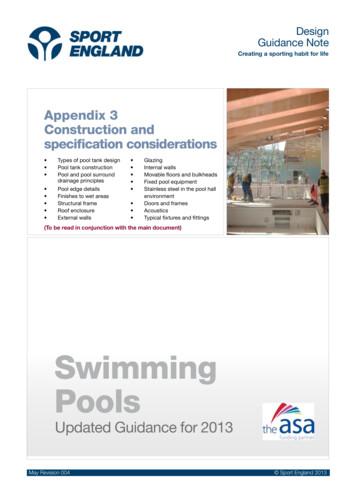
Transcription
DesignDesignGuidanceNoteGuidanceNoteSwimming PoolsCreating a sporting habit for lifeAppendix 3Construction andspecification considerations Types of pool tank designPool tank constructionPool and pool surrounddrainage principles Pool edge detailsFinishes to wet areasStructural frameRoof enclosureExternal walls GlazingInternal wallsMovable floors and bulkheadsFixed pool equipmentStainless steel in the pool hallenvironmentDoors and framesAcousticsTypical fixtures and fittings(To be read in conjunction with the main document)SwimmingPoolsUpdated Guidance for 2013NovemberMay Revision004 Revision 0041 Sport England2012 2013Sport England
Swimming PoolsDesignGuidance NoteConstruction and specification considerationsleakage does occur over the life of the pool tank orproblems identifying any leakage path for repair.The need to pay particular attention to the detailedconstruction and specification for swimming poolscan scarcely be overstated. The building mustwithstand a warm, humid and aggressive internalenvironment and external temperatures expectedin the winter season. This can be a highly technical,complicated and demanding subject, requiring theservices of specialist consultants. Key factorsinclude: Heavy wear and tear and possible abuseduring use Avoidance of interstitial and surfacecondensation that can lead to corrosion/rotand failure of various elements - particularlythose concealed within the structure Ease of maintenance to ensure a clean andhygienic environment that eliminates dust, dirtand water traps The creation of safe conditions for users.Structural movement joints in the pool tank shouldbe avoided where possible. Joints between thetank and the pool surround should also beminimised where possible. If joints are unavoidable,these must have an effective proprietary water barsystem suitable for their application.Pool surrounds should be designed to the samestandard as the pool tank, and provision made toprevent lateral water travel to other areas.Materials should beselected with regard totheir environmentalsustainability, while alsoensuring durability andlifecycle qualities: Recyclable content BRE green guide rating Environmental profile.The following notes are intended to illustrate therange of potential problem areas and point to theneed to ensure experienced professional expertiseis available in all areas of the project team and thatdue account is taken of current research andrecommendations.Other concrete pool construction forms includesprayed concrete (gunnite) and concreteblockwork permanent formwork filled withreinforced concrete. These forms are primarilyassociated with private and hotel pools, and thereare considerations in respect of their use in largerpools that will require very careful attention. Expertindependent advice should be sought beforeconsidering these forms of pool construction.Types of pool tank designThe pool tank and the pool surround need to bedesigned as water retaining structures with highlevels of insulation (insulation to the pool surroundwill only be required for thermal compliance) 1.There are two main construction techniques:The use of tanking membranes in the poolsurrounds, as an alternative to water retainingconcrete, should generally be avoided. However iftanking is unavoidable great care must be taken inthe selection, detailing and testing of the membrane.The risk of damage due to thermal shock when thepool is emptied or filled with water and heated is acritical issue. This must be taken into account andintegrated into the design, construction andoperation of the building as set out in Table 1 below.Concrete pool tanksThese would normally be constructed fromshuttered in situ reinforced concrete to BS 8007.They can be formed with or without a screed/render and normally have a ceramic tile finish.Waterproofing additives can be used to reduce therisk of leakage. The tank structure should bethoroughly tested for water tightness, through afull depth tank test, before finishes are applied.Any faults should be remedied before tiling orlining work is undertaken. Most repairs will bemore effective from the wet side.Pre-cast concrete panels should generally beavoided due to problems of guaranteeing watertightness at the joints. Permanent shuttering shouldalso be avoided due to risks of deterioration ifRate 2Max fill/empty rate0.03 m/hour (0.75 m/day)Max heating rate0.25 C/hour (6 C/day)Table 12 BS5385: Part 4: 2009 Wall and floor tiling – Part 4: Design andinstallation of ceramic and mosaic tiling in special conditions –Code of practice.1 Approved Document L requires a minimum U-value of 0.25W/m2/K where the pool tank is ground bearing.May Revision 004Activity1 Sport England 2013
