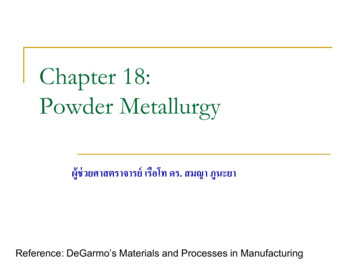
Transcription
Chapter 18:Powder ��ารย์ เรือโท ดร. สมญา ภูนะยาReference: DeGarmo’s Materials and Processes in Manufacturing
18.1 Introduction Powder metallurgy is the name given to the processby which fine powdered materials are blended,pressed into a desired shape, and then heated tobond surfacesTypically used when large amounts of small,intricate parts with high precision are requiredLittle material waste and unusual mixtures can beutilizedUsed for parts in the automotive industry, householdappliances, and recreational equipment (to name afew)
18.2 The Basic Process Four basic steps 1. Powder manufacture2. Mixing or blending3. Compacting4. SinteringFigure 18-1 Simplified flow chart of thebasic powder metallurgy process.
18.3 Powder Manufacture Properties of powder metallurgy products are highlydependent on the characteristics of starting powdersSome important properties and characteristics Chemistry and purityParticle sizeSize distributionParticle shapeSurface textureUseful in producing prealloyed powders Each powder particle can have the desired alloycomposition
Powder Manufacture The majority of commercial powder is produced bysome form of melt atomization Atomization is a process where liquid metal is fragmentedinto small droplets that cool and solidify into particlesFigure 18-2 Twomethods for producingmetal powders: (a)melt atomization and(b) atomization from arotating consumableelectrode.
Additional Methods of PowderManufacture Methods Chemical reduction of particulate compoundsElectrolytic depositionPulverization or grindingThermal decomposition of particulate hydridesPrecipitation from solutionCondensation of metal vaporsAlmost any metal or alloy can be convertedinto powder
18.4 Rapidly Solidified Powder(Microcrystalline and Amorphous) If the cooling rate of an atomized liquid isincreased, ultra-fine or microcrystalline sizedgrains can formSome metals can solidify without becomingcrystalline (called amorphous materials)Amorhpus materials can have high strength,improved corrosion resistance, and reducedenergy to induce and reverse magnetization
18.5 Powder Testing and Evaluation Powders should be evaluated for their suitability forfurther processingFlow rate measures the ease with which powder canbe fed and distributed into a dieApparent density is the measure of a powder’sability to fill available space without externalpressureCompressibility is the effectiveness of appliedpressureGreen strength is used to describe the strength ofthe pressed powder after compacting
18.6 Powder Mixing and Blending The majority of powders are mixed with otherpowders, binders, and lubricants to achievethe desired characteristics in the finishedproductSufficient diffusion must occur duringsintering to ensure a uniform chemistry andstructureUnique composites can be producedBlending or mixing operations can be doneeither wet or dry
18.7 Compacting Loose powder is compacted and densified into ashape, known as green compactMost compacting is done with mechanical pressesand rigid tools Hydraulic and pneumatic presses are also used
Figure 18-3 (Left) Typical press for the compacting of metal powders. A removable die set (right)allows the machine to be producing parts with one die set while another is being fitted to produce asecond product. (Courtesy of Alfa Laval, Inc., Warminster, PA.)
Compaction Sequence Powders do not flow like liquid, they simplycompress until an equal and opposing force iscreated This opposing force is created from a combination of (1)resistance by the bottom punch and (2) friction between theparticles and die surfaceFigure 18-4 Typical compaction sequence for a single-level part, showing the functions of the feed shoe,die core rod, and upper and lower punches. Loose powder is shaded; compacted powder is solid black.
Additional Considerations DuringCompacting When the pressure isapplied by only onepunch, the maximumdensity occurs rightbelow the punchsurface and decreasesaway from the punchFor complex shapes,multiple punchesshould be usedFigure 18-5 Compaction with a single moving punch,showing the resultant nonuniform density (shaded),highest where particle movement is the greatest.Figure 18-6 Density distribution obtained with a doubleacting press and two moving punches. Note theincreased uniformity compared to Figure 18-5. Thickerparts can be effectively compacted.
Effects of CompactingFigure 18-8 Compaction of a two-thickness part withonly one moving punch. (a) Initial conditions; (b) aftercompaction by the upper punch. Note the drasticdifference in compacted density.Figure 18-7 Effect of compacting pressure on greendensity (the density after compaction but before Figure 18-9 Two methods of compacting a doublesintering). Separate curves are for severalthickness part to near-uniform density. Both involve thecommercial powders.controlled movement of two or more punches.
Classes of Powder Metallurgy Equipment The complexity of the part dictates the complexity ofequipmentEquipment has been grouped into classesFigure 18-10 Sample geometriesof the four basic classes of pressand-sinter powder metallurgyparts. Note the increased pressingcomplexity that would be requiredas class increases.
