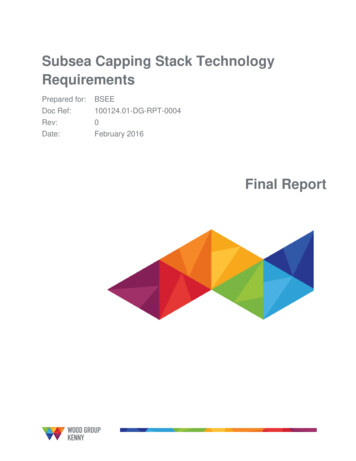
Transcription
Subsea Capping Stack TechnologyRequirementsPrepared for:BSEEDoc Ref:100124.01-DG-RPT-0004Rev:0Date:February 2016Final Report
Subsea Capping Stack Technology RequirementsFinal ReportLimitations of the ReportThe scope of this report is limited to the matters explicitly covered and is prepared for thesole benefit of the Bureau of Safety and Environmental Enforcement (BSEE). Inpreparing the report, Wood Group Kenny (WGK) relied on information provided by BSEEand third parties. WGK made no independent investigation as to the accuracy orcompleteness of such information and assumed that such information was accurateand complete.All recommendations, findings, and conclusions stated in this report are based on factsand circumstances as they existed at the time this report was prepared. A change in anyfact or circumstance on which this report is based may adversely affect therecommendations, findings, and conclusions expressed in this report.100124.01-DG-RPT-0004 Rev 0 February 2016Page 3 of 188
Subsea Capping Stack Technology RequirementsFinal ReportExecutive SummarySince 2010, the industry has made great strides in increasing the capabilities for subsea wellcontrol response based on learnings from the Macondo incident. This study provides a detailedanalysis of the subsea capping stack availability, storage locations, and technical capabilities.This study also reviews the regulations and standards and a draft Code of Federal Regulations(CFRs) and a Potential Incident of Noncompliance (PINC) list for subsea capping stacks hasbeen developed.The subsea capping stack is part of the Source Control and Containment Equipment (SCCE),along with the cap and flow system, the containment dome, and other subsea and surfacedevices, equipment, and vessels. The collective purpose of SCCE is to control a spill sourceand stop the flow of fluids into the environment. This study, which is specific to subsea cappingstacks, does not consider other SCCE.Literature Review and Industry SurveysWood Group Kenny (WGK) has conducted a detailed literature review to evaluate available U.S.regulations for source control and containment. It was determined that current U.S. regulationsinclude no information related to SCCE. The Bureau of Safety and Environmental Enforcement(BSEE) issued Notice to Lessees and Operators (NTL) 2010-N10, which required Operators todemonstrate that they have access to capping and containment equipment to receive approvalfor the Application for Permit to Drill (APD). In April 2015, the BSEE published a Proposed Rulefor well control that would consolidate the current regulations and NTLs. As part of the ProposedRule, the BSEE provided a separate section for source control and containment.In February 2015, the Department of the Interior (DOI), acting through the BSEE and theBureau of Ocean Energy Management (BOEM), proposed regulations on requirements forexploratory drilling in the Arctic Outer Continental Shelf (OCS). This proposed Arctic regulationrequires access to SCCE with a subsea capping stack positioned to arrive at a well within 24hours after a loss of well control, and a cap and flow system and a containment domepositioned to arrive at the well within 7 days after a loss of well control. Currently, there are noactive U.S. regulations or inspection criteria guidelines for subsea capping stacks.American Petroleum Institute Recommended Practice (API RP) 17W provides guidelines for thedesign, manufacture, use, preservation, transportation, and maintenance procedures of subseacapping stacks. The development and delivery of subsea capping stacks began immediatelyfollowing the Macondo incident in 2010, prior to the issuance of API RP 17W. The design ofthese systems was based on the existing subsea equipment (for example, Blowout Preventer[BOP] rams, valves, and chokes), for which industry standards were already established. Thestrategy for the design of subsea capping stacks was employed to allow for rapid delivery toindustry, based on conventional components, field-proven track records, accepted reliability,100124.01-DG-RPT-0004 Rev 0 February 2016Page 4 of 188
