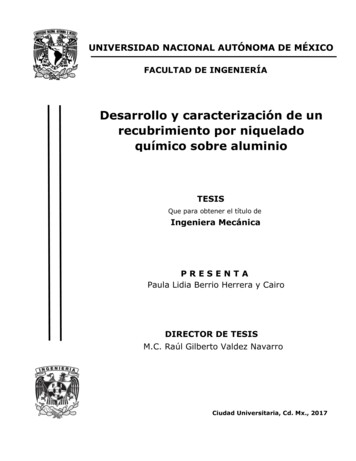
Transcription
UNIVERSIDAD NACIONAL AUTÓNOMA DE MÉXICOFACULTAD DE INGENIERÍADesarrollo y caracterización de unrecubrimiento por niqueladoquímico sobre aluminioTESISQue para obtener el título deIngeniera MecánicaPRESENTAPaula Lidia Berrio Herrera y CairoDIRECTOR DE TESISM.C. Raúl Gilberto Valdez NavarroCiudad Universitaria, Cd. Mx., 2017
Para empezar quiero agradecerle a la Universidad Nacional Autónoma de Méxicopor abrirme sus puertas y dejarme formar parte de esta grandiosa institución desdeel bachillerato (ENP 7).No habría podido llegar hasta este punto sin el apoyo incondicional de mi mamá quesiempre ha buscado lo mejor para mí, de mi hermana Perlita, solo diré que no mepudo haber tocado una mejor hermana, y de mi abuelito Memo que me ha cuidadodesde que era bebé.Este proceso lo comencé a lado de mi amigo del bachillerato, César, que meconvenció de no tirar la toalla después de un mal primer semestre y con él que pasémomentos muy graciosos como cuando nos perdimos al intentar llegar al EdificioPrincipal desde el metro Universidad en la semana de bienvenida.Lo único bueno de ese primer semestre fue conocer a Keren y a Daniela con lasque pase momentos muy buenos. Y al final de la carrera conocí a Félix, una personasúper especial, que no solo me ayudó en la fase experimental de la tesis sinotambién me ha hecho crecer como persona y confiar más en mí.Le agradezco a mi director de tesis M.I. Raúl Valdez por tenerme paciencia, a laDra. Alba Covelo por permitirme utilizar las instalaciones del laboratorio CENISApara realizar la parte experimental de la tesis y al Dr. Carlos por ayudarme con laparte de espectroscopia de impedancia electroquímica de este trabajoEste trabajo culmina una etapa muy importante y no hubiera sido posible sin todasaquellas personas que de una u otra manera intervinieron y estuvieron presentesen mi vida.¡Muchas gracias a todos!I
Agradecimientos ------------------- IObjetivos ----------------------------- 1Introducción ------------------------ 1Capítulo 1 Antecedentes ------ 21.1 Niquelado químico ----- 21.1.1 Alternativas de recubrimiento por niquelado -------------- 71.1.2 Propiedades del niquelado químico ------------------------ 141.1.3 Parámetros de proceso más importantes y su efectoen el recubrimiento -------- 231.1.4 Aplicaciones -------- 321.2 Aluminio. Propiedades y Características ----------------------- 361.2.1 Modificaciones de las propiedades del sustrato -------- 391.3 Corrosión ------------------ 45Capítulo 2 Experimentación -------------------------------------------------- 522.1 Niquelado químico --- 522.1.1 Preparación de probetas ---------------------------------------- 522.2 Aplicación del recubrimiento --------------------------------------- 542.2.1 Parámetros del proceso ------------------------------------------ 54II
2.3 Caracterización del recubrimiento ------------------------------- 582.3.1 Microscopía --------- 582.3.2 Adherencia --------- 592.3.3 Espectroscopía de Impedancia Electroquímica (EIS)- 62Capítulo 3 Resultados y análisis ---------------------------------------------- 643.1 Medición de pH -------- 643.2 Microscopía ------------- 653.3 Adherencia ---------------- 743.4 Espectroscopía de Impedancia Electroquímica (EIS) ------- 77Conclusiones ---------------------- 85Bibliografía ------------------------- 87Referencia de imágenes ----- 89III
Obtener un recubrimiento Ni-P por la vía química sobre aluminio. Evaluar la adherencia de los recubrimientos generados con el sustrato por medio deensayos de pull-off. Evaluar la resistencia a la corrosión de los recubrimientos generados por la técnica deEspectroscopia de impedancia electroquímica.Como se sabe, el aluminio es utilizado con frecuencia en estructuras expuestas al medioambiente, esto es porque su proceso de degradación electroquímica genera una capa de óxidoque lo protege. Cuando el aluminio se expone a un ambiente acuoso no es posible que estacapa de óxido se genere por lo que el aluminio se deteriora. Para evitar que el aluminio secorroa, se le puede añadir una capa protectora (recubrimiento). De esto trata este trabajo,añadir un recubrimiento (niquelado) a un sustrato (aluminio) y evaluarlo.El proceso para recubrir las probetas de aluminio consistió en dos etapas. Para la primeraetapa se requería convertir la superficie a recubrir en una superficie catalíticamente activa, estose logró por medio de un zincado. La segunda y última etapa fue realizar la deposición en elbaño de níquel (niquelado).Para caracterizar el recubrimiento se realizó un análisis de composición para asegurar que setuviera un depósito níquel-fósforo (Ni-P), se visualizaron zonas importantes y se midió elespesor por medio del microscopio óptico haciendo una comparación con el microscopioelectrónico de barrido; se midió la fuerza de adherencia del recubrimiento y se realizó unanálisis de Espectroscopía de Impedancia Electroquímica (EIS).1
Los recubrimientos se utilizan para aislar las regiones anódica y catódica, también impiden ladifusión del oxígeno o del vapor de agua que son iniciadores de corrosión o de oxidación. Losrecubrimientos temporales, como por ejemplo, la grasa y el aceite, proporcionan cierto nivel deprotección pero son fácilmente superados. Los recubrimientos orgánicos, como la pintura, olos recubrimientos cerámicos, como el esmalte y el vidrio, dan una mayor protección. Sinembargo, si se destruye el recubrimiento, se expone un pequeño sitio anódico que sufre deuna corrosión rápida y localizada [1].En la electrodeposición de metales, una solución acuosa (un electrolito) es regularmente usadaen parte porque muchas de las sales metálicas tienen una alta solubilidad y también por labuena conductividad eléctrica de dichas soluciones. Los portadores de corriente son partículasconocidas como iones eléctricamente cargados.Todos los procesos de deposición metálica a partir de soluciones de sales metálicas puedenser clasificados como reacciones de reducción química. La disolución de un metal da unadesintegración de la solución salina, lo cual da origen a un proceso de oxidación. Unareducción puede verse como el proceso electroquímico donde sus electrones son tomados.Los dos tipos de reacción son complementarios como se muestra en la ecuación 1:𝑀𝑒 𝑧 𝑧𝑒 𝑀𝑒𝑧: 𝑣𝑎𝑙𝑒𝑛𝑐𝑖𝑎𝐸𝑐. 1En el caso de deposición química donde no se suministra una corriente externa al proceso, loselectrones requeridos para llevar a cabo la descarga de iones metálicos se producen por unareacción química en la solución.2
Todos los procesos de deposiciones químicas pueden ser clasificados en alguno de lossiguientes tres tipos:1. Deposición por intercambio de iones o intercambio de carga (reacciones dedesplazamiento, cementación, galvanizado por inmersión).2. Deposición por contacto con el metal a recubrir, inmerso en una solución de la salmetálica a depositar, con un segundo metal u otra pieza del mismo metal.3. Deposición del metal a partir de soluciones que contienen agentes reductores.El desarrollo de los baños de níquel a lo largo del tiempo, comienza en 1844 cuando sedescubrió que el níquel metálico podía ser depositado desde una solución acuosa de sus salespor reducción con hipofosfito. En los años siguientes, hubo más estudios sobre la reacciónpero el metal formado de esa manera era regularmente en polvo. Algunos investigadoresobtuvieron recubrimientos brillantes, una vez que era agregado el agente reductor en todas lassuperficies en el recipiente de reacción. Varios años después, se describió la reacción de lassales del níquel en un medio alcalino con hipofosfito en presencia de un activador de paladio.Ninguno de estos estudios llegó a una aplicación práctica.El descubrimiento de la tecnología de deposición química del níquel como se usa hoy en día,se puede decir que fue hecha en 1946 cuando se desarrolló un sistema práctico.El estudio se hizo a partir de la electrodeposición de aleaciones de níquel tungsteno de unbaño de citrato a ciertas temperaturas. El cátodo era un tubo de acero montadoconcéntricamente con respecto al ánodo, donde solamente la superficie interna fue revestida.El depósito mostró un alto porcentaje de esfuerzos internos atribuidos a la presencia de losproductos oxidantes del citrato. En un intento de resolver el problema, se agregó un rango deagentes oxidantes, incluyendo hipofosfito. Se encontró que la superficie exterior del tubo deacero estaba recubierto con níquel, en adición a la eficiencia de la alta corriente. Estosresultados fueron interpretados en términos de reducción química tomando lugarsimultáneamente con la electrodeposición. Se determinó la naturaleza catalítica de la reaccióny se prescribieron las condiciones de operación, mostradas en la Tabla 1.3
