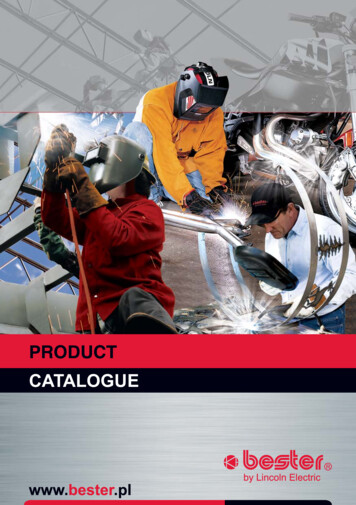
Transcription
PRODUCTCATALOGUE
Why Bester?Bester branded welding machines are probably the most recognized brandin Poland. Decades of unfading popularity among welding specialists justprove their reliability. Whether for occasional, light works or professionalheavy duty welding, Bester can always meet your expectations.Lincoln Electric Bester:Bester welding machines are manufactured at Lincoln Electric Bester S.A.,located in Bielawa, Poland.All products are designed with precision by experienced team of engineersand with the application of the latest worldwide technologies. CNC machining centres, vacuum impregnation of transformers, electronics assembly,assembly lines and full range of auxiliary equipment help to meet toughestquality standards.Lincoln Electric Bester S.A. company is part of Lincoln Electric Corporation.Lincoln Electric:Lincoln Electric Co. was founded in 1895 and nowadays is the world leader indesign, development and manufacturing of arc welding equipment, weldingrobotic systems as well as plasma and gas cutting equipment. Headquartered in Cleveland, USA, it has manufacturing plants, group companies anddivisions in 21 countries as well as global distribution and sales network.There are currently four manufacturing plants in Poland: Welding equipment in Poland, Welding consumables in Spawmet, Świętochłowice, Fluxed- cored wires in Dzierżoniów, Gus cutting apparatus in Harris Calorific in Dzierżoniów.
ExpertiseAll products are designed by welding professionals – experienced engineersusing the most advanced tools and latest technologies.ExperienceWe have been manufacturing top quality welding machines and consumablesfor over 60 years.ReliabilityLincoln Electric Bester S.A. can boast the most advanced in the weldingbranch laboratory for testing machines, with the best measuring apparatus.All Bester branded machines are covered with 2 years full warranty withoutany surprises.Customer ServiceWe provide developed distribution network and 60 servicing points allover Poland.The company objective is to guarantee that all defects are removed in 48 hours.Total SolutionsWe supply not only welding machines but also welding consumables, fumesextraction systems, accessories and welding technologies.Quality & PriceWe guarantee incredibly attractive quality to price rate.
Table of contentsProcess welding guidesStick electrode welding MMA .Gas shielded MIG/MAG welding .Plasma cutting .Useful information .6789Equipment for stick welding (MMA)Besterka 1400 1800 2200 .Bester 151 181 210 .STB 225 STB 250 .SPF 420–D SPF 670–D .10111213Equipment for MIG/MAG weldingMinimagster 1501 1501S Midimagster 1613 1801 .Magster 190 220 .Magster 280 330 (4x4) .Magster 380 450 / PDE 50 51 .14151617Plasma cuttingBest Cut 2000C . 18Battery chargersHector 1208 1210 1214 . 19Sprintercar 1225 plus 2425 . 20Herkules 150 300 501 . 21
Process welding guideStick electrode welding (MMA)Welding directionCoatingArcWeld poolParent materialElectrode coreShielding atmosphereMolten slagSolidified slagSolidified weld metalIn this welding process, an electric arc is created between a coated consumable electrodeand the work piece to be welded, causing the parent material to be fused together andthe electrode to melt. The electrode is of similar material as the parent material, and bymelting provides the weld (or joint) with a reinforcing filler material. The electrode may becoated with basic, rutile or cellulose material, and as the coating burns it protects the arcand weld pool from the atmosphere with a gaseous shroud, the slag which solidifies overthe newly deposited weld also protects it from the atmosphere.Process welding guides6The power source gives constant current at the output (CC) and depending on appliedstick electrode, can supply AC or DC current. Usually the best quality welds you can receive using DC characteristic.The output current level depends on stick electrode diameter, dimensions and thicknessof welded material. Also very important is welding position. Generally speaking – smallerdimensions of welded material equals smaller diameter of the stick electrode and outputcurrent.
