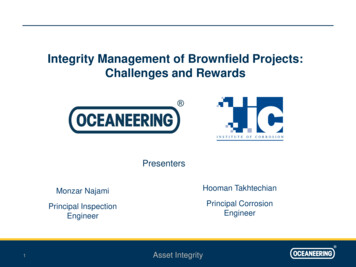
Transcription
Integrity Management of Brownfield Projects:Challenges and RewardsPresenters1Monzar NajamiHooman TakhtechianPrincipal InspectionEngineerPrincipal CorrosionEngineerAsset Integrity
Integrity Management of Brownfield Projects: Challenges and RewardsAgenda2 Introductions About Oceaneering Integrity Build : Definition and Objectives Brownfield RBA Overview Challenges of RBA Programmes Operational Elements and Influencing Factors Industry Best Practice - Process, Plant, People, Performance Conclusion and DiscussionAsset Integrity
About OceaneeringOceaneering provides services to deep water, space, Oil & Gas, andMotion entertainment environments to execute with new, leading-edgeconnections to solve tomorrow’s challenges, today.Founded in 1964 as an ROV/ Diving specialistOceaneering Acquisition of OIS in 2004 ( Asset Integrity )Branches in 5 continentsHas more than 8000 employees3
Worldwide Locations4
Inspection, Maintenance,and Repair (IMR)Asset IntegrityGrayloc ConnectorsVideo, Communications, andApplicationsDecommissioningInstallation ServicesDiving ServicesUmbilicalsInstallation WorkoverControl Systems (IWOCS)Subsea ConnectionsBOP InterventionROV ServicesIntervention ToolingSubsea ControlValvesDredging5Flow AssurancePipeline Repair
Integrity Management of Brownfield Projects: Challenges and RewardsAsset Integrity6Data ManagementRisk, Reliability, andMaintenanceDevelopment,management, andmaintenance ofcustomer andcompany softwaresystemsRisk assessments,critical analysisreliability studies,CMMS optimization,maintenance programs,spare parts analysisEngineering SolutionsSolutions for corrosion,structural, pipeline, andprocess plantrequirements includingasset life assessmentsSubsea EngineeringSolutionsFitness-for-serviceengineering andinspection,due diligence studies,inspection campaignmanagement, andpipeline engineering
Integrity Management of Brownfield Projects: Challenges and RewardsThe Aim of this Presentation is to :7 Share Best Practice for Operators/EPC/Vendors for a more efficient Integrity NewBuild (INB) programmes (Brownfield) Respond and adapt to Cost, efficiency, and Quality demands Lessons learnt/Best Practice in INB can benefit the existing operating facilities (e.g.Generic RBA / FM programmes) The Use of Technology (Recent Software RBA, CAD, IDB -Inspection Data Base)improves Governance & StandardizationAsset Integrity
Equipment Life Cycle FlowchartDesign & Offsite ManufactureSite ConstructionETP 32-10ETP 32-20I N T E G R I T YB U I L DScope DefinitionDesignAsset RecordsProcurement including offsitemanufactureSite Fabrication, Construction & TestingProceduresHandover / rcesIn-Service InspectionTrainingMaintenance, Repairs & ReplacementsAlterations, Re-rating & Life ExtensionRetirementETP 32-30 & ETP 32-40O P E R A T I O NCommissioningDecommissioningDismantling, Demolition & Disposal8Historical Data whereavailable e.g.- corrosion rates- suitable materials- inspection requirementsAsset Integrity
Integrity BuildIntegrity Build: Why is it required? Compliance & Standardization (Legislative Governance, such as safety Case, & RegionalRequirements) Ensure that integrity is designed into the project. To ensure safe and reliable operation of the facilities, by producing Inspection and Integrity plans,uploaded into the Maintenance Management System (MMS)Integrity Build: Deliverables? Front End Integrity Management Strategies include RBA, PSV, Vibration, Baseline, FHA (FlexibleHose Assembly), Inspection Dwgs, Structural, etc. (Desk Top related)Integrity Build RBA process, Inspection Plans, CUI register, PSV assessmentetc. (Site related activities): Programmes Baseline Inspection, Vibration, PSV, Dead Legs, etc.implementation during the Facilities Construction stage prior to commissioning Operation Related Strategies: FIMS, CMS, FM Strategy9
