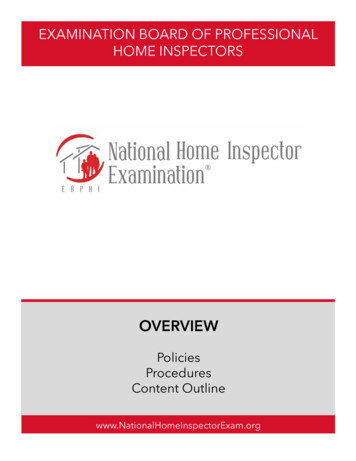
Transcription
EXAMINATION BOARD OF PROFESSIONALHOME INSPECTORSOVERVIEWPoliciesProceduresContent Outlinewww.NationalHomeInspectorExam.org
Examination Board of Professional Home Inspectors , Inc.The Examination Board of Professional Home Inspectors (EBPHI) is an independent, not-for-profit corporation foundedin 1999. EBPHI’s mission is “to establish the standard of competence for home inspectors and to enhance consumerconfidence in home inspection professionals.” The National Home Inspector Examination (NHIE) addresses this missionby encouraging regulatory bodies in state and local governments, as well as professional membership organizations, toadopt the National Home Inspector Examination for competency assessment.Administration of the NHIE ensures that home inspection professionals meet basic knowledge and practice requirementsfor the purposes of regulation. Successful completion of the examination fulfills the needs of the public, the governmentand of home inspectors.POLICIES AND PROCEDURESRegistration InformationPayment InformationThe states of Tennessee and Oklahoma have contractedwith PSI, Inc. to administer the National Home InspectorExamination. Tennessee and Oklahoma:Illinois, South Dakota and Washington:The states of Illinois, South Dakota and Washington haveelected to add state-specific questions to the National HomeInspector Examination. The National Home InspectorExamination in Illinois, South Dakota and Washington isadministered by Applied Measurement Professionals (AMP).Florida: Examination Fee The state of Florida has elected to add state-specificquestions to the National Home Inspector Examination.The National Home Inspector Examination in Florida isadministered by PearsonVUE.Texas and Nevada:The states of Texas and Nevada have contracted withPearsonVUE to administer the National HomeInspector Examination.All Other States:EBPHI contracts with PSI, Inc. to administer the NationalHome Inspector Examination at more than 220 proctoredtest centers throughout North America.The cost of the National Home InspectorExamination is 225 per test in most states and 325in Canada. Please confirm when you call the testingcenter to register.Veterans Reimbursement: If you pass the NHIE andyou are eligible for GI Bill education benefits youmay be eligible to get reimbursed for the cost of thisexam. You will need to complete a VBA-22-0803ARE and submit it to the VA for reimbursement.When you submit the VBA-22-0803-ARE make sureyou remember to include a copy of your receipt ofpaid in full for this exam, and a copy of your examresults. For questions please contact the Departmentof Veterans Affairs.To Change or Cancel a ReservationWithout Penalty 2Payment is required at the time of online or phoneregistrations.Payments are NOT accepted at the testing centers.Examination fees are nonrefundable, nontransferableand subject to change.To change or cancel a reservation without a monetarypenalty, notify the test administrator’s Customer CareCenter no less than four business days before thescheduled examination.Cancellations received less than four business daysbefore the scheduled examination will be charged thefull examination fee.2019 Examination Board of Professional Home Inspectors
If you are absent for a scheduled examination andhave not rescheduled or cancelled according to policy,the full examination fee for the missed examinationsession is due. You will not be permitted to takesubsequent examinations until all fees owed to PSI,Inc. for previous examinations have been paid.If you are taking the exam through a different testadministrator, contact them (See “RegistrationInformation” section) for their policies and procedures. Permitted Absence from aScheduled ExaminationIf you are unable to attend the examination on the day youare scheduled to test, you may be excused for the followingreasons: Illness of either yourself or an immediate familymember Death in your immediate family Disabling traffic accident Court appearance or jury duty Military dutyRe-examination Procedures To make an appointment for re-examination,follow the online or telephone procedures outlinedpreviously for making an examination appointment.You may retake the National Home InspectorExamination as many times as you wish (unlessotherwise regulated by your state). However, youmust wait 30 days between retakes. Each examinationrequires a separate fee.Special Examination Arrangementsand Services EBPHI certifies that its test administrators complywith the provisions of the Americans with DisabilitiesAct (42 USCG Section 12101, et. seq.) and TitleVII of the Civil Rights Act, as amended (42 U.S.C.2000e, et. seq.) in accommodating individuals who,because of a disability, need special arrangements toenable them to take the examination. If you needspecial arrangements for testing because of a disablingcondition, you may ask for special testing services. Allexamination sites provide access for individuals withmovement disabilities.Any individual requesting special