Process welding guideMIG/MAG Process (Gas shielded MIG/MAG welding)GunNozzleShielding gasArcWeld poolSolidifield weld metalContact tipWelding directionSolid wire or Flux-cored wireShielding atmosphereParent materialThe MIG/MAG welding process (or GMAW – Gas Metal Arc Welding) is when an electricArc is created between a continuous consumable wire and the work piece to be welded,protected within a gas atmosphere. This atmosphere can be either inert (Argon) or active(CO2 or mixture of Argon and CO2).The wire is continuously fed through a gun to the weld pool by a wire feeder. Either SolidWire (GMAW) or Cored Wire (FCAW-GS – flux-cored arc welding, gas shielding) can beused.MIG/MAG Process (Self shielded Flux-Cored welding)GunGun tube insulator / thread protectionArcWeld poolContact tipShielding atmosphereFlux-cored wireMolten slagParent materialSolidifield slagSolidifield weld metalInnershield welding is an Arc welding process in which welding heat is created from an arcbetween a continuous flux cored wire and the work piece. The flux provides gas shieldingfor the arc and a slag covering of the weld deposit.MIG/MAG welding is recommended for welding all metals, including stainless steeland aluminium alloys. It is also faster process than stick electrode welding (MMA)Process welding guidesWelding direction7
Process welding guidePlasma cuttingPlasma cutting is a process which uses an electric arc and air. When the air is flowingthrough the electric arc started between two electrodes it becomes ionised and thanks toa large density of power the plasma arc appears. A nozzle mounted in the torch focusesthe arc.High temperature inside the plasma arc and very high speed of the plasma stream blowsout the molten material from the gap.For plasma cutting we are using DC (-) supplied from an inverter based power sources.Using plasma cutting you can cut all construction materials that are conductive.Thank to high temperature of the plasma stream it is possible to start cutting immediately,without pre-heating.Basic parameters of plasma cutting: Cutting current (A), Cutting voltage (V), Cutting speed (m/min), Air pressure (MPa), Adjustment of the cutting electrode by the operator, Diameter of cutting nozzle (mm), Position of the torch.Process welding guides8Using hand cutting the operator should only adjust the cutting speed and distancebetween the electrode and base material. The rest of parameters are constant on thelevel which was previously set by operator.Depending on the base material you may have to use different plasma gases e.g. Oxygen,air, nitrogen, argon and mixes of argon/hydrogen or nitrogen/argon.Plasma cutting is a fast and clean process. As a result you achieve clean and smoothedges. It is also a less expensive and a comfortable way of cutting as compressed air ischeaper than other gases. In other words it is very easy and user friendly – the operatordoes not have to be very skilled or experienced.
Process welding guideUseful informationWelding transformerIt is used to supply an electric arc which allows the parent material to melt and fuse together,a filler material of similar chemical composition as the parent material can be used to fill theweld joint. The power source is a transformer supplied with 230 V or 400 V input voltage. As anoutput it gives the current with low voltage but high amperage. To get the arc you have to connect the ground cable to the work piece and place a welding electrode in the electrode holderand scratch the electrode. Generally transformers are the power sources for MMA welding andMIG/MAG where you use the continuous welding wire instead as a consumable electrode.The inverterThe inverter can be supplied with 230 V or 400 V input voltage. The difference comparedto the transformer is that inverter changes the frequency of input voltage. Increasingthe frequency (much more than 50 Hz from the network) it is also possible to get veryhigh current from small transformers and the advantage of inverter are small weight anddimensions. It is mainly used for stick electrode welding (MMA) and TIG welding.Welding consumablesWelding consumables are the filler materials which have the same or very similar composition to the base material. The base material and the consumable