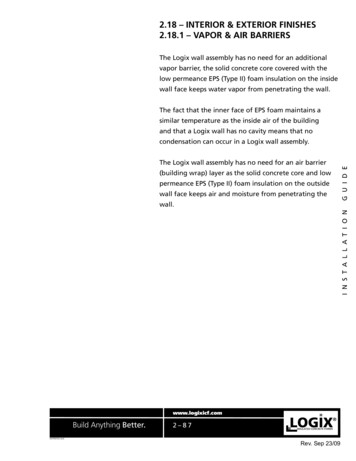
Transcription
2.18 – INTERIOR & EXTERIOR FINISHES2.18.1 – VAPOR & AIR BARRIERSThe Logix wall assembly has no need for an additionalvapor barrier, the solid concrete core covered with thelow permeance EPS (Type II) foam insulation on the insidewall face keeps water vapor from penetrating the wall.The fact that the inner face of EPS foam maintains asimilar temperature as the inside air of the buildingand that a Logix wall has no cavity means that nocondensation can occur in a Logix wall assembly.G U I D EThe Logix wall assembly has no need for an air barrier(building wrap) layer as the solid concrete core and lowpermeance EPS (Type II) foam insulation on the outsidewall face keeps air and moisture from penetrating theI N S T A L L A T I O Nwall.www.logixicf.comBuild Anything BetterREPRINTED 20162–87 Rev. Sep 23/09
2.18.2 – INTERIOR DRYWALLDrywall should be installed in the same manner on aLogix wall as on a stud wall, with the following timesaving exceptions: All webs (studs) are on 8 inch (203 mm) centersfrom floor to ceiling for easy attachment of anytype of interior wall finish. The butt joints of the sheetrock do not need tofall on webs (studs) as the foam provides solidG U I D Ebacking wherever the joints fall. However, theedge of sheetrock panels should not exceed morethan 4” from webs.I N S T A L L A T I O N A foam-compatible adhesive can be used toeffectively fasten the sheetrock to the Logix wallalong with screws. Always make sure to verifythe local code for types and spacing for sheetrockfasteners. Typically, adhesive alone is not allowedas a fastener of sheetrock, but again check withlocal building codes.Many local building codes require the application of 1/2inch (13 mm) drywall or other suitable thermal barrierin any living space even though the EPS foam has a fireretardant component. Always verify local building coderequirements.www.logixicf.comBuild Anything BetterREPRINTED 20162–88 Rev. Nov 23/15
2.18.2 – INTERIOR DRYWALL CONTINUEDNon-habitable spaces such as crawl spaces, attics, andother types of hidden areas typically do not require athermal barrier (drywall).Embedded furring tabs are fixed at each corner of theLogix 90 corner forms for solid sheetrock fastening at allI N S T A L L A T I O NG U I D Ecorners.www.logixicf.comBuild Anything BetterREPRINTED 20162–89 Rev. Sep 23/09
2.18.3 – EXTERIOR SIDINGSiding material of some kind must be installed over theEPS foam to protect it from the UV rays of the sun. Foamleft exposed to the sun will degrade on the exposedsurface by slowly breaking and getting “dusty”.I N S T A L L A T I O NG U I D ENOTE: When using Logix Platinum Series care shouldbe taken to protect exposed foam surfaces fromreflected sunlight and prolonged solar exposure untilwall cladding or finish material is applied. Shadeexposed foam areas, or remove sources of reflectivesurfaces, where heat build up onto exposed foammight occur. For more information refer to BASFTechnical Leaflet N-4 Neopor, “Recommendationsfor packaging, transporting, storing and installingbuilding insulation products made from Neopor EPSfoam.” (The BASF Technical Leaflet is attached toevery bundle of Logix Platinum forms delivered to ajob site).Metal and vinyl siding can be installed directly over thetop of the EPS.Although air guns can be used, Logix recommends theuse of screw guns when attaching exterior siding. Alwaysfollow manufacturer’s recommendations and local codesto determine the size and spacing of fasteners for allsiding products.Any type of siding that is used on a typical wood-framedbuilding can be used on a Logix building.The siding channel stock around doors and windowscan be fastened to whatever type of buck material waschosen, in a similar fashion as wood framed building.www.logixicf.comBuild Anything BetterREPRINTED 20162–90 Rev. Nov 23/15