Tabla 1. Composición de los baños y datos de operación [2]Tipo de baño123Cloruro de níquel NiCl2.6H2O (g/l)303030Hipofosfito de sodio NaH2PO2 (g/l)101010gCloruro de amonio NH4Cl ( /l)501000Citrato de sodio Na3C6H5O7.51/2H2O (g/l)1000100Valor de pH8-98-96-8Temperatura ( C)909090(μm6124Tasa de deposición /h)Apariencia del depósitobrillante mate semi brillanteLos baños a base de componentes reductores de boro se trabajaron en 1942 cuando se logrósintetizar el borohidrato de sodio (NaBH4).Un baño de deposición química está compuesta por lo siguiente: fuente de metal, agentereductor, agente complejante, aceleradores, estabilizadores, regulador, regulador de pH yagente activador; en la Tabla 2 se muestra el funcionamiento de cada uno de los componentes.Tabla 2. Componentes y sus funciones en un baño de deposición química del níquel [12]ComponenteIones de níquelIones esReguladoresRegulador depHAgentes deremojoFunciónFuente del metalAgente reductorForma complejos de níquel, previene el exceso de concentración deiones de níquel libres para estabilizar la solución y prevenir laprecipitación de fosfito de níquel. También actúa como regulador de pH.Activan los iones de hipofosfito y aceleran la deposición. Modo deacción se opone estabilizadores y complejantes.Previenen la degradación de la solución mediante el blindaje de losnúcleos con actividad catalítica.Controlador de pHPor subsecuente ajustador de pHIncrementa la actividad de la superficie a ser recubierta.4
Todos los baños de deposición química poseen ciertas características:a. Los baños contienen iones de níquel y agentes reductores en equilibrio meta estable.El baño se estabilizará normalmente tal que los dos componentes no reaccionenespontáneamente uno con otro bajo temperaturas normales de operación. Laestabilidad del baño es un criterio importante.b. El níquel contenido en estos baños es muy bajo (2 a 8 g/l).c. La tasa de deposición es usualmente entre 10 a 25 μm/h.d. Aparte de la composición del baño, la tasa de deposición es estrechamente dependientede la temperatura, pH y con la edad del baño. Los reguladores, complejantes,aceleradores y estabilizadores añadidos a las formulaciones para asegurar la tasa dedeposición óptima y la estabilidad del baño.e. La deposición metálica es iniciada y mantenida por un catalítico, al removerlo terminala reacción.f. La superficie a recubrir actúa como catalítica en algunos casos, donde estos materialesson catalíticamente activas o cuando es activado usando un catalizador. El depósitometálico en sí mismo debe ser catalíticamente activa con el fin de que el procesoheterogéneo continúe.g. La reducción del níquel es acompañada por la evolución del hidrógeno. El índice molarde níquel depositado por la evolución de hidrógeno entra en el rango de 1:1.76 a 1:1.93.h. Recubrimientos formados por deposición química no son normalmente del metal purotambién contienen fósforo o boro, derivados de los agentes reductores. Las cantidadespresentes dependen de las condiciones de deposición. Cuando se utilizan metalespesados como estabilizadores (Tl, Pb, Cd) estos podrían estar incorporados en eldepósito.i.Los químicos consumidos en la reacción, debe ser repuesto, ya sea sobre una basecontinua o a intervalos regulares cuando la concentración caiga después de un niveldado.Los métodos de deposición química de níquel, se clasifican por el agente reductor que se utilizaen la solución acuosa, el pH del baño y la temperatura de deposición.5
