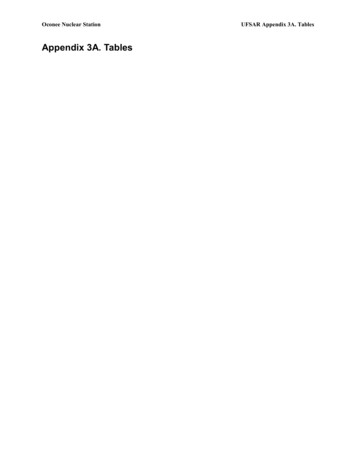
Transcription
Oconee Nuclear StationAppendix 3A. TablesUFSAR Appendix 3A. Tables
Oconee Nuclear StationUFSAR Table 3-1 (Page 1 of 1)Table 3-1. System Piping ClassificationPiping ClassDesign CriteriaDesigned ForSeismic LoadingAClass I, USAS B31.7(2)YesBClass II, USAS B31.7YesCClass III, USAS B31.7YesDUSAS B31.1.0Yes(1)EUSAS B31.1.0NoFUSAS B31.1.0YesGUSAS B31.1.0NoHGood Industry PracticeNoNote:1. Portions are considered a Class III system in accordance with FSAR Section 3.2.2.1.2. Class I RCS piping was re-analyzed to the 1983 ASME Code (No Addenda) during thereplacement steam generator analysis.(31 DEC 2004)
Oconee Nuclear StationUFSAR Table 3-2 (Page 1 of 6)Table 3-2. System Component ClassificationDesign CodeDesigned For SeismicLoading (D DynamicAnalysis) (S StaticAnalysis)Reactor VesselASME III, Class AYes – DReactor Vessel HeadASME III, Class I, 1989 Edition,No AddendaYes – DPressurizerASME III, Class AYes - DReactor Coolant Pump CasingASME III, Class A (not codestamped)Yes - DSteam GeneratorASME III, Class AYes - DHP Injection PumpSee Table 6-3Yes - Note 1Letdown CoolerASME III-C & VIIIYes - DSeal Return CoolerASME III-C & VIIIYes - Note 2Letdown Storage TankASME III-CYes - Note 2Purification DemineralizerASME III-CYes - Note 2Letdown FilterASME III-CYes - Note 2RC Pump Seal FilterUSAS B31.7, Paragraph 2-724,Class IIYes - Note 3Boric Acid Mix TankUSAS B96.1NoLithium Hydroxide Mix Tank-NoCaustic Mix Tank-NoTSP BasketsAISCYes -DBoric Acid Pump-NoLithium Hydroxide Pump-NoHydrazine Pump-NoCaustic Pump-NoPressurizer Sample CoolerASME III-C & VIIINoSteam Generator Sample CoolerASME VIIINoReactor Coolant SystemHigh Pressure Injection SystemChemical Addition and SamplingSystemComponent Cooling System(31 DEC 2014)
Oconee Nuclear StationUFSAR Table 3-2 (Page 2 of 6)Design CodeDesigned For SeismicLoading (D DynamicAnalysis) (S StaticAnalysis)Component Cooling Pump-Yes - Note 1Component CoolerASME VIIIYes - Note 2Component Cooling Surge TankAWWA D-100Yes - SCRD Cooling Coil FilterASME VIIIYes - SSpent Fuel CoolerASME III-C & VIIIYes - Note 2Spent Fuel Pump-Yes - Note 1Spent Fuel FilterASME III-CYes - SBorated Water Recirculation Pump-Yes - Note 1Spent Fuel DemineralizerASME III-CYes - Note 2Fuel Transfer TubeASME III-BYes - DIncore Instrument Handling TankAWWA D-100Yes - DLP Injection PumpSee Table 6-3Yes - Note 1LP Injection CoolerASME III-C & VIIIYes - Note 2Borated Water Storage TankAWWA D-100Yes - SCore Flooding TankASME III-CYes - DSee Table 6-3Yes - Note 1Penetration Room FilterSee Section 6.5.1Yes - SPenetration Room FanSee Section 6.5.1Yes - Note 4LP Service Water Pump-Yes - Note 1SSF Systems and ComponentsSee Section 9.6.4.5Note 9See Section 6.2.2Yes - DReactor Fuel Cooling SystemLow Pressure Injection SystemReactor Building Spray SystemReactor Building Spray PumpReactor Building PenetrationRoom Ventilation SystemLP Service Water SystemReactor Building Cooling SystemReactor Building CoolersRecirculated Cooling WaterSystem(31 DEC 2014)
Oconee Nuclear StationUFSAR Table 3-2 (Page 3 of 6)Design CodeDesigned For SeismicLoading (D DynamicAnalysis) (S StaticAnalysis)RCW Pump-NoRCW Heat Exchanger U1/U2ASME VIIIYes - Note 8RCW Heat Exchanger U3-NoRCW Surge TankASME VIII (not code stamped)NoQuench TankASME III-CYes - Note 2Quench Tank CoolerASME III-C & VIIIYes - Note 2Component Drain Pump-Yes - Note 1Coolant Bleed Holdup TankASME VIII (not code stamped)Yes - SBleed Transfer Pump-Yes - Note 1Deborating DemineralizerASME III-CYes - Note 2Concentrated Boric Acid StorageTankUSAS B96.1Yes - S-NoCoolant Bleed