Swimming PoolsDesignGuidance NoteStainless steel pool tanksIssues to be carefully considered as part of thesystem selection and design process include:Prefabricated sectional stainless steel tankstructures are becoming more common, althoughin the UK these are still an emergent market. Theyare supported on a concrete slab and are eithersite welded to form a complete tank structure orare bolted together. A welded reinforced plasticliner may also be used for the walls and/or floor ofthe tank. The need for independent structures for thesteel pool tank support framework and poolsurround retaining walls, allowing periodicchecks for potential leaks and degradation Selection of the support structure and panelmaterials and their fixings to avoid or minimisethe risk of corrosion Establishing that the pool system will last theintended design life of the building. A ‘cost inuse’ appraisal for the proposed life of thebuilding is recommended Provision of a watertight joint at the junctionbetween the steel tank and the pool surroundneeds careful consideration. The poolperimeter details are critical: a tanked poolsurround may be required, and the interface ofthe pool and surround needs careful detailingin order to avoid leakage. Where pool liners areused, the pool wall panel liner should be fullybonded to the metal panel Fixed pool equipment: The pool surroundsrequire a number of fixing points for temporaryequipment associated with the variouselements of the swimming progamme. Seepages 10-11 for details The length of manufacturer’s guarantees forthe polymer liner and the risk of mechanicaldamage.Tank under construction in stainless steel panels withan integrated overflow and raised endAdvantages of the stainless steel pool include: They are quicker to assemble and install (butwill require an extensive period for design andoff-site fabrication) Elimination of issues associated with aconventional concrete pool tank Finished quality and dimensional tolerances ofthe tank can be more closely controlled.May Revision 0042 Sport England 2013
Swimming PoolsDesignGuidance NotePool tank constructionA comparison of the essential key differences (assuming other factors can be treated as equal)StructuralConcreteStainless SteelOption 1:Option 1: Monolithic design for whole of tank and pool surrounds when constructed fromin situ water-retaining concrete to BS8007/ BS EN 1992 Part 3 gives ahighly-stable structureStainless steel side walls incorporatingstructural back framing fixed to areinforced concrete floorOption 2: 3Option 2: Gunnite sprayed reinforced concrete Reinforced concrete blockwork withwaterproof renders/coatingsPolished stainless steel side walls andfloors incorporating structural backframing and welded seamsStainless steel wall panels are generallyavailable up to 3.0 m depth only – deeperpools will need a composite wall ofconcrete (lower) and stainless steel (upper)An integral stainless steel transfer channelAn Integral transfer channel is the most can be part of these systemscommon optionSome fixtures and fitting can be integratedFixtures and fittings need to be integrated into an integrated transfer channelinto the tank designJunction with pool surrounds and floorstructure need special careWaterproofing Inherent within well-constructed in situ Option 1reinforced concrete pools meeting BS Factory bonded PVC-faced galvanised8007 / BS EN 1992 Part 3or stainless steel wall panels and looseCan be augmented by waterproof linerPVC floor liner, with all seams thermallyand/or renderweldedOption 2 Bare polished stainless steel wall andfloor panels with welded panel jointsOption 3 FinishesOption 1 Option 1Fully ceramic tiles on render backing is the preferred finishPVC factory applied finish to wall panelsand loose PVC liner sheet to floorOption 2Option 2 Structure as option 1 with loose fittedPVC waterproof pool liner withthermally-welded seamsSpecialist finish renders and paint Ceramic tile option to upper wallfinishes have been used where long-termsections subject to design and stiffeningdurability is not so importantOption 3 Loose PVC liner3 Gunnite and reinforced concrete construction are more commonly used for private / hotel / fitness centre pools and are unlikely toachieve the long-term life of an in situ RC pool.May Revision 0043 Sport England 2013
