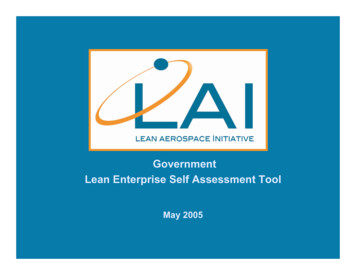
Transcription
GovernmentLean Enterprise Self Assessment ToolMay 2005
What Is the Lean Enterprise SelfAssessment Tool (LESAT)? A tool for self-assessing the presentstate of “leanness” of an enterpriseand its readiness to change Comprised of capability maturitymodel for assessing (1) Enterprise leadership(2) Life cycle and enabling processes(3) Enabling infrastructure LESAT supports both Source: Lean Aerospace Initiative, MIT 2001lean.mit.edu “As- Is” AnalysisAND“To-Be” Vision 2005 Massachusetts Institute of Technology shields/May 05 - 2
Government Lean EnterpriseSelf-Assessment ToolLESAT revised making it moreappropriate for governmentorganizational use Background: Review of LESAT relative to SPOoperation indicated 60-70% ofLESAT usable in governmentcontext Developed with small team Primary focus for use is: SPOs Government organizations withmultiple functions needed to fulfillmissionSource: Lean Aerospace Initiative, MIT 2001 as modified by MIT on 5/15/05Successfully tested with Global Hawk& C-17 SPOslean.mit.edu 2005 Massachusetts Institute of Technology shields/May 05 - 3
Lean Transformation Requiresan Enterprise ApproachExtended EnterpriseCore EnterpriseUpstreamSupply Chainlean.mit.eduDirect CustomersDirect ate FunctionsCorporate cle Serviceand SupportSocietyAcademia 2005 Massachusetts Institute of Technology shields/May 05 - 4
Perspectives on Assessment Most LAI members have launched “lean changeinitiatives”Many have used LAI’s Transition to Lean (TTL)RoadmapExperience with TTL led early adopters to ask: How lean are we? How do we know how much progress we have made?Where should we focus next?LESAT is intended to address these questionslean.mit.edu 2005 Massachusetts Institute of Technology shields/May 05 - 5
LESAT Section I Links Directlywith Enterprise TTLSection I:Lean Transformation/Leadership Practices directly linked to enterprise Transition to Lean Model (TTL)Assesses the following elements: Strategic integration Leadership and commitment Value stream analysis and balancing Change management Structure and systems Lean transformation planning, execution andmonitoringlean.mit.edu 2005 Massachusetts Institute of Technology shields/May 05 - 6
Enterprise Level RoadmapI.BI.BEntry/Re-entryCycleDecision toPursueEnterpriseTransformationI.AI.AFocus on the ValueStreamAdopt LeanParadigm Build Vision Convey Urgency Foster Lean Learning Make the Commitment Obtain Senior ision Map Value Stream Internalize Vision Set Goals & Metrics Identify & Involve KeyStakeholdersDetailedLeanVisionDevelop Lean Structure &Behavior Organize for Lean Implementation Identify & Empower Change Agents Align Incentives Adapt Structure & Systems EnvironmentalCorrectiveAction IndicatorsI.GI.GShort Term CycleFocus on ContinuousImprovementDetailedCorrective ActionIndicators Monitor Lean Progress Nurture the Process Refine the Plan Capture & Adopt New KnowledgeOutcomes onEnterpriseMetricslean.mit.eduLong Term meworkCreate & RefineTransformation Plan Identify & Prioritize Activities Commit Resources Provide Education & Training Implement Lean Initiatives Develop Detailed Plans Implement Lean ActivitiesEnterpriseLevelTransformationPlan 2005 Massachusetts Institute of Technology shields/May 05 - 7
LAI Process Architecture Viewof the Lean EnterpriseLife Cycle ProcessesEnabling InfrastructureProcessesEnterprise LeadershipProcesseslean.mit.eduSource: Lean Aerospace Initiative, MIT 2001 2005 Massachusetts Institute of Technology shields/May 05 - 8
LESAT is Consistent with a ProcessArchitecture View of the Lean EnterpriseLESATSection IILife Cycle Processes(Source of Value)LESATSection IIIEnabling InfrastructureProcesses(Supporting Role)LESATSection IEnterprise LeadershipProcesses(Transformation Enabler)Source: Lean Aerospace Initiative, MIT 2001lean.mit.edu 2005 Massachusetts Institute of Technology shields/May 05 - 9
Research Supported CausalRelations in Lean EnterpriseTransformationLife Cycle Processes(LESAT Sec II)EnablesLeads,EnablesLeads,EnablesEnabling InfrastructureProcesses(LESAT Sec III)Enterprise LeadershipProcesses(LESAT Section I)lean.mit.edu 2005 Massachusetts Institute of Technology shields/May 05 - 10
