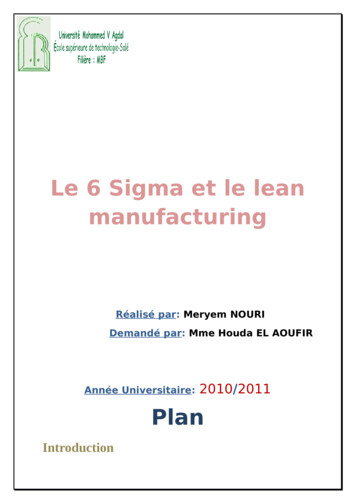
Transcription
Le 6 Sigma et le leanmanufacturingRéalisé par: Meryem NOURIDemandé par: Mme Houda EL AOUFIRAnnée Universitaire:2010/2011PlanIntroduction
1ère Partie : Le 6 SigmaI- Son historique ;II- Sa signification ;III- Ses principes et méthodes d’amélioration ;123-Principes ;La méthode DMAAC ;La méthode DMAPV.IV- Ses acteurs ;2ème Partie : Le lean manufacturingI- Signification du lean manufacturing;II- Ses outils ;III- Les 7 gaspillages (ou Mudas).3èmePartie : Lien entre 6 sigma et lean manufacturingI- Points communs ;II- Points opposés.Conclusion
IntroductionLes travaux préliminaires (essentiellement localisé en production) étantinitialisés, il est possible de passer à l’amélioration globale et la mise souscontrôle cybernétique du système Entreprise afin d’entretenir la boucle versl’Excellence Industrielle. On va ainsi entrer dans une démarche de pilotage etd’amélioration continue des processus.Chaque acteur à son niveau va être invité à traquer les gaspillages quialourdissent son travail et pénalisent ses performances. Traditionnellement, onidentifie sept familles de gaspillages : surproduction, attente, transport, stocks,processus, mouvements, rebuts.Chaque nouvelle période amène ses nouveaux outils. Le Six Sigma et le leanmanufacturing en font partie, annoncés comme moyens pour survivre dans unmonde où les prix baissent, pour concurrencer les leaders tout en évitant lesgaspillages, et pour établir un langage commun dans les services de l’entreprise.Méthodes axées sur la prévention, elles visent à l’optimisation continuelle desproduits et des modes des productions.1ère Partie : Le 6 Sigma
I-Son historique :Pendant des années les Japonais ont défini le standard de la qualité et, dans de nombreux cas,ils continuent de le faire aujourd’hui. Mais au milieu des années 80 la société AméricaineMotorola a décidé qu’il était temps de se mesurer aux japonais en matière de qualité. BobGalvin, alors président de Motorola, estima que les niveaux de qualité "traditionnels", situésentre 3 et 4 sigma, n’étaient simplement plus suffisants. Motorola se fixa un objectif de 6sigma et se dota des moyens d'atteindre ce niveau d'excellence. Leurs efforts donnèrent desrésultats impressionnants. Dans les quelques années qui suivirent, Motorola améliora lesniveaux de qualité de 4 à environ 5.5 sigma et économisa quelque 2.2 millions.Encouragées par le succès de Motorola, plusieurs autres sociétés s'engagèrent dans unedémarche similaire. Mais, ce n’est vraiment qu’en 1993 que Six Sigma commença réellementà transformer les entreprises. Et cette fois ce fut différent : Six Sigma commença à prendreforme, et pas seulement comme un simple système qualité.Six Sigma est devenu un système complet de leadership et de support basé sur des outilsstatistiques de résolution de problèmes développés par Motorola.Peu de temps après, Jack Welch, alors président de General Electric, commença a étudiercette méthodologie. Après un certain temps et beaucoup d’observation, Welch s’engagea.Inutile de dire que quand G.E. fait quelque chose, elle le fait jusqu’au bout. Dans les annéesqui suivirent, G.E. dit avoir économisé