2.18.4 – STEEL PANEL SIDINGSteel panel siding can be applied vertically to a Logix wallwhen the style of the panel matches the Logix web 8 inch(203 mm) increments for fastening purposes.When a panel siding is chosen that doesn’t fit with 8 inch(203 mm) increment for fastening, two different methodsare available:METHOD 1:A 1/2 inch (13 mm) or 3/4 inch (19 mm) strip of woodprovide the manufacturer’s specified fastener spacing.METHOD 2:The panels can be installed horizontally, by fasteningdirectly into the webs.NOTE: Although air guns can be used, Logix recommendsthe use of screw guns when attachingexterior siding. Always follow manufacturer’srecommendations and local codes to determinethe size and spacing of fasteners for all sidingproducts.www.logixicf.comBuild Anything BetterREPRINTED 20162–91 Rev. Sep 23/09I N S T A L L A T I O NG U I D Ecan be attached horizontally to the webs in the wall to
2.18.5 – WOOD SIDINGAny wood siding can be attached to the Logix wall in thesame manner as to a traditional framed building. Thespacing of the web studs on 8 inch (203 mm) centersallows for industry standard spacing of fasteners.Typically, screws are used for attaching wood siding oreven half-log siding to the Logix wall.Although air guns can be used, Logix recommends a screwgun with screws in clips (Quik Drive). This is usually thefastest method for applying wood siding. Always followG U I D Emanufacturer’s recommendations and local codes todetermine the size and spacing of fasteners for all sidingproducts.I N S T A L L A T I O NA good practice for installing wood siding on a wall, isto apply the siding over vertical 1 inch x 2 inch (25 mm x51 mm) wood nailing strips with a screen at the bottom.The screen keeps insects out while the space allows airto circulate behind the siding. The air circulation helpsequalize the moisture content in the wood siding, whichmakes for much more dimensionally stable siding andlonger lasting application.www.logixicf.comBuild Anything BetterREPRINTED 20162–92 Rev. Sep 23/09
2.18.6 – EIFSThere are now acrylic-based stucco products available thatare more flexible and easier to work with than traditionalcement-based stucco. Collectively these products areknown as EIFS (Exterior Insulation Finish Systems) andalmost always require an EPS substrate.Because Logix blocks are made with EPS, they are anatural fit for EIFS finishes. In addition, the webs in Logixblocks are embedded 1/2 inch (13 mm) deep in the EPSG U I D Efoam to comply with EIFS manufacturer requirements.It is important to follow the EIFS manufacturer’sI N S T A L L A T I O Napplication procedures.www.logixicf.comBuild Anything BetterREPRINTED 20162–93 Rev. Sep 23/09
2.18.7 – TRADITIONAL STUCCO(CEMENT-BASED)Logix walls will accept traditional cement-basedstucco product. Although air guns can be used, Logixrecommends a screw gun when attaching the wire lathmesh to Logix walls. Use screws with a wide head orscrews along with washers to best hold the mesh in place.Consult local building codes for vertical and horizontalfastener placement requirements. The center-to-centefastener spacing requirements for nails and staplesmust be followed for screws as well. Again, check withG U I D Elocal codes for all specific requirements relating to theapplication of stucco over EPS insulation.I N S T A L L A T I O N2.18.8 – CEMENT COMPOSITE SIDINGRecently the new cement fiber siding products havegained popularity. This type of siding can usually befastened directly to the Logix webs. Although air gunscan be used, Logix recommends a screw gun to fasten flatheaded exterior screws at 16 inch (406 mm) centers. Thescrews pull the siding in tight and hold the siding securelyin place. Some manufacturers may require the sidingto be strapped out to allow air space behind. Verticalor shake patterns will require strapping for fastening.Always follow manufacturer’s recommendations and localcodes to determine the size and spacing of fasteners forall siding products.Check with your siding manufacturer for specificrequirements.www.logixicf.comBuild Anything BetterREPRINTED 20162–94 Rev. Sep 23/09
2.18.9 – BRICK VENEERThe Logix Brick Ledge form units are used to support abrick veneer as the exterior finish material. The BrickLedge forms are simply placed at a level where the brickis desired to begin. The design of the form creates areinforced concrete ledge.With standard reinforcing, the Brick Ledge can bear up to1300lb/ft (19kN/m) of wall.wall is attainable.To install Brick Ledge form units, follow the instructionson Section 2.7.4 of the guide. When reinforcing steelI N S T A L L A T I O Nand concrete are in place within the wall, brick is laid onthe ledge and tied back to the webs with brick ties asFor full size CAD drawing seespecified.Section 5, CAD Drawingswww.logixicf.comBuild Anything BetterREPRINTED 20162–95G U I D EWith site-specific engineering, up to 3000lb/ft (44kN/m) of Rev. Sep 23/09
