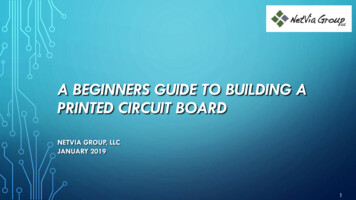
Transcription
A BEGINNERS GUIDE TO BUILDING APRINTED CIRCUIT BOARDNETVIA GROUP, LLCJANUARY 20191
2
3
INTRODUCTIONMANUFACTURING A BASIC MULTILAYER PRINTED CIRCUIT BOARD CAN BESUMMARIZED AS FOLLOWS: PLANNING & CAM: CREATION OF BUILD PLAN AND NECESSARY TOOLING IMAGING: INNER LAYER IMAGE APPLIED TO SUBSTRATES DEVELOP, ETCH, STRIP: ETCH COPPER FEATURES INNER LAYER AOI: COMPARE ETCHED PANEL TO CAM DATA LAMINATION: BONDING INNER LAYERS TOGETHER DRILL: DRILL HOLES IN THE BOARD PER DESIGN & HOLE SIZES DESIRED COPPER 1: INITIAL COPPER DEPOSIT INTO THE DRILLED HOLES IMAGING: OUTER LAYER IMAGE APPLIED TO THE PANELS COPPER 2: PLATE THE OUTER LAYERS WITH COPPER (IE. PATTERN PLATE) STRIP, ETCH, STRIP: ETCH COPPER FEATURES OUTER LAYER AOI: COMPARE ETCHED PANEL TO CAM DATA SOLDER MASK: PROTECTIVE COATING APPLIED TO THE OUTER LAYERS SCREEN PRINTING: PRINT A “LEGEND” ON TO THE BOARD (TEXT IDENTIFIERS) FINAL FINISH: APPLYING A FINAL FINISH TO EXPOSED COPPER ROUTE: CUTTING OF THE FINISHED BOARDS FROM THE PANEL FINAL QC: VISUAL & ELECTRICAL TESTING PRIOR TO SHIPMENT TO THE CUSTOMER4
BASICS – A QUICK VIEWTHE FOLLOWING 3 SLIDES WILL SHOW A BASIC VIEW OF THE STEPSPREVIOUSLY MENTIONED.FOLLOWING THOSE THREE SLIDES WE WILL GO INTO GREATER DETAILSHOWING AN ACTUAL REPRESENTATION OF PCB FABRICATION.NOTE, THERE ARE MANY UNMENTIONED STEPS USED IN FABRICATION,THE PRESENTATION WILL FOCUS ON THE MAIN PROCESS STEPS.5
BASICS QUICK VIEWINNER LAYER DRYFILM APPLICATIONINNER LAYER DRY FILMEXPOSED /DEVELOPEDINNER LAYERCOPPER ETCHEDDRY FILM RESIST STRIPPEDALL LAYERS ARELAMINATED TOGETHERLAMINATED PANEL ISTHEN DRILLED6
BASICS QUICK VIEWELECTROLESS COPPERDEPOSITED INTODRILLED HOLESTIN IS PLATED TOEXPOSED AREASOUTER LAYER DRYFILM APPLIEDDRY FILM RESIST ISSTRIPPEDOUTER LAYER IMAGEEXPOSED / DEVELOPEDALL EXPOSEDCOPPER IS ETCHEDCOPPER II ORPATTERN PLATETIN IS STRIPPED7
BASICS QUICK VIEWLIQUID PHOTOIMAGEABLE SOLDERMASK IS APPLIEDPANEL IS IMAGED ANDUN-DESIRED SOLDERMASK IS DEVELOPEDOFFSILK SCREEN LEGEND ISPRINTED TO BOARD PERCUSTOMER DESIGNFINAL FINISH DEPOSITEDTO EXPOSED AREAS8
PLANNINGONCE A CUSTOMER ORDER IS RECEIVED IT IS GIVEN TO “PLANNING” TO DETERMINETHE STEPS NEEDED TO FABRICATE THE CUSTOMER DESIGN.EACH ORDER IS ASSIGNED A “TRAVELER” WHICHFOLLOWS EACH PANEL THROUGHFABRICATION.TRAVELERFOR FULLYPLANNEDBOARD –ALL STEPSNEEDEDFOR THEBUILD9