Governance & ComplianceIntegrity BuildOperator/Partners/RegionProject DeliverablesIntegrity Management SystemsProcess detailsCase for SafetyCMMS UploadUse ofTechnologyContinuousImprovementRisk Based AssessmentVibrationLocal Processes &Integrity SystemsPSVBaseline InspectionInspectionProgrammeProjectClose ntFabric MaintenanceEngineering DesignReview & RevampProjectDead LegStakeholderEngagementFront End IMSStrategiesLife CycleApproachPSV TestingProgrammeCorrosionManagementPHASE (A) PREPARE10Inspection JobPlans ( WSE)Sept 2016PHASE (B)DEVELOPPHASE (C & D) APPROVE DELIVERCommissioningIMS StrategiesIMS & Philosophy,Implementationstrategy
A Typical RBA process (Greenfield vs. Brownfield)Planning11Implementation
Brownfield RBA Process HighlightsCritical path data maturity & Quality for Brownfield revamp projectHistorical DataFormat /content/availability/QA /Revamp ProjectInspection reportsInspection Resultsinterpretation/ActionsExisting WSEFormat and ContentsFitness for DesignAssessment:Helpful and insightfulExisting MMS(SAP/Maximo etc)Comprehensive/RedundantBrownfield data InputCrucial for PoF evaluation12Relevant InsightsAsset Integrity
RBA Process for a typical Brownfield FacilityHigh level Criticality review as per-Location (Offshore/Onshore)-Unit/System criticality (Safety, Environmental, Business)-Process/Utility-Fluid corrosivity (Wet, Dry, Sour, .)-Material Selection (CS, CRA, Clad, Non-metal, .)-Threat complexity and barrier effectiveness-Inspection requirements / complexity-History of failure / Significant anomalies in the same or similar facilities13HighMediumLow Feed gas / Unstabilized HCcondensate Offshore unmanned platform Separation and Processing facilities Carbon steel material for wetsystem No barrier: Uncoated CRA Failure history in the same / similarfacilities. Requirement for baseline Intrusive inspection / Advance NIItechniques required Low critical utility (Air, Nitrogen,lube oil, fire water .) Low critical Vendor package(chemical injection, waste watertreatment, .) Non metals Passive barrier by design No major failure in the industry Only visual inspectionDehydrated HC, Export productUtility system (Boilers,Closed drainCritical vendor packageInlandBarrier effectiveness to bereviewed: Storage tank CP /Chemical injection Failure history in the industry No complex NDT / KnownCMLsAsset Integrity
Challenges in conducting a Brownfield RBAChallenges in the consequence assessment-Methodology (Quantitative/Qualitative)-Stakeholders engagement-Different scenarios-Various modes of failure-Availability of backup data-On time assessmentStakeholders Process safetyengineer Environmentalengineer Mechanicalengineer Operation andMaintenance14Failure modes Pin hole leakMedium sizeLarge sizeFull ruptureBackup data New / oldstudies HAZOP, FRA, ENVIIDAsset IntegrityMethodology Brainstormingsessions Software Manualcalculation Use of otherQRA doneTime Adequate timebefore RBAassessment
Challenges in conducting a Brownfield RBAChallenges in the data collection-Data availability-Data validation-Anomaly reports-Tagging-Monitoring recordsData Availability Materialcertificates Weldingprocedures Equipmentdrawings Datasheets Baseline data Inspectionreports .15Data validationAnomaliesTagging Traceability Gap analysis MOC (management ofchange) List ofanomalies NCRs / TQs Repair records Root causeFailure Analysis FFS ( fitness forservice) . Corrosion circuitmapping Insp. IsometricsCML taggingAsset IntegrityMonitoring Process dataCorrosion rateChemicalsDeposits/Corrosionproduct analysis
Challenges in conducting a Brownfield RBAChallenges in the Threat AssessmentHow much credit can we take from the existing data?Monitoringrecords Availability Reliability Validity due tochange in theprocess Samplinglocationsrelevant? .Corrosion ratesfrom Inspection Baseline dataavailable? Thicknessmeasurementtechnique Spot/Scan? MeasurementpointsMaterials Change inmaterial specand standard Coating type Manufacturingprocess Cladding/ weldoverlay .Anomalies Manufacturingdefects Root causeanalysisavailable?Risk assessment Participation ofoperation rep.In the RBAreview sessions Late lifescenariosSolution: Hybrid corrosion rate assessmentTheoretical estimated rate vs. Calculated rate based on actual data16Asset Integrity