EvaporatorDemineralizerASME III-CYes - Note 2Coolant Bleed Evaporator Feed TankAWWA D-100Yes - SCoolant Bleed EvaporatorASME VIII (lethal)Yes - SRecirculating Pump-Yes - SConcentrate CoolerASME VIII (lethal)Yes - SSeparatorASME VIII (lethal)Yes - SVapor CondenserASME VIII (lethal)Yes - SDistillate Pump-Yes - SDistillate CoolerASME VIII (lethal)Yes - SCondensate Test TankUSAS B96.1Yes - SCondensate Test Tank Pump-Yes - Note 1Condensate DemineralizerASME III-CYes - SCoolant Bleed Evaporator FeedPump-Yes - SCoolant Storage SystemConcentrated Boric Acid StorageTank PumpCoolant Treatment System(31 DEC 2014)
Oconee Nuclear StationUFSAR Table 3-2 (Page 4 of 6)Design CodeDesigned For SeismicLoading (D DynamicAnalysis) (S StaticAnalysis)Condenser-Yes - SUpper Surge TankASME VIIIYes - SEmergency Feedwater Pump-Yes - Note 1Emergency Feedwater Pump Turbine-Yes - Note 1High Activity Waste TankNote 7Yes - Note 5High Activity Waste Tank Pump-NoLow Activity Waste TankNote 7Yes - Note 5Low Activity Waste Tank Pump-NoWaste Holdup TankAWWA D-100Yes - SWaste Holdup Transfer Pump-Yes - Note 1Spent Resin Storage TankAWWA D-100Yes - SSpent Resin Transfer Pump-Yes - Note 1Spent Resin Sluicing Pump-Yes - Note 1Waste Evaporator Feed TankAWWA D-100Yes - SWaste EvaporatorASME VIII (lethal)Yes – SASME VIII (lethal)ASME VIII (lethal)ASME VIII (lethal)ASME VIII (lethal)Yes – SYes – SYes – SYes – SYes – SYes - SReactor Building Sump Pump-Yes - Note 1Waste Evaporator Feed Pump-Yes - SSteam & Power ConversionSystem (Pertinent ComponentsOnly)Liquid Waste Disposal SystemRecirculating PumpConcentrate CoolerSeparatorVapor CondenserDistillate PumpDistillate CoolerGaseous Waste Disposal System(31 DEC 2014)
Oconee Nuclear StationUFSAR Table 3-2 (Page 5 of 6)Design CodeDesigned For SeismicLoading (D DynamicAnalysis) (S StaticAnalysis)Waste Gas Compressor-Yes - SWaste Gas SeparatorASME VIIIYes - SSeal Water Cooler-Yes - SWaste Gas TankASME VIII-CYes - SWaste Gas Filter-Yes - SWaste Gas Exhauster-NoIntake Structure-Yes - SCCW Pumps-Yes - SCCW Intake Pipe-Yes - SCCW Discharge Pipe-Yes - SECCW Piping (Structural Portion)-Yes - SCondenser-Yes - SESV Pumps-Yes - Note 6ESV TanksASME Secton VIIIYes - SCondenser Cooling Water SystemEssential Siphon Vacuum (ESV)System(31 DEC 2014)
Oconee Nuclear StationUFSAR Table 3-2 (Page 6 of 6)Design CodeDesigned For SeismicLoading (D DynamicAnalysis) (S StaticAnalysis)Notes:1. Vendor certification that component will meet seismic loading requirement.2. Static and Dynamic Analyses performed.3. Shock tested in lieu of analysis.4. Vendor certification that component will meet seismic loading requirement will be furnished.5. Tank meets loading requirement by its location in Auxiliary Building basement floor.6. Seismic Adequacy evaluated using experience based criteria and procedures.7. Stainless Steel Lining for Concrete Sump8. Dynamic analysis performed. Static and/or dynamic analyses can be performed for future changesthat affect the U 1/2 RCW Heat Exchanger. Seismic loads are applied to this U 1/2 Heat Exchangersince the attached CCW piping is Class D-seismic.9. The SSF systems and components needed for safe shutdown are designed to withstand the safeshutdown Earthquake. See Sections 9.6.4.1 and 9.6.4.310. A separate PSW structure is provided for major electrical equipment. The PSW structure isdesigned to withstand the Maximum Hypothetical Earthquake (MHE) and tornado missiles, windand differential pressure in accordance with Regulatory Guide 1.76 (Revision 1). Othercomponents that receive backup power from the PSW System retain their existing seismic andquality classifications. See Section 9.7.(31 DEC 2014)