des millions de dollars grâce à Six Sigma. Le succèsincroyable de Six Sigma chez General Electric donna le signal à de nombreuses autressociétés.C’est ainsi que les grands noms de l’industrie américaine se sont emparés de la méthode.1985-87: MOTOROLA – Les bases de la démarche sont posées par l’extension de l’usage desstatistiques à tous les processus1990: IBM “International Business Machine”1991: Texas Instrument1993-94: ABB1994-96: Allied Signal, General Electric, Kodak1996-98: Nokia, Sony, Polaroid, Toshiba, Ford Motor, Whirlpool, Invensys, etc.Aujourd’hui : c’est par leur intermédiaire que le Six Sigma arrive en France
II- Signification :Six Sigma est une méthodologie empirique bien structurée, visant à éliminer les défauts,pertes, ou problèmes de contrôle qualité pouvant survenir lors de la fabrication, desprestations de services, du management, et des autres activités de l'entreprise. Laméthodologie Six Sigma utilise une combinaison de techniques éprouvées de maîtrisestatistique des procédés, de méthodes simples et avancées d'analyse des données, et uneformation systématique de tout le personnel, à chaque niveau de l'organisation impliquéedans l'activité ou le processus ciblé par Six Sigma.Le Six Sigma est souvent utilisé pour concilier plusieurs objectifs : doter l’organisationd’actions mesurables et efficaces, réduire les pertes et coûts de la qualité, et bien souvent pouraméliorer l’image de marque du groupe. Ce dernier aspect a d’ailleurs fait naître denombreuses controverses aux Etats Unis car certains groupes se sont appuyés sur ce critèrepour s’attirer les faveurs des investisseurs. Or, autant le Six Sigma est synonyme de bonnespratiques à l’intérieur de l’entreprise, autant il ne peut être retenu comme seul critère de santéfinancière.L’image marketing du Six Sigma a permis aux patrons de s’approprier la qualité, les notionsde variabilité des processus et d’insatisfaction client, domaine autrefois réservé au seulservice qualité. Les arguments financiers avancés ont séduit les dirigeants et cette méthodeleur est apparue comme un moyen de rationaliser la qualité, de l’intégrer dans le business,pour qu’enfin elle rapporte.Signification concrète :Plus en donnant au sigma une valeur élevée, plus le nombre des défectuosités baisse et lesbénéfices augmentent.En 2sigma, on se trouve avec 308.500 million de pièces défectueuses, en 3sigma on a 6.200million défauts, en augmentant la valeur du sigma à 5 on aura 232 million défauts, et enarrivant à 6sigma on constate une forte baisse des défectuosités «3.4 millions de défauts ».
Dans la vie pratique, en appliquant l’indicateur 6 sigma, on obtiendra ce qui suit :III- Ses principes et méthodes d’amélioration :1-Principes :Six Sigma repose sur les notions de client, processus et mesure ; il s'appuie surtout sur :1. les attentes mesurables du client ;2. des mesures fiables mesurant la performance du processus de l'entreprise comparé àces attentes ;3. des outils statistiques pour analyser les causes sources influant sur la performance ;4. des solutions attaquant ces causes sources ;5. des outils pour contrôler que les solutions ont bien l'impact escompté sur laperformance.
