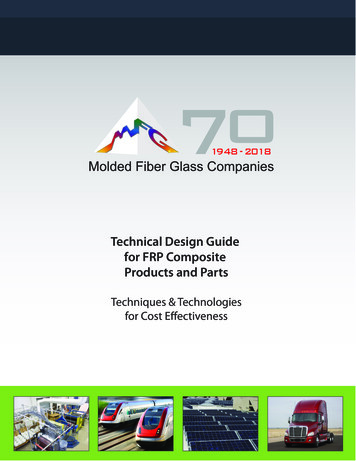
Transcription
1948 - 2018Technical Design Guidefor FRP CompositeProducts and PartsTechniques & Technologies
This manual is an overview of the Fiber ReinforcedPlastic/Composite (FRP/Composite) material system.Materials and processes are presented along with designguidelines and comparisons to alternate materials. Becauseof the versatility of FRP/Composites, the designer isencouraged to collaborate with a molder and/or materialsupplier to optimize the application.
Definition of CompositesComposites are a combination of two or more materialsyielding properties superior to those of the individualingredients. One material is in the form of a particulate orfiber, called the reinforcement or discrete phase. The otheris a formable solid, called the matrix or continuous phase.The region where the reinforcement and matrix meet iscalled the interface. Composite properties are determined bychemical and mechanical interaction of the combined materials.Wood and concrete are composites under this definition.This document is limited to the application of the subset ofcomposites called Fiber Reinforced Plastic (FRP) thatcombine fibers of glass or other materials (the reinforcement)with thermoset and/or thermoplastic resins (the matrix).
What areFRP/Composites?Fiberglass reinforced plastic,commonly known as fiberglass,was developed commerciallyafter World War II. Since thattime, the use of fiberglass hasgrown rapidly.The term “fiberglass” describes athermoset plastic resin that isreinforced with glass fibers.In this manual, the more generalterms Fiber Reinforced Plastic/Composites or FRP/Compositeswill be used to describe theseextremely useful material systems.Plastic resins come in two differentclasses - thermosets andthermoplastics. From a practicalperspective, it’s easy to rememberthat thermosets maintain their moldedshape at higher temperatures andcannot be melted and reshaped.Thermoplastics will melt at a giventemperature and can be solidifiedinto new shapes by cooling toambient temperatures. Thermosetsand thermoplastics are describedwith more detail in the ResinSystems section of this document.Reinforcing fibers include glass, carbon,aramid and other man-made and naturalmaterials that are further described inthe Reinforcement section of thisdocument. These are used in a varietyof forms and combinations to providethe required properties.The plastic resin systems determinechemical, electrical, and thermalproperties. Fibers provide strength,dimensional stability, and heatresistance. Additives provide colorand determine surface finish, andaffect many other properties suchas weathering and flame retardance.Processing of FRP/Compositesinvolves complex chemical reactions.Final properties are determined bymany factors including the type,amount, and composition of theresin systems and reinforcements.In addition, the use of additives cangreatly affect the FRP/Compositeproperties.