are melted with theelectric arc and after solidifying giving the appearance of the weld. Welding consumablesare mainly stick electrodes, welding wire and TIG wire.The table of stick electrode diameter and current is depending on thickness of base materialDiameter of the electrode (mm)Current (A)0,8 – 1,41,635 – 521–2252 – 752–32,575 – 1003–43,2100 – 1324 – 104132 – 175Duty cycleThe duty cycle of a welding machine is the percentage of time in a 10 minute cycle atwhich the welder can operate the machine at rated welding current. Excessive extensionof the duty cycle will cause the thermal protection circuit to activate.Shielding gasesCO2Mix of 75% Argon i 25% CO2100% Argonmainly for steelfor majority of carbon steelsfor aluminium alloysProcess welding guidesBase material thickness (mm)9
Besterka1400 1800 2200The Besterka series are three conventional welding transformers dedicated for MMAwelding. Small dimensions and relatively low weight allow to use these machines in allconditions. As a standard all models are equipped with the cooler which increases theefficiency of work (better duty cycle). Besterka you can easily use at home, farm but alsoin garage or small repair shops.Every unit is equipped with welding cables and input cable with plug.Advantage:Equipment for stick welding (MMA)10 Recommended welding consumables:efficient regulation of welding current;cooling;portable, light;thermal protection;meets EN 60974-6; -10 and CE.Omnia 46, Pantafix, Supra.Super 46, Perfect, Univers.ProductnameProductnumberInputvoltageRange ofstick FuseMax. weldingcurrentWeightBesterka1400B18233–1230 V50 Hz1,4 – 3,22,5 mm3,2 mm150 / 560 s110 / 650 s20120 A / 22,8 V17,5Besterka1800B18234–1230 V50 Hz1,4 – 42,5 mm3,2 mm4,0 mm270 / 730 s125 / 700 s80 / 730 s25150 A / 24 V19,5Besterka2200B18235–1230 / 400 V50 Hz1,4 – 42,5 mm205 / 580 s300 / 560 s105 / 660 s105 / 565 s75 / 730 s62 / 665 s16,25145 A / 23,8 V160 A / 22,4 V203,2 mm4,0 mm(kg)
Bester151 181 210Bester 151, 181 and 210 are brand new inverter based welding units in the Bester brand.It can be used for MMA welding with DC current. These units have small dimensions, arelight and thank to continuous control of welding current and are user friendly and simpleto use. With Bester inverters you can weld with max. 3,2 mm (Bester 151) and 4,0 mmfor Bester 181 or 210.All units as an option can weld with the TIG method. After connecting a special TIG torchwith gas valve the units are immediately ready to work. To start the arc you just have toscratch the tungsten electrode (Bester 151) or simply touch and lift (Bester 181 or 210)and the arc starts automatically.Every unit is equipped with welding cables and input cable with plug. All are also availablein a case.ProductnameProductnumberBester 151K12033–9Bester 181K12034–9Bester 210K12035–9Recommended welding consumables:InputvoltageRated outputcurrent / Duty cycle230 V140 A / 30%Omnia 46, Pantafix, Supra.Super 46, Perfect, Univers.FuseCurrentrange10 – 1204,61610 – 1406,710 – 1607120 A / 25%160 A / 35%Weight(kg)Equipment for stick welding (MMA)Advantage: thermal protection; possibility to weld with TIG; amperage meter (only Bester 210); built in „Anti Stick”; Hot Start and Arc Force (Bester 181and 210); generator compatibility (Bester 181and 210); meets EN 60974-6; -10 and CE.11
STB225 250Welding transformers STB are reliable and very popular power sources dedicated forstick electrode welding with AC current.Every unit is equipped with welding cables and input cable with plug.Advantage: reliability; easy to use; welding with max. 5 mm stick electrode; continuous control of welding current; possibility to cut with the electrode; thermal protection; meets EN60974 and CE.Equipment for stick welding B-250B18054–2Input voltageCurrent range400 V, 50 Hz40 – 225Recommended welding consumables:Omnia 46, Pantafix, Supra.Super 46, Perfect, Univers.OCV voltageInput current (A) /Input power (kVA)Weight(kg)62 – 6741 (20%) / 16 (20%)50,561 – 6744,5 (35%) / 18 (35%)52,5