Oconee Nuclear StationUFSAR Table 3-3 (Page 1 of 1)Table 3-3. Summary of Missile EquationsMissileCategoryPrincipleSymbolic Form of EquationIStored strainenergy equalskinetic energyσεv mV o 22Solution2Vo σ φ2Note: The above equation was revised in 2004 update.σ 2 v mV o 2E2IIWork done isConverted tokinetic energy2mVoFl 2 IIINewton's secondlawVo 2PA olmNote: The above equation was revised in 2004 update.PA o lF ma& X&& a VgEρ(1 FmA& ρ f A o Vf m V VV M f Aj()Note: The above equation was revised in 1999 update.VV) 1n (1 ) K1 VfVfΚ2r X tan βoNote: The above equation was revised in 1995 update.K 1 (1 KVoV) 1n (1 o ) 2VfVfroNote: The above equation was revised in 1999 update.K2 ρf A o A mmπ tan βNote:1. Either graphical techniques or numerical methods must be used to obtain the solution to category III.(31 DEC 2004)
Oconee Nuclear StationUFSAR Table 3-4 (Page 1 of 1)Table 3-4. List of Symbolsσ ultimate tensile stress, (lb/ft2)ρ density of missile, (#/ft3)ε strain σ/E, (in./in.)E modulus of elasticity, (lb/ft2)v volume of missile, (ft3)m mass of the missile, (lb-sec2/ft)V velocity of missile, (ft/sec)g gravity constant, (ft/sec2)F force on the missile, (lb)l stroke length, (ft)P system pressure, (lb/ft2)Ao missile area under pressure, throat area, (ft2)ρf density of fluid, (#/ft3)Vf jet velocity, (ft/sec)Am projected area of missile, (ft2)Aj jet area, (ft2)β angle of jet expansion, ( from normal)X distance missile travels, (ft)Vo initial velocity of missile, (ft/sec)ro radius of throat (ft)K2 constant(31 DEC 2000)
Oconee Nuclear StationUFSAR Table 3-5 (Page 1 of 1)Table 3-5. Properties of Missiles - Reactor Vessel & Control Rod DriveDescriptionWeight(lbs.)ImpactArea (in2)Velocity(ft/sec)KineticEnergy(Ft-lbs)1. Closure head nut [Note 1]80389711,6802. Closure stud w/nut [Note 1]660719796,4003. 1" Valve bonnet stud0.50.673.5424. C. R. nozzle flange bolt & nut3.03.197438II1. CRD closure cap8.07.02155,742III1. C. R. drive assembly100064.090125,777MissileClassIDeleted row(s) per 2004 updateNote:1.These values are from the NSSS and Bechtel vendor calculations. HydraNuts have beenestablished as acceptable alternate closure head nuts. Each HydraNut weighs approximately 108lbs. This increase in weight and associated parameters in the table due to the use of theHydraNuts remains bounded by those of the control rod drive described in Section 3.5.1.1.(31 DEC 2014)
Oconee Nuclear StationUFSAR Table 3-6 (Page 1 of 2)Table 3-6. Properties of Missiles - Steam GeneratorMissileClassImpactArea 51672. Feedwater inlet flange bolt0.3.667.5213. 16" I.D. manway stud, tube side8.02.167.55664. 5" Inspection opening cover stud1.51.273.51255. 1" Valve bonnet stud0.5.673.5421. 1½" Vent valve stem & wheel5.0.4544.51542. Sample line 1" valve stem &wheel4.0.335.8803. Sample line 1" EMO valve stemand wheel4.0.335.8801. 16" I.D. manway cover, tubeside9556155151,950,0002. 16" I.D. manway cover, shellside4786157772,230,0003. 5" I.D. inspection cover, tubeside80150515160,0004. 5" I.D. inspection cover, shellside40150852220,0005. 1½" Vent valve bonnet andassembly243837151,1806. Sample line 1" valve bonnet &assy.302724327,4607. Sample line 1" EMO bonnet l Steam GeneratorIIIIII1.1½" Vent valve bonnet stud(31 DEC 2003)