Challenges in conducting a Brownfield RBATypical list of damage mechanisms considered in the pressure system RBADamage TypeInternal ThreatsExternal ThreatsAmine corrosionAtmospheric corrosionChloride pitting corrosionChloride pitting corrosionCO2 corrosionCorrosion under insulation / fireproofing (CUI / CUF)Corrosion by chemicals (including well workover fluids)Crevice corrosion (including flange faces)Crevice corrosion (including flange faces)Galvanic corrosionErosion, erosion-corrosion and solids-free flow-induced damageMarine corrosion (including external MIC and Splash Zone)Galvanic corrosionMechanical damage (abrasion, wear, galling and fretting)H2S (pitting) corrosionSoil corrosion (including external MIC)High temperature degradationStray current corrosionWastageMechanical damage (abrasion, wear, galling and fretting)Microbiologically Influenced Corrosion (MIC)Oxygen corrosionPreferential weld corrosion (PWC)Stray current corrosionCrackingAmine stress corrosion crackingCarbonate stress corrosion crackingChloride stress corrosion cracking (SCC)Chloride stress corrosion cracking (SCC)Fatigue (Corrosion)Fatigue (Corrosion and Mechanical)Hydrogen embrittlementHydrogen embrittlementHydrogen induced cracking (HIC) and Stress-oriented HIC (SOHIC)Liquid metal embrittlement (Hg)Sulphide stress cracking (SSC)17Asset Integrity
Challenges in conducting a Brownfield RBAChallenges in the Brownfield Deadleg Management-Deadleg identification-Deadleg risk assessment-Operational / Physical deadlegs-MitigationDeadlegidentification Isometricsavailable? Line walk carriedout? Deadleg tagging(old and newtags) .18Threat assessment Failure historiescaptured? Sampling fromdeposits /stagnant fluidsAsset IntegrityOperational /Physical deadlegs Change in theprocesscaptured? Isolated,mothballed,decommissioneditems .Mitigation in place Draining Flushing Chemicaltreatment Preservationphilosophy
Challenges in conducting a Brownfield RBAChallenges in the Brownfield CUI Management-Coating Spec. under insulation-Insulation type-Removal of unnecessary insulation-High critical location-Failure histories19CoatingRisk assessment Coating spec forthe temperature Old/New spec. . Failure historiescaptured? Insulation type Actual operatingtemperature .High criticallocationsMitigation inplace Cyclictemperature Branches damagedcladding? Line walk done? . Removal ofunnecessaryinsulation Availablescreening andNII techniques?Asset Integrity
Challenge of developing and implementing an asset integrityprogram during Brownfield development projectsSchedule andmilestones oftentake primacyover integritymanagementprocesses,20Risk for delay inemerging vitalintegrity relatedinterventionsTask conflictPlanningChallengesAsset IntegrityCost variancethroughout theprojectQA issuesduringimplementation– clear andcommonacceptancecriteria forexistinganomalies
Operational Elements and Influencing FactorsI N F L U E N C EOPSELEMENTSBESTPRACTICE21GOVERNANCEPLANT TATIONENGAGEMENTCOMPETENCYBEST PRACTICEBEST PRACTICEBEST PRACTICEBEST PRACTICEAsset Integrity
Best Practice-ProcessGOVERNANCESTANDARISATIONBEST PRACTICE22 Clear Governance and Compliance strategies (overseaselement) Timely Brownfield RBA scheduling : Post revamp project (Not too early and not too late )PLANT TCOMPETENCYBEST PRACTICEBEST PRACTICEBEST PRACTICE Generic Inspection Plans for Low Criticality levels Standard Inspection isometric – same process Semi quantitative RBA approach to equipment of same category Baseline Inspections: Define early & align with Project Plans Define and Engage with stakeholders early vendors /projectetc More scrutiny re Revamp project documentation and decisionmaking processes Ensure commensurate costing for Brownfield RBA FIMS & CMS Strategies to be developed and aligned with theRBA process Document Control : Extend the change processes outside ofthe organization to include Vendors ( Share documents)Asset Integrity