SPF420–D 670–DSPF units are rugged and reliable, conventional welding rectifiers designed to work inhard environment conditions. Units are easy to move thank to big wheels, useful pull barsand lifting hooks. It is also possible to weld with all stick electrodes – rutile, basic andcellulosic.The unit is equipped with 5 m long input cable.ProductnameSPF 420-DProductnumberInput voltageB18326–1Recommended welding consumables:Rated outputcurrent / Duty cycleOmnia 46, Pantafix, Supra.Super 46, Perfect, Univers.FuseCurrentrangeWeight(kg)400 A / 35%315 A / 60%240 A / 100%63 / 405 – 400126670 A / 35%500 A / 60%400 A / 100%100 / 6315 – 670150230 / 400 V – 3 f.SPF 670-DB18328–1Equipment for stick welding (MMA)Advantage: excellent arc characteristics; Hot Start supporting excellent arc starting; Arc Force protecting electrode sticking; fan on demand (F.A.N. ) built-in reducespower and the intake of dust and fumes; ready to be moved, equipped withwheels, pull bar and two lifting hooks; digital meters showing welding Amperage; arc gouging capability; meets IEC974-1 and CE standards;13
Minimagster 1501 1501SMidimagster 1613 1801Mini and Midimagster are semiautomatic welders designed to be user friendly and easy touse. Units allow welding with 0,6–0,8 mm wires. Depending on the needs of the customer,these units are available in 230 V or 400 V input voltage version. Every model is equippedwith welding gun.Minimagster 1501 and 1501S can be used for welding without shielding gas – after applying self-shielding welding wire Innershield NR211-MPMini and Midimagster is excellent for hobby works but also for all repair shops, car bodyworks etc.Equipment for MIG/MAG welding14Advantage: different input voltages – 230 V or 400 V; professional 2–roll drive; possibility to weld without shielding gas(only Minimagster 1501 and 1501S); equipped with welding gun; meets IEC974-1, RoHS and CE.ProductnameRecommended welding consumables:Ultramag,Innershield NR211-MP.DSM SG2.ProductnumberInputvoltageRated outputcurrent / Duty SB18214–1B18214–2230 V230 / 400 V115 A / 20%1640 – 115 A3235Midimagster1613B18220–1400 V140 A / 15%1640 – 140 A48Midimagster1801B18219–1230 / 400 V160 A / 10%1640 – 160 A50
Magster190 220Magster 190 and 220 are the continuation of recognizable units on the market, thesesemiautomatic welding machines are rugged, reliable and functional. Units are recommended for welding with solid wire with diameters 0,6–1,0 mm which can be fed withprofessional 2–roll drive.Magsters are also equipped with all useful functions like spot welding, 2/4 stroke andburnback. As a standard all units are equipped with 3 m long welding gun and gas heaterconnection socket.Paneldescription:ProductnameMagster 190ProductnumberRecommended welding consumables:Ultramag, Supramig.DSM SG2.1.2.3.4.5.6.7.Input voltageB18215–1Euro connector,Thermal protection light,Main switch,Wire feed speed,Spot welding,Burnback,Welding voltage.Rated outputcurrent / Duty cycleCurrentrangeWeight(kg)175 A / 35%25 – 180 A70200 A / 35%40 – 215 A72400 VMagster 220B18216–1Equipment for MIG/MAG weldingAdvantage: professional wire drive system; CO2 heater socket; functions: 2/4 stroke, spot welding, burnback; equipped with 3 m welding gun; easy to understand graphic controlpanel; meets IEC974-1, ROHS and CE15
Magster280 330 (4x4)These semiautomatic welders the Magster 280 and 330 are fully industrial machinesfor welding small to medium industries. Clear and easy to understand front panel isuseful when you have to set precisely the welding parameters and obtain excellent arccharacteristics. As standard all units are equipped with all helpful functions like spot welding, 2/4 stroke and burnback. Additionally units marked with 4x4 symbols are equippedwith A/V meters and 4–roll wire drive system for precise wire feeding which is necessarywhen you weld aluminium alloys. As standard all units are equipped with 3 m long weldinggun and gas heater connection socket.Equipment for MIG/MAG welding16Advantage: professional wire drive system, also 4-roll; CO2 heater socket; functions: 2/4 stroke, spot welding,burnback; additionally for 4x4 version – A/V metersand 4–roll wire drive system; easy to understand graphic control panel; meets IEC974-1, ROHS and CE.Ultramag, Ultramag SG3,Supramig, Supramig Ultra,Outershield MC700,LNM 304 LSi, LNM 316 LSi,LNM AlMg5, LNM AlSi5.DSM SG2, DSM SG3,DSM 308 LSi, DSM Recommended welding consumables:ProductnumberMagster 280B18217–1Magster 280 4X4B18228–1Magster 330B18218–1InputvoltageEuro connector,Voltage meter (V),Current meter (A),Thermal protection light,Main switch,Wire feed speed,Spot welding,Burnback,Welding voltage.Rated outputcurrent / Duty cycleCurrentrange250 A / 35%35 – 270 A300 A / 35%35 – 320 A400 VMagster 330 4X4B18229–1Weight(kg)80