Aparte de las sales de níquel utilizadas, el componente más importante es el agente reductory por lo tanto el uso de un sistema de clasificación basado en esto. Los agentes reductorescomúnmente utilizados son: hipofosfito, borohidrato, aminoboranos e hidracina, ver Tabla 3.De estos, predomina el hipofosfito de sodio, NaH2PO2.H2O, el cual forma cristaleshigroscópicos e incoloros que son fácilmente solubles en agua.Tabla 3. Agentes reductores para deposición química de níquel [2]ComponenteFórmulaHipofosfito de sodioNaH2PO2H2OBorohidrato de sodioNaBH4Borohidrato de dimetilamina (CH3)2NH.BH3Borohidrato de 1.2-1.1-1.2El mecanismo de deposición del baño con hipofosfito tiene como reacción completa en lareducción de hipofosfito de los iones de níquel por lo general se escribe como:3𝑁𝑎𝐻2 𝑃𝑂2 3𝐻2 𝑂 𝑁𝑖𝑆𝑂4 3𝑁𝑎𝐻2 𝑃𝑂3 𝐻2 𝑆𝑂4 2𝐻2 𝑁𝑖 0𝐸𝑐. 2La misma reacción puede ser formulado:2𝐻2 𝑃𝑂2 𝑁𝑖 2𝐻2 𝑂 2𝐻2 𝑃𝑂3 𝐻2 2𝐻 𝑁𝑖 0𝐸𝑐. 3Todas estas reacciones toman lugar en superficies catalíticamente activas sin energía externa,con altas temperaturas (entre 60 a 95 C). En adición con el níquel metálico Ni0 se formanalgunas moléculas de hidrógeno. De esa manera los recubrimientos químicos de níquel formana partir del hipofosfito son actualmente aleaciones Ni-P con un contenido del 3 a 15% defósforo.Existen dos tipos de baños de hipofosfito, ácidos y alcalinos. Durante los años 50’s, los bañosácidos con hipofosfito ofrecían mayores ventajas en comparación con los baños alcalinoamoniaco. Desde una tasa alta de deposición, aumento de estabilidad, mejor simplificación delcontrol del baño y depósitos Ni-P con propiedades perfeccionadas. El pH predilecto de estosbaños va entre 4.6 a 5, operados a temperatura desde 85 a 95 C. La tasa de deposición estáen un rango de 10 a 30 μm/h.6
La primera patente comercial del baño químico de níquel fue en 1916 basado en hipofosfitoalcalino. El comportamiento de los iones de níquel en solución alcalina es muy parecido a unmedio ácido, siendo acompañado por la transformación de hidrógeno y la oxidación dehipofosfito a fosfito. La tasa de deposición es un poco lenta en soluciones alcalinas y losdepósitos formados son más porosos y menos resistentes a la corrosión, aunque a menudomás brillante. Por otro lado, estas soluciones, son extremadamente estables aún sin la adiciónde agentes.Las soluciones alcalinas fueron introducidas gradualmente a la industria y como resultado enaplicaciones especializadas y el desarrollo de bajas temperaturas en el depósito químico. Unpunto significante es la metalización de plásticos con deposición química de níquel, suscondiciones de operación en temperatura es menor a 65 C. Las concentraciones de níquel ehipofosfito de estos baños son similares a los encontrados en soluciones ácidas. El amoniacotiene mayor importancia como agente complejante para los iones de níquel [2].Una opción para modificar las propiedades de este tipo de depósito, es la codeposición departículas duras, especialmente de compuestos cerámicos, a fin de intentar dotar de mayorresistencia al desgaste a estos recubrimientos o conferirles determinadas propiedadesespecíficas. También se ha hecho por medio de procesos electrolíticos, que para lograr undeterminado porcentaje de incorporación en volumen o en peso, en el depósito, es menor lacantidad de partículas requeridas para el proceso químico que para el electrolítico.La figura 1 muestra un arreglo experimental para la deposición de un recubrimiento químicocompuesto de níquel. Se emplea para ello un recipiente cilíndrico con un fondo cónico y unachaqueta exterior. El electrolito con las partículas dispersadas a una temperatura apropiada esbombeado a través del fondo. La chaqueta exterior recoge el electrolito que se derrama. Elsustrato es suspendido en el comportamiento inerte. Para conservar las partículas ensuspensión, el electrolito se agita ligeramente. Se emplean diversos métodos para conseguirla agitación, entre los que se puede mencionar: agitación por aire, circulación del baño,7