Oconee Nuclear StationMissileClassUFSAR Table 3-6 (Page 2 of 2)Weight(lbs.)DescriptionImpactArea ent Steam GeneratorIIIIII1.1½" Vent valve bonnet stud2.0.873.51672. Feedwater inlet flange bolt0.3.667.5213. 16" I.D. manway stud, tube side8.02.167.55664. 6” Handhole opening cover stud1.51.273.51255. 1" Valve bonnet stud0.5.673.5421. 1½" Vent valve stem & wheel5.0.4544.51542. Sample line 1" valve stem &wheel4.0.335.8803. Sample line 1" EMO valve stemand wheel4.0.335.8801. 16" I.D. manway cover, tubeside9556155151,950,0002. 16" I.D. manway cover, shellside4786157772,230,0003. 6” Handhole opening cover, tubeside80150515160,0004. 6” Handhole opening cover,shell side40150852220,0005. 1½" Vent valve bonnet andassembly243837151,1806. Sample line 1" valve bonnet &assy.302724327,4607. Sample line 1" EMO bonnet &assy.1152713834,250(31 DEC 2003)
Oconee Nuclear StationUFSAR Table 3-7 (Page 1 of 1)Table 3-7. Properties of Missiles - .)ImpactArea (in2)Velocity(ft/sec)KineticEnergy(Ft-lbs)1. 4" Valve bonnet stud3.01.873.52502. 5" Valve bonnet stud3.02.473.52503. 16" Manway cover stud7.53.167.55304. Heater bundle stud25.07.073.521005. 3/4" Valve stem stud0.8.4573.5671. Spray line 4" EMO valve stem91.0135.025602. Sample line 3/4" valve stem4.372.73303. Sample line 3/4" EMO valvestem4.372.73301. 16" I.D. manway cover250615375546,0002. Heater bundle assembly25008503755,400,0003. Spray line 4" EMO valve bonnetand assembly3251505211,370,0004. 2½" x 6 Relief valve bonnetand assembly17565232146,0005. Sample line 3/4" valve bonnetand assembly202136441,1506. Sample line 3/4" EMO valvebonnet and assembly11521258118,400(31 DEC 2000)
Oconee Nuclear StationUFSAR Table 3-8 (Page 1 of 1)Table 3-8. Properties of Missiles - Quench Tank and ctArea (in2)Velocity(ft/sec)KineticEnergy(Ft-lbs)QUENCH TANKSIIIIII1. 1½" Drain valve bonnet stud0.6.273.5502. 4" Valve bonnet stud2.0.373.51671. 1½" EMO drain valve stem5.0.4511.092. 4" EMO valve stem9.01.021.5651. 1½" EMO drain valve & op.assy.2202073.518,4502. 1½" Drain valve bonnet & assy.202073.51,6703. 4" EMO valve bonnet & op. assy.3556573.529,780INSTRUMENTSIII1. RTE1.0.22086702. RTE & Plug2.04.04486230(31 DEC 2000)
Oconee Nuclear StationUFSAR Table 3-9 (Page 1 of 2)Table 3-9. Properties of Missiles - System a (in2)Velocity(ft/sec)KineticEnergy(Ft-lbs)Core Flooding LineI14" C.V. bonnet stud2.01.773.5167I14" Valve bonnet stud3.54.067.5248II14" C.V. check pivot stud10.01.752499650II14" P.O. valve stem98.05.014331,100III14" C.V. bonnet & assembly525.01254481,640,000III14" P.O. valve bonnet and assembly1900.06505589,180,000L.P. Injection LineI12" C.V. bonnet stud2.01.773.5167II12" C.V. check pivot stud101.752499,650III12" C.V. bonnet and assy.450955582,170,000R.V. Outlet Line to L.P. SystemI10" Valve bonnet stud2.51.773.5177IRelief valve bonnet stud0.5.373.542IRelief valve stem assy.4012.535.3768II10" EMO valve stem503.113013,200III10" EMO valve bonnet & assy.12704155586,140,000R.V. Inlet Line from H.P. SystemI4" C.V. bonnet stud1.0.873.583.5II4" C.V. check pivot stud3.0.81581170III4" C.V. bonnet and assy.3019558145,000S.G. Outlet Line to Pump InletI1" Drain valve bonnet stud0.8.673.567II1" Drain valve stem assy.4.0.384438III1" Drain valve & bonnet assy.30.02744884,380Pressurizer to C.A. System LineI3/4" Valve bonnet stud1.0.4573.583II3/4" Valve stem4.373330II3/4" EMO valve stem4.373330III3/4" Valve bonnet and assy.202142556,250(31 DEC 2000)