Subsea Capping Stack Technology RequirementsFinal Reportestablished technical knowledge base, and availability of spare parts. In addition, an objective ofthis strategy was to avoid the high costs and long lead times generally associated with thedevelopment of new safety equipment technology by shortening the process typicallyassociated with its conception, design, fabrication, testing, and certification.Subsea Capping Stack AvailabilityThe consortiums and organizations that own subsea capping stacks are listed in thefollowing table.TypeNo. of SubseaCapping StacksMWCCConsortium3Ingleside, TXU.S. Gulf of MexicoHWCGConsortium2One in Houston, TX andanother in Ingleside, TXU.S. Gulf of MexicoOSPRAGConsortium1Aberdeen, ScotlandU.K. Continental ShelfGlobal (except U.S. waters)NameStaging LocationRegion ServedOSRLConsortium4One at each location:Brazil, Norway, Singapore,and South AfricaWellCONTAINEDOrganization2One in Aberdeen, Scotlandand another in SingaporeGlobal (inclusive of U.S.waters)Operator3One in Alaska; others inAberdeen, Scotland, andSingaporeGlobal (Shell operationsonly)ShellHouston stack (Global BPoperations)BPOperator2One in Houston andanother in AngolaAngola stack (BPoperations only in Angolanwaters)For the U.S. Gulf of Mexico (GOM), it is mandatory for Operators conducting subsea drillingoperations to demonstrate access to a subsea capping stack and the necessary expertise andassets to mobilize and install the stack offshore. Five subsea capping stacks to facilitatecompliance with this requirement are staged within the Gulf Coast region. Two consortiums andone organization support the U.S. GOM. The Marine Well Containment Company (MWCC) is aconsortium that provides access to three subsea capping stacks, and HWCG LLC is aconsortium that provides access to two subsea capping stacks. In addition, WellCONTAINED100124.01-DG-RPT-0004 Rev 0 February 2016Page 5 of 188
Subsea Capping Stack Technology RequirementsFinal Reportorganization maintains two subsea capping stacks outside of the U.S. These stacks can bemobilized to U.S. GOM if needed. Currently, WellCONTAINED does not support Operators inobtaining permits to drill in the U.S. GOM region.For the U.K. Continental Shelf (UKCS), three subsea capping stacks are staged within theregion. The Oil Spill Prevention and Response Advisory Group (OSPRAG) is a consortium thathas one subsea capping stack staged in Aberdeen, U.K. The WellCONTAINED organizationhas one subsea capping stack staged in the U.K., which is available for global use. The Oil SpillResponse Limited (OSRL) consortium has one subsea capping stack staged in Norway that isavailable for global use.Outside of the U.S. and U.K. regions, excluding Operator-owned stacks, the industry hasaccess to six subsea capping stack systems that are made available through the OSRLconsortium and the WellCONTAINED organization. The OSRL consortium has a total of foursubsea capping stacks that are available for use outside of U.S. waters; they are staged inNorway, Brazil, Singapore and South Africa. The WellCONTAINED organization has twosubsea capping stacks available for use globally; they are staged in the U.K. and Singapore.In summary, the U.S. and U.K. are the only regions with dedicated consortiums (e.g., MWCC,HWCG, and OSRPAG) to support subsea capping stack response. However, there is subseacapping stack access for all regions of the world through the OSRL consortium and theWellCONTAINED organization. The caveat to this statement is that most of the countries do nothave regional access to a subsea capping stack, and they are dependent on the consortium orthe organization-owned capping solutions staged at varying strategic locations