Swimming PoolsDesignGuidance NoteConcreteRobustnessStainless Steel Robust - minimal risk of damage from vandalism or pool hall activities Durable Stable construction Workmanship is critical to waterproofingand long term life of the poolPVC lining is liable to mechanicaldamage from sharp objects. e.g.puncture resulting in leakage Potential movement issues at thejunctions with loose linings and morerigid wall/floor and wall/surround Workmanship is critical to waterproofingand long-term life of the poolService lifeProven long service life. Examples c 100 years Periodic replacement of liners required(c 10 years )MaintenanceMinimal long-term maintenance of pool tank structure. Re-grouting of ceramic tiles maybe required c 20 year intervals. Life of finishes will depend upon quality of materials,maintenance of pool water quality, waveaction and chemicals utilizedRegular inspection and quick repair ofPVC liner damage required Long construction period for building the concrete shell Wet trade for pool finishes require anextensive period for application and curingLengthyoff-sitedesignandprefabrication time requires earlyplacement of the contract ConstructionAnnual inspection of stainless steelstructure to check for pitting/corrosionShort installation period Maximum warranty period 15 years Reductions in programme time arepossible compared to a concrete pool(likely to be more appropriate fortemporary and portable facilities) Long overall construction program Resolution of severe defects and leakage can be complex requiring potentialdrainage of pool and resulting inextended closureResolution of severe defects andleakage can be complex requiringpotential drainage of pool and resultingin extended closure Dimensional control dependentquality of workmanship on siteon Dimensional control achieved throughfactory prefabrication and site control Lack of a long-term warranty(Depending on type of contract, the latentdefects period will be 6/12 years and thepatent defects period will be 12 months)Quality controlOldest examples c 40 yearsCostsTank constructionNormally used as benchmarkCheaper in terms of capital costs andshort-term expenditureOther associatedcosts in theconstructionprocessDependent on the undercroft and basement Dependent on the undercroft and basementplant room configurations and the contractors plant room configurations and theallowances for preliminariescontractors allowances for preliminariesPeriodic liningreplacement andclosedown costs(over a 60 year period)Over a period of 60 years, periodic close Over a period of 60 years, periodic closedown of the pool would be expected for down of the pool would be expected forrepairs to tiles and grouting. Possibility of replacing the lining from 10 yearsretiling in refurbishment terms from 25 years Other maintenancecostsMay Revision 004Shorter contract prelims are likelyMechanical damage to lining wouldrequire urgent repair4 Sport England 2013
Swimming PoolsDesignGuidance NotePool and pool surround drainage principleswith a slotted plastic grille. The following areimportant factors regarding finishes to a pool:BS EN 15288-1: 2008 requires the pool surroundto be designed to avoid contamination of the poolwater by water flowing on to the floor. Drainage ofthe pool surround areas should be independent ofthe deck level pool water recirculation drainagechannel. This can be achieved using twin channelson the pool surround incorporating either individualgrilles over two separate channels or a single grillespanning over an integral twin channel system.However, careful consideration of grille width andselection of a suitable specification is needed, inparticular to achieve the necessary slip resistance/ health and safety requirements. An appropriate surface treatment to concretepool tanks is required to provide a key forapplied finishes. This is usually achievedthrough mechanical keying of the concretesurface to expose the coarse aggregate Compatibility of the tiling specification with thetile adhesive and grouting Soft water, aggressive chemicals, rapidlymoving water or heavy wear may require tilingto receive epoxy based adhesives and/orgrouts in lieu of cementitious based onesFallHowever, for cost, application and programmereasons, the use of epoxy grouts should beminimised Waterproof membranes should generally notbe used between pool tiling and a concretepool structure, as these can be the cause ofsubsequent failure of the finishes if there is anyshocking of the tank during emptying orheating of the pool. The pool tank should bedesigned to be waterproof The noise of the circulating water continuouslyfalling into the deck level channel can bedistracting. In order to minimise the impact ofwater flow, the pool side of the deck levelchannel should be set at an angle so that thewater runs down the channel side face ratherthan tumbling into the channel. See SectionB-B overleaf.To sewerWater treatmentsystem and
The pool tank and the pool surround need to be designed as water retaining structures with high levels of insulation (insulation to the pool surround will only be required for thermal compliance) 1. There are two main construction techniques: Concrete pool tanks These would normally be constructed from shuttered in situ reinforced concrete to BS 8007