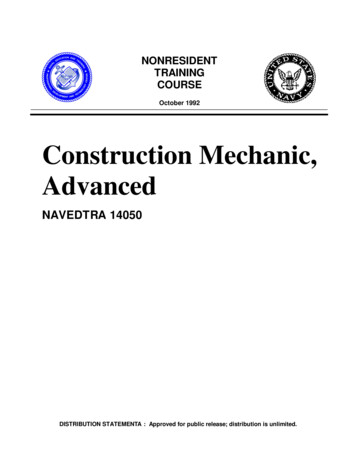
Transcription
NONRESIDENTTRAININGCOURSEOctober 1992Construction Mechanic,AdvancedNAVEDTRA 14050DISTRIBUTION STATEMENTA : Approved for public release; distribution is unlimited.
Although the words “he,” “him,” and“his” are used sparingly in this course toenhance communication, they are notintended to be gender driven or to affront ordiscriminate against anyone.DISTRIBUTION STATEMENT A: Approved for public release; distribution is unlimited.
PREFACEBy enrolling in this self-study course, you have demonstrated a desire to improve yourself and the Navy.Remember, however, this self-study course is only one part of the total Navy training program. Practicalexperience, schools, selected reading, and your desire to succeed are also necessary to successfully roundout a fully meaningful training program.THE COURSE: This self-study course is organized into subject matter areas, each containing learningobjectives to help you determine what you should learn along with text and illustrations to help youunderstand the information. The subject matter reflects day-to-day requirements and experiences ofpersonnel in the rating or skill area. It also reflects guidance provided by Enlisted Community Managers(ECMs) and other senior personnel, technical references, instructions, etc., and either the occupational ornaval standards, which are listed in the Manual of Navy Enlisted Manpower Personnel Classificationsand Occupational Standards, NAVPERS 18068.THE QUESTIONS: The questions that appear in this course are designed to help you understand thematerial in the text.VALUE: In completing this course, you will improve your military and professional knowledge.Importantly, it can also help you study for the Navy-wide advancement in rate examination. If you arestudying and discover a reference in the text to another publication for further information, look it up.1992 Edition Prepared byEQCM Thomas A. BrowningPublished byNAVAL EDUCATION AND TRAININGPROFESSIONAL DEVELOPMENTAND TECHNOLOGY CENTERNAVSUP Logistics Tracking Number0504-LP-026-7230i
Sailor’s Creed“I am a United States Sailor.I will support and defend theConstitution of the United States ofAmerica and I will obey the ordersof those appointed over me.I represent the fighting spirit of theNavy and those who have gonebefore me to defend freedom anddemocracy around the world.I proudly serve my country’s Navycombat team with honor, courageand commitment.I am committed to excellence andthe fair treatment of all.”ii
CONTENTSPageCHAPTERPublicWorks TransportationAIfa CompanyEngineShops 7. Clutches8. Air.: .Overhaul.11. Troubleshooting Transmissions,Differentials.Transfer Cases, and12. Wheel and Track Alignment.INDEXSystems.4-l.6-l.7-l8-1.9-l.10-l.13. Air-Conditioning.3-l.5-lBrake Systems .Transmissionsl- 12-l.and Automatic9. The Shop Inspector10. HydraulicsSystemsand TroubleshootingCompressor.and Overhaul5. Fuel System Overhaul6. InspectingShops Supervisor.11-l.12-l.13-l. . . . . . . . . . . . . . . . . . . . . . . . . . . . . . . . . INDEX-l.