agitación por ultrasonido, etc. El tipo de movimiento del material y la técnica de suspensiónpueden afectar el resultado. Condiciones de un flujo irregular impiden una dispersión uniformede la segunda fase. Este factor es más crítico para los procesos químicos.Figura 1. A: compartimiento inerte de suspensión, B: sustrato, C: compartimiento deelectrolito derramado, D: chaqueta exterior, E: recipiente con fondo cónico, F: sistema debombeoLa estabilidad del baño químico, con adición de partículas es menor, de modo que se debenadicionar estabilizadores para prevenir la descomposición espontánea. Todas lasprecauciones recomendadas para el mantenimiento de los baños para la obtención dedepósitos químicos, por supuesto, deben seguirse los procesos con adición de partículas. Serecomienda la filtración periódica y un monitoreo frecuente del nivel de impurezas del baño.Es posible preparar materiales compuestos con cualquier metal que pueda ser usado comodepósito químico. Así, recubrimientos químicos compuestos a base de Ni, Cu, Au, Co, y Sn, yse pueden agregar una amplia variedad de partículas, como:a. Minerales como caolín, grafito, cuarzo, talco, diamante.b. Cerámicos, principalmente óxidos, carburos, boruros, nitruros, siliciuros, silicatos,carbonatos, fosfatos, oxalatos y fluoruros de: aluminio, boro, cromo, hafnio, molibdeno,silicio, calcio, tantalio, vanadio, tungsteno, zirconio, manganeso, magnesio, bario,estroncio, cerio, hierro, níquel y titanio.8
c. Metales y aleaciones de: boro, cromo, vanadio, titanio, tantalio, molibdeno, zirconio,hafnio y tungsteno, así como aceros inoxidables [3].A diferencia de lo que ocurre en el niquelado químico normal, en los baños de niqueladoquímico compuestos, resultan críticos, para efectos de la estabilidad de la solución y laeficiencia del proceso: el control del pH, el adecuado nivel de agitación y la presencia deestabilizadores y activadores en mayor cantidad en la solución.La mayor aplicación de los recubrimientos químicos compuestos es la de combatir el desgaste.La dureza de este tipo de recubrimientos depende de la matriz y de la resistencia adicionalproporcionada por las partículas y también se incrementa con la aplicación de tratamientostérmicos.En cuanto a la resistencia al desgaste, esta es función de diversos factores, particularmentedel tamaño de la partícula y la fracción en volumen de la fase dispersada, dureza de laspartículas y la matriz y de la compatibilidad entre la fase dispersada y la matriz.Comparado con los recubrimientos compuestos electrolíticos experimentan menor desgaste,lo cual se atribuye a la mayor dureza de las partículas, pero sobre todo a una mejor unión entrelas partículas y la matriz. Tan fuerte interacción puede ser debida a la nucleación delrecubrimiento de níquel sobre diferentes puntos de la partícula y, adicionalmente, laencapsulación de la partícula por el recubrimiento. En el caso de los recubrimientoselectrolíticos, las partículas son sostenidas únicamente por las salientes.Se ha conseguido ampliar, por ejemplo, la vida útil de moldes para plásticos mediante el usode recubrimientos químicos Ni-P-SiC (figura 2); como dados de forja empleados para lamanufactura de piezas hechas de materiales compuestos, han incrementado hasta tres vecessu vida útil mediante estos revestimientos. Ventajas similares se han reportado sobre tornillospara extrusión de polímeros o partes de bisagras de puertas de coche. Por otro lado,recubrimientos químicos Ni-P-Diamante se han empleado para mejorar la resistencia aldesgaste de diversas herramientas [4].9
Figura 3. Inserto para torno de controlnumérico de acero inoxidable conrecubrimiento Ni-P-Diamante.Figura 2. Molde para inyección de plásticoshecho de acero con recubrimiento Ni-P-SiC.La deposición electrolítica de los metales está basada en la descarga catódica de ionesmetálicos. Durante la electrolisis de la solución de la sal metálica, los iones metálicos sonreducidos al metal químico puro en el cátodo que actúa como fuente de electrones, el ánodosirve como pila de electrones. Los electrones requeridos son producidos desde una fuente decorriente externa. En el cátodo:𝑀𝑒 2 𝑧𝑒 𝑀𝑒𝐸𝑐. 4Cuando el ánodo de sacrificio es usado, el proceso reversible ocurre: 2𝑀𝑒 𝑀𝑒 2 𝑧𝑒𝐸𝑐. 5Se emplea para cubrir un objeto con una capa de metal por medio de la electricidad. Se usa lacorriente eléctrica para mover pequeñas partículas o moléculas de metal con una cargaeléctrica positiva a través de una solución química para depositarlos en un objeto o matriz quetiene carga eléctrica negativa.Se logra colocando dentro de un baño de sustancias químicas, una placa del metal delrevestimiento (polo positivo) y el objeto que se requiere revestir (polo negativo). Al pasar lacorriente a través de la solución química los iones salen de la placa de metal, se dirigen haciael objeto y se depositan en su superficie, como se muestra en la figura 4.10
