNew option Side marker lamp, parts don't005R have a standard marked location.tool for installing drainplugs is differentfrom standard, TM used replacement005R without informing TLTargetCompletedate Initials DateCountermeasureRe-layout work station to include oneTL1 shift's requirement of lamps.7/28/08JCget standard tool from store, replace atTL1 workstation8/3/08RS7/26/08Quality Systems Basics rev March 2009Global Purchasing and Supply ChainFRPSNCPVSWPOSWI (SOS)OI(JES)MGCSOTEPVLPARiskContamSCMMCWS245
LAYERED PROCESS AUDITS7.2.6 - Management Review Requirements LPA Review Process–––––Shift Leader is Process OwnerRegularly schedule review meetingReview compliance & completion performanceElevate past due countermeasures to next levelReview audit questions for Continuous Improvement (add, delete,revise as needed) When appropriate, the Layered Process Audit nonconformanceshall be added to the Fast Response system and/or the C.A.R.E.checklist. Layered Process Audit results shall be added to the LessonsLearned database when appropriate. Audit results shall be summarized and reviewed by themanufacturing site leadership.Quality Systems Basics rev March 2009Global Purchasing and Supply ChainFRPSNCPVSWPOSWI (SOS)OI(JES)MGCSOTEPVLPARiskContam
–A LPA Checklist that evaluates current processes to established standards. –Identification of corrective action requirements and countermeasures. –Regular review process by senior management of the audit results and corrective actions. LAYERED PROCESS AUDITS 7.2 - Process explanation (continued) Quality Systems Basics rev March 2009 FR PS NCP VS WPO SWI (SOS) OI(JES) MGC SOT EPV