LESAT Structure is Consistent withEnterprise ArchitectureLife Cycle ProcessesEnabling InfrastructureProcessesEnterprise LeadershipProcessesSection ISection IISection IIITransformation eThe focus is onlean practices andprocesses that aredeveloped andmaintained at thetop level of theenterprise to guideits lean activities.LifeThese processesresult in valuedeliveryto theCyclecustomer andstakeholders overtheProcesseslife of theproduct or service.These enablingprocesses providesupporting servicesto otherorganizational unitswhom they serve asinternal customersSource: Lean Aerospace Initiative, MIT 2001lean.mit.edu 2005 Massachusetts Institute of Technology shields/May 05 - 11
Lean Enterprise Practices There are 55 lean enterprise practices in the assessment,divided amongst the three major sections Section 1 Leadership/Transformation (28 practices)Section 2 Lifecycle Processes (19 Practices)Section 3 Enabling Infrastructure (8 Practices) Each practice is assessed on a capability maturity scale of1 to 5 There is a practice maturity definition for every maturitylevel in every practice, provided on a maturity matrixassessment sheetlean.mit.edu 2005 Massachusetts Institute of Technology shields/May 05 - 12
Maturity Level DefinitionsLeanMaturationWorld ClassLeast Capablelean.mit.eduLevel 5Recognized Best Practice TransformerLevel 4Continuous Improvement ReformerLevel 3Systematic Approach PerformerLevel 2General Awareness AdopterLevel 1Minimal Awareness Traditional 2005 Massachusetts Institute of Technology shields/May 05 - 13
Generic Capability Maturity Levels(Facilitator’s Guide, pp.13)Level 5Exceptional, well-defined, innovative approach is fully deployedacross the extended enterprise (across internal and externalvalue streams); recognized as best practice.Level 4On-going refinement and continuous improvement acrossthe enterprise; improvement gains are sustained.Level 3A systematic approach/methodology deployed in varyingstages across most areas; facilitated with metrics; goodsustainment.Level 2General awareness; informal approach deployed in a fewareas with varying degrees of effectiveness and sustainment.Level 1Some awareness of this practice; sporadic improvementactivities may be underway in a few areas.lean.mit.edu 2005 Massachusetts Institute of Technology shields/May 05 - 14Source: U.S. and U.K. Lean Aerospace Initiative, 2001
What can LESAT Do? Simple, easy to use by enterprise leadership Ability to accommodate both single and aligned organizations(gov’t-contractor, gov’t-gov’t) Can be integrated with an enterprise change initiative(Enterprise Transition to Lean Roadmap) Directly supports your strategic planningFocuses on lean attributes and interactionsTests alignment with enterprise planningProvides guidance for “next steps” Gap analysis capability Easy way to capture change opportunitiesCan be repeated to measure progresslean.mit.edu 2005 Massachusetts Institute of Technology shields/May 05 - 15
Methodology for Employing LESAT(Description - Facilitator’s Guide pp.21)LESATStep 1: Facilitate a meeting to introduce the tool.Identify and hear from the enterprise leader andlean championsStep 2: Enterprise leaders and staff conductLESAT assessment. Facilitator answers questionsand compiles data for leadership reviewStep 3: Leadership reconvenes to jointlyreview results of present maturity levelStep 4: Leadership identifies andagrees on actionable itemsLean Journeylean.mit.eduStep 5: Team is formed to developaction plans and prioritize resourcesfor lean enterprise improvement 2005 Massachusetts Institute of Technology shields/May 05 - 16
Generic LESAT Maturity MatrixTemplate(blue text changes for each practice, green text entered by assessor for each practice)Section, Group # and Group Name: Brief description of this Group number. In Section I, the Group isone of the Primary Activities from the Transition-to-Lean (TTL) Roadmap (blue)DiagnosticQuestionsLP#1.0 Generic questions regarding the perform ance of the enterprise relative to this Group of practices(blue)Capability LevelsLeanPracticesLevel 1A specific leanpracticeassociatedw ith this GroupSound bitphrase (blue)Level 2Level 3Level 4Level 5Statem entdescribing littleaw areness ofthis leanpractice (blue)CDStatem entdescribingw orld-classbehavior forthis leanpractice (blue)CDCDCDCDLean IndicatorsOutcom es and lean behaviors that an enterprise w ill exhibit as it proceeds on its Leantransform ation(blue)EvidenceSupporting data utilized in assessing the current capability level of the Enterprise on thislean practice (green)OpportunitiesInputs to plans of action to leverage opportunities or to m ove to the desired level ofcapability (green)lean.mit.eduSource: U.S. and U.K. Lean Aerospace Initiative, 2001 2005 Massachusetts Institute of Technology shields/May 05 - 17