Best Practice-PlantPLANT STATUSGOVERNANCEDOCUMENTATION Preservation of existing equipment Plant specific: U/G Piping- CP- CUI- MIC-FM Acceptance Criteria during revamp project and repairs Permanently mothballed equipment/pipework FM Opportunities- Blasting on Live LinesBEST PRACTICE23MEASUREMENTENGAGEMENTCOMPETENCYBEST PRACTICEBEST PRACTICE Historical data Punch List items – and handover process As build P & ID and construction drawings In-situ verification of existing equipment ( 3D laser mapping)STANDARISATIONBEST PRACTICEORGANIZATION Boundary Definition ( Pipelines/ Utilities etc) Define process systems ( what is included) Pressure Systems - limits ( e.g. Tubing- vendor skids,auxiliaries etc) Interface documents -Elect/Inst/Pipeline/Vendors processes Vendor skids documentation and inclusion in baseline FM strategy applicable to Brown fieldAsset Integrity
Best Practice-PeopleORGANIZATIONGOVERNANCEPLANT STATUSENGAGEMENTSTANDARISATION24BEST PRACTICEMEASUREMENT Plant operators –Engage workforce-with local experience EPC/OPS/IMS/Operator – Communication protocols Use of Technology ( Docs sharing, comms, etc) Understand Company Culture and Human Element More Engagement with RBA workshopsDOCUMENTATIONCOMPETENCYBEST PRACTICEBEST PRACTICE Management Structure “Organogram” Roles & Responsibilities Outline interface processes Project Primacy pitfalls Stakeholder identification, engagement plan Establish effective communication -”Integrity Sale pitch” Human Factors Vs Process: Ownership, Inclusion, Work load,error traps, latent conditions, Competency, Training and Awareness Safety during Brownfield Revamp- “ e.g. beware of live lines” Integrity TA for revamp : Operation TeamAsset IntegrityBEST PRACTICE
Best Practice-PerformanceMEASUREMENTGOVERNANCEPLANT STATUSNORGANIZATIONENGAGEMENTSTANDARISATIONBEST PRACTICE25DOCUMENTATIONBEST PRACTICE Project KPI and periodic monitoring Peer Review Self Verification Process Integrity Reviews ad as built correctionsCOMPETENCYBEST PRACTICEBEST PRACTICEAsset Integrity Competency Reviews ( QA system) Technical Reporting Validity Use of technology/software / data management protocols Lack of experience of integrity inspection process(construction vs. Integrity) Forensic Inspections: Minimize /Manage Improve Inspection QA/Reporting/Recommendation ( errortraps) Identify and manage Critical Path risks at early stages of theproject
Integrity Management of Brownfield Projects: Challenges and RewardsConclusion and Discussion RBA Brownfield Facilities; It is an Acid Test for the Facilities Major opportunities ( FM Blasting on Live Lines/Temp Repairs/RO) Generic RBA’s for low risk items( Cuts cost and adds value) Project primacy : Risk Review By Operator Get in early – Design phase- before manufacturing start Implementation Baseline inspection to be part of Engineering Projects Team work and local Ops experience inclusion The Need of a rigorous selection process for Integrity Contractor Revamp Project: Reporting and recommendation ( QA issues)26Asset Integrity
Thank You for Your Attention!For more information please visit:www.oceaneering.com/asset-integrityOr contact:Monzar Najami (mnajami@oceaneering.com)Hooman Takhtechian (htakhtechian@oceaneering.com)27Asset Integrity
2 Asset Integrity Introductions About Oceaneering Integrity Build : Definition and Objectives Brownfield RBA Overview Challenges of RBA Programmes Operational Elements and Influencing Factors Industry Best Practice - Process, Plant, People, Performance Conclusion and Discussion Agenda Integrity Management of Brownfield Projects: Challenges and Rewards