INSTRUCTIONS FOR TAKING THE COURSEassignments. To submit youranswers via the Internet, go to:ASSIGNMENTSThe text pages that you are to study are listed atthe beginning of each assignment. Study thesepages carefully before attempting to answer thequestions. Pay close attention to tables andillustrations and read the learning objectives.The learning objectives state what you should beable to do after studying the material. Answeringthe questions correctly helps you accomplish theobjectives.http://courses.cnet.navy.milGrading by Mail: When you submit answersheets by mail, send all of your assignments atone time. Do NOT submit individual answersheets for grading. Mail all of your assignmentsin an envelope, which you either provideyourself or obtain from your nearest EducationalServices Officer (ESO). Submit answer sheetsto:SELECTING YOUR ANSWERSRead each question carefully, then select theBEST answer. You may refer freely to the text.The answers must be the result of your ownwork and decisions. You are prohibited fromreferring to or copying the answers of others andfrom giving answers to anyone else taking thecourse.COMMANDING OFFICERNETPDTC N3316490 SAUFLEY FIELD ROADPENSACOLA FL 32559-5000Answer Sheets: All courses include one“scannable” answer sheet for each assignment.These answer sheets are preprinted with yourSSN, name, assignment number, and coursenumber. Explanations for completing the answersheets are on the answer sheet.SUBMITTING YOUR ASSIGNMENTSTo have your assignments graded, you must beenrolled in the course with the NonresidentTraining Course Administration Branch at theNaval Education and Training ). Following enrollment, there aretwo ways of having your assignments graded:(1) use the Internet to submit your assignmentsas you complete them, or (2) send all theassignments at one time by mail to NETPDTC.Grading on the Internet:Internet grading are:assignmentDo not use answer sheet reproductions: Useonly the original answer sheets that weprovide— reproductions will not work with ourscanning equipment and cannot be processed.Follow the instructions for marking youranswers on the answer sheet. Be sure that blocks1, 2, and 3 are filled in correctly. Thisinformation is necessary for your course to beproperly processed and for you to receive creditfor your work.Advantages to you may submit your answers as soon asyou complete an assignment, and you get your results faster; usually by thenext working day (approximately 24 hours).COMPLETION TIMECourses must be completed within 12 monthsfrom the date of enrollment. This includes timerequired to resubmit failed assignments.In addition to receiving grade results for eachassignment, you will receive course completionconfirmation once you have completed all theiv
PASS/FAIL ASSIGNMENT PROCEDURESFor subject matter questions:If your overall course score is 3.2 or higher, youwill pass the course and will not be required toresubmit assignments. Once your assignmentshave been graded you will receive coursecompletion milComm: (850) 452-1001, Ext. 1826DSN: 922-1001, Ext. 1826FAX: (850) 452-1370(Do not fax answer sheets.)Address: COMMANDING OFFICERNETPDTC (CODE 314)6490 SAUFLEY FIELD ROADPENSACOLA FL 32509-5237If you receive less than a 3.2 on any assignmentand your overall course score is below 3.2, youwill be given the opportunity to resubmit failedassignments. You may resubmit failedassignments only once. Internet students willreceive notification when they have failed anassignment--they may then resubmit failedassignments on the web site. Internet studentsmay view and print results for failedassignments from the web site. Students whosubmit by mail will receive a failing result letterand a new answer sheet for resubmission of eachfailed assignment.For enrollment, shipping,completion letter .navy.milToll Free: 877-264-8583Comm: (850) 452-1511/1181/1859DSN: 922-1511/1181/1859FAX: (850) 452-1370(Do not fax answer sheets.)Address: COMMANDING OFFICERNETPDTC (CODE N331)6490 SAUFLEY FIELD ROADPENSACOLA FL 32559-5000COMPLETION CONFIRMATIONAfter successfully completing this course, youwill receive a letter of completion.NAVAL RESERVE RETIREMENT CREDITERRATAIf you are a member of the Naval Reserve, youwill receive retirement points if you areauthorized to receive them under currentdirectives governing retirement of NavalReserve personnel. For Naval Reserveretirement, this course is evaluated at 17 points.These points will be credited in units, as follows:Errata are used to correct minor errors or deleteobsolete information in a course. Errata mayalso be used to provide instructions to thestudent. If a course has an errata, it will beincluded as the first page(s) after the front cover.Errata for all courses can be accessed andviewed/downloaded at:Unit 1 - 12 points upon satisfactory completionof assignments 1 through 7.http://www.advancement.cnet.navy.milSTUDENT FEEDBACK QUESTIONSUnit 2 – 5 points upon satisfactory completionof Assignment 8 through 11.We value your suggestions, questions, andcriticisms on our courses. If you would like tocommunicate with us regarding this course, weencourage you, if possible, to use e-mail. If youwrite or fax, please use a copy of the StudentComment form that follows this page.(Refer to Administrative Procedures for NavalReservists on Inactive Duty, BUPERSINST1001.39, for more information about retirementpoints.)v