LESAT Section ISection ITransformation /LeadershipThe focus is onlean practices andprocesses that aredeveloped andmaintained at thetop level of theenterprise to guideits lean activities.lean.mit.eduSection IISection IIILifecycleEnablingProcessesInfrastructure I.AEnterprise StrategicPlanning I.B Adopt the Lean ParadigmLifeThese processesThese enabling I.CFocusontheValue Streamresult in valueprocessesprovide I.DDevelopLeanStructureand Behaviordeliveryto thesupporting servicesCycle I.E CreateTransformation Plancustomerand and Refineto other I.F ImplementInitiatives unitsstakeholdersover LeanorganizationalProcessesthe I.Glife ofthe on Continuouswhom theyImprovementserve asFocusproduct or service.internal customers 2005 Massachusetts Institute of Technology shields/May 05 - 18
LESAT Section I - 28 Lean PracticesI.A. Enterprise Strategic PlanningI.A.1 Integration of Lean in strategic planningprocessI.A.2 Focus on customer valueI.A.3 Leveraging the extended enterpriseI.B. Adopt Lean ParadigmI.B.1 Learning and education in “Lean” forenterprise leadersI.B.2 Senior management commitmentI.B.3 Lean enterprise visionI.B.4 A sense of urgencyI.C. Focus on the Value StreamI.C.1 Understanding current value streamI.C.2 Enterprise flowI.C.3 Designing future value streamI.C.4 Performance measuresI.D Develop Lean Structure and BehaviorI.D.1 Enterprise organizational orientationI.D.2 Relationships based on mutual trustI.D.3 Open and timely communicationslean.mit.eduI.D.4 Employee empowermentI.D.5 Incentive alignmentI.D.6 Innovation encouragementI.D.7 Lean change agentsI.E. Create & Refine Transformation PlanI.E.1 Enterprise-level Lean transformation planI.E.2 Commit resources for LeanimprovementsI.E.3 Provide education and trainingI.F. Implement Lean InitiativesI.F.1 Development of detailed plans based onenterprise planI.F.2 Tracking detailed implementationI.G. Focus on Continuous ImprovementI.G.1 Structured continuous improvementprocessesI.G.2 Monitoring lean progressI.G.3 Nurturing the processI.G.4 Capturing lessons learnedI.G.5 Impacting enterprise strategic planning 2005 Massachusetts Institute of Technology shields/May 05 - 19
Example LESAT Practice- I.B Adopt Lean Paradigm I.B. Adopt Lean Paradigm - Transitioning to lean requires a significant modification to the business model of the enterprise.It is imperative that the enterprise leadership understands and buys into the lean paradigm since they will be required to createa vision for doing business, behaving and seeing value in fundamentally different ways.DiagnosticQuestionsLP#I.B.3. Do enterprise leaders and senior managers understand the lean paradigm at the enterprise level?Do all senior leaders and management enthusiastically support a transformation to lean?Has a common vision of lean been communicated throughout the enterprise and w ithin the extended enterprise?Has a compelling case been developed for the Lean transformation?LeanPracticesCapability LevelsLevel 1Level 2Level 3Level 4Level 5LeanEnterpriseVisionNew mentalmodel of theenterpriseSenior leadershave varyingvision of lean,from none tow ell-defined.Senior leadersadopt commonvision of lean.Lean vision hasbeen communicatedand is understood bymost employees.Common visionof lean is sharedby the extendedenterprise.Stakeholders haveinternalized the leanvision and are an activepart of achieving it.Lean Indicators The role that lean plays in achieving the vision is clearly defined The vision has been communicated to all levels and has extensive buy-in by most employees. The vision incorporates a new mental model of how the company w ould act and behave according toCDCDCDCDClean principles and practicesEvidenceOpportunitieslean.mit.eduSource: U.S. and U.K. Lean Aerospace Initiative, 2001 2005 Massachusetts Institute of Technology shields/May 05 - 20D