Magster380 450 / PDE 50 51Magster 380 and Magster 450 are fully professional welding power sources.Depending on the users needs they can work with the PDE50 or PDE 51 separate semiautomatic wire feed unit. The PDE50 has built in helpful functions like: burnback, 2/4stroke, cold feed and gas purge. The PDE51 has more advanced features like: run-in function, A/V meter, bigger – 40 mm drive rolls and the possibility to work with water cooledwelding guns.As standard all power sources are equipped with 3 m long welding gun and CO2 heatersocket.Recommended welding consumables:Ultramag, Ultramag SG3,Supramig, Supramig Ultra,Outershield MC700, LNM 304 LSi,LNM 316 LSi, LNM AlMg5,LNM AlSi5, Outershield 71C,Outershield 71 EH.PODAJNIKIŹRÓDŁA PRĄDUDSM SG2, DSM SG3, DSM 308 LSi,DSM 316, DSP 71.ProductnameProductnumberInput voltageRated outputcurrent / Duty cycleCurrentrangeWeight(kg)Magster 380B18223–1400 V360 A / 40 %40 – 360 A129Magster 450B18224–1400 V420 A / 40 %40 – 420 AMagster 450 W154B18225–1162ProductnameProductnumberNumber of driverolls / diameter of rollWire feedspeed rangeDigitalV/AWeight(kg)PDE 50B18226–14 / 30 mm1 – 20 m / minOption15,5PDE 51B18227–14 / 40 mm1 – 20 m / minYes16Equipment for MIG/MAG weldingAdvantage: A/V meters (for PDE50 as an option); functions: 2/4 stroke, burnback; low suspended the place for gas bottle; run-in (only PDE51); meets IEC974-1, RoHS and CE.17
Best Cut2000CBestCut 200C is an energy efficient plasma cutter which is the most universal onthe market. Thanks to modern inverter technology it is also small, portable and compact(18 kg).Just after plug-in to normal 230 V network with 16 A safety fuse the machine is ready tobe used. It cuts fast, precisely and there is no need to grind after.The cutter has built in air compressor which allows using it immediately after supplyinginput voltage.A special design with two air filters and moisture filter to ensure a dry oil free supply ofclean air coming from the internal compressor.The unit is equipped with input cable with plug (2,5 m), ground cable (2,1 m) and handplasma torch (LC-25 – 3 m)Advantage: continuous control of cutting current; possibility to cut steel (up to 12 mm) but also aluminium and stainless steel; built-in air compressor; thermal protection; meets EN60974, EN50199 and CE.Plasma cutting18ProductnameBest Cut 2000CProductnumberInputvoltageFuseK12037–9230 V 1f, 50 Hz16 A (slow)Cuttingcapacitydo 8 mm *do 12 mm *** steelCutting sppedDimensions(mm)Weight(kg)1,0 m / min ***385 x 215 x 48018** steel sheets cutting*** for 4 mm carbon steel
Hector1208 1210 1214Hector series are the battery chargers designed for car batteries up to 160 Ah used inmotor cars and delivery cars. Units are light and portable and the housing is designed withhandle and place for cables.Advantage: charging with decreasing current („W” characteristic); safety fuse (switches off when short circuit or wrong connection to battery poles); charging current meter; safety class II.ProductnumberHector 1208B18085–1Hector 1210B18087–1Hector 1214B18089–1– capacity recommendedInputvoltage230 V50 / 60 HzOutputvoltageChargingcurrentBatterycapacity15h (Ah)420 – 45 – 90525 – 60 – 110735 – 88 – 160DimensionsWeight(mm)(kg)2,212238 x 193 x 902,6Battery chargersProductname19
Sprintercar1225 plus 2425Sprintercar series are battery chargers for motorcycle, car and tractor batteries witha voltage 6 V, 12 V or 24 V and capacity up to 600 Ah. Units are equipped with 4–stepcharging control.Advantage: charging with decreasing current („W” characteristic); safety fuse (switches off when short circuit or wrong connection to battery poles); charging current meter; metal housing with handle; safety class II.Battery chargers20ProductnameSPRINTERcar1225 –1220 – 230 V50 / 60 acity15h (Ah)12612,51140 – 24030 – 200DimensionsWeight(kg)(mm)4,5255 x 208 x 182241212,51540 – 24050 – 3006,3