2-La méthode DMAAC :La puissance de Six Sigma réside dans son approche "empirique", pilotée par les données (etl'utilisation de mesures quantitatives pour vérifier la manière dont le système se comporte)pour atteindre l'objectif d'amélioration du processus et la réduction de la dispersion. Cecis'opère par l'application de projets dits "d'amélioration Six Sigma" qui, à leur tour suiventla série des étapes "DMAAC de Six Sigma" (Définir, Mesurer, Analyser, Améliorer etContrôler). Plus précisément : Définir : Cette phase s'attache à la définition des objectifs et limites du projet, etl'identification des questions nécessaires pour atteindre le niveau de sigma le plusélevé possible. Mesurer : L'objectif de mesurer la stratégie Six Sigma consiste à rassembler lesinformations disponibles à propos de la situation courante, pour obtenir les données deréférence concernant les performances actuelles du processus, et d'identifier les zonesà problèmes. Analyser : L'objectif de l’analyse dans l'effort de qualité Six Sigma consiste àidentifier la ou les causes les plus probables des problèmes de qualité, et de confirmerces causes à l'aide des outils analytiques appropriés. Améliorer : Cette phase consiste à mettre en place des solutions visant à résoudre lesproblèmes (causes les plus probables) identifiées lors de la phase précédente(Analyser). Contrôler : Il consiste à évaluer et suivre l'évolution des résultats de la phaseprécédente (Améliorer).3-La méthode DMAPV :Il existe une variante de la séquence fondamentale DMAAC de Six Sigma, appelée DMAPV,et qui s'applique à la conception de nouveaux processus. Dans la séquence DMAPV, la phaseDéfinir est identique à celle de DMAAC; la phase Mesurer s'attache à mesurer les besoins duclient et/ou de l'application/marché, la phase Analyser s'intéresse à l'analyse des options duprocessus et enfin, les phases Améliorer et Contrôler sont remplacées par les phases Plan(pour adapter le processus aux besoins du client et/ou de l'application/marché) et Vérifier(vérifier les performances du plan et ses capacités à répondre aux critères définis dans laphase Plan).
IV- Ses acteurs :La méthode Six Sigma concerne l'ensemble des strates d'une organisation et s'appuie surplusieurs ressources humaines qui lui sont propres, qui ont toutes leur rôle à jouer. L'imagecouramment admise est celle d'une pyramide de fonctions d'expertise croissante : Le Green Belt «ceinture verte», dont on attend qu'il consacre partiellement sontemps (fréquemment autour de 25%) à la conduite de projets d'amélioration. Le Black Belt «ceinture noire», chef d'équipe qui se consacre à plein temps à leperfectionnement (conduite de projets, formation des Green Belts ou alors d'autresBlack Belts) et doit maîtriser la méthode dans son ensemble. Il est plus spécialisé enDMAAC. Le Master Black Belt, formateur de Blacks Belts, garant du respect de la démarche,encadre les Blacks Belts hiérarchiquement. Le Deployment Leader ou Champion («directeur du déploiement» ou plusfréquemment «directeur du dispositif d'excellence»), chargé d'élaborer la stratégie,le contenu de la formation, les budgets, etc.Précisons que ces acteurs du Six Sigma ont leurs propres règles de certification, avec desexamens, des académies, des séminaires professionnels. Néanmoins, on peut citer lacertification de l'American Society for Quality (ASQ) qui bénéficie d'une reconnaissanceinternationale. Certaines entreprises ont signé des accords de reconnaissance mutuelle decertification Six Sigma, qui font qu'une certification Six Sigma mérite de figurer dans un CV.
2ème Partie : Le lean manufacturingI-Signification du lean manufacturing :Le Lean Manufacturing est une approche à la gestion des flux et des installations dontl'objectif est de réduire drastiquement les délais de production. Cette réduction des délais vaentraîner des réductions de coûts très fortes (réduction des en-cours, des stocks, des pertes detemps, etc.) et contribuer à améliorer la qualité des produits.Le Lean Manufacturing n’a pas pour seul objectif d’obtenir à court ou moyen terme uneamélioration significative des résultats. Le Lean est avant tout un changement profond deculture et de mentalité dans l’unité de production. Ce n’est qu’à cette condition que lesrésultats obtenus pourront être durables, et que la marche vers l’excellence pourra sepoursuivre.Il s’inscrit clairement dans une démarche de développement durable, en évitant lesgaspillages, en responsabilisant le personnel dans une optique positive résolument tournéevers l’avenir. C’est l’un de ses principaux objectifs.En sensibilisant chacun des acteurs de la chaîne, le lean manufacturing développe en parallèleles notions de productivité et de qualité de production. La qualité de vie dans l’atelier estaccrue et on améliore les conditions de travail de l’ouvrier en le responsabilisant dans ses