Diagnostic Questions forI.B - Adopt the Lean ParadigmI.B. Adopt Lean Paradigm - Transitioning to lean requires a significant modification to the business model of the enterprise.It is imperative that the enterprise leadership understands and buys into the lean paradigm since they will be required to createa vision for doing business, behaving and seeing value in fundamentally different ways.DiagnosticQuestionsLP#I.B.3. Do enterprise leaders and senior managers understand the lean paradigm at the enterprise level?Do all senior leaders and management enthusiastically support a transformation to lean?Has a common vision of lean been communicated throughout the enterprise and w ithin the extended enterprise?Has a compelling case been developed for the Lean transformation?LeanPracticesCapability LevelsLevel 1Level 2Level 3Level 4Level 5LeanEnterpriseVisionNew mentalmodel of theenterpriseSenior leadershave varyingvision of lean,from none tow ell-defined.Senior leadersadopt commonvision of lean.Lean vision hasbeen communicatedand is understood bymost employees.Common visionof lean is sharedby the extendedenterprise.Stakeholders haveinternalized the leanvision and are an activepart of achieving it.Lean Indicators The role that lean plays in achieving the vision is clearly defined The vision has been communicated to all levels and has extensive buy-in by most employees. The vision incorporates a new mental model of how the company w ould act and behave according toCDCDCDCDClean principles and practicesEvidenceOpportunitieslean.mit.eduSource: U.S. and U.K. Lean Aerospace Initiative, 2001 2005 Massachusetts Institute of Technology shields/May 05 - 21D
Diagnostic Questions forI.B - Adopt the Lean Paradigm Do enterprise leader and senior managers understand the leanparadigm at the enterprise level? Have all senior managers made a commitment toenthusiastically support a transformation to lean? Has a common vision of lean been communicated throughoutthe enterprise and within the extended enterprise? Has a compelling case been developed for the leantransformation?lean.mit.edu 2005 Massachusetts Institute of Technology shields/May 05 - 22
Maturity Definitions for PracticeI.B.3 - Lean Enterprise VisionI.B. Adopt Lean Paradigm - Transitioning to lean requires a significant modification to the business model of the enterprise.It is imperative that the enterprise leadership understands and buys into the lean paradigm since they will be required to createa vision for doing business, behaving and seeing value in fundamentally different ways.DiagnosticQuestionsLP#I.B.3. Do enterprise leaders and senior managers understand the lean paradigm at the enterprise level?Do all senior leaders and management enthusiastically support a transformation to lean?Has a common vision of lean been communicated throughout the enterprise and w ithin the extended enterprise?Has a compelling case been developed for the Lean transformation?LeanPracticesCapability LevelsLevel 1Level 2Level 3Level 4Level 5LeanEnterpriseVisionNew mentalmodel of theenterpriseSenior leadershave varyingvision of lean,from none tow ell-defined.Senior leadersadopt commonvision of lean.Lean vision hasbeen communicatedand is understood bymost employees.Common visionof lean is sharedby the extendedenterprise.Stakeholders haveinternalized the leanvision and are an activepart of achieving it.Lean Indicators The role that lean plays in achieving the vision is clearly defined The vision has been communicated to all levels and has extensive buy-in by most employees. The vision incorporates a new mental model of how the company w ould act and behave according toCDCDCDCDClean principles and practicesEvidenceOpportunitieslean.mit.eduSource: U.S. and U.K. Lean Aerospace Initiative, 2001 2005 Massachusetts Institute of Technology shields/May 05 - 23D
Maturity Definitions for PracticeI.B.3 - Lean Enterprise VisionI.B.3 Lean Enterprise Vision - new mental model of the enterpriseLevel 5Stakeholders have internalized the lean vision & are anactive part of achieving itLevel 4Common vision of lean is shared by the extendedenterpriseLevel 3Lean vision has been communicated and is understoodby most employeesLevel 2Senior leaders adopt common vision of leanLevel 1Senior leaders have varying visions of lean, from none towell-definedSource: U.S. and U.K. Lean Aerospace Initiative, 2001lean.mit.edu 2005 Massachusetts Institute of Technology shields/May 05 - 24