testing arrangementsdue to impaired sensory, manual, or verbal skillsor other disability must submit a request to theappropriate test administrator. This request must include your name, address, social security number,test date desired, test location, time of examinationand a description of the special requirements. Thisrequest must also include supporting documentationfrom a physician or other qualified professionalreflecting a diagnosis of the condition and anexplanation of the need for test aids or modifications.Test administrators will provide auxiliary aids andservices except where it may fundamentally alter theexamination or results or result in an undue burden.Due to the unique nature of each request for specialarrangements and the types of variables involved withtesting (testing frequencies as permitted by each stateand individual test center capabilities), an individualrequesting special services should do so in advance.Test administrators will determine the time and placeof specially arranged examinations and confirm thesearrangements with the individuals directly. All specialexamination arrangements are subject to ExaminationBoard of Professional Home Inspectors’ policies.Reporting TimeSpecific reporting times will be given when you make yourexamination reservation. It is suggested that you reportfor testing at least 15 minutes before your examinationappointment. Allow additional time to find the test center.TardinessIndividuals who arrive late for their scheduled examinationforfeit their reservation. Persons excluded from testingbecause of lateness will be considered absent and will owethe test administrator the full examination fee.At the Testing Center When you arrive at the test center, report to the testcenter manager. Present your confirmation number,identification and any other required documents. Themanager will request information from you and takeyour picture. This photograph will be printed on yourscore report.The test center manager will assign you a seat andassist you with your computerized testing unit. Youwill have an opportunity to go through a tutorial tobecome familiar with the system. The time you spendon the tutorial will not reduce the time allotted fortaking your examination. When you feel comfortable,you may begin your examination.You are given four hours to complete the NationalHome Inspector Examination. The timing of thePolicies, Procedures, Content3
examination begins the moment you look at the firstquestion on your exam. After four hours have elapsed,the testing unit will automatically turn off. Alert thetest center manager when you have completed yourtest by raising your hand.If you encounter any problem during the exam, pleasenotify the test center manager immediately. If yourproblem is not addressed to your satisfaction, contactEBPHI by email at info@homeinspectionexam.org.Examination Comments Should you wish to comment on any question onthe exam, be sure to flag it and then follow theinstructions at the end of the test. Comments areaccepted only for specific, individual questions; afailing score on the NHIE is not considered groundsfor comment.Comments on questions on the National HomeInspector Examination are reviewed by theExamination Board of Professional Home Inspectorswith advice from its test development contractor.Should a question require modification or eliminationsuch that failing scores might be changed, affectedcandidates will be rescored. In no case will resolutionof candidate comments result in modification ofindividual candidate scores. Comment determinationsthat do not affect passing scores will not be applied, butmay affect future versions of the exam.Test Center RegulationsTo ensure that all individuals are tested under equallyfavorable conditions, the following regulations andprocedures are observed at each test center: No personal belongings such as briefcases, large bags,study materials, extra books or papers, electronicpagers or cell phones are permitted in the testingroom. Any items brought into the testing room willbe collected and returned after the test is completed.Test administrators are not responsible for lost ormisplaced items. No one is permitted to eat, drink, or smoke duringthe examination. Under no circumstances will you be permitted towork beyond the time allotted for the examination.Time limits are generous, with ample time to answerall questions and to check all work. You may not leave the room during an examinationwithout permission from the test center manager. Ifyou need to leave the examination for any reason, noextra time will be allowed for the examination.4 Examinees using any type of format to copy orphotograph some or any part of the questions or answers,using notes, books or other aids, taking part in an act ofimpersonation, or removing test materials or notes fromthe testing room will be summarily dismissed from theexamination and reported to the Examination Boardof Professional Home Inspectors and/or their respectiveregulatory agency and may be subject to