Overhaul; Troubleshooting Electrical Systems;Fuel System Overhaul; Inspecting andTroubleshooting Brake Systems; Clutches andAutomatic Transmissions; Air CompressorOverhaul; The Shop Inspector; Hydraulics;Troubleshooting Transmissions, Transfer Cases,and Differentials; Wheel and Track Alignment;and Air-Conditioning Systems.COURSE OBJECTIVESIn completing this nonresident training course,you will demonstrate a knowledge of the subjectmatter by correctly answering questions on thefollowing: The Public Works TransportationShops Supervisor; The ALFA Company ShopsSupervisor; Engine Troubleshooting andvi
Student CommentsCourse Title:Construction Mechanic, AdvancedNAVEDTRA:14050Date:We need some information about you:Rate/Rank and Name:SSN:Command/UnitStreet Address:City:State/FPO:ZipYour comments, suggestions, etc.:Privacy Act Statement: Under authority of Title 5, USC 301, information regarding your military status isrequested in processing your comments and in preparing a reply. This information will not be divulged withoutwritten authorization to anyone other than those within DOD for official use in determining performance.NETPDTC 1550/41 (Rev 4-00)vii
CHAPTER 1PUBLIC WORKSsupervisor in the PW maintenance branch, youwould probably not have to plan and constructa new transportation shop, but, rather, wouldsupervise the repair of equipment. However, ifyou are involved in the establishment of a newbase, you will probably be consulted about thelocation and layout of the maintenance shops.You can obtain detailed information on thephysical layout of the buildings by referring toNaval Facilities Planning Guide, P-437, FacilitiesNumber 214 20B, Drawing 6028198. The locationof tools and shop equipment depends on theamount and type of equipment to be maintained.The PW transportation organization discussedin this chapter is typical of the type usually foundwithin a public works activity. The titles andorganization may vary from activity to activity.To learn more about these organizations, youshould obtain and study current NAVFACinstructions and publications that pertain to thepublic work centers and public work departments.By referring to figure 1-1, you can see that theTRANSPORTATION SHOPSSUPERVISORA supervisor should possess a large amountof TACT and DIPLOMACY. Directing shopactivities requires that you contact all types ofpeople; for example, the mechanics who work foryou, the personnel (military and/or civilian) whooperate the equipment, and the officer (or civilian)to whom you are responsible. You must be carefulnot to let prejudices interfere with your goodjudgment.A transportation maintenance shop supervisorwill need all of his past experience in diagnosingmechanical troubles accurately, scheduling andplanning repair work skillfully, using all kinds ofrepair equipment, and directing the many activities in maintaining transportation and earthmoving equipment.At some time during your career in the Navy,you may be assigned as a foreman in a publicworks (PW) transportation maintenance shop.You may also have to serve as supervisor of aConstruction Battalion equipment maintenanceshop. Because of the variation in the two differenttypes of duty, the responsibilities of a foremanin a PW transportation maintenance shop will bediscussed in this chapter, and the battalionequipment company shops supervisor’s responsibilities will be discussed in the following chapter.Although many of the positions have the samebasic duties, the methods of doing the work maydiffer considerably. Certain areas of cost controlvary a great deal. Duty in a transportationmaintenance shop includes work of a continuingnature. Therefore, to provide continuity, civilservice personnel are also employed.PUBLIC WORKS TRANSPORTATIONDEPARTMENT FUNCTIONALORGANIZATIONA PW transportation department of a navalshore facility is generally stationary. As aFigure 1-1.—Functional organization for transportationmanagement.1-1
4. Maintaining a balanced workload forsubordinate work units by shifting personneleffectively among the units5. Coordinating the work in areas of responsibilities with other activities and department/division supervisory personnel to maintaina balanced scheduled work flow6. Reviewing and analyzing production,cost, and personnel utilization records to evaluatethe progress of work and to control or reducecosts7. Reviewing completed work records (ShopRepair Order, NAVFAC Form 9-11200/3A,shown in figure 1-2, and other computer reports)to assure that production and quality standardsare met8. Inspecting the shop areas periodically andchecking safety conditions, cleanliness, security,requirements for materials, and shop equipment9. Acting on any personnel matterconcerning subordinates and assisting in theresolution of grievances referred by subordinatesupervisors10. Promoting safety programs within theimmediate organization, reviewing the safetyperformance of the supervisors, and initiatingcorrective action as required11. Seeing that progress, production, cost,and other records are prepared, maintained, andconsolidated12. Developing training programs foremployees and subordinate supervisorstransportation division is broken down into twobranches: operations branch and equipmentmaintenance branch. Note that both come underthe control of the transportation