Corrosion ResistanceHigh Strength, LightweightDimensional StabilityParts Consolidation andTooling MinimizationHigh Dielectric Strength andLow Moisture AbsorptionMinimum Finishing Requiredresponsible for applications incorrosive environments such asthose found in the chemical processingand water treatment industries.Resistance to corrosion provideslong life and low maintenance inmarine applications from sailboatsand minesweepers to seawalls andoffshore oil platforms.High Strength, LightweightFRP/Composites provide highstrength to weight ratios exceedingthose of aluminum or steel. Highstrength, lightweight FRP/Compositesare a rational choice whenever weightsavings are desired, such as componentsfor the transportation industry.Dimensional StabilityDesign FlexibilityFRP/Composites have highdimensional stability under varyingphysical, environmental, and thermalstresses. This is one of the most usefulproperties of FRP/Composites.There can be many benefitsobtained by the use of FRP/Composites. These benefits andcharacteristics should be consideredearly in the design process.A single FRP composite moldingoften replaces an assembly ofseveral metal parts and associatedfasteners, reducing assembly andhandling time, simplifying inventory,and reducing manufacturing costs.A single FRP/Composite tool canreplace several progressive toolsrequired in metal stamping.FRP/Composites do not rust, corrodeor rot, and they resist attack frommost industrial and householdchemicals. This quality has beenThe excellent electrical insulatingproperties and low moistureabsorption of FRP/CompositesLow to Moderate Tooling CostsCorrosion ResistanceParts Consolidation andTooling Minimization.High Dielectric Strength andLow Moisture Absorptionqualify them for use in primarysupport applications such as circuitbreaker housings, and where lowmoisture absorption is required.Minimum Finishing RequiredFRP/Composites can be pigmentedas part of the mixing operation orcoated as part of the moldingprocess, often eliminating the needfor painting. This is particularlycost effective for large componentssuch as tub/shower units. Also, oncritical appearance components, aclass “A” surface is achieved.Low to Moderate Tooling CostsRegardless of the molding methodselected, tooling for FRP/Compositesusually represents a small part ofthe product cost. For eitherlarge-volume mass-production orlimited runs, tooling cost is normallysubstantially lower than that of themultiple forming tools required toproduce a similar finished partin metal.Design FlexibilityNo other major material systemoffers the design flexibility ofFRP/Composites. Presentapplications vary widely. They rangefrom commercial fishing boat hullsand decks to truck fenders, fromparabolic TV antennas to transitseating, and from outdoor lamphousings to seed hoppers. Whatthe future holds depends on theimagination of today’s designengineers as they develop evenmore innovative applications forFRP/Composites.3
Fibers and ResinsMuch of the strength ofFRP/Composites is due tothe type, amount andarrangement of the fiberreinforcement. While over90% of the reinforcements in useare glass fibers, other reinforcementshave established a critical niche.E-glass is the most commonly usedfiber reinforcement. It is strong,has good heat resistance, and highelectrical properties. For morecritical needs, S-Glass offers higherheat resistance and about one-thirdhigher tensile strength (at a highercost) than that of E-glass.Carbon Fibers (graphite) areavailable in a wide range of propertiesand costs. These fibers combinelight weight with very high strengthand modulus of elasticity. Themodulus of elasticity is a measureof the stiffness or rigidity in amaterial. For high stiffnessapplications these reinforcementsare hard to beat, with a modulus ofelasticity that can equal steel. FRP/Composites with carbon fiberreinforcement also have excellentfatigue properties. The primary useof carbon fibers is in aircraft andaerospace, in which weight savingsare a major objective. While its costlimits carbon’s use in commercialapplications, it is used extensively wherematerial content is low, such assporting equipment.4Aramid, or aromatic polyamidefibers (Kevlar or Twaron )provide high strength and lowdensity (40% lower than glass) aswell as high modulus. These fiberscan be incorporated in manypolymers and are extensively usedin high impact applications, includingballistic resistance.Natural Fibers such as Sisal, Hempand Flax have been used for manyapplications with low strengthrequirements. They are limited toapplications not requiring resistanceto moisture or high humidity.Arrangement of the glass fibers how the individual strands arepositioned – determines bothdirection and level of strengthachieved in a molded FRP/Composite.The three basic arrangements of glassfiber reinforcement are unidirectional,bidirectional and multidirectional.Unidirectional arrangements providethe greatest strength in the directionof the fibers. Unidirectional fibers canbe continuous or intermittent,depending on specific needsdetermined by part shape andprocess used. This arrangementpermits very high reinforcementloading for maximum strengths.The fibers in a bidirectional arrangementare in two directions – usually at 900to each other, thus providing thehighest strength in those directions.The same number of fibers neednot necessarily be used in bothdirections. High fiber loading canbe obtained in woven bidirectionalreinforcements.Multidirectional or randomarrangements provide essentiallyequal strength in all directions of thefinished part.