CAMAFTER A TRAVELER IS CREATED THE JOB IS SENT TO “CAM” TO CREATE ALLNECESSARY PROGRAM FILES FOR BOARD FABRICATION.EXAMPLE OF CAM PLANNING BOARD DESIGN PER CUSTOMER SUPPLIED FILES10
IMAGING (INNER LAYERS)BASE MATERIAL FOR INNER LAYERS TYPICALLY CONSISTS OF A SUBSTRATE (COMMONLYWOVEN FIBERGLASS) WITH COPPER ON EACH SIDE. MATERIALS ARE SENT TO “IMAGING”& DRY FILM IS APPLIED ON BOTH SIDES. ON INNER LAYERS A “POSITIVE” IMAGE IS USEDTO COVER / PROTECT ONLY COPPER WHICH IS TO REMAIN.BaseMaterialDRY FILM IS APPLIEDTO THE PANELDESIGN IS LASERIMAGED TO THEFILMED PANEL(S)REPRESENTATION OFMATERIALS PRE-EXPOSURE11
IMAGING (INNER LAYERS)ONCE AN IMAGE IS EXPOSED ON TO THE PANEL IT IS THEN DEVELOPED. ANYAREAS EXPOSED TO U.V. LIGHT WILL HARDEN AND NOT DEVELOP OFF.IMAGEDPANELENTERINGDEVELOPERPANEL EXITINGDEVELOPER – ALLUNEXPOSED /UN-HARDENEDFILM REMOVEDREPRESENTATIONOF BEFORE / AFTER12
ETCH (INNER LAYER)NOW THAT THE CIRCUITRY WHICH IS TO REMAIN ON THE PANEL IS DEFINED &PROTECTED WITH EXPOSED DRY FILM, WE ETCH AWAY UNDESIRED COPPER FROMTHE PANELS.PANELENTERINGTHE ETCHLINEPANEL EXITINGTHE ETCH LINE– ALLUNPROTECTEDCOPPERETCHED OFFREPRESENTATION OFBEFORE / AFTER13
ETCH (INNER LAYER)THE FINAL STEP INVOLVED IN THE STRIP & ETCH OF INNER LAYERS IS REMOVINGTHE HARDENED DRY FILM FROM THE SUBSTRATE.HARDENED DRY FILMREMOVED TO REVEALCOPPER DESIGN ONTHE INNER LAYERREPRESENTATION OFBEFORE / AFTER14
QC - INNER LAYERINNER LAYERS GO THROUGH AOI (AUTOMATED OPITICAL INSPECTION) WHICHCOMPARES THE ETCHED PANEL TO CUSTOMER CAM FILES TO INSURE IT MATCHESTHE DESIGN, INSURING THERE ARE NO SHORTS OR OPENS IN THE CIRCUITRYCAM DATA BEING LOADED INTO AOIAOI MACHINE INSPECTINGPANEL, COMPARING TOLOADED CAM DATA15
LAMINATIONINNER LAYERS ARE THEN “STACKED UP” IN THE PROPER ORDER, LAMINATEDTOGETHER WITH ADHESIVE (“PRE-PREG”), AND A LAYER OF COPPER IS PLACED ONBOTH THE TOP & BOTTOM TO FORM THE OUTER LAYERS.PANELSARE“STACKEDUP” INORDERTHEN PLACED IN APRESS FORLAMINATIONREPRESENTATION OFBEFORE / AFTER16
DRILLONCE LAMINATED, PANELS WILL BE DRILLED PER DESIGN.LAMINATED PANELPRIOR TO DRILLREPRESENTATION OFBEFORE / AFTERDURING DRILLPANEL AFTER DRILLING17
ELECTROLESS COPPERONCE DRILLED, THE HOLES ARE PLATED IN AN “ELECTROLESS” PROCESS (“COPPER1”) TO DEPOSIT ALL HOLES WITH A LAYER OF COPPER WHICH WILL PROVIDE AMETALIZED BASE WHICH ADDITIONAL COPPER CAN THEN BE PLATED ON TO.ELECTROLESS COPPERBATH LINETHROUGH HOLES BEFORE &AFTER ELECTROLESSREPRESENTATION OFBEFORE / AFTER18