Lean Indicators for PracticeI.B.3 - Lean Enterprise VisionI.B. Adopt Lean Paradigm - Transitioning to lean requires a significant modification to the business model of the enterprise.It is imperative that the enterprise leadership understands and buys into the lean paradigm since they will be required to createa vision for doing business, behaving and seeing value in fundamentally different ways.DiagnosticQuestionsLP#I.B.3. Do enterprise leaders and senior managers understand the lean paradigm at the enterprise level?Do all senior leaders and management enthusiastically support a transformation to lean?Has a common vision of lean been communicated throughout the enterprise and w ithin the extended enterprise?Has a compelling case been developed for the Lean transformation?LeanPracticesCapability LevelsLevel 1Level 2Level 3Level 4Level 5LeanEnterpriseVisionNew mentalmodel of theenterpriseSenior leadershave varyingvision of lean,from none tow ell-defined.Senior leadersadopt commonvision of lean.Lean vision hasbeen communicatedand is understood bymost employees.Common visionof lean is sharedby the extendedenterprise.Stakeholders haveinternalized the leanvision and are an activepart of achieving it.Lean Indicators The role that lean plays in achieving the vision is clearly defined The vision has been communicated to all levels and has extensive buy-in by most employees. The vision incorporates a new mental model of how the company w ould act and behave according toCDCDCDCDClean principles and practicesEvidenceOpportunitieslean.mit.eduSource: U.S. and U.K. Lean Aerospace Initiative, 2001 2005 Massachusetts Institute of Technology shields/May 05 - 25D
Lean Indicators for PracticeI.B.3 - Lean Enterprise Vision The role that lean plays in achieving the vision is clearlydefined The vision has been communicated to all levels andhas extensive buy-in by most employees The vision incorporates a new mental model of how thecompany would act and behave according to leanprinciples and practiceslean.mit.edu 2005 Massachusetts Institute of Technology shields/May 05 - 26
LESAT Section IISection ISection IISection IIITransformation eThe focus is onlean practices andprocesses that aredeveloped andmaintained at thetop level of theenterprise to guideits lean activities.lean.mit.eduLifeThese processesresult in valuedeliveryto theCyclecustomer andstakeholders overtheProcesseslife of theproduct or service.Theseenablingthe Enterprise II.A Set-upprocessesprovide II.B BuildRelationshipssupportingservices II.C Developthe Planto other II.D. Implement the Planorganizational units II.E omers 2005 Massachusetts Institute of Technology shields/May 05 - 27
LESAT Section IISection II: Life Cycle ProcessesAssess: Enterprise level core processes Capability to use resourcesProgram ManagementRelationship DevelopmentRequirements DefinitionLean Behavior throughout the Value StreamAlignment of ExpectationsService, Support and SustainabilityKey integrative practiceslean.mit.edu 2005 Massachusetts Institute of Technology shields/May 05 - 28
LESAT Section II - 19 Lean PracticesII.A.Set-up the Enterprise II.A.1 Leverage Lean capability for newopportunities II.A.2 Optimize the capability and utilization ofassets II.A.3 Provide capability to manage risk, cost,schedule and performance II.A.4 Allocate resources for program/projectdevelopment effortsII.B. Build Relationships II.B.1 Define and develop relationships withstakeholders Optimize the relationship Foster innovation and knowledge-sharingII.C. Develop the Plan IICB.1 Establish a requirements definitionprocess to optimize lifecycle value II.C.2 Capture data from the extended enterpriseto optimize future requirements definitions II.C.3 Incorporate stakeholder value into designof products and processes II.C.4 Incorporate downstream stakeholdervalues into products and processes II.C.5 Create a multidisciplinary approachlean.mit.eduII.D.Implement the Plan II.D.1Utilize knowledge and capability indecision making II.D.2 Foster lean behavior throughout the valuestream II.D.3 Align customer requirements andexpectations with the extended enterprisecapabilities II.D.4 Transition product/service to thecustomer in a lean fashionII.E. Learn, Improve and Sustain II.E.1 Enhance value of delivered products andservices to customers and the enterprise II.E.2Provide post delivery service, support andsustainability II.E.3 Maintain challenge of existing processes 2005 Massachusetts Institute of Technology shields/May 05 - 29