Oconee Nuclear StationUFSAR Table 3-9 (Page 2 of 2)MissileClassDescriptionWeight(lbs.)ImpactArea (in2)Velocity(ft/sec)KineticEnergy(Ft-lbs)III3/4" EMO valve bonnet and assy.11521280140,000Primary Pump Seal Water Return to H.P. System LineI3" EMO valve bonnet stud1.01.073.583.5II3" EMO valve stem25.0.3125.76150III3" EMO valve bonnet and assy.285.0855071,137,000Letdown Cooler Inlet & Outlet LinesI1½" EMO valve bonnet stud2.0.873.5167II1½" EMO valve stem1.01.0153.21830III1½" EMO valve bonnet and assy.250.038320397,000Primary Pump Seal Water Inlet and Outlet LinesI3" Inlet C.V. bonnet stud1.0.873.583.5I3" Outlet valve bonnet stud2.01.073.5167II3" C.V. check pivot stud3.0.8158.41170II3" Outlet valve stem25.02.4125.76150III3" Inlet C.V. bonnet and assy.25.085558120,800III3" Outlet valve bonnet and assy.65.085523276,000Primary Pump Vent & Drain LinesI1½" Vent & drain valve bonnet stud2.0.873.5167II1½" Vent & drain valve stem5.01.0153.21830III1½" Vent & drain valve bonnet andassy.55.038435.0161,600(31 DEC 2000)
Oconee Nuclear StationUFSAR Table 3-10 (Page 1 of 1)Table 3-10. Missile CharacteristicsWeightImpact Area5944 lbsSide On - 8.368 sq ftEnd On - 3.657 sq ftVelocityKinetic Energy Ft-LbsInitial - 710 fpsImpactInitial - 46.5 x 106ImpactCylinder - 502 fpsDome - 431 fpsCylinder - 23.25 x 106Dome - 18.0 x 106(31 DEC 2000)
Oconee Nuclear StationUFSAR Table 3-11 (Page 1 of 1)Table 3-11. Depth of Penetration of ConcreteCase ICase IICase IIICylinderDomeCylinderDomeCylinderDome6"5½"12 3/4"12¼"35½"25"(31 DEC 2000)
Oconee Nuclear StationUFSAR Table 3-12 (Page 1 of 5)Table 3-12. Containment CoatingsSurface1. Carbon Steel0 F - 200 FDry Film ThicknessCoating SystemsManufacturerOriginal SystemRemarksNote 1Prime CoatCarbo Zinc 113.0 mils DFTCarbolineFinish CoatPhenoline 305 Finish4.0 mils DFTCarboline7.0 mils DFTNote 2Maintenance System2. Carbon Steel0 F - 200 Fover Original SystemDP-SP28 Power Tool CleaningMaintenance CoatDP#78-1 Carboline 8902.0 to 7.0 mils DFTCarbolineNew SystemDP-SP5 White Metal Blast Cleaning2.0 mils DFTCarbolinePrime CoatDP#12-1 Carbo Zinc 11 SG5.0 mils DFTCarbolineFinish CoatDP#78-1 Carboline 8907.0 mils DFTOriginal SystemNote 2Note 1Prime CoatCarboline 191 Primer2.0 mils DFTCarbolineFinish CoatPhenoline 305 Finish5.0 mils DFTCarboline7.0 mils DFTMaintenance SystemNote 2over Original SystemDP-SP28 Power Tool CleaningMaintenance CoatDP#78-1 Carboline 890New SystemDP-SP5 White Metal Blast CleaningPrime CoatDP#78-1 Carboline 8902.0 mils DFTCarbolineFinish CoatDP#78-1 Carboline 8905.0 mils DFTCarboline2.0 to 7.0 mils DFTCarbolineNote 27.0 mils DFT(31 DEC 2000)
Oconee Nuclear StationUFSAR Table 3-12 (Page 2 of 5)SurfaceCoating Systems3. Carbon Steel0 F - 750 FOriginal SystemPrime CoatNew systemPrime Coat4. Carbon Steel0 F-250 FTank LiningDry Film ThicknessManufacturerRemarksNote 1Carbo Zinc 11DP-SP5 White Metal Blast CleaningDP#12-1 Carbo Zinc 11 SG3.0 mils DFTCarbolineNote 23.0-5.0 mils DFTCarbolineNew SystemDP-SP5 White Metal Blast CleaningPrime CoatDP#71-1 7155HHB Plasite Phenolic4.0 mils DFTWisconsinIntermediate CoatDP#71-1 7155HHB Plasite Phenolic4.0 mils DFTWisconsinFinish CoatDP#71-1 7155HHB Plasite Phenolic4.0 mils DFTWisconsinNote 212.0 mils DFT5. ConcreteFloorsNote 1Original SystemPrime Coat195Epoxy Surfacer8.0 mils DFTCarbolineFinish CoatPhenoline 305 Finish4.0-8.0 mils DFTCarboline12.0-16.0 mils DFTMaintenance SystemNote 2over Original SystemDP-SP25Maintenance CoatDP#78-1 Carboline 890CarbolineNew SystemNote 2Prime CoatDP-SP25Finish CoatDP#36-1 Starglaze 2011SSeal ConcreteCarbolineDP#78-1 Carboline 8908.0 mils DFTCarboline8.0 mils DFT(31 DEC 2000)