Figura 4. Sistema de una electrodeposición.Del ánodo salen los iones para depositarse en el cátodo, pero cuando el ánodo es insoluble elelectrólito, éste último tiene las sales del metal que se va a recubrir sirve como fuente de iones.Si los ánodos sueltan iones más aprisa de lo que el objeto los recoge, se dice que los ánodostienen una eficiencia demasiado alta. Mientras más tiempo pasa el objeto o matriz dentro delbaño más gruesa es la capa de metal que se forma [5].Para el caso específico del níquel, el desarrollo en todos los aspectos en la deposición deníquel fue asistido por la introducción de mejores ánodos. La importancia de su alta pureza fuecada vez más reconocida en los años 20’s. Sin embargo un ánodo tan puro fue más difícildisolver. Ahora se utilizan cestas de titanio para sostener piezas de ánodos.El níquel primario está disponible en varias formas, como las mostradas en figura 5, cenporelectrodeposición.Independientemente de las formas, hay dos tipos importantes de níquel primario, una de ellases la variedad inactiva y otra es la que se activa por la presencia del azufre. Ambos tipos tienensus protagonistas pero uno u otro cuando estén contenidos en las cestas de titanio hasuplantado en gran parte a los ánodos individuales [6].11
Figura 5. Pellets de níquelLa limpieza del objeto base que va a ser sometido al proceso de electrodeposición consiste enlavarlo, desengrasarlo y desoxidarlo, de tal manera que su superficie prácticamente solocontenga moléculas del metal del que está hecho. Los objetos no metálicos se vuelvenelectroconductivos limpiándolos y enseguida pintándolos con pintura electroconductiva.Antes de la electrodeposición, la preparación del objeto implica lograr áreas eléctricamenteconductivas, proteger de la acción química del baño aquellas partes que no deben serafectadas y hacer que las superficies estén absolutamente limpias. La cera, la laca natural yartificial son los materiales más usados para proteger las partes que no se quieren recubrir.Hay varios pasos en la preparación del objeto para la electrodeposición, éstos son: pulidomecánico, desengrasado, desoxidado (decapado), electrolimpieza y electrorremoción. Elpulido es necesario porque la superficie final tiene la misma forma que después del pulido. Losbaños electrolíticos se preparan mezclando varias sales metálicas, ácidos y álcalis en aguadestilada.El níquel es un metal no corrosivo que se usa normalmente, tanto para fines decorativos (figura6) o también como una base anticorrosiva sobre la que se aplica un depósito de otros metales,particularmente de cromo. Es un material fácil de manejar en la electrodeposición, con laventaja de que produce un acabado duro, terso y brillante.12
Figura 6. Objetos recubiertos por electrodeposición de níquelUno de los baños más utilizados es el baño Watts, tiene distintas variaciones en su formulación,una de las más empleadas es la siguiente:a. Sulfato de níquel300 gramos por litrob. Cloruro de níquel50 gramos por litroc. Ácido bórico35 gramos por litroLa temperatura para el proceso de electrodeposición de níquel va de 40 a 70 C, con unadensidad de corriente de 1 a 5 amperes por centímetro cuadrado de superficie del cátodo. Serequiere agitación continua del electrolito. Un buen depósito se tiene entre los 5 y los 15minutos de exposición, aunque pueden hacerse depósitos gruesos de varias horas.Cuando el depósito resulta rayado, como arrugado, se debe a falta de agitación. Los depósitosrugosos se deben a impurezas en el electrolito, el cual se deberá filtrar. Los depósitos conpicaduras se presentan por utilizar una corriente excesiva. Un depósito con adhesión pobre,se debe a interrupciones en la corriente o a falta de limpieza en el objeto Una posiblemodificación al baño se logra agregando al electrolito abrillantadores comerciales, siguiendolas instrucciones de los fabricante [5].13
