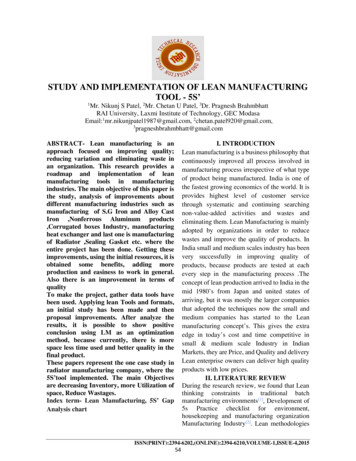
Transcription
STUDY AND IMPLEMENTATION OF LEAN MANUFACTURINGTOOL - 5S’1Mr. Nikunj S Patel, 2Mr. Chetan U Patel, 3Dr. Pragnesh BrahmbhattRAI University, Laxmi Institute of Technology, GEC ModasaEmail:1mr.nikunjpatel1987@gmail.com, il.comABSTRACT- Lean manufacturing is anapproach focused on improving quality;reducing variation and eliminating waste inan organization. This research provides aroadmap and implementation of leanmanufacturing tools in manufacturingindustries. The main objective of this paper isthe study, analysis of improvements aboutdifferent manufacturing industries such asmanufacturing of S.G Iron and Alloy CastIron ,Nonferrous Aluminum products,Corrugated boxes Industry, manufacturingheat exchanger and last one is manufacturingof Radiator ,Sealing Gasket etc. where theentire project has been done. Getting theseimprovements, using the initial resources, it isobtained some benefits, adding moreproduction and easiness to work in general.Also there is an improvement in terms ofqualityTo make the project, gather data tools havebeen used. Applying lean Tools and formats,an initial study has been made and thenproposal improvements. After analyze theresults, it is possible to show positiveconclusion using LM as an optimizationmethod, because currently, there is morespace less time used and better quality in thefinal product.These papers represent the one case study inradiator manufacturing company, where the5S’tool implemented. The main Objectivesare decreasing Inventory, more Utilization ofspace, Reduce Wastages.Index term- Lean Manufacturing, 5S’ GapAnalysis chartI. INTRODUCTIONLean manufacturing is a business philosophy thatcontinuously improved all process involved inmanufacturing process irrespective of what typeof product being manufactured. India is one ofthe fastest growing economics of the world. It isprovides highest level of customer servicethrough systematic and continuing searchingnon-value-added activities and wastes andeliminating them. Lean Manufacturing is mainlyadopted by organizations in order to reducewastes and improve the quality of products. InIndia small and medium scales industry has beenvery successfully in improving quality ofproducts, because products are tested at eachevery step in the manufacturing process .Theconcept of lean production arrived to India in themid 1980’s from Japan and united states ofarriving, but it was mostly the larger companiesthat adopted the techniques now the small andmedium companies has started to the Leanmanufacturing concept’s. This gives the extraedge in today’s cost and time competitive insmall & medium scale Industry in IndianMarkets, they are Price, and Quality and deliveryLean enterprise owners can deliver high qualityproducts with low prices.II. LITERATURE REVIEWDuring the research review, we found that Leanthinking constraints in traditional batchmanufacturing environments[1], Development of5s Practice checklist for environment,housekeeping and manufacturing organizationManufacturing Industry[2]. Lean 210,VOLUME-1,ISSUE-4,201554
INTERNATIONAL JOURNAL OF ADVANCES IN PRODUCTION AND MECHANICAL ENGINEERING nable foundries is often seen as a set oftools that reduce the total cost and improve thequality of manufactured products the leanmanagement is philosophy is one which targetswaste reduction in every facet of themanufacturing business. Metal casting industriesare actively involved to reduce the scraprejection and rework during the manufacturingprocess of the components. To achieve theseproduction concerns must follow the qualitycontrol procedures correctly and timelyimplementation of the lean manufacturing [4].The lean manufacturing of small industry couldImplementation the philosophy in own contendlean production concept successfully, aninvestigation in two middles sizes industries,India[10]. Value stream mapping techniqueinvolves flowcharting the steps, activitiesmaterial flows, communications and otherprocess elements that are involved with a processor transformation. In this respect, value streammapping helps an organization to identify thenon –value –adding elements in a targetedprocess. Different flow layouts are selected thatreduces the transport time [6], production leadtime and lower –in-process inventory [8]. Theproposedframeworkforleansigmaimplementation need to be validated in differentscenarios for establishing its validity[5] and theultimate goal of this system is to focus onachieving total communication efficiency thatuses Green and lean TQM system[7]. Leanmanufacturing philosophy asks for eliminationof