tâches quotidiennes. L’implication de l’employé dans l’exercice de ses tâches doit luipermettre de limiter les pertes qu’il occasionne, de contribuer à limiter les déchets qui nuisentà la fois à la productivité et à l’environnement, à les trier, mais également à mieux concevoirl’organisation générale de l’espace de travail. Le lean manufacturing vise une progressioncontinue. Les principes doivent devenir des réflexes et faire partie de la culture d’entreprise.On cible donc le personnel en place tout en préparant le terrain pour les générations futuresII- Ses outils :Le Lean Manufacturing comprend entre autres les outils suivants : Le 5S : Le 5S permet d’éliminer ce qui est inutile, définir une place pour chaquechose, nettoyer, définir les gammes et procédure nécessaires, enfin auditer et mesurerl’amélioration. Cet outil de base du Lean a pour principal objectif de changer lesmentalités et mettre en route une politique d’amélioration continue. L'analyse VSM (Value Stream Mapping) : Cette méthode d'analyse du Leanmanufacturing permet de définir les principales réserves de productivité d'une unité deproduction en suivant le flux complet de la production d'une pièce. La mesure dutemps d'écoulement des pièces, des niveaux de stock et de leurs valeur, permet dedéfinir un certain nombre de chantiers d'amélioration à mettre en place en prioritédans une démarche Lean Manufacturing. Le SMED (Single Minute Exchange Die) : Cette méthode du Lean Manufacturing,d’abord utilisée pour réduire les temps de changement d’outillage, peut être employéepour flexibiliser tout processus productif ou administratif. L’objectif est l’éliminationprogressive des stocks et l’amélioration de la productivité grâce à la mise en placed’une organisation réactive et flexible. Le TPM (Total Productive Maintenance) : Le TPM est un outil essentiel du LeanManufacturing pour mesurer les pannes et arrêts machine, et les risques associés. Unplan d'action correctif peut alors être mis en place, ainsi qu'un véritable managementde la maintenance préventive. Le Hoshin de flux : Cette méthode regroupe plusieurs outils du Lean Manufacturingpour optimiser les flux grâce à la réduction des temps d’écoulement, l’élimination desstocks intermédiaires, la suppression des temps non productifs, et l’équilibrage despostes de production.
Les Poka-Yoke : Ce sont des systèmes simples permettant d'éviter les erreursinvolontaires des opérateurs. Les Poka-Yoke sont aussi appelés "détrompeurs" ou"systèmes anti-erreur" et sont couramment utilisés dans le Lean Manufacturing. Le Kanban : C'est un système d'ordonnancement de la production à base de cartes(ou via un système visuel simple) permettant de tirer les flux. Le Kanban estfréquemment utilisés dans le Lean Manufacturing pour le management des flux tirés.Il permet le management des flux internes en laissant la gestion des flux externe. La visualisation ou l'affichage opérationnel : C'est un élément essentiel de toutedémarche Lean, dont l'objectif est d'informer en temps réel et de permettre uneréaction immédiate aux problèmes. L'affichage opérationnel du Lean Manufacturingdoit donc se mettre en place à tous les niveaux de l'entreprise, et prendre en compteles objectifs définis et les problématiques rencontrées à chaque niveau.II- Les 7 gaspillages ( ou Mudas ) :La roue des sept gaspillages illustre les différentes catégories de gaspillage contrelesquels le Lean Manufacturing va lutter. Il convient de se fixer des priorités et d’attaqueren premier les gaspillages qui ont le poids économique dans l’entreprise. En général, unaudit préliminaire permet de déceler les principales sources de gaspillage et d’en évaluerle coût. Sur la base de cette analyse, un plan de Productivité (Lean Manufacturing) peutêtre bâti et mis en œuvre pour la recherche de l'excellence industrielle.