2.18.10 – BELOW GRADE WATERPROOFING,DAMPPROOFING & PARGINGThere are many methods available to protect the “belowgrade” and the “just above grade” areas of the exteriorof your building.Dampproofing is used on concrete or masonry surfaces torepel water in above grade walls. The 2.75 inch (70 mm)and thicker foam panels of the Logix insulated concreteforms acts as dampproofing, therefore, no additionaldampproofing treatment is required.G U I D ENOTE: Although dampproofing above grade walls is nottypically required, check with local building codesI N S T A L L A T I O Nfor dampproofing requirements.www.logixicf.comBuild Anything BetterREPRINTED 20162–96 Rev. Sep 23/09
2.18.10.1 – BELOW GRADEWATERPROOFINGLogix recommends a rubberized “peel and stick”waterproofing membrane. The membrane is appliedvertically to the wall from grade level down to andoverlapping the top of the footing. It is recommendedto use protection board (1/2 inch EPS or EXP foam sheetsor similar) to prevent damage to the waterproofingmembrane during backfilling.Free flow drainage material with a maximum fluid densityof 30 pcf (480 kg/m3) is recommended, i.e., sand or sand-NOTE: Membrane should be installed within one weekprior to backfill being placed. Sunlight and hightemperatures may cause the membrane to beginto “sag” which may cause wrinkles in the materialwhich may result in tears or punctures duringthe placement of the backfill material. Shouldyou choose to use one of the many other typesof waterproofing available be sure to followthe manufacturer’s recommended installationprocedures.STEP 1: Prep the wall and footing area to be covered byremoving dirt and debris.STEP 2: Snap chalk lines for the “grade” line.STEP 3: Measure the height from grade line to footing.Add enough length to cover the top of thefooting and cut pieces of membrane to length.www.logixicf.comBuild Anything BetterREPRINTED 20162–97 Rev. Sep 23/09I N S T A L L A T I O NG U I D Egravel mix.
2.18.10.1 – BELOW GRADEWATERPROOFING CONTINUED Also cut smaller 4” - 6” (102mm - 152mm) piecesto be applied as “corner caps”. This will providedouble ply protection in the corners.STEP 4: Apply the “corner cap” pieces on each corner first.STEP 5: Starting at a corner, line up the membrane soit is hanging vertically (using our vertical cutlines as a guide to keep membrane plumb). Pullback the first 8” - 10” (203mm - 254mm) of theG U I D Erelease paper and press the membrane to thewall. Continue pulling back the release paper andpressing membrane to the wall.I N S T A L L A T I O NSTEP 6: Continue applying cut pieces of membranearound the wall, maintaining 2 inch (51 mm)overlap by using the printed marks on themembrane as a guide.NOTE: Extreme temperatures, both cold and hot,may cause the installer to consider othertypes of waterproofing. Be sure to follow themanufacturer’s installation process.www.logixicf.comBuild Anything BetterREPRINTED 20162–98 Rev. Sep 23/09
2.18.10.2 – ABOVE GRADE PARGINGThe area that is above grade line and below the exteriorsiding material must be parged to protect the EPS fromdamage.Parging is a coating material that is applied to give afinished appearance to the small area of wall that isabove grade level but below where the siding materialswill begin. Logix Prepcoat is the preferred option for thisdirt or debris. The wall may need to be “scuffed”to reveal fresh EPS beads.STEP 2: Mix Prepcoat dry material with water to a pastyconsistency.STEP 3: Using a trowel apply a thin, 1/16” - 1/8” (2mm 3mm) “skim coat” of Prepcoat.STEP 4: Pre-cut pieces of Logix fiber mesh 1” - 2” (25mm- 51mm) wider than the area to be parged. Thiswill allow for an over-lap over the waterproofingmembrane to create a “drip ledge”.STEP 5: Embed the mesh in the skim coat firmly.STEP 6: Once the area is dry to the touch apply a secondcoat of Prepcoat. This coat can be painted orstained if desired.www.logixicf.comBuild Anything BetterREPRINTED 20162–99 Rev. Sep 23/09I N S T A L L A T I O NSTEP 1: Prep the wall area to be covered by removing anyG U I D Earea.