wastes widen in the manufacturing system byfocusing on products value stream andeliminating non value adding activities throughcontinuous improvement [9]. An equipmentreplacement decision problem within the contextof lean manufacturing implementation. Inparticular, we demonstrate how the value streammapping suite of tools can be used to map thecurrent state map the current state of a productionline and design a desired future state. We providea roadmap for how VSM can provide necessaryinformation for analysis of equipmentreplacement Decision problem encountered inlean manufacturing [11].III. CONCLUSION FROM LITERATUREREVIEWSFrom the literature review, we conclude that inthe different direction, the various researchesdone on the lean manufacturing tools andtechniques but there are less number of companyaware about the LM tools and implementation ofthe same. So we implemented the 5s’ concept inthe company.IV. LEAN MANUFACTURING TOOLSAND TECHNIQUESThe core of Lean is based on the continuouspursuit of improving the processes, a philosophyof eliminating all non-value adding activities andreducing waste within an organization. TheValue adding activities are simply only thosethings the customer is willing to pay for,everything else is waste, and should beeliminated, simplified, reduced, or integrated.There are a number of Lean techniques availablesuch as, Value Stream Mapping, VisualWorkplace, Setup Reduction, Cellular/FlowManufacturing, Pull Systems and TotalProductive Maintenance just to name a few;however, it is absolutely essential that Lean isviewed from a total system perspective.Otherwise, either a company risks putting all ofits efforts into the wrong areas, and/or theimprovement process will come to a grindinghalt after the initial project.V. CASE STUDY1. COMPANY PROFILE: Name and Address:Banco Products(India) limitedBIL padara roadNear bhaili railway stationVadodara Product: Gasket, Oil Seal & Radiators Turn Over: 20 cr. Working people: 40 per 2 shift2. REASON FOR IMPLEMENTATIONGap analysis of the company, so we can get theclear idea about scope of work (Refer Tableno.1). It is found that many area scopes of 5s inthis company.3. IMPLEMENTATION OF 5SStep 1 –Sort Out –Remove all items from theworkplace that workplace that are not needed forcurrent 0,VOLUME-1,ISSUE-4,201555
INTERNATIONAL JOURNAL OF ADVANCES IN PRODUCTION AND MECHANICAL ENGINEERING (IJAPME)Figure 1: Improper arrangement of the parts (Jigs / Tooling)mm5S GAP ANALYSIS SHEETDATE: 1/12/2012COMPANY NAME: BANCO Products (India) LTD.SR NO234ITEMAre all notices and other information available in the Work area uptoDateIs unused equipment and machinery eliminated from the plantIs obsolete inventory and raw material eliminated from the plantAre doorways free from material and blockages5Are safety instructions and guide line display6Are all work area boundries clearly marked27Are storage places for all work in progress designated and marked28Are storage places for all tools and equipment properly maintainrecord29Are all machinary, storage euipment and colunms identified and labled10Are all pipes, controls, and gauges identified and labled311Is the plant free from trash and dirt3identification on finish goods are found butsemifinished and raw material are not foundat certain interval cleaning is done12Is the floor free from all foreign material3in production area increase freqency of cleaning1314Are machines clean and good repairAre sources of dust, dirt and foreigh material under control115Are oil analysis and other techniques used to gauge machine condition116Are cleaning and checking schedule available and in documented use11Are up to date work instructions, including quality checks availableand in use at all work station18Are all bins and parts properly identified and taggedAre gauages and indicator labled to clearly show the normal operating19range20Are all start up safety checks carried out and documented21Is everyone wearing proper safety shoes, glowes, safety glass22Are all unused tools and equipment properly stored23Are all raw materials and work in progress properly storedAre all personnel fully trained in the tasks they are responsible for,24and regularly testedIs there a regular auditing process to verify compliance with all25elements of the production and safety systemTOTALScoring Method0 'NO', where the only choise is '0' or'4', otherwise it means 'not at all'.1 some evidence of a plan but very little conformance2 about half the instances noted were in conformance3 instances note were mostly in conformance, but one or more problems were4 'yes'.where the only choise