Woven FabricsReinforcements are supplied inseveral basic forms to provideflexibility in cost, strength,compatibility with the resin system,and process requirements.Regardless of the final form, allfiber reinforcements originate assingle filaments. A large numberof filaments are formedsimultaneously and gathered into astrand. A surface treatment is thenThisappliedm to facilitate subsequentprocessing, maintain fiber integrity,and provide compatibility withspecific resin systems. After thistreatment, the strands are furtherprocessed into various forms ofreinforcements for use in moldingFRP/Composites.Continuous Strand RovingThis basic form of reinforcement issupplied as untwisted strandswound into a cylindrical packagefor further processing. Continuousroving is typically chopped forspray-up, preform or sheet moldingcompounds. In the continuous form,it is used in pultrusion andfilament-winding processes.Woven RovingWoven from continuous roving,this is a heavy, drapable fabricavailable in various widths, thicknessesand weights. Woven roving costs lessthan conventional woven fabric andis used to provide high strength in largestructural components such as tanksand boat hulls. Woven roving is usedprimarily in hand lay-up processing.Made from fiber yarns, wovenfabrics are of a finer texture thanwoven roving. They are available ina broad range of sizes and inweights from 21/2 to 18 oz./sq. yd.Various strength orientations arealso available.Also, penetrationoReinforcing MatMade from either continuousstrands laid down in a swirl patternor from chopped strands, reinforcingmat is held together with a resinousbinder or mechanically stitched.These mats are used for mediumstrength FRP/Composites.Combination mat, consisting ofwoven roving and chopped strandmat bonded together, is used tosave time in hand lay-up operations.Hybrid mats of glass and carbonand aramid fibers are also available forhigher-strength reinforced products.Surfacing MatSurfacing mat or veil is a thin fibermat made of monofilament and isnot considered a reinforcingmaterial. Rather, its purpose is toprovide a good surface finishbecause of its effectiveness inblocking out the fiber pattern ofthe underlying mat or fabric.Surfacing mat is also used on theinside layer of corrosion-resistantFRP/Composite products toproduce a smooth, resin-richsurface.Chopped FibersChopped strands or fibers areavailable in lengths from 1/8” to 2”for blending with resins andadditives to prepare moldingcompounds for compression orinjection molding and otherprocesses. Various surface treatmentsare applied to ensure optimumcompatibility with different resinsystems.The matrix or resin is the othermajor component of an FRP/Composite. Resin systems areselected for their chemical, electricaland thermal properties. The twomajor classes of resins are thermosetsand thermoplastics.Thermoset ResinsThermosetting polymers are usuallyliquid or low melting point solidsthat can easily combine with fibersor fillers prior to curing. Thermosetsfeature cross-linked polymer chainsthat become solid during a chemicalreaction or “cure” with the applicationof a catalyst and heat. The highlevel of cross-linking providesfor reduced creep compared tothermoplastics. The thermosetreaction is essentially irreversible.Among the thermoset resins forFRP/Composites, the family ofunsaturated polyesters is by far themost widely used. These resins aresuitable for practically every moldingprocess available for thermosets.Polyesters offer ease of handling,low cost, dimensional stability, anda balance of good mechanical,chemical, and electrical properties.