penalties.The use of calculators is not permitted.Test center personnel are not familiar with thequestions on the NHIE and have been instructed notto attempt to assist with the tested material.Cancellations and DelaysTest administrations are delayed or cancelled only inemergencies. If severe weather or a natural disastermakes the test center inaccessible or unsafe, the testadministration may be cancelled. Listen to your local radiostations for announcements and information regardingsevere weather conditions that may result in test delaysand/or cancellations.How the Test Is ScoredThe National Home Inspector Examination is “scalescored” from 200-800, with 500 as the passing score. Yourpass/fail status is determined by whether you answeredenough questions correctly to meet or to exceed the passingscore of the examination. This passing score is establishedby the methodology suggested in accepted standards forpublic protection examinations.Using Your Score ReportIf you took this examination to qualify for licensing orother regulation in your state, contact the regulatingagency to determine how to submit your passing scorereport. You will find links to various regulatory bodies atwww.nationalhomeinspectorexam.org.At PSI, Inc. test centers, you will receive an original copyof your score report prior to your departure. If you aretaking the exam through a different test administrator,contact them for information.Upon passing the NHIE you are also able to add yourcredentials to our Home Inspector Database located on ourwebsite. When you submit your name to be entered to ourInspector Database you will also receive a communicationstoolkit to promote your achievement! Submit yourinformation at tabase.2019 Examination Board of Professional Home Inspectors
CONTENT OUTLINEThis content outline based on the role delineation study, it is intended to provide candidates with topics for study that mayappear on the National Home Inspector Examination. The percentage of questions on the examination for each content area isindicated below. The contents of this document are neither a complete listing of all topics covered by the examination nor allskills necessary to perform a competent inspection.DOMAIN 1: PROPERTY AND BUILDING INSPECTION/SITE REVIEW (63%)TASK 1: Identify and inspect site conditions toassess defects and issues that may affect peopleor the performance of the building. (5%)A. Vegetation, Grade, Drainage and RetainingWallsi.ii.Common types, materials and terminologyApplicable standards, installation methods andclearanceiii. Typical defects (e.g., negative grade, earth to woodcontact, overgrown vegetation, missing drainage/drains)iv. Common safety issuesTASK 2: Identify and inspect building exteriorcomponents to assess defects and issues that mayaffect people or the performance of the building.(5%)A. Wall Cladding, Flashing, Trim, Eaves,Soffits and Fasciai. Common types, materials and terminologyii. Applicable standards and installation methodsiii. Typical defects (e.g., missing sections, improperinstallation, water infiltration, decayB. Exterior Doors and Windowsi. Common types, materials and terminologyii. Applicable standards and installation methodsiii. Typical defects (e.g., decayed wood, missing flashings,cracked glass)iv. Common safety issues (e.g., safety glazing, sashsupport)B. Driveways, Patios and Walkwaysi. Common types, materials and terminologyii. Applicable standards and installation methodsiii. Typical defects (e.g., root damage, large cracks,improper slope)iv. Common safety issues (e.g., trip hazards, slipperysurface)C. Pool and Spa Access Barriersi.ii.Applicable safety standards and terminologyCommon safety issues (e.g., fencing, latches, alarms)C. Decks, Balconies, Stoops, Stairs, Steps,Porches and Applicable Railingsi. Common types, materials and terminologyii. Applicable standards and installation methodsiii. Typical defects (e.g., improper deck ledgerattachment, improper rail or stair construction,missing flashing)iv. Common safety issues (e. g., loose handrails andguards, handrails not graspable, uneven riser height)D. Garage Vehicle Doors and Operatorsi.ii.iii.iv.Common types, materials and terminologyApplicable standards and installation methodsTypical defects (e.g., damaged rollers, broken springs)Common safety issues (e.g., missing/failing/malfunctioning safety sensors, improper adjustmentof pressure reverse)Policies, Procedures, Content5