Complex Compacting If an extremely complex shape is desired, thepowder may be encapsulated in a flexible mold,which is then immersed in a pressurized gas orliquid Process is known as isostatic compactionIn warm compaction, the powder is heated prior topressingThe amount of lubricant can be increased in thepowder to reduce frictionBecause particles tend to be abrasive, tool wear is aconcern in powder forming
18.8 Sintering In the sintering operation, the pressed-powdercompacts are heated in a controlled atmosphere toright below the melting pointThree stages of sintering Burn-off (purge)- combusts any air and removes lubricantsor binders that would interfere with good bondingHigh-temperature- desired solid-state diffusion and bondingoccursCooling period- lowers the temperature of the products in acontrolled atmosphereAll three stages must be conducted in oxygen-freeconditions
18.9 Hot-Isostatic Pressing Hot-isostatic pressing (HIP) combinespowder compaction and sintering into asingle operation Gas-pressure squeezing at high temperaturesHeated powders may need to be protectedfrom harmful environmentsProducts emerge at full density with uniform,isotropic propertiesNear-net shapes are possible
18.10 Other Techniques to Produce HighDensity P/M Products High-temperature metaldeformation processes canbe used to produce highdensity P/M partsCeracon process- a heatedpreform is surrounded byhot granular material,transmitting uniformpressureSpray forming- inert gasespropel molten droplets ontoa moldFigure 18-11 One method of producingcontinuous sheet products from powderedfeedstock.
18.11 Metal Injection Molding (MIM) orPowder Injection Molding (PIM) Ultra-fine spherical-shaped metal, ceramic, orcarbide powders are combined with athermoplastic or wax Becomes the feedstock for the injection processThe material is heated to a paste likeconsistency and injected into a heated moldcavityAfter cooling and ejection, the binder materialis removed Most expensive step in MIM and PIM
MIMFigure 18-12 Flow chart of the metal injectionmolding process (MIM) used to produce small,intricate-shaped parts from metal powder.Figure 18-13 Metal injection molding (MIM)is ideal for producing small, complex parts.(Courtesy of Megamet Solid Metals, Inc., St.Louis, MO.)
18.12 Secondary Operations Most powder metallurgy products are readyto use after the sintering processSome products may use secondary operationto provide enhanced precision, improvedproperties, or special characteristicsDistortion may occur during nonuniform cooldown so the product may be repressed,coined, or sized to improve dimensionalprecision
Secondary Operations If massive metal deformation takes place in thesecond pressing, the operation is known as P/Mforging Increases density and adds precisionInfiltration and impregnation- oil or other liquid isforced into the porous network to offer lubricationover an extended product lifetimeMetal infiltration fills in pores with other alloyingelements that can improve propertiesP/M products can also be subjected to theconventional finishing operations: heat treatment,machining, and surface treatments
Figure 18-14 (Right) Comparison ofconventional forging and the forgingof a powder metallurgy preform toproduce a gear blank (or gear).Moving left to right, the top sequenceshows the sheared stock, upsetsection, forged blank, and exteriorand interior scrap associated withconventional forging. The finishedgear is generally machined from theblank with additional generation ofscrap. The bottom pieces are thepowder metallurgy preform andforged gear produced entirely withoutscrap by P/M forging. (Courtesy ofGKN Sinter Metals, Auburn Hills, MI.)Figure 18-15 P/M forgedconnecting rods have beenproduced by the millions. (Courtesyof Metal Powder IndustriesFederation, Princeton, NJ.)
18.13 Properties of P/M Products The properties of P/M products depend on multiplevariables Type and size of powderAmount and type of lubricantPressing pressureSintering temperature and timeFinishing treatmentsMechanical properties are dependent on densityProducts should be designed (and materialsselected) so that the final properties will be achievedwith the anticipated final porosity
P/M Materials
18.14 Design of Powder Metallurgy Parts Basic rules for the design of P/M parts Shape of the part must permit ejection from diePowder should not be required to flow into smallcavitiesThe shape of the part should permit theconstruction of strong toolingThe thickness of the part should be within therange for which P/M parts can be adequatelycompactedThe part should be designed with as few changesin section thickness as possible
Basic Rules for P/M Parts Parts can be designed to take advantage of the factthat certain forms and properties can be producedby P/M that are impossible, impractical, oruneconomical by any other methodThe design should be consistent with availableequipmentConsideration should be made for producttolerancesDesign should consider and compensate fordimensional changes that will occur after pressing
Figure 18-17 Examples of poor and good design features for powder metallurgy products.Recommendations are based on ease of pressing, design of tooling, uniformity of properties, andultimate performance.
18.15 Powder Metallurgy Products Porous or permeable products such as bearings, filters, andpressure or flow regulatorsProducts of complex shapes that would require considerablemachining when made by other processesProducts made from materials that are difficult to machine ormaterials with high melting pointsProducts where the combined properties of two or more metalsare desiredProducts where the P/M process produces clearly superiorpropertiesProducts where the P/M process offers and economic advantage
18.16 Advantages and Disadvantages ofPowder Metallurgy Advantages Elimination or reductionof machiningHigh production ratesComplex shapesWide variations incompositionsWide property variationsScrap is eliminated orreduced Disadvantages Inferior strengthpropertiesHigh tooling costsHigh material costSize and shapelimitationsDimensional changesduring sinteringDensity variationsHealth and safetyhazards
18.17 Summary Powder metallurgy can produce products outof materials that are otherwise very difficult tomanufactureP/M products can be designed to provide thetargeted propertiesVariations in product size, production rate,quantity, mechanical properties, and cost
18.1 Introduction Powder metallurgy is the name given to the process by which fine powdered materials are blended, pressed into a desired shape, and then heated to bond surfaces Typically used when large amounts o