They can be formulated for highresistance to acids, weak alkalies andorganic solvents. They are notrecommended for use with strongalkalis. Other formulations aredesigned for low or hightemperature processing, for roomtemperature or high-temperaturecure, or for flexible or rigid endproducts.Vinylesters provide excellentThisresistance to water, organic solventsand malkalis, but less resistance toacids than polyesters. Vinylestersare stronger than polyesters andmore resilient than epoxies. Moldingconditions for vinylesters are similarto those for polyesters.Epoxies are another family ofthermoset resins used in FRP/Composites. They have excellentadhesion properties and are suitedfor service at higher temperatures –some as high as 500oF. Epoxy-matrixFRP/Composites are processed by anyof the thermoset methods. Epoxiesare more expensive than polyesters,and cure times are longer, but theirextended range of properties canmake them the cost/performancechoice for critical applications.Epoxy/fiber structures have generallyhigher fatigue properties than polyesters.Polyurethanes are a family of resinsthat offer very high toughness, highelongation, faster cure times andgood coupling to a variety ofreinforcements. Polyurethanes areeasily foamed in a controlled process toproduce a wide range of densities.6Additives are easily incorporatedinto resin systems to providepigmentation, flame retardance,weather resistance, superior surfacefinish, low shrinkage and otherdesirable properties.Gel coats consisting Also,of a penetrationspecialo formulation provide anresinextremely smooth next-to-moldsurface finish on FRP/Composites.They are commonly applied inhand lay-up and spray-up processesto produce a tough, resilient,weather-resistant surface. Gel coats,which may be pigmented, are sprayedonto the mold before thereinforcement and resin areintroduced.Other thermosetting resin systems,generally formulated with choppedstrand or milled fiber reinforcementfor compression or transfermolding are:Phenolics-Good acid resistance,good fire/smoke, and thermalproperties.Silicones -Highest heat resistance,low water absorption, excellentdielectric properties.Melamines -Good heat resistance,high impact strength.Diallyl phthalates -Good electricalinsulation, low water absorption.Thermoplastic ResinsThermoplastic polymers can softenand become viscous liquids whenheated for processing and thenbecome solid when cooled. Theprocess is reversible allowing areasonable level of process wasteand recycled material to be reusedwithout significant effect on theend product. Thermoplastic resinsallow for faster molding cycle timesbecause there is no chemicalreaction in the curing process.Parts may be formed as fast as heatcan be transferred into and out ofthe molding compound.Polypropylene and polyethylene arethe most common thermoplasticresins used in FRP/Composites.They have excellent resistance toacids and alkalies and have goodresistance to organic solvents. Theirrelatively low melting points allowfor rapid processing at lower cost.Nylon and Acetal are highlyresistant to organic solvents andmay also be used where increasedmechanical properties are required.
Another form of reinforcementused with LCM as well as mostother molding processes is calledmat. This material is a randomdistribution of fibers in roll orsheet form. Its use is limited toparts that are relatively flat, havecurvature in only one plane, or havea slight compound curvature.Liquid Composite Molding (LCM)The molding experience of thousandsof applications in the past fivedecades has enabled FRP/Composites polymer chemists todevelop a number of standardresin-reinforcement-additivecombinations that are used for mostproduction needs. Industryresearch teams also stand ready tocustom design new blends ofmaterials to provide the exact needsThisof newm applications. Because mosthigh production-volume FRP/Composite parts are made bycompression molding, severalready-to-mold material forms havebeen developed to facilitate andspeed the molding process. Eachof these forms is designed to bestproduce a specific type of finishedproduct and provide a distinctive set ofproperty and appearance features.A fiber preform of the part is producedby forming fibers and a resin binderin a controlled manner to the sameshape as the part to be molded.The combination is cured toprovide physical integrity