Oconee Nuclear StationSurfaceUFSAR Table 3-12 (Page 3 of 5)Dry Film ThicknessCoating Systems6. ConcreteWallsManufacturerOriginal SystemDP-SP17Prime CoatDP#36-1 46-X-29-00 Epoxy Surfacer8.0 mils DFTCarbolineFinish CoatDP#69-1 76 Series-00 High Build Epoxy4.0-8.0 mils DFTCarbolineRemarksNote 112.0-16.0 mils DFTMaintenance SystemNote 2over Original SystemDP-SP17Maintenance CoatDP#78-1 Carboline 890New SystemDP-SP17Seal ConcreteCarbolinePrime CoatDP#36-1 Starglaze 2011S5.0 mils DFTCarbolineFinish CoatDP#78-1 Carboline 8908.0 mils DFT2.0 to 5.0 mils DFTCarbolineNote 2Notes:“HISTORICAL INFORMATION NOT REQUIRED TO BE REVISED”1. Original coating systems have satisfactorily withstood the following autoclave tests designed to simulate LOCA conditions with no loss ofadherence or erosion of material from surface:Carbon Steela.Test specimens: Coating system applied to sandblasted carbon steel coupons.b.Water chemistry: 3000 ppm boron as boric acid in water; also 3% boric acid(31 DEC 2000)
Oconee Nuclear StationSurfacec.Coating SystemsUFSAR Table 3-12 (Page 4 of 5)Dry Film ThicknessManufacturerRemarksTemperature:For 3000 ppm boron3 hours at 285 F-290 F2 days at 200 F6 days at 150 F4 days at 130 FFor 3% Boric Acid3 hours at 75 F-300 F3 hours at 300 F3 hours at 300 F-180 F15 hours cooling to ambientTotal 24 hour cycle repeated ten timesConcretea.Test specimens: Prepared concrete coupons.b.Water Chemistry: 3000 ppm boron as boric acid in water; also 3% boric acid .c.Temperature:2 hours at 75 F - 300 F14 hours at 300 F2 hours at 75 F4 hours cooling to ambient We understand testing performed by ANS Subcommittee for Protective Coatings for Reactor Containment Facilities and by Dr. C D Watsonat Oak Ridge did not disclose any significant difference between results of static autoclave exposure and autoclave exposure using a sprayof solution on panels. On this basis either static or dynamic exposure to spray solution is considered to be acceptable as basis for testing. We do not have available test results on jet impingement effects; however, it is felt that there is no coating system available which would(31 DEC 2000)
Oconee Nuclear StationUFSAR Table 3-12 (Page 5 of 5)withstand a high temperature, high velocity steam jet. We believe that the assumption of large scale, rapid LOCA by means of a doubleended pipe failure or otherwise, negates the possibility of concentrated local jet impinging on a coated steel area of substantial size.Therefore, we believe the autoclave tests in which specimens were subjected to steam and water at elevated temperatures more nearlyapproximate overall building environment under LOCA conditions than would a local steam jet application. We understand ANS subcommittee found no system for coating steel or concrete for resisting steam jet impingement and therefore hasestablished no standards for this condition of exposure . Decontamination factor for Phenoline 305 is 325. Test methods described in Oak Ridge National Laboratory Reports ORNL-3589, 3916and others. Carbo Zinc 11 withstands in excess of 3 x 109 Roentgens when irradiated in water. There is no serious damage to Phenoline 305 at 6 x 109Roentgens when irradiated in air. Phenoline 305 withstands in excess of 2 x 109 Roentgens irradiated in water .2. Maintenance coating over Original Coating Systems and New Coating Systems have satisfactorily withstood radiation and autoclave tests withno loss of adherence or erosion of material from surface. Coating Systems are qualified by Engineering in accordance with ANSI N101.2 and ANSI N101.4 for (A) LOCA Conditions and (B)Radiation Tolerance. Coating specifications for shop and field application include the following: Scope, Coating System, Approved Materials, ApplicationProcedures, Touchup Procedures, Workmanship Guide, Inspection Requirements, Record Requirements, and Product Data Sheets. A Materials Certification of each batch of coating material procured is in accordance with ANSI N101.4 and is provided by theManufacturer. Distribution of Containment Coating Specifications and Coating Schedules are transmitted by Document Control.(31 DEC 2000)