Herkules150 300 501Herkules series are the battery chargers for 12 V or 24 V batteries with capacity up to1000 Ah. Units are equipped with starting assist function for car and truck batteries with5–step charging control.Advantage: charging with decreasing current („W” characteristic); digital measure of charging current (digital A meter); starting assist function; safety fuse (switches off when short circuit or wrong connection to battery poles); metal housing with handle; safety class II.ProductnameProductnumberHERKULES 150B18091–1HERKULES 300B18092–1HERKULES 500B18093–1HERKULES 150220 – 230 V50 / 60 HzOutputvoltageChargingcurrentBattery capacity8 h (Ah)15 h (Ah)24122032 – 160–241230120 – 250–24125060–160 – 800200 – werStartingcurrentB18091–11,5112015018483 x 820 x 305HERKULES 300B18092–132250300HERKULES 500B18093–16350050025483 x 890 x 32032Battery chargersProductnameInputvoltage21
StickElectrodesTOP 5ElectrodeClassificationGeneral descriptionDimensions(mm)Weight(kg)OMNIA 46ISO 2560-A: E 38 0 R 11AWS A5.1 E6013 rutile all–around electrode,all position electrode,very easy to use,for „clean” structural steel,for low open circuit voltage transformers.2,0 x 3002,5 x 3503,2 x 3503,2 x 4504,0 x 3504,0 x 4504,24,8 /1,95,3 / 1,96,25,0 / 1,95,9SUPRAISO 2560-A: E 38 0 RC 11AWS A5.1 E 6012 all position rutile electrode,excellent on painted or rusty steel,excellent vertical down welding properties,shipbuilding repairs,recommended for bridging wide gaps,weldable in all positions with one current setting.2,5 x 3503,2 x 3504,0 x 3505,0 x 3502,85,05,05,2PANTAFIXISO 2560-A: E 38 0 RC 11AWS A5.1 E6013 general purpose rutile electrode,for thin plates and bridging wide gaps,excellent in pipe welding and construction,good striking and restriking,good X-ray soundness.2,0 x 3002,5 x 3503,2 x 3504,0 x 3502,42,84,85,4BASIC 7018ISO 2560-A: E 42 4 B 42 H5AWS A5.1 E7018 basic, low hydrogen electrode,excellent weldability,good impact toughness down to -40 C,good operating characteristics and gap bridging,suitable for buffer layers on steels having a higher carbon content,good X-ray soundness.2,0 x 3002,5 x 3503,2 x 3503,2 x 4504,0 x 3504,0 x 4505,0 x 4506,0 x 4503,04,64,55,94,66,15,85,5CONARC 49ISO 2560-A: E 46 3 B 32 H5AWS A5.1: E7018 H4R universal basic electrode for shipbuilding and light constructionwork, almost no spatter, nice wetting and full weld pool control, one current setting for all positions possible, easy welding and 120% recovery contributes to highproductivity.2,5 x 3503,2 x 3504,0 x 3504,0 x 4505,0 x 4506,0 x 4502,74,54,65,96,06,5www.lincolnelectric.pl
CUSTOMER ASSISTANCE POLICYThe business of Lincoln Electric Bester SA is manufacturing and selling high quality welding equipment, consumables and cuttingequipment.Our challenge is to meet the needs of the customer and to exceed their expectations. On occasion, purchasers may ask Lincoln Electricfor advice or information about their use of our products. We respond to our customers based on the best information in our possessionat that time. Lincoln Electric is not in a position to warrant or guarantee such advice and assumes no responsibility, with respect to suchinformation or advice. We expressly disclaim any warranty of any kind, including any warranty of fitness for any customer’s particular purpose,with respect to such information or advice. As a matter of practical consideration, we also cannot assume any responsibility for updating orcorrecting any such information or advice once it has been given, nor does the provision of information or advice create, expand or alter anywarranty with respect to the sale of our products.Lincoln Electric is a responsive manufacturer, but the selection and use of specific products sold by Lincoln Electric is solely within the controlof, and remains the sole responsibility of the customer. Many variables beyond the control of Lincoln Electric affect the results obtained inapplying these types of fabrication methods and service requirements.Subject to change – This information is accurate to the best of our knowledge at the time of printing.www.bester.plCC 08-09
The output current level depends on stick electrode diameter, dimensions and thickness of welded material. Also very important is welding position. Generally speaking – smaller dimensions of welded material equals smaller diameter of the stick electrode and output current. Process welding guide