Las propiedades de los depósitos de niquelado químico son muy diferentes a los deelectrodeposición. Esto es debido al mecanismo de deposición totalmente diferente y a lapresencia de fósforo o boro en el depósito.Todas las propiedades funcionales de los depósitos Ni-P o Ni-B dependen en mayor o menorgrado en la composición del baño y las condiciones de deposición. Los siguientes hechosenlistados reflejan esta relación:1. Las propiedades de los depósitos de niquelado químico depende de las condiciones dedeposición, en estructura atómica y microestructura.2. El rango de propiedades de los depósitos de niquelado químico es grande y despuésde un tratamiento de color, se hace más grande aún.3. Muchas de las propiedades asignadas al depósito son el resultado de la combinacióndel sustrato y el depósito.Dependen en la aplicación particular, una o más de las propiedades del depósito seráespecialmente importante y la selección del tipo de niquelado químico y las condiciones deldepósito serán seleccionadas certeramente. Apariencia y brilloEn contraste con la electrodeposición de níquel, muchos de los depósitos lucen como acerobrillante (plateado). Por su alta resistencia al desgaste, éstos retienen su brillo por más tiempoque una electrodeposición. En términos de color no existen diferencias apreciables entre losdistintos depósitos químicos.El brillo de un depósito puede ser juzgado por la claridad con la cual una imagen de un objetoes reflejada. Tal reflexión es caracterizada en términos de su intensidad relativa a la luzincidente (porcentaje de reflectancia) como función de la longitud de onda. Hay una compleja14
relación matemática entre el brillo y la morfología del depósito sobre un rango entre 20 a 200nm. Espesor del depósitoEl espesor de un depósito químico de níquel no es, en sí mismo, una propiedad aunque puededeterminar en gran medida la calidad y utilidad de tal recubrimiento.Una vez que la reacción de cementación ha iniciado el mecanismo de deposición (inmersión –tiempo efectivo), el espesor del depósito está dado por el producto:𝑡𝑎𝑠𝑎 𝑑𝑒 𝑑𝑒𝑝𝑜𝑠𝑖𝑐𝑖ó𝑛 𝑡𝑖𝑒𝑚𝑝𝑜 𝑑𝑒 𝑑𝑒𝑝𝑜𝑠𝑖𝑐𝑖ó𝑛Una de las principales ventajas del niquelado químico es el hecho de que el espesor del metaldepositado es uniforme sobre toda la superficie del sustrato, independientemente de su formao geometría; la figura 7 y la figura 8 muestran una comparación esquemática de la forma delespesor entre depósitos químicos y electrodepósitos.Figura 7. Esquema del espesor de unrecubrimiento por medio de un depósito químicoFigura 8. Esquema del espesor de unrecubrimiento por medio de unaelectrodeposición15
AdherenciaLa utilidad de un material compuesto (recubrimiento – sustrato) es restringida en la medida enque la adherencia del depósito esté intacta. Un revestimiento intacto implica, en el caso desustratos metálicos, que una unión verdadera metal a metal debe formarse entre el depósito yel metal base. En tales casos, la adherencia medida por la prueba Pull-Off, es del mismo ordende magnitud como la resistencia a la tracción de la más débil de los metales.La adherencia del niquelado químico en materiales no conductores tal como plásticos ocerámicos depende en incrustación mecánica asociada a las fuerzas de Van de Waals yfuerzas de enlace heteropolar. La fuerza de adherencia en estos casos es de alrededor deorden de magnitud menor que para la unión metal a metal: En ambos casos, no obstante, lafuerza de adherencia principalmente depende del pretratamiento del sustrato. DensidadEn la siguiente tabla (Tabla 4) se muestra el valor aproximado de la densidad dependiendo delporcentaje del fósforo en el recubrimiento según las normas DIN e ISO.Tabla 4. Relación entre la cantidad de fósforo en el depósito y el valor aproximado de su densidad [2]Contenido de fósforo P (wt%)4689101212.5Densidad (g/cm3)Norma DINNorma ISO 452750966--8.5 0.28.08.3 0.2--8.1 0.2--7.85--
c. La tasa de deposición es usualmente entre 10 a 25 μm/ h. d. Aparte de la composición del baño, la tasa de deposición es estrechamente dependiente de la temperatura, pH y con la edad del baño. Los reguladores, complejantes, aceleradores y estabilizadores añadidos a las formulaciones para asegurar la tasa de