Oconee Nuclear StationUFSAR Table 3-13 (Page 1 of 1)Table 3-13. Service Load Combinations for Reactor Building1. D F L To2. D F L P TA E(or W)3. D F L P'Where:D Dead LoadL Appropriate Live LoadF Appropriate Prestressing LoadP Pressure Load (Varies with time from design pressure to zero pressure)To Thermal Loads Due to Operating TemperatureTA Thermal Loads Based on a Temperature Corresponding to a Pressure PE Design EarthquakeP' Test Pressure 1.15 PW Wind Load(31 DEC 2000)
Oconee Nuclear StationUFSAR Table 3-14 (Page 1 of 2)Table 3-14. Accident, Wind, and Seismic Load Combinations and Factors for Class 1 ConcreteStructuresY 1/ 1.0D 1.0P 1.0T E')Y 1/ (1.05D 1.25P 1.0T 1.25E or W)Y 1/ (1.05D 1.5P 1.0T)Y 1/ 1.0D 1.0Wt 1.0Pi) for Tornado Forces.(Use 0.95 where dead load subtracts from critical stress.) (Wind, W, to replace earthquake, E, in theabove formula where wind stresses control)WhereY required yield strength of the structure as defined above.D dead loads of structure and equipment plus any other permanent loadingscontributing stress, such as hydrostatic or soils. In addition, a portion of "live load"should be added when it includes piping, cable trays, etc. suspended from floors andan allowance should be made for future additional permanent loads.P design accident pressure.T thermal loads based on a temperature corresponding to the factored design accidentpressure.E seismic load based on design earthquake.E' seismic load based on maximum hypothetical earthquake.W wind load.Wt stress induced by tornado wind velocity (drag, lift and torsion).Pi stress due to differential pressure. Concrete capacity reduction factor. 0.90 for concrete flexure. 0.85 for tension, shear, bond and anchorage in concrete. 0.75 for spirally reinforced concrete compression members. 0.70 for tied compression members. 0.90 for fabricated structural steel embedments. 0.90 for mild reinforcing steel (not prestressed) in direct tension excludingsplices. 0.85 for mild reinforcing steel with mechanical splices (for lap splices, 0.85as above for bond and anchorage). 0.95 for prestressed tendons in direct tension.(31 DEC 2000)
Oconee Nuclear StationUFSAR Table 3-14 (Page 2 of 2)Additional Notes:The Class 1 structures are proportioned to maintain elastic behavior when subjected to variouscombinations of dead loads, accident loads, thermal loads and wind or seismic loads. The upper limitof elastic behavior is considered to be the yield strength of the effective load-carrying structuralmaterials.The yield strength for steel (including reinforcing steel) is considered to be the minimum given in theappropriate ASTM specification. Concrete structures are designed for ductile behavior whereverpossible; that is, with steel stress controlling the design. The values for concrete, as given in theultimate strength design portion of the ACI 318-63 Code, will be used in determining "Y", the requiredyield strength of the structure.The design loads applied to the structures are increased by load factors based on the probability andconservatism of the predicted normal design loads.(31 DEC 2000)
Oconee Nuclear StationUFSAR Table 3-15 (Page 1 of 1)Table 3-15. Inward Displacement of Liner PlateCaseNominal PlateThickness(In.)Initial InwardDisplacement(In.)AnchorSpacing L1(In.)AnchorSpacing L2(In.)Factor 250.2530154.25(31 DEC 2000)
Oconee Nuclear StationUFSAR Table 3-16 (Page 1 of 1)Table 3-16. Stress Analysis Results(31 DEC 2003)
Oconee Nuclear StationUFSAR Table 3-17 (Page 1 of 1)Table 3-17. Stress Analysis Results(31 DEC 2000)