around theworld. It can be surmised that these regions and countries will likely have longer response timesbecause of the length of time associated with marine transport of the subsea capping stack fromtheir storage locations to the incident sites.Recommended CFR and PINC ListWGK has worked with the Well Containment Consortiums (MWCC, HWCG LLC, and OSRL)and a manufacturing company (Trendsetter Engineering) to draft regulations for subsea cappingstacks based on global learnings and experience with subsea capping stacks. WGKrecommends that the drafted Code of Federal Regulations (CFR) be incorporated as part of 30CFR 250 Subpart D.WGK also drafted the PINC List for subsea capping stacks in accordance with the formatincluded in the National PINC Guideline List. WGK participated in a workshop with the WellContainment Consortiums to review the draft PINC List and to get their feedback. WGKrecommends that the PINC List be appended to the current Drilling PINCs. BSEE personnel canuse this PINC List for inspection in the field and at onshore support bases.100124.01-DG-RPT-0004 Rev 0 February 2016Page 6 of 188
Subsea Capping Stack Technology RequirementsFinal ReportThe subsea capping stack CFR and the PINC List are only recommendations to BSEE: BSEEmay modify and use them in the future.Recommendations: Evaluate subsea capping stack components that can accommodate weight savings. Thiscould involve using gate valves instead of BOP rams for smaller bore sizes. The gatevalves can provide the same pressure rating as BOP rams. The benefits associated withthe use of gate valves include improved sealing reliability (metal-metal sealing surface),reduction in weight, and simplified operation, thereby avoiding the need for SubseaAccumulator Module (SAM) units.Because of the geographic distances between subsea capping stack storage locations andpotential incident sites, it is recommended that a specific subsea capping stack should beidentified prior to the commencement of operations within each deep water drilling regionand the associated mobilization planning that is conducted to determine the estimatedresponse time. This process would allow for the assessment of an estimated responsetime to ensure that it is acceptable as well as to identify areas for efficiency improvementrelated to deployment and installationDevelop subsea capping stacks for High Pressure High Temperature (HPHT) conditions.The consortium owners should consider procuring new HPHT subsea capping stacks orimproving the capabilities of the existing ones, depending on the members’ planned wellsto which the consortium may need to respond. Shell has contracted Trendsetter to delivera 400 F subsea capping stack in 2016, and MWCC has contracted Trendsetter to deliver a20,000 psi subsea capping stack by 2017.Review other parts of SCCE (such as the containment system1, debris removal, anddispersant equipment). Currently, there are no minimum requirements for the containmentsystem and no consistency on what defines a containment system. There are differenttechnologies and levels of containment system (interim versus long-term), depending onthe capabilities. It must be noted that the absence of ‘minimum requirements’ or adefinition of a containment system has allowed development (in the U.S. GOM at least) oftwo different, robust solutions. In addition, the interfaces between subsea capping stacksand containment systems have not been standardized; this could lead to delays indeployment and recovery operations should an incident occur.Although BSEE currently uses terminology such as ‘Cap,’ ‘Cap and Flow,’ and ‘SourceControl and Containment Equipment,’ it is highly recommended that this terminology beassessed and reviewed against terminology which is being standardized internationally.1A containment system includes any system or component downstream of the subsea capping stack thatdirects flow.100124.01-DG-RPT-0004 Rev 0 February 2016Page 7 of 188