TASK 3: Identify and inspect roof components toassess defects and issues that may affect peopleor the performance of the building. (6%)A. Roof Coveringsi.ii.iii.iv.Common types, materials and terminologyApplicable standards and installation methodsTypical repair methods and materialsTypical defects (e.g., improper installation, cracking,damage, decay)v. Characteristics of different roofing materialsvi. Sheathing and underlayment requirements fordifferent types of roof coveringsC. Roof Flashingsi. Common types, materials and terminologyii. Applicable standards and installation methodsiii. Typical defects (e.g., separation, improper installation,missing flashing)D. Skylights and Other Roof Penetrationsi. Common types, materials and terminologyii. Applicable standards and installation methodsiii. Typical defects (e.g., leakage, improper installation,deteriorated boot)B. Roof Drainage Systemsi. Common types, materials and terminologyii. Applicable standards and installation methodsiii. Typical defects (e.g., ponding, improper slopes,clogging/leaking)TASK 4: Identify and inspect structuralcomponents to assess defects and issues that mayaffect people or the performance of the building.(4%)A. Foundationi. Common types, materials and terminologyii. Applicable standards and installation methodsiii. Typical modifications, repairs, upgrades and retrofitmethods and materialsiv. Typical defects (e.g., cracks, settlement) and theircommon causes and effectsv. Soil types and conditions and how they affectfoundationsvi. Applied forces and how they affect foundation systems(e.g., wind, seismic, loads)vii. Water management (e.g., waterproofing, foundationdrains)B. Floor Structurei. Common types, materials and terminologyii. Applicable standards and installation methodsiii. Typical modifications, repairs, upgrades and retrofitmethods and materialsiv. Typical defects (e.g., improper cuts and notches instructural members, decayed or damaged structuralmembers)6v.Applied forces and how they affect floor systems (e.g.,wind, seismic, loads)C. Walls and Vertical Support Structuresi. Common types, materials and terminologyii. Applicable standards and installation methodsiii. Typical modifications, repairs, upgrades and retrofitmethods and materialiv. Typical defects (e.g., decayed or damaged structuralmembers, earth to wood contact, structuraldeformation)v. Seismic and wind-resistant construction methods andhardwareD. Roof and Ceiling Structuresi. Common types, materials and terminologyii. Applicable standards and installation methodsiii. Typical modifications, repairs, upgrades and retrofitmethods and materialsiv. Typical defects (e.g., moisture stains, sagging rafters,modified/damaged trusses)v. Applied forces and how they affect roof/ceilingstructures (e.g., wind, seismic, loads)2019 Examination Board of Professional Home Inspectors
TASK 5: Identify and inspect electrical systems toassess defects and issues that may affect peopleor the performance of the building. (6%)A. Electrical Service: Service Lateral, ServiceDrop, Service Entrance, Service Equipmentand Service Groundingi. Common types, materials and terminologyii. Applicable standards and installation methodsiii. Typical modifications, repairs, upgrades and retrofitmethods and materialsiv. Typical defects (e.g., height, deteriorated conductorsheathing)v. Electrical service amperagevi. Service grounding and bondingvii. Alternative energiesviii. Common safety issues (e.g., exposed conductors,improper cover fasteners, missing dead front cover)B. Interior Components of Service Panels andSubpanelsi.i.ii.iii.iv.v.vi.vii.viii.ix.Common types, materials and terminologyApplicable standards and installation methodsTypical modifications, repairs, upgrades and retrofitmethods and materialsTypical defects (e.g., double-tapping, over-fusing)Panel grounding and bondingPanel wiringTheory of operation and purpose of over-currentprotection devices (e.g., circuit breakers and fuses,GFCI, AFCI)Inspection safety proceduresKnown problem electrical panel boards (e.g., FederalPacific/Stab-Lok)Common safety issues (e.g. open knock outs,discoloration at conductor connections, multipleneutrals under one screw)TASK 6: Identify and inspect cooling systems toassess defects and issues that may affect peopleor the performance of the building. (4%)A. Coolingi. Common types, materials and terminologyii. Applicable standards and installation methodsiii. Typical defects (e.g., suction line insulation missing,condensation and/or rust on components, restrictionof air flow at the condensing unit)C. Wiring Methodsi.Common types (e.g., non-metallic sheathed cable,conduit), materials and terminologyii. Applicable standards and installation methodsiii. Typical modifications, repairs, upgrades and retrofitmethods and materialsiv. Typical defects (e.g., improper use of or lack ofjunction boxes, unprotected non-metallic sheathedcable, lack of proper support)v. Concerns and considerations about solid-conductoraluminum wiringvi. Obsolete electrical wiring system (e.g., knob and tubewiring, cloth-covered NM cable)vii. Common safety issues (e.g., open splices, no cableclamps at penetrations, exposed conductors)D. Devices, Equipment and Fixtures (e.g.,switches, receptacles, lights, fans)i. Common types, materials and terminology.ii. Applicable standards and installation methodsiii. Typical modifications, repairs, upgrades and retrofitmethods and materialsiv. Typical defects (e.g., reverse polarity, open equipmentgrounds, non-functional GFCI or AFCI protection)v. Equipment groundingvi. Wiring, operation and location of typical devices andequipment (e.g., receptacles and