IMAGING (OUTER LAYERS)AFTER ELECTROLESS PLATING, OUTER LAYERS ARE DRY FILM COATED FORIMAGING. ON OUTER LAYERS A “NEGATIVE” IMAGE IS USED TO EXPOSE AREAS SOTHEY MAY SELECTIVELY RECEIVE ADDITIONAL COPPER PLATING (IE. PATTERNPLATE).IMAGED PANEL AFTERDEVELOPER, SHOWINGCIRCUITRY NOW EXPOSEDPANEL IS DRYFILMED, THENLASERIMAGEDREPRESENTATION OFBEFORE / AFTER19
PLATINGWITH COPPER CIRCUITRY NOW EXPOSED, AN EXTRA LAYER OF COPPER IS APPLIEDTO BUILD UP SURFACE LAYER COPPER THROUGH AN ELECTROLYTIC PROCESS (THISSTEP IS COMMONLY REFERRED TO AS “COPPER 2” OR PATTERN PLATE).PANEL AFTER RECEIVING“2ND COPPER” PLATINGREPRESENTATION OFBEFORE / AFTERPANEL IN SECONDCOPPER PLATING TANK20
PLATINGAS THE PANELS STILL HAVE THE ORIGINAL BASE COPPER ON THEM, BEFORE ETCHING OFFCOPPER, THE PANELS ARE PLATED WITH A LAYER OF TIN (“TIN RESIST”).TIN IS PLATED OVER ALLEXPOSED COPPERPANELS ARE PLACED INTO ATIN PLATING TANKREPRESENTATION OFBEFORE / AFTER21
ETCH (OUTER LAYERS)WITH TIN PROTECTING THE COPPER WE WANT TO KEEP, PANELS NOW HAVE THEIRPHOTO-RESIST (DRY FILM) STRIPPED OFF.PANELSEXITINGRESISTSTRIP LINEPANELS ARESTRIPPEDOF ALL DRYFILM RESISTREPRESENTATION OFBEFORE / AFTER22
ETCH (OUTER LAYERS)PANELS ARE PUT THROUGH THE ETCHER TO HAVE ALL NON-TIN COATED AREASETCHED OFF THE PANEL.PANELSENTERINGETCHERPANELSEXITINGETCHER – ALLUNPROTECTEDCOPPERETCHED OFFREPRESENTATION OFBEFORE / AFTER23
ETCH (OUTER LAYERS)THE LAYER OF TIN PROTECTING DESIRED CIRCUIT AREAS IS STRIPPED FROM H ALLTINSTRIPPEDREPRESENTATION OFBEFORE / AFTER24
QC - OUTER LAYEROUTER LAYERS GO THROUGH AOI TO COMPARE THE ETCHED PANEL TO CUSTOMERCAM DATA TO INSURE IT MATCHES THE DESIGN AND THERE ARE NO SHORTS OROPENS IN THE CIRCUITRYPANEL CAM DATA BEINGLOADED IN TO AOIAOI MACHINE INSPECTINGPANEL, COMPARING TOLOADED CAM DATA25
SOLDER MASKWITH PANELS NOW FULLY RESEMBLING FINAL DESIGN, IT IS NECESSARY TOPROTECT THE BOARDS FROM SUBSEQUENT SOLDERING, EXTERNAL FORCES &ENVIRONMENT. TO DO SO, A LAYER OF SOLDER MASK IS APPLIED TO THESURFACES USING SIMILAR IMAGING TO DRY FILM.PANEL COATEDWITH LIQUIDPHOTO-IMAGEABLESOLDER MASK (LPI)SOLDER MASKAPPLIEDSOLDER MASKDEVELOPEDAND IS THEN IMAGEDTO UV LIGHT INSELECT AREAS TOHARDEN THE SOLDERMASKREPRESENTATION OFBEFORE / AFTER26