Example LESAT Practice- II.D Implement the Plan II. D. Im plem ent the Plan - The plan must be designed and managed according to the principles and practices of the lean paradigmDiagnosticQuestions Is lean knowledge and capability regarded as a strategic capability?Has enterprise strategy been aligned to capitalize on lean capability?Are products pulled in accordance with customer demand in real-time?Are production schedules and capacity considered prior to making a contract commitment?Have the enterprise processes been ordered and adapted for flow?Is the customer ready to effectively use and deploy the product/service when it is received?Is there a process to identify and eliminate bottlenecks in the work flow?Capability LevelsLP#Lean PracticesII.D.2Foster Lean Behav iorThroughout the ValueStreamPromoting stakeholderinnovation and flexibilityLevel 1Level 2Processes andrelationshipsbased onpast/historicalnorms.There are pocketswithin the valuestream where theobjectives of thetask, program ormission influencecreation of newprocesses tomaximize value.CLean Indicators(Examples)DCLevel 3DAll members of thevalue stream haveestablishedprocesses that fosteropen sharing ofinformation with “nospin” assessmentsCDLevel 4Level 5Senior leadershipinvolvement allowsstakeholders todevelop innovativeapproaches thatare flexible tochangingconditions.Stakeholders alongthe vlaue stream areempowered todevelop flexible andinnovative processesbased on valuedelivered to theextended enterprise.CDC Conversion to lean has freed up resources for re-deployment. Bottlenecks have been identified and eliminated to allow processes to flow seamlessly. Work is performed only when “pulled” from subsequent “customers” in the value chain.Ev idenceOpportunitieslean.mit.eduSource: U.S. and U.K. Lean Aerospace Initiative, 2001 2005 Massachusetts Institute of Technology shields/May 05 - 30D
Diagnostic Questions for- II.D Implement the Plan II. D. Im plem ent the Plan - The plan must be designed and managed according to the principles and practices of the lean paradigmDiagnosticQuestions Is lean knowledge and capability regarded as a strategic capability?Has enterprise strategy been aligned to capitalize on lean capability?Are products pulled in accordance with customer demand in real-time?Are production schedules and capacity considered prior to making a contract commitment?Have the enterprise processes been ordered and adapted for flow?Is the customer ready to effectively use and deploy the product/service when it is received?Is there a process to identify and eliminate bottlenecks in the work flow?Capability LevelsLP#Lean PracticesII.D.2Foster Lean Behav iorThroughout the ValueStreamPromoting stakeholderinnovation and flexibilityLevel 1Level 2Processes andrelationshipsbased onpast/historicalnorms.There are pocketswithin the valuestream where theobjectives of thetask, program ormission influencecreation of newprocesses tomaximize value.CLean Indicators(Examples)DCLevel 3DAll members of thevalue stream haveestablishedprocesses that fosteropen sharing ofinformation with “nospin” assessmentsCDLevel 4Level 5Senior leadershipinvolvement allowsstakeholders todevelop innovativeapproaches thatare flexible tochangingconditions.Stakeholders alongthe vlaue stream areempowered todevelop flexible andinnovative processesbased on valuedelivered to theextended enterprise.CDC Conversion to lean has freed up resources for re-deployment. Bottlenecks have been identified and eliminated to allow processes to flow seamlessly. Work is performed only when “pulled” from subsequent “customers” in the value chain.Ev idenceOpportunitieslean.mit.eduSource: U.S. and U.K. Lean Aerospace Initiative, 2001 2005 Massachusetts Institute of Technology shields/May 05 - 31D
