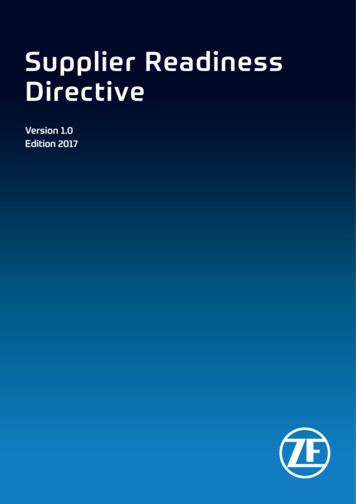
Transcription
Supplier ReadinessDirectiveVersion 1.0Edition 2017
3PrefaceSupplier Readiness is a specialized extension to theAPQP process that is specifically designed to managecomponents with high risk or special priority and theirrespective suppliers through all levels of the GlobalDevelopment and Product Evolution Process (GDPEP).The Supplier Readiness concept is to take a proactiveand collaborative approach to ensure that the identifiedZF suppliers are fully ready to support production onschedule.The goal of this program is to secure the right part, inthe right quantity, in the right quality and at the rightlocation for pre-series, ramp-up and the start of seriesproduction. When properly executed, the SupplierReadiness process allows ZF and the supplier to identifyand address potential issues early in the process,thereby reducing the cost impact and chance of delay.In the event that a supplier is selected for the SupplierReadiness process, the participation is mandatory.The purpose of this manual is to provide a clear andconcise description of the Supplier Readiness processfor current and prospective ZF suppliers.Dr. Michael KarrerHead of Supplier Management ZF Group
Table of Contents01 020304PREFACE1PREFACE1.1 Index of Terms24INTRODUCTIONTO SUPPLIERREADINESS2INTRODUCTION TO SUPPLIERREADINESS52.1 Roles in Readiness Project 62.2 Tools & 53.6SUPPLIER READINESSPROCESS7Technical Review7APQP Kick-off Meeting7Meeting Preparation8Meeting Output9Supplier Readiness ProjectStatus Tracking9SupplyOn (eAPQP) or VIN(PTS)9Milestone Meetings10Change Management10Sub-Supplier Readiness10Run@Rate11Project Closure and ProcessRelease12APPENDIX4APPENDIX4.1 Checklist1313
51.1 Index of TermsAPQPAdvanced Product Quality PlanningPEPProduct Evolution ProcessBoMPPAPBill of MaterialProduction Part Approval ProcessPTSProgram Tracking SystemSDBSourcing Decision BoardRFQSDESOPVINRequest for QuotationSupplier Development EngineerStart of ProductionVendor Information Network
6Supplier Readiness DirectiveIntroduction to Supplier Readiness2 Introduction to Supplier ReadinessThis manual will cover each stage of the SupplierReadiness process shown in the diagram below.There are five meeting types within the SupplierReadiness process (blue boxes):1. Technical Review (for suppliers which arecandidates for nomination)2. APQP Kick-off meeting (for nominated suppliers)3. Regular Milestone Meetings4. Process Release5. Final Project Meeting (optional)In preparation for the Technical Review the supplier isobliged to update the Basic Technical Workbook, provided by ZF Commodity Purchasing.Throughout the APQP process, the status and actionitems are recorded and monitored through ZF’s suppliercommunication portals (SupplyON or VIN).Supplier Readiness ProcessZF SupplierReadiness TeamZF InternalRiskAnalysisSupplierBoM .RFQ.Offer. Short List .Pre-fill lReview (withSuppliers onShort List)Submitupdated BasicTechnicalWorkbook toZF SupplierApproval fromtechnicaland qualityperspectiveOutput:SupplierCommitment to ZFSupplier ReadinessProcessFeasibility check(with feasibility studyand compliance matrix