3èmePartie : Lien entre 6 sigma et lean manufacturingLean Manufacturing et Six Sigma sont deux systèmes de contrôle de la qualité que lesentreprises peuvent utiliser pour aider à améliorer la qualité de votre fabrication. Ces deuxsystèmes ont un peu de points communs, mais ils ont aussi quelques différences aussi . Afinde déterminer quel système va fonctionner le mieux dans une telle entreprise, les responsablesdevront comprendre comment ils se ressemblent et comment ils sont différents . C'estimportant parce que chaque système a ses avantages et ses inconvénients.Six sigma est un système de contrôle de la qualité qui est conçu pour se concentrer sur lesprocessus des entreprises. En se concentrant sur le processus Six Sigma les e/ses vont voir
quel genre d'améliorations peuvent être apportées à chacun des processus afin que la qualitédu produit peut être améliorée. Lean manufacturing est un système de contrôle de la qualitéqui met l'accent sur la réduction des coûts globaux de l’entreprise en se débarrassant de toutesles activités qui ne sont pas nécessaires au processus de fabrication.Les deux processus sont conçus pour garder un œil sur la satisfaction de la clientèle.I- Points communs: Elimination les déchets de l’usine de fabrication. Les deux méthodes veulent sedébarrasser de tous les déchets, les approches qu'ils utilisent pour atteindre cet objectifsont très différentes. Par exemple, six sigma se concentre sur l'amélioration duprocessus d'affaires tout en réduisant les déchets, le lean manufacturing met l'accentsur la réduction des coûts et l'augmentation du chiffre d'affaires en supprimant toutesles activités inutiles.Les deux méthodes sont modelées, Six sigma utilise le modèle DMAIC, tandis que lafabrication sans gaspillage utilise des principes qui sont spécifiques à la fabricationsans gaspillage.II- Points opposés : Une grande différence entre les deux est le genre de groupes qu'ils utilisent. Les deuxsix sigma et la fabrication sans gaspillage s'appuient sur des équipes pour obtenir lesrésultats souhaités, mais la façon dont les équipes sont mises ensemble et formésvarie. Avec six sigma, il est soutenu par une ceinture noire avec une équipe interfonctionnelle, ce qui signifie que l'équipe puisse se concentrer sur plus d'une zone del'usine de fabrication. Avec la fabrication sans gaspillage, il y a juste une petite équipeopérationnelle qui est utilisé pour traiter les questions qui peuvent trouver sur unebase quotidienne. La petite équipe opérationnelle dans la fabrication maigre n'est pasune formation polyvalente, de sorte qu'ils ne peuvent se concentrer sur autre chose quece qu'ils sont formés à traiter.
Les approches que les 2 méthodes utilisent pour l’élimination des déchets sont trèsdifférentes. Par exemple, six sigma se concentre sur l'amélioration du processusd'affaires tout en réduisant les déchets, le lean manufacturing met l'accent sur laréduction des coûts et l'augmentation du chiffre d'affaires en supprimant toutes lesactivités inutiles. Une autre grande différence entre les deux systèmes est les outils qu'ils utilisent pouratteindre leurs résultats souhaités. Six sigma utilise cartographie des processus pourconnaître les différents processus, ainsi que la description des processus, elle utiliseégalement des organigrammes pour tracer chaque processus pour voir où lesaméliorations peuvent être apportées. Avec la fabrication sans gaspillage, le principaloutil qu'il utilise est le flux de valeur, qui est un graphique qui montre comment lavaleur du produit ou du procédé est transmis aux clients.Peu importe la façon dont ces deux systèmes fonctionnent, ce que les E/ses doivent faire estde décider quel système fonctionne le mieux pour leur production.ConclusionLes deux méthodes 6 Sigma & Lean Manufacturing consistent donc àidentifier et à éliminer toutes les pertes d’efficacité qui jalonnent la chaîne de lavaleur (depuis la réception de la matière jusqu’à l’expédition du produit).
Il est bien évident que les actions Lean Manufacturing et le pilotage Six Sigma,qui peuvent apparaître séquentiels au lancement des démarches, ne sont enaucun cas bornées dans le temps et seront donc amenées à co-évoluer,intelligemment et avec une vision globale et concertée de préférence.Bibliographie : Manager la performance industrielle, Yves Beunon et BrunoSéchet, Gereso éditions.Webographie :www-igm.univ-mlv.fr/ dr/XPOSE2002/6sigma/definition.htm
rce.com
Motorola se fixa un objectif de 6 sigma et se dota des moyens d'atteindre ce niveau d'excellence. Leurs efforts donnèrent des résultats impressionnants. Dans les quelques années qui suivirent, Motorola améliora les niveaux