2.18.11 – ATTACHING FIXTURESFor attaching fixtures Logix provides furring tabs spacedevery 8 inches, which provides more fastening points thanstud walls.Different methods are used to attach fixtures dependingon whether the fixture is light or heavy in weight.Furring tabsLIGHT WEIGHT FIXTURESFixtures that are light in weight, or are not subjected toheavy loads, such as small picture frames or mirrors, canG U I D Ebe attached to the wall without having to fasten into thefurring tabs by using typical hanging pins, finishing nailsor plugs.I N S T A L L A T I O NLight weight fixtures such as curtain rods, large pictureframes or mirrors, bathroom accessories, etc., require amore secure attachment to the wall.The Grappler, a product made specifically for ICFs,provides a stronger attachment for fixtures that arelight in weight but require a more secure hold. TheGrappler is also useful in areas where a stronger fasteningpoint is required in an area where furring tabs may beabsent. The Grappler is a 4” x 8” steel meshed platethat is pressed into the surface of the Logix form panelsbefore drywall is placed. Once the drywall is installedthe Grappler is sandwiched between the ICF and drywallcreating a much stronger and secure attachment area.www.logixicf.comBuild Anything BetterREPRINTED 20162–100 Rev. Jul 18/13
2.18.11 – ATTACHING FIXTURES CONTINUEDHEAVY WEIGHT FIXTURESAdditional backing is recommended to support heavierwall fixtures, such as kitchen cabinetry, wall mountedfixtures, grab bars, hand rails, etc.Different attachment methods can be employeddepending on the type of attachment.CabinetsMethod 1: Plywood board can be attached to theplace of gypsum board, providing a thermalbarrier comparable to gypsum and a strongattachment surface for heavier items andfixtures. Be certain to attach the plywoodboard to the Logix webs with a sufficientnumber of screws to hold heavy items in placefor when loads are applied.Method 2: Create horizontal channels behind thecabinets equal in width to a 2x4 and install2x4 backing directly to the concrete surfaceusing sufficiently long concrete screws and arotohammer. Attach the cabinets to the 2x4s.Grab BarsMethod 1: Before placing drywall, place the Grapplersonto Logix at grab bar fastening points. Installthe drywall and fasten the grab bar to theGrapplers.For full size CAD drawing seeSection 5, CAD Drawingswww.logixicf.comBuild Anything BetterREPRINTED 20162–101 Rev. Sep 23/09I N S T A L L A T I O NG U I D ELogix wall behind the heavier cabinets in
2.18.11 – ATTACHING FIXTURES CONTINUEDMethod 2: Use Tap Con screws to anchor the grab bardirectly to the concreted.Method 3: For a stronger hold remove the foam andreplace with wood blocking behind the grabbar mounting bracket. The wood blockingshould be mechanically fastened to theconcrete.TelevisionsG U I D EMethod 1: Face mounted TVs upto 200lbs can be securedto the furring tabs with a minimum of 4 coursethread screws. Care must be taken to ensurethe screws are properly fastened to the furringI N S T A L L A T I O Ntabes. Fastening to Grapplers in combinationwith furring tabs will also work.Method 2: Replace the drywall behind the mountingbracket with plywood extending the fullheight of the mounting bracket and coveringat least 3 furring tabs in length. Fasten theplywood with sufficient number of screws tothe furring tabs. Conceal the plywood withdrywall compound to blend with the drywalland attach the mounting bracket to theplywood.TV mounts that swivel causes heavier loading conditionsand should be anchored to the concrete with plywoodand tapcons.www.logixicf.comBuild Anything BetterREPRINTED 20162–102 Rev. Sep 23/09
2.18.12 – HOLDING POWER OF SCREWSFASTENED TO Logix FURRINGTABSWeb fastener withdrawal and shear testing using course and fine thread drywall screws.Tests were conducted on furring tabs embedded 1/2 inch (52 mm) from the surface of the2.75 inch (70 mm) Logix EPS panels .Max. stance1Max. AverageShearResistanceAllowable ShearResistance2Coarse ThreadDrywall Screw166lb (75.3kg)33lb (15.0kg)367lb (166.5kg)49lb (22.2kg)Fine Thread DrywallScrew169lb (76.7kg)34lb (15.4kg)328lb (148.8kg)49lb (22.2kg)NOTE: The numbers in this table represent resistance at failure. Good building practicemandates a minimum of a 5 to 1 safety factor in calculating fastener loading. Forcomplete test results on additional fasteners, see Section 8 in the Logix Design Manualor consult your local Logix representative.www.logixicf.comBuild Anything BetterREPRINTED 20162–103 Rev. Nov 11/10I N S T A L L A T I O NG U I D E1kg 9.81 Newtons1. Allowable withdrawal resistance values are based on a factor of safety of 5.2. Allowable shear resistance values are based on a factor of safety of 3.2 within defined deflection limits (for more detailedinformation contact info@Logixicf.com)
INSTALLATION GUIDE. wwwlgii. 2-93. Rev Build Anything Better. 2.18.6 - EIFS. There are now acrylic-based stucco products available that . are more flexible and easier to work with than traditional cement-based stucco. Collectively these products are known as EIFS (Exterior Insulation Finish Systems) and almost always require an EPS .