division director,who reports through a chain of command to thepublic works officer (PWO).DUTIES AND RESPONSIBILITIESOF SUPERVISORY PERSONNELThis phase of our discussion deals with theduties and responsibilities of various supervisorypersonnel within the maintenance branch. Theindividual assignments depend upon the needs ofthe activity and the skill and experience ofpersonnel available. The public works officermakes the final decision.TRANSPORTATION DIVISIONDIRECTORAs head of the transportation division, thetransportation director exercises full technical,managerial, and administrative responsibility fororganizing, directing, and controlling the workof the division. The director also functions as thetechnical advisor within and outside the activityin planning and procuring vehicle/equipmentrequirements for the activity and other supportedcustomers.The transportation director exercises completemanagerial responsibilities for the efficient,economical, and timely administration of thedivisions; directs operations assignments; managesscheduled preventive maintenance (PM) as wellas repair/overhaul; and is charged with therequisition and disposition of automotive vehicles,construction equipment, materials-handling equipment, and miscellaneous specialized equipment.PRODUCTION CONTROLSUPERVISORThe production control supervisor is responsible for receiving, inspecting, andclassifying, within applicable Navy codes, all newand used equipment; preparing reports onequipment received; scheduling equipment intothe shop for its first servicing; and arranging forits inclusion into the PM program. Additionally,the production control supervisor determines partsand tools required to support equipment duringits life cycle; directs the inspection of vehiclescoming into the shop to find the nature and extentof repair or PM service required; and determinesthe most economical means and methods ofrepairs. The production control supervisor appliesstandard hours and cost estimates on individualequipment jobs; initiates shop repair orders; andschedules work into the various work centers/shops for orderly accomplishment. Finally, theproduction control supervisor directs theinspection of the mechanics’ work while inprogress; ensures a quality inspection uponMANAGER OF THE EQUIPMENTMAINTENANCE BRANCHThe manager of the maintenance branch isresponsible for planning, work direction, andadministration, and acts as, and assumes theduties of, the transportation director in case ofthe absence of that person. The maintenancebranch’s responsibilities include the following:1. Preparing and submitting the maintenancedivision fiscal financial budget2. Scheduling work for subordinatesupervisors and planning for the efficient use ofmaterials and equipment3. Organizing, coordinating, and directingthe work activities of personnel and unitssupervised1-2
Figure 1-2.—Shop Repair Order, NAVFAC Form 9-11200/3A.completion of this work; and directs the maintenance of PM records, shop backlog records, andvehicle history files.4. Consulting with higher authority and staffpersonnel to make sure that appropriate tools,materials, and equipment are available asneeded5. Requesting and coordinating the servicesand work of other shops when required6. Assigning work by written or oral orders7. Assisting in the training of subordinatesin work methods, procedures, and the operationof tools and equipment, both new and already inuse8. Certifying that the work is efficient andeconomical and that the work is performedsafely9. Anticipating operational problems andacting to overcome delays10. Directing and recommending changes inshop layout to improve efficiency11. Ensuring that subordinates houseclean12. Issuing and enforcing safety practices andfire regulationsMAINTENANCE AND REPAIRFOREMANThe foreman of the maintenance and repairshop supervises subcenters, such as the body andpaint shop, battery shop, tire shop, toolroom, andlubrication shop. Responsibilities of the foremaninclude the following:1. Establishing priorities and sequences inwhich scheduled workloads will be accomplished,primarily on a day-to-day/job-by-job basis2. Analyzing and interpreting shop repairorders, work requests, and other workdocumentation and specifications to determinework requirements3. Assigning work among subordinates andproviding specific material requirements1-3
the equipment on hand so you can point outmaintenance services that need attention. It isbetter to hold the instructions with small groupsand to keep them as informal as possible. Do notforget to stress operator maintenance on theoverall operating efficiency of the equipment.13. Checking attendance and leave ofsubordinates and other personnel mattersCONSTRUCTION EQUIPMENT SHOPFOREMANThe foreman of the construction and specialized equipment shop supervises the machineshop as a subcenter. The responsibilities arebasically the same as those given under themaintenance and repair foreman, except for thetechnical supervision. This shop is responsible forthe maintenance, repair, and major overhaul(mechanical and electrical) of specializedequipment, such as tractors, graders, ditchdiggers,bulldozers, road rollers, asphalt machines, farmtractors, jet starters, auxiliary power units,emergency generators, pumps, and aircraft towtractors.The machine shop bores cylinders; rebuilds