Oconee Nuclear StationUFSAR Table 3-18 (Page 1 of 1)Table 3-18. Stress Analysis Results(31 DEC 2003)
Oconee Nuclear StationUFSAR Table 3-19 (Page 1 of 1)Table 3-19. Stress Analysis Results(31 DEC 2003)
Oconee Nuclear StationUFSAR Table 3-20 (Page 1 of 1)Table 3-20. Stress Analysis Results(31 DEC 2003)
Oconee Nuclear StationUFSAR Table 3-21 (Page 1 of 1)Table 3-21. Stress Analysis Results(31 DEC 2003)
Oconee Nuclear StationUFSAR Table 3-22 (Page 1 of 1)Table 3-22. Bent Wire Test ResultsSTRESS(psi)SampleGroup No.123456Bend Angle(Degrees)-3060903060Bend Radius 50228,100SERIES I Heat#A67386AverageSERIES II Heat#A72005Average(31 DEC 2000)
Oconee Nuclear StationUFSAR Table 3-23 (Page 1 of 1)Table 3-23. Auxiliary Building Loads and ConditionsAREACONDITIONSControl RoomA,B,C,D,ECable RoomA,B,C,D,EElectrical EquipmentRoomA,B,C,D,ESpent Fuel PoolA,B,C,D,EBlow out panels designed to relieve 3 psi differentialpressureSpent Fuel Storage RacksA,DInherently resistant to wind loadsSpent Fuel HandlingCraneA,D,EInherently resistant to wind loads. Hold down deviceprovidedPenetration Room FramesA,B,DPhysical separation provided for missile protectionCable ShaftA,B,C,D,EElevator Steel ShaftA,DMain Steam PipeSupportsA,B,DHot Machine ShopA,DBalance of AuxiliaryBuildingA,B,DFrame designed for B, but not external walls abovegrade. Areas below grade are inherently protectedagainst missiles in C and E.A All normal dead, equipment, live, and wind loads due to 95 mph wind or design basisearthquake.B Normal dead and equipment loads plus tornado wind load due to 300 mph wind.C Tornado missiles of (1) 8 in. diameter x 12 ft. long piece of wood, 200 pounds, 250 mph, and(2) 2,000 pound automobile, 100 mph, 20 sq. ft. impact area, for 25 ft. above grade.D Normal dead and equipment loads plus maximum hypothetical earthquake loads.ETurbine-generator missile, 5,944 pounds, 502 fps, kinetic energy of 23.25 x 106 ft.-lbs., sideon impact area of 8.368 sq. ft. and end on impact area of 3.657 sq. ft. Deleted row(s) Per 2009 Update(31 DEC 2009)
Oconee Nuclear StationUFSAR Table 3-24 (Page 1 of 1)Table 3-24. Mark-BZ Fuel Assembly Seismic and Loca Results at 600 FLoading CaseAllowable ImpactLoad (lbs)Grid DeformationAllowable GridDeformation (in.)SSE2824 (1)None0.0LOCA Core Flood LineGuillotine2824None0.0LOCA Decay HeatLine Guillotine2824None0.0SSE and LOCA2824None0.0Note:1. That the allowable load is actually higher than the elastic load limit given, since the criteria of SSEis to ensure control rod insertion. Therefore, the value given is conservative.(31 DEC 2000)
Oconee Nuclear StationUFSAR Table 3-25 (Page 1 of 1)Table 3-25. Deleted per 1996 Update(31 DEC 2000)
Oconee Nuclear StationUFSAR Table 3-26 (Page 1 of 1)Table 3-26. Stress Limits for Seismic, Pipe Rupture and Combined LoadsCaseLoading CombinationStress LimitsIDesign loads operating basis earthquakeloadsPm 1.0Sm(PL Pb ) 1.5SmIIDesign loads safe shutdown earthquakeloadsPm 1.2Sm(PL Pb ) 1.2(1.5Sm )IIIDesign Loads pipe rupture loadsPm 1.2Sm(PL Pb ) 1.2(1.5Sm )IVDesign loads safe shutdown earthquakeloads pipe rupture loadsPm 2 / 3Su(PL Pb ) 2 / 3Su1wherePL Primary local membrane stress intensityPm Primary general membrane stress intensityPb Primary bending stress intensitySm Allowable membrane stress intensitySu Ultimate stress for unirradiated material at operating temperatureNote:1. All sy
Tables Appendix 3A. Tables . Oconee Nuclear Station UFSAR Table 3-1 (Page 1 of 1) (31 DEC 2004) Table 3-1. System Piping Classification . Steam Generator ASME III, Class A ASME III, Class I, 1989 Edition, No Addenda ASME III, Class A ASME III, Class A (not code st