Subsea Capping Stack Technology RequirementsFinal ReportSome examples of major discrepancies include the U.S. term ‘Cap and Contain’ (whichmeans installation and shut-in with a subsea capping stack), while the term ‘Capping’means the same thing internationally. In the U.S., the term ‘Cap and Flow’ implies that acapping stack has been installed, but the well is being flowed to a surface vessel;internationally, the term ‘Containment’ has the same meaning.100124.01-DG-RPT-0004 Rev 0 February 2016Page 8 of 188
Subsea Capping Stack Technology RequirementsFinal ReportRevision History (Optional)RevisionDateCommentsA11 Nov 2015Issued for Internal ReviewB30 Nov 2015Issued for Client ReviewC30 Dec 2015Issued for Client Review with Comments Incorporated009 Feb 2016Issued for UseHOLDSNo.SectionCommentSignatory LegendRevisionRoleComments0PreparedBhaskar Tulimilli (BT)CheckedJorge Alba (JA)ApprovedEddie Mouret (EM)100124.01-DG-RPT-0004 Rev 0 February 2016Page 9 of 188
Subsea Capping Stack Technology RequirementsFinal ReportTable of Contents1.0Introduction. 201.1General . 201.2Background . 201.3Report Objectives . 211.4Abbreviations . 222.0Source Control and Containment (or Well Containment) . 262.1Introduction . 262.2Post-Blowout Remediation . 262.3Subsea Capping Stacks . 272.3.1 Subsea Capping Stack Categories . 282.3.2 Major Components of a Subsea Capping Stack. 302.4Well Containment Response Work Flow . 372.4.1 General. 372.4.2 Site Survey and Initial Assessment . 392.4.3 Debris Removal . 392.4.4 Subsea Dispersant Application . 402.4.5 Capping . 412.4.6 Capture and Collection . 422.4.7 Relief Well . 433.0Available Subsea Capping Stacks and their Technical Capabilities . 443.1Introduction . 443.2Subsea Capping Stacks Consortiums and Organizations . 443.2.1 Marine Well Containment Company . 463.2.2 HWCG LLC . 513.2.3 Oil Spill Prevention and Response Advisory Group . 553.2.4 Subsea Well Response Project/Oil Spill Response Limited . 573.2.5 WellCONTAINED . 643.2.6 Shell . 693.2.7 BP . 734.0Subsea Capping Stacks Gap Analysis . 78100124.01-DG-RPT-0004 Rev 0 February 2016Page 10 of 188
Subsea Capping Stack Technology RequirementsFinal Report5.0Specifications, Standards, and Recommended Practices Applicable to SubseaCapping Stacks. 825.1Introduction . 825.2API Specifications Relevant to Subsea Capping Stacks . 825.2.1 API 16D – Specification for Control Systems for Drilling Well Control Equipment andControl Systems for Diverter Equipment . 825.2.2 API 6A – Specification for Wellhead and Christmas Tree Equipment/ISO 10423 . 835.2.3 API 16A – Specification for Drill-through Equipment/ISO 13533 . 835.2.4 API 17D – Design and Operation of Subsea Production Systems – Subsea Wellheadand Tree Equipment . 845.2.5 API 6AV1 – Specification for Validation of Wellhead Surface Safety Valves andUnderwater Safety Valves for Offshore Service . 845.3API Standard 53 – Blowout Prevention Equipment Systems for Drilling Wells . 845.4API Recommended Practices Relevant to Subsea Capping Stacks . 855.4.1 API 17W – Recommended Practice for Subsea Capping Stacks . 855.4.2 API 17H – Recommended Practice for Remotely Operated Vehicle (ROV) Interfaces onSubsea Production Systems . 865.4.3 API 17G – Recommended Practice for Completion/Workover Risers . 866.0U.S and Global Regulations Available for Subsea Capping Stacks . 886.1Introduction . 886.2International Regulators Capping Solutions . 886.2.1 Australian Capping Solution. 886.2.2 Canadian Capping Technology . 896.2.3 Norway Capping Solution . 906.2.4 U.K. Capping Solution . 916.2.5 Brazil Capping Solution . 916.2.6 New Zealand Capping Solution . 916.2.7 De
MWCC Consortium 3 Ingleside, TX U.S. Gulf of Mexico HWCG Consortium 2 One in Houston, TX and another in Ingleside, TX U.S. Gulf of Mexico OSPRAG Consortium 1 Aberdeen, Scotland U.K. Continental Shelf OSRL Consortium 4 One at each location: Brazil, Norway, Singapore, and South Africa Global (except