alltypes of gasoline and diesel engines, automatictransmissions, and differentials; and performsother related repairs.SERVICE STATION MAINTENANCEService station maintenance is the service youwould expect from any first-rate filling stationwhen you purchase fuel; namely, washing thewindshield and checking the oil, battery andradiator water, fan belt, tire condition, and soforth. Unfortunately, shortages of personnel havesometimes curtailed this type of maintenance.Service station maintenance is a visible area ofpublic works but is not intended to relieve theoperators of their responsibility.SAFETY INSPECTIONSVehicles will be inspected periodically byqualified automotive inspection personnel forsafety as follows:Each motor vehicle will be inspected for safetyat intervals not to exceed 12 months or 12,000miles, whichever occurs first. To avoidunnecessary downtime, perform the safetyinspection at the time of the scheduledserviceability inspection according to themanufacturer’s recommendation.All deficiencies uncovered during the safetyinspection that affect the safe operation of thevehicle will be corrected before the vehiclebecomes operational again.PREVENTIVE MAINTENANCEThe most important phase of the maintenancesystem is scheduled periodic preventive maintenance (PM). PM is the systematic inspection,detection, and correction of potential equipmentfailures before they develop into major defects.The purpose of PM is to keep equipment in safeand reliable condition with maximum equipmentavailability and minimum cost of maintenance.OPERATOR MAINTENANCEUNSCHEDULED MAINTENANCESERVICEOperators are the first line of defense againstequipment wear, failure, and damage. Equipmentmust be inspected by the operator daily—before,during, and after operations—so that defects ormalfunctions can be detected before they resultin serious damage, failure, or accident.It is your responsibility, as a CM1, to see thatthe operators are performing their duties. Youshould work with the operations branch in making recommendations regarding operator PM.Changes may be necessary in the operator PM tocope with certain operating conditions. You mayneed to set up classes of instruction for theoperators so that they will become familiar withthe right way to maintain their equipment,especially when new equipment is received in theactivity. If you do set up classes, be sure tocoordinate your training periods with the foremanin charge of the equipment operations branch sothat you do not interfere with the foreman’sequipment operating schedules. Also, try to haveUnscheduled maintenance service is the correction of deficiencies reported by the vehicleoperator that occur between scheduled safety orother inspection and services prescribed by themanufacturer. Unscheduled maintenance serviceswill be limited to correcting only those itemsreported as deficient by the operator andconfirmed by qualified inspection personnel.Unreported deficiencies observed by the inspectorat an unscheduled service and, in particular, thoseaffecting safety are to be corrected before thevehicle is released for service.COST CONTROLThe Navy’s cost control system is designed toobtain complete cost data on maintenance andoperation of automotive, construction, fire fighting,railway, weight-handling, and materials-handling1-4
transportation office. These reports provide thefacts required by supervisors to pinpoint deficientareas and should be used for corrective action.The objectives of the transportationmanagement reports are to provide the following:equipment. Actual performance of maintenancework is compared to hourly standards for suchwork, as established and published by variousmanufacturers and the Naval FacilitiesEngineering Command (NAVFAC), to determineefficiency of maintenance operations. The Navyalso uses cost control to justify the performanceof repairs at its activities.1. Information on the productivity of maintenance shop personnel (actual versus standardhours)2. Data on overhead costs3. Comparison between activity costs andcommercial costs4. Comparison between actual direct laborhours expended and established maintenanceinput standards5. Comparison between actual and standardmaintenance costsRECORDS AND REPORTSIn the cost control system, all costs accumulated in the maintenance and operation ofthe equipment are recorded and charged toappropriations and allotments. These costs maybe director indirect labor or material. They mayalso include services provided, such as shop stores,utilities, and even building maintenance.To evaluate performance and to assist in effective management of transportation maintenance, a series of transportation managementreports has been designed that will furnish usefulinformation to management at all levels. Thesereports are prepared by the accountable fiscaloffice from the cost records maintained in thatoffice and from feeder reports prepared by theVariances indicated in reports frequentlyrequire a searching review of detailed shop recordsto determine the causes. The individual ShopRepair Order, NAVFAC Form 9-11200/3A,shown in figure 1-2, and the Shop RepairOrder (Continuation Sheet), NAVFAC Form9-11200/3B, shown in figure 1-3, contain all ofthe basic data required for this review.Figure 1-3.—Shop Repair Order (Continuation Sheet), NAVFAC Form 9-11200/3B.1-5