lights, appliances,ground fault circuit interrupter protection, arc faultcircuit interrupter protection)vii. Common safety issues (e.g., absence of GFCI)E. Alternative Energy Systemsi.Common types, materials and terminology (e.g., solar,wind)ii. Applicable standards and installation methodsiii. Disconnect locationiv. Common safety issues (e.g., improper connection toother systems, lack of disconnect method)iv.Theory of refrigerant cycle (e.g., latent and sensibleheat, air conditioning, heat pumps)v. Testing methodsvi. Condensate control and disposalvii. Alternative energiesB. Distribution Systemsi. Common types, materials and terminologyii. Applicable standards and installation methodsiii. Typical defects (e.g., damaged or disconnected ducts,incorrect installation)Policies, Procedures, Content7
TASK 7: Identify and inspect heating systems toassess defects and issues that may affect peopleor the performance of the building. (5%)A. Heatingi.ii.iii.iv.v.vi.vii.Common types, materials and terminologyApplicable standards and installation methodsTypical defects (e.g., dirty fan, misfiring oil burner)Theory of heating system operationTesting methodsCondensate control and disposalBy-products of combustion (e.g., H2O, CO2, CO,NO2), their generation and how and when theybecome a safety hazardviii. Common safety issuesix. Alternative energiesTASK 8: Identify and inspect insulation, moisturemanagement systems and ventilation systems inconditioned and unconditioned spaces to assess defectsand issues that may affect people or the performance of thebuilding. (4%)A. Thermal Insulationi. Common types, materials and terminologyii. Applicable standards and installation methodsiii. Typical defects (e.g., missing, uneven, or damagedinsulation, flame spread concerns, improperclearances)iv. Theory of heat transfer and energy conservationv. Recommended insulation levels (e.g., R-value)vi. Common safety issues (e.g., fire hazards)8B. Distribution Systemsi. Common types, materials and terminologyii. Applicable standards and installation methodsiii. Typical defects (e.g., damaged or disconnected ducts;clogged, missing or damaged filters; leaking pipes)C. Vent Systemsi. Common types, materials and terminologyii. Applicable standards and installation methodsiii. Typical defects (e.g., separated vent, back drafting,clearance to combustible materials)iv. Theory of vent system operationv. Common safety issuesB. Moisture Managementi. Common types, materials and terminologyii. Applicable standards and installation methodsiii. Typical defects (e.g., improper vapor retarderinstallation)iv. Theory of moisture generation, relative humidity andmoisture movement in buildingsv. Effects of moisture on building components,occupants and indoor air qualityvi. Moisture control systems (e.g., humidifiers/dehumidifiers, vapor retarders)C. Ventilation Systems of Attics, Crawl Spacesand Roof Assembliesi.ii.iii.iv.Common types, materials and terminologyApplicable standards and installation methodsTypical defectsTheory of air movement in building assemblies (e.g.,stack effect, pressure differences)v. Closed attics and crawl spacesvi. Screening, sizing and location requirements forventilation openings2019 Examination Board of Professional Home Inspectors
TASK 9: Identify and inspect mechanical exhaustsystems to assess defects and issues that mayaffect people or the performance of the building.(5%)A. Mechanical Exhaust Systems (e.g., bath,kitchen, dryer)i.i.ii.Common types, materials and terminologyApplicable standards and installation methodsTypical modification, repair, upgrade and retrofitmethods and materialsiii. Typical defects (e.g., improper termination, plasticdryer ducts)TASK 10: Identify and inspect plumbing systemsto assess defects and issues that may affectpeople or the performance of the building. (5%)A. Water Supply Distribution Systemi. Common types, materials and terminologyii. Applicable standards and installation methodsiii. Typical modification, repair, upgrade and retrofitmethods and materialsiv. Typical defects (e.g., cross-connection, back flow,dissimilar metals)v. Common water pressure/functional flow problemsand how they affect the water distribution system(e.g., hard water build-up, old galvanized piping,pressure reducer valves)B. Fixtures and Faucetsi. Common types, materials and terminologyii. Applicable standards and installation methodsiii. Typical modification, repair, upgrade and retrofitmethods and materialsiv. Typical defects (e.g., leaks, fixture attachmentv. Common safety issues (e.g., absence of anti-scaldvalve, hot/cold reverse)C. Drain, Waste and Vent Systemsi.ii.Common types, materials and terminologyApplicable standards and installation methods (e.g.,supports/spacing)iii. Typical modification, repair, upgrade and retrofitmethods and materials (e.g., joining dissimilar pipingmaterials)iv. Theory and usage of traps and ventsiv.v.Relationship between mechanical systems andventilation systemsCommon safety issues (e.g., fire hazards)B. Indoor Air Management Systems (e.g.,heat recovery ventilators)i. Common types, materials and terminologyii. Applicable standards and installation methodsiii. Typical modification, repair, upgrade and retrofitmethods and materialsiv. Typical defects (e.g., inoperative, no bypass ducting)v.Identification of public or private disposal (whenpossible)vi. Typical defects (e.g., flex pipe, deterioration, leakage,venting or drain slope)D. Water Heating Systemsi.ii.Common types, materials and terminologyApplicable standards and installation methods (e.g.,storage tank, tankless)iii. Typical defects (e.g., vent/flue issues, fuel connectionand temperature pressure relief system defects)iv. Accessory items (e.g., seismic restraints, expansiontanks, recirculation systems)v. Connections to and controls for energy sourcevi. Combustion air requirementsvii. Common safety issues (e.g., no temperature pressurerelief valve, missing or improperly connected vents)E. Fuel Storage and Fuel Distribution Systemsi.i.ii.Common types, materials and terminologyApplicable standards and installation methodsTypical defects (e.g., missing piping supports, missingshut-off, leaking storage tank)iii. Common safety issuesF. Drainage Systems, Sump Pumps, SewageEjection Pumps, Related Valves and Pipingi. Common types, materials and terminologyii. Applicable standards and installation methodsiii. Typical defects (e.g., inoperative sump pump,improperly installed system, broken lid)iv. Pump and discharge locationsPolicies, Procedures, Content9
TASK 11: Identify and inspect interior componentsto assess defects and issues that may affect peopleor the performance of the building. (4%)A. Walls, Ceiling, Floors, Doors and Windowsand Other Interior System Componentsi. Common types, materials and terminologyii. Applicable standards and installation methodsiii. Typical defects in interior surfaces caused by defects inother systems (e.g., structural movement, moisture stains)iv. Typical defects in interior surfaces NOT caused byother systems (e.g., defective operation of doors andwindows, damage, absence of safety glazing)v. Egress requirements (e.g., window security bar release,basement windows, sill height)vi. Applicable fire/safety and occupancy separationrequirements (e.g., fire walls, fire rated doors andpenetrations)vii. Smoke alarms and carbon monoxide alarmsTASK 12: Identify and inspect fireplaces, fuelburning appliances and their chimney and ventsystems to assess defects and issues that may affectpeople or the performance of the building. (6%)A. Solid fuel-burning (wood, pellet, coal)fireplaces and appliancesi.ii.iii.iv.v.vi.vii.viii.ix.10Common types, materials (manufactured, masonry)and terminologyCommon solid fuel chimney, vent connector, venttypes, materials and terminologyCommon masonry fireplace types, masonry flues,materials, applications, terminology and installationmethodsMasonry chimney foundation, height, clearancerequirements and terminations (e.g., clearances tocombustible materials)Applicable standards and installation methodsFuel types, combustion characteristics andcombustion air requirementsTypical defects (e.g., hearth defects, clearancerequirements, smoke chamber and flue issues)Operation of equipment, components and accessoriesCommon safety issues (e.g., creosote buildup, lack ofspark arrestors)B. Steps, Stairways, Landings and Railingsi. Common types, materials and terminologyii. Applicable standards and installation methodsiii. Typical defects (e.g., improper riser height and treaddepth, baluster spacing, loose guards)iv. Common safety issues (e.g., loose treads, missinghandrails)C. Installed Countertops and Cabinetsi.ii.iii.iv.Common types, materials and terminologyApplicable standards and installation methodsTypical defects (e.g., damaged components)Common safety issues (e.g., improperly securedcabinets and countertops)D. Smart Homesi.Emerging smart home technologies, applications,terminology and operationB. Gas and liquid fuel-burning (natural gas,propane) fireplaces and appliancesi.ii.iii.iv.v.vi.vii.viii.ix.Common types, materials (vented, direct vent,unvented) and terminologyCommon gas and liquid fuel chimneys, ventconnectors, vent types, materials and terminologyCommon masonry and manufactured fireplacetypes, flues, materials, applications, terminology andinstallation methodsChimney foundation, height, clearance requirements andterminations (e.g., clearances to combustible materials)Applicable standards and installation methodsFuel types, combustion characteristics andcombustion air requirementsTypical defects (e.g., hearth defects, clearancerequirements, smoke chamber and flue issues)Operation of equipment, components and accessoriesCommon safety issuesTASK 13: Identify and
Examination Board of Professional Home Inspectors , Inc. The Examination Board of Professional Home Inspectors (EBPHI) is an independent, not-for-profit corporation founded in 1999. EBPHI's mission is "to establish the standard of competence for home inspectors and to enhance consumer confidence in home inspection professionals."