SOLDER MASKONCE THE IMAGE IS APPLIED TO THE PANELS, THE SOLDER MASK IS NOWHARDENED IN SPECIFIC AREAS WHERE IT IS DESIRED TO REMAIN. THOSE AREASWHICH WERE NOT EXPOSED OR HARDENED, ARE REMOVED IN THE SOLDER MASKDEVELOPER.PANEL AFTEREXPOSURE,ENTERING THEDEVELOPERPANEL EXITINGTHE DEVELOPER,ONLY DESIREDSOLDER MASKLAYER REMAININGSOLDER MASKAPPLIEDSOLDER MASKDEVELOPEDREPRESENTATION OFBEFORE / AFTER27
SILK SCREEN / LEGEND PRINTWITH SOLDER MASK APPLIED, PANELS ARE NOW LEGEND PRINTED.SOLDER MASKEDPANEL PRIOR TO SILKSCREEN LEGENDAPPLICATIONREPRESENTATION OFBEFORE / AFTERPANEL AFTERLEGEND HAS BEENAPPLIED28
FINAL FINISHA FINAL PLATING OVER EXPOSED COPPER AREAS WITH THE CUSTOMERS CHOICEOF COATING (NICKEL/GOLD, HASL/TIN LEAD SOLDER, SILVER OR TIN – THERE AREMANY OPTIONS AVAILABLE & SELECTION WILL BE BASED ON CUSTOMERS NEEDS).PANEL PRIOR TORECEIVING GOLDPLATINGPANEL AFTERRECEIVINGGOLD PLATINGREPRESENTATION OFBEFORE / AFTER29
ROUTETYPICALLY MULTIPLE BOARDS ARE BUILT ON A PANEL FOR EFFICIENCY AND ONCETHE BUILD IS COMPLETE, THEY NEED TO BE CUT OUT OF THE PANEL, WHICH IS ATTHE ROUTE STEP.PANEL WITHMULTIPLEBOARDS PRIORTO ROUTEPANEL ANDBOARDSDURING ROUTEFULLYROUTEDBOARDS30
FINAL TESTINGWITH THE FABRICATION PROCESS NOW COMPLETE, BOARDS ARE ELECTRICALLY TESTED TOCONFIRM FUNCTIONALITY. CROSS SECTIONS ARE PERFORMED TO CONFIRM INTEGRITY OFPLATED THROUGH HOLES, HOLE WALL PLATING & INNER LAYER “REGISTRATION”.“FLYING PROBE” ELECTRICAL TESTEXAMPLE OF A BOARD CROSS SECTION31
CURRENT TECHNOLOGIES BLIND/BURIED/STACKED VIAS ETCHED RESISTORS CASTELLATIONS32
BLIND/BURIED/STACKED VIAS33
35
36
ETCHED RESISTORS37
39
CASTELLATED HOLES40
41
FUTURE TECHNOLOGIES 3D PRINTED PCBS43
44
45
ADVANTAGES AND DISADVANTAGESPROS MINIMAL EQUIPMENT REQUIREDABILITY TO PRODUCE PROTOTYPES QUICKLYABILITY TO PRINT CIRCUITRY ON 3D SURFACESCONS (CURRENTLY) LOW PRODUCTION CAPABILITIES LIMITED MULTILAYER TECHNOLOGY LIMITED THRU HOLE PLATED TECHNOLOGY LIMITED RESOLUTION46
47SAMPLE FOOTER TEXT10/12/201947
48
49
50
IF YOU WOULD LIKE TO CONSIDERNETVIA GROUP FOR YOUR PCBFABRICATION OR SHOULD YOU HAVEANY QUESTIONS, YOU CAN EMAIL USAT: SALES@NETVIAGROUP.COMNETVIA GROUP, LLCJANUARY 2019MAIN: (972) 573-1400FAX: (972) 573-1410ADDRESS: 230 IRBY LN.IRVING, TX 7506151
a beginners guide to building a printed circuit board netvia group, llc january 2019 1. 2. 3. introduction manufacturing a basic multila