A shop repair order (SRO) is the transportation equivalent of the specific job order. It isinitiated by the control section inspector/estimatoror other specifically authorized personneldesignated by the equipment maintenance branchsupervisor. It is the authorizing document,estimating form, and cost control record ofmaintenance expenditures. Repair costs areestimated in advance to ensure that costs staywithin economic limitations and to provide astandard against which to measure job performance and productivity of the mechanics.Estimates for transportation repairs are takenfrom commercial Flat Rate Manuals or estimatingguides. Labor costs and material costs are loggedon the SRO by shop personnel, and the completeddocument then serves as a principal source of datafor transportation reports and analysis.COST JUSTIFICATIONThe Navy system of preventive maintenance,implemented by the cost control system with itsaccounting procedures and reports, is a continuingjustification for the transportation maintenanceshop’s existence. Costs must be justified unlessthe work is highly classified or the geographicallocation is extreme.Remember that needed repairs alone do notjustify repair by the service maintenance shop.PRESERVATION, STORAGE, ANDDEPRESERVATION OF VEHICLESAND EQUIPMENTThere is more to storing vehicles andequipment than merely driving them into openareas, warehouses, or active storage. The processof preparing vehicles and equipment for storageis complex. It is important that you consider allcomponents of the equipment, as well as the basicunit, to ensure efficient operation with a minimumamount of work after storage. The objective ofpreservation and storage is to provide efficient andeconomical protection to components and equipment from environmental and mechanical damageduring handling, shipment, and storage from thetime of original purchase until they are used.NAVFAC P-434, Management and OperationsManual for Construction Equipment Departments,chapters 8 and 9 and appendix E, contains thestandards and guides for equipment preservation.DEPTH OF MAINTENANCE,REPAIR, AND OVERHAULThe depth of maintenance, repair, andoverhaul is governed by many factors, mainlyeconomics. The goal is to provide the best serviceavailable at the least possible costs.The geographic location of an activity has agreat influence on the depth of maintenance,repair, and overhaul that a maintenance shopmust perform. Maintenance costs must comparewith national standards. It is easy to see that anactivity near a large city, where many repairservices are available at commercial shops, islimited as to the type of repairs allowed. Becauseof the large volume of work, many of thesespecialized commercial shops can perform servicesat a reduced cost. When the commercial shop isnearby, there are no appreciable transportationor shipping costs to be added to the cost ofrepairs. On the other hand, an activity located agreat distance from commercial sources of repairservices and supplies would be able to justifydoing its own major repairs because of the time,need, and shipping charges involved in having thework performed outside.The three levels of preserving and packagingequipment for storage are A, B, and C.Level A is that level of preservation that willprotect adequately against corrosion, deterioration, and physical damage during shipment,handling, indeterminate storage, and worldwideredistribution.Level B is the degree of preservation andpackaging that will protect adequately againstknown conditions less hazardous than A. LevelB should be based on firmly establishedknowledge of the shipment and storage conditionsand a determination that money will be saved.This level requires a higher degree of protectionThe size of an activity also governs the amountand depth of maintenance, repair, and overhaulservices. Here, volume is the determining factorthat reduces the maintenance cost to a levelcomparable to that of available commercialfacilities.1-6
than that afforded by Level C preservation andpackaging.is prevented or reduced to a minimum. Onlyunboxed automotive and construction equipmentis included in the active storage program.Level C is the level of preservation thatprotects adequately against corrosion, deterioration, and physical damage during shipment fromthe supply source to the first receiving activity forimmediate use.Upon reactivation, material preserved andpackaged for storage or shipment requiresdepreservation and servicing before use. Equipment is to be lubricated under the manufacturer’sinstructions. Seals and closures should beremoved. Housings, casings, and other enclosuresshould be drained of preservatives and refilledwith specified operating fluids before operation.Those components that were removed for storageshould be reinstalled.The proper level of preservation depends onthe availability of information on the probablehandling, shipping, storing units, and conditionsthat the vehicles and equipment will undergobefore final issue to the command. Physicalcharacteristics of the vehicles and equipment mustalso be considered.Upon activation, in equipment co
Construction Mechanic, Advanced NAVEDTRA 14050. DISTRIBUTION STATEMENT A: Approved for public release; distribution is unlimited. Although the words “he,” “him,” and “his” are used sparingly in this course to enhance communication, t