Diagnostic Questions forII.D - Implement the Plan Is lean knowledge and capability regarded as a strategiccapability? Has enterprise strategy been aligned to capitalize on leancapability? Are products pulled in accordance with customer demand inreal-time? Are production schedules and capacity considered prior tomaking a contract commitment? Have the enterprise processes been ordered and adapted forflow? Is the customer ready to effectively use and deploy theproduct/service when it is received? Is there a process to identify and eliminate bottlenecks in thework flow?lean.mit.edu 2005 Massachusetts Institute of Technology shields/May 05 - 32
Maturity Definitions for Practice II.D.2 II.D.2 Foster Lean Behavior throughout the Value StreamII. D. Im plem ent the Plan - The plan must be designed and managed according to the principles and practices of the lean paradigmDiagnosticQuestions Is lean knowledge and capability regarded as a strategic capability?Has enterprise strategy been aligned to capitalize on lean capability?Are products pulled in accordance with customer demand in real-time?Are production schedules and capacity considered prior to making a contract commitment?Have the enterprise processes been ordered and adapted for flow?Is the customer ready to effectively use and deploy the product/service when it is received?Is there a process to identify and eliminate bottlenecks in the work flow?Capability LevelsLP#Lean PracticesII.D.2Foster Lean Behav iorThroughout the ValueStreamPromoting stakeholderinnovation and flexibilityLevel 1Level 2Processes andrelationshipsbased onpast/historicalnorms.There are pocketswithin the valuestream where theobjectives of thetask, program ormission influencecreation of newprocesses tomaximize value.CLean Indicators(Examples)DCLevel 3DAll members of thevalue stream haveestablishedprocesses that fosteropen sharing ofinformation with “nospin” assessmentsCDLevel 4Level 5Senior leadershipinvolvement allowsstakeholders todevelop innovativeapproaches thatare flexible tochangingconditions.Stakeholders alongthe vlaue stream areempowered todevelop flexible andinnovative processesbased on valuedelivered to theextended enterprise.CDC Conversion to lean has freed up resources for re-deployment. Bottlenecks have been identified and eliminated to allow processes to flow seamlessly. Work is performed only when “pulled” from subsequent “customers” in the value chain.Ev idenceOpportunitieslean.mit.eduSource: U.S. and U.K. Lean Aerospace Initiative, 2001 2005 Massachusetts Institute of Technology shields/May 05 - 33D
Maturity Definitions for Practice II.D.2II.D.2 Foster Lean Behavior throughout the Value Stream - Promotingstakeholder innovation and flexibilityLevel 5Stakeholders along the value stream are empowered to develop flexible andinnovative processes based on value delivered to the extended enterprise.Level 4Senior leadership involvement allows stakeholders to develop innovativeapproaches that are flexible to changing conditions.Level 3All members of the vlaue stream have established processes that foster opensharing of information with “no spin” assessments.Level 2There are pockets within the value stream where the objective of the task,program, or mission influence creation of new processes to maximize value.Level 1Processes and relationships are established based on past/historicalnormslean.mit.edu 2005 Massachusetts Institute of Technology shields/May 05 - 34
Example LESAT Practice- II.D Implement the Plan II. D. Im plem ent the Plan - The plan must be designed and managed according to the principles and practices of the lean paradigmDiagnosticQuestions Is lean knowledge and capability regarded as a strategic capability?Has enterprise strategy been aligned to capitalize on lean capability?Are products pulled in accordance with customer demand in real-time?A
Enterprise Level Roadmap Entry/Re-entry Cycle Focus on the Value Stream Initial Lean Vision Short Term Cycle Create & Refine Transformation Plan Lean Transformation Framework Adopt Lean Paradigm Enterprise Strategic Planning Focus on Continuous Improvement Outcomes on Enterprise Metrics Implement Lean Initiatives Enterprise Level Transformation .