duringhandling and moldingoperations.Also,penetrationoParts molded using LCM withpreforms are particularly suited forboxlike, deep-drawn shapes inFRP/Composite parts. The fibersstay in place during molding andalso ensure good wet-out of thematrix resin, which is added at thepress. The result is uniform propertiesin the plane of the part walls becausethere is no flow of reinforcementduring molding. The fiber contentof preform-molded parts can becontrolled from 15 percent to amaximum of approximately 50 percentby weight. Fiber lengths vary from1/2” to 3”.FRP/Composite Compound FormsA few ready-to-mold compoundforms have been developed to supportthe highest volume productionwhile maintaining good mechanicalproperties in complicated parts.Of these, sheet molding and bulkmolding compounds (SMC/BMC)are based on thermoset resins whilethermoplastic resins are used inglass mat thermoplastic and longfiber-reinforced thermoplastic(GMT/LFTP). Sheet Molding Compound (SMC)SMC contains long glass fibers (1”to 2”) dispersed in a resin matrix.The fiber arrangement can bedirectional, random, or a combinationof both. SMC is manufactured in ahighly automated, continuous flowprocess. The compound takes theform of a flexible, leather-like sheetthat is easily cut, weighed and placed inthe mold for curing to the desiredpart configuration.F7
Compression-Molded ReinforcedThermoplasticReinforced thermoplastics can becompression molded into many partsusing processes similar to those forSMC and BMC. There are twomaterial forms available for such molding.oAlso, penetrationThisA continuous process creates a “sandwich” of glass and resin paste between sheets of film in SMC production.mStandard SMC contains up to 35percent of randomly oriented fibersby weight. Because there is nomixing or extruding involved inpreparing sheet molding compound, thefibers remain undamaged and at theiroriginal lengths. This plus the higherfiber loading provides very goodmechanical properties in compression-molded SMC parts, especiallythose having relatively thin crosssections.FRP/Composite parts molded fromSMC are characterized by high strength,very smooth surfaces and excellent detailin complex shapes. However, becauseSMC flows in the mold, fiber orientationand properties can vary throughout apart, particularly in deep-drawn shapes.Several variations of SMC are available.One contains 8” to 12” unidirectionalfibers and another contains continuousunidirectional fibers. Other versions havehigher fiber contents of up to 65 percentby weight and are used for structuralapplications.8 Bulk Molding Compound (BMC)BMC is a mixture of short (1/8 to1/2 in.) fibers with resin containingfiller, a catalyst, pigment and otheradditives required by the application.The premixed material, having theconsistency of modeling clay, isusually extruded into rope or logshapes for easy handling.The strength of BMC-molded FRP/Composite is lowest of those madefrom ready-to-mold forms becausethe mixing operation degrades thefibers and the fiber content is lowest.In addition, properties are subject tofiber orientation because the compoundmust flow to fill the mold. However,BMC is economical and satisfies awide variety of high-volume,compression-molded parts requiringfine finish, dimensional stability,complex features, and moderateoverall mechanical properties.Glass Mat Thermoplastic (GMT) is afiberglass reinforced sheet that hasbeen available for many years. It istypically 30% – 50% glass fiber in apolypropylene matrix. When heatedabove its melting point, GMT can becompression molded very similar toSMC.Long Fiber-reinforced Thermoplastic(LFTP) is a process that has morerecently been commercialized. Thisprocess uses a special thermoplasticextruder to compound thermoplasticpellets with long fibers of up to 2inches. The melted resin/fiber material isejected from the extruder as a charge thatis immediately compression molded,very similar to BMC.The properties of these moldingsvary depending on the fiber fractionand type of thermoplastic used.Typically such materials are lowerweight and have high impact resistance,but have lower modulus and lowerheat resistance than those usingthermoset resin.The most common thermoplasticresins are polypropylene andpolyethylene; however, engineeringplastics such as thermoplasticpolyesters or nylon can be used toachieve higher properties.