is '0',or'4',otherwise complete conformance with1701234COMMENTS2in testing and store area not identified222unused equipment parts are store in store area3safety instructions are given by Supervisor but notDisplayonly machinary record found and properly storageof tools but not keep record03cleaning schedule prapared but not followedregularlywork instruction are found but not displayed at allwork station1112232in store area some parts of unused equipmentproperly stored but not identified area2by external consultants ISO internal audit carriedout4545/10045%Implementation CriteriaScoreTarget of implementation daysif 20365-500if 20-40250-300if 40-70150-250if more than 70if more than 702Table 1: Gap Analysis Sheet of BANCO Products India E-1,ISSUE-4,201556
INTERNATIONAL JOURNAL OF ADVANCES IN PRODUCTION AND MECHANICAL ENGINEERING (IJAPME)Step-2 – Set In Order – Arrange needed itemsso that they are easy to find, use and put away.Before implementationAfter implementationFigure 2: Shows the status before and afterimplementation of 5SFigure 3: Right thing is in right placeSpatter removing after weldingBeforeAfterFigure 4: Implementation status before &after of 5S within 2 monthsStep 3: (Clean Lines) shine every things,everything is dust free (clean and safe workplan)Neat & clean gang ways painted floorNo leakage of oil on the material &shopfloorFigure 5: Shows the Status after 5 MonthImplementation of the Shop FloorShop floors shine everything Dust freeenvironmentFigure 6: Shows the Status after 5 MonthImplementation of the Shop FloorStep 4- StandardizationWork station layout, work Area layout, andwork in processAir LineLiquid/ Lubrication LineFigure 7: Implementation of the color codingIn sustains the benefits achieved byimplementing 1s, 2s & 3s.avoids Reoccurrence, in all the process continuity 1,ISSUE-4,201557
INTERNATIONAL JOURNAL OF ADVANCES IN PRODUCTION AND MECHANICAL ENGINEERING (IJAPME)work and also provides guidelines for the newpeopleSTEP 5–SELF–DISCIPLINE (follow thestandards)Figure 8: Whatever has been decided mustbe followed exactly as per h10%40%2 Hrs1 ch3time ofgoodsTable 2: 5S Result of case studyVI. CONCLUSIONAccording to case study, we conclude that leantools can be used effectively in any kind ofsectors as it is a world class manufacturingtool. The prime objective is to carry outprocess activity mapping for waste reduction.In this study bottleneck product was identified.Further value stream analysis tool wasemployed for identification of wastes in aprocess. The significance of each type of theerror was studied and waste ranking wascarried out. Current state map is plotted to4. sustainable foundries’, China foundryVol.8 No.1assess current status, waste eliminationtechniques are presented and future state mapis also preferred for improvement. The resultof study shows 20% waste reduction in thearea of unnecessary inventory, transportationand waiting. A 5S and Value stream mappingtools can be effectively employed to reducewastes and ultimately improve the process.IV. FUTURE RESEARCHThere is an infinite number of ways ofimplement Lean Manufacturing in theseIndustries. In this project Value StreamMapping is done theoretically but in actualpractice it can be useful. Many industries arenot aware of these tools. RegardingImplementation of 5s it is popular at highermanagement level, but by referring this projectit will be popular in a worker also. By using 5sand Value Stream Mapping moral of workerscan be increased. But this is possible in futureby conducting training program of such type.V. ACKNOWLEDGEMENTAuthors of this paper thankfully acknowledgethe generous and continuous support ofBANCO PRODUCTS (INDIA) LTD.BARODA, Gujarat for giving an opportunityto do the work with them and also wishes toapologize for the unintentional exclusion ofmissing references and would appreciatereceiving comments and pointers to otherrelevant literature for a future update.VI. REFERENCES1. Oduoza, C.F. (2008). ‘Lean thinkingconstraintsintraditionalbatchmanufacturing environments’, AdvancesinproductionEngineering&management.2. N. Khamis, M.N.Ab Rahman, A.R.Ismail(2009). ‘Development of 5s Practicechecklist for Manufacturing Industry’,World congress on Engineering.3. R.M. Torielli ,R.A.abrahams , R.W.smillie. ‘Using lean methodologies foreco
5s Practice checklist for environment, housekeeping and manufacturing organization Manufacturing Industry[2]. Lean methodologies . INTERNATIONAL JOURNAL OF ADVANCES IN PRODUCTION AND MECHANICAL ENGINEERING (IJAPME) ISSUE-4,2015 55 for economically and environmentally sustainable foundries[3] is often seen as a