FRP/CompositeMolding MethodsResponding to the requirementsof a demanding marketplace, the FRP/Compositeindustry is ever on the movedeveloping new resin systems, newtypes of reinforcements, and newcombinations of these materials.And in keeping with theseadvancements, processes continueto be improved, refined and furtherautomated to provide better outputwhile reducing handling time andcosts. Today’s presses feature evercloser control of processing times,temperatures and pressures, as wellas part dimensions. Overall part sizecapability continues to increase,permitting the commonplaceproduction of sizes and weights ofFRP/Composites not possible just afew years ago.In addition to the wide variety ofmaterial combinations, there aremany choices available for processingFRP/Composite products. Thesechoices provide for even greaterflexibility in optimizing the shape,properties and production cost ofFRP/Composite components.Matched die molding, contact moldingand more specialized molding methodsrepresent the top-level choices. Thedesigner is encouraged to collaboratewith a molder and/or materialsupplier to optimize the application.Matched Die MoldingMatched die molding methodsproduce highly consistent, net-shapeand near-net shape parts with twofinished surfaces and low labor cost.These methods include compression;low pressure, low temperaturecompression; transfer compression;resin transfer, injection; andstructural reaction injection molding.finished surfaces, and outstandingpart to part repeatability. Trimmingand finishing costs are minimal. Compression MoldingThe molding process is an economicalcompression molding method formanufacturing intermediate volumesof parts using a low-pressure cureand inexpensive molds.Compression molding is the primarychoice for most high-volume FRP/Composite parts made from BMC,SMC, Liquid Composite (preform),GMT, or LFTP. The high-pressuremolding process produces highstrength, complex parts in a widevariety of sizes. Matched metal moldsare mounted in a hydraulic ormechanical molding press. The materialcharge is placed in the open mold.The heated mold halves are closed,and pressure is applied. Moldingtime, depending on part size andthickness, ranges from about one tofive minutes. Inserts and attachmentscan be molded in.Compression-molded FRP/Composites are characterizedby net size and shape, two excellent Low Pressure-Low TemperatureCompression MoldingThis method uses composite ornickel-shell molds that may not beheated, but usually are constructed withcoils to heat or control mold temperature.Preform or mat reinforcement isplaced on the lower mold half anda resin/filler mixture is added.The mold is closed under moderatepressure of 20 to 200 psi, and theFRP/Composite part cures. This issuited mainly for relatively simpleshapes, without ribs or bosses. Transfer Compression MoldingThis process is characterized bymolding operations using a transfercylinder that is usually built into thetool. The material charge made ofresin, reinforcement and additives ismoved to the transfer cylinder andsubsequently forced into the closedmold cavity or cavities by thetransfer piston. It is best suited forvery thick parts, like transformerbobbins, and is very effective formultiple-cavity molds.1
Resin Transfer Molding (RTM)Resin Forced into Mold Under PressureSuitable for medium-volume productionof rather large FRP/Compositecomponents, resin transfer molding isusually considered an intermediateprocess between the relatively slowThisspray-up with lower tooling costs andthe mfaster compression-moldingmethods, which require higher toolingcosts. RTM parts, like compressionmolded parts, have two finishedsurfaces, but molded parts requiresecondary trimming. Gel coats maybe used to provide a high-quality,durable finish. Reinforcement mat orwoven roving is placed in the mold,which is then closed and clamped.Catalyzed, low-viscosity resin ispumped in under pressure, displacingthe air and venting it at the edges,until the mold is filled. Molds forthis low-pressure system areusually made from FRP/Compositesor nickel-shell faced FRP/Composite construction. Injection MoldingReinforced thermoset moldingcompounds can be injectionmolded in similar equipmentcommonly used for thermoplasticresins. The principle difference liesin the temperatures maintained invarious areas of the system. Withthermoplastics, the injection screwand chamber are maintained at arelatively high temperature, and thedie is cooled so the Also,moldedpart posite, the screw andchamber are cooled so the resindoes not cross-link and gel, and thedie is heated so it does cross-linkand cure. Injection molding offershigh-speed production and lowdirect labor costs. Combined withthe excellent mechanical propertiesavailable from a long-fibered BMC,the result is a capability for highvolumes of complex parts withproperties approaching those ofcompression or transfer molded parts. Structural Reaction InjectionMolding (SRIM)This method is suitable for medium-tohigh volume FRP/Composite partsrequiring superior strength with no lossin toughness or flexibility. The SRIMprocess also produces parts with highimpact resistance and lower weight, andis excellent for larger part sizes.Like injection molding, resin isinjected into a closed mold. However,the SRIM process utilizes a preform orreinforcing mat, which is placed intothe mold prior to closure, resulting ineven distribution of glass and uniformmechanical properties.SRIM parts offer two finished surfaces,but the polyurethane systems typicallyused do not provide a good cosmeticsurface or a high level of dimensionaldurability. For structural applications,however, the low temperature andpressure characteristics of SRIM makelarge structural shapes practical.Contact Molding MethodsContact, or open mold methodsprovide a lower tooling cost whenonly one finished surface is required.These methods also allow for ashorter product development cyclebecause of the simplified toolingfabrication process. Hand Lay-UpThe simplest and oldest of thefabrication processes for FRP/Composites, hand lay-up, is used inlow-volume production of largecomponents such as boat hulls andassociated parts.A pigmented gel coat is first sprayedonto the mold for a high-quality surface.When the gel coat has cured, glassreinforcing mat and/or wovenroving is placed on the mold, andthe catalyzed resin is poured,brushed or sprayed on. Manualrolling then removes entrapped air,densifies the FRP/Composite andthoroughly wets the reinforcementwith the resin. Additional layers ofm or woven roving and resin arematadded for thickness. A catalyst oraccelerator initiates curing in theresin system, which hardens theFRP/Composite without external heat.
sParts have one finishedHand lay-up offers low-cost tooling,simple processing and a wide range ofpart size potential.DesignParts haveonechangesfinishedaresmade easily. Parts have one finishedand require secondary trimming.ssurface Spray-UpThismSimilar to hand lay-up in simplicity,Similar tohandgreaterlay-upin fersgreater shapecomplexityandfasterproduction.It toouses aand fasterproduction.It too useslow-costopenmold (one finishedpart alow-cost open(one ace),roomtemperaturecuringresin,andis suitedfor producingresin, FRP/Compositeand is suited for producinglargeparts such aslarge FRP/Compositepartshoodssuch astub/showerunits and ventintub/showerunitsquantities.and vent hoodslowto moderateCureinislow to moderatequantities. Cureusuallyat room temperature,but isusuallyat room temperature,but ofcanbe acceleratedby applicationcan be acceleratedby application ofmoderateheat.Wovenmoderate heat.rChoppedfiber reinforcement andChopped resinfiber arereinforcementcatalyzeddeposited inandthecatalyzedare depositedin themoldfromresina combinationchopper/mold froma combinationspraygun. Aswith lay-up, chopper/manualspray gun.As entrappedwith lay-up,manualrollingremovesair andwetsrollingremovesentrapped airWovenand wetsthefiberreinforcement.the fiberreinforcement.rrovingWovenis oftenadded in specificareasrovingis often addedin specificareasrforthicknessor greaterstrength.for thicknessgreaterPigmentedgelorcoatscanstrength.be used toPigmentedgel coatscolorfulcan be usedtoproducea smooth,surface.produce a smooth, colorful surface. Vacuum Bag MoldingFlexible FilmSealHeat SourceEdge m bag processingaoVacuumbageliminateprocessinguses a airvacuumtoentrappedvacuumto eliminateairand excessresin fromentrappeda lay-up formandexcessa resina lay-upformon eithermale fromor femalemold.Aoneither a maleor(usuallyfemale usuallyalcohol or nylon)placed polyvinylover thealcoholor nylon)is placedoverAthelay-up andsealed atits edges.lay-upsealed onat itsAvacuumandis drawntheedges.bag formedvacuumis anddrawnthe bag formedby the film,the onFRP/Compositeisbythe ureiscured,at roomor witheithermoderateheattempera
Plastic/Composite (FRP/Composite) material system. Materials and processes are presented along with design guidelines and comparisons to alternate materials. Because of the versatility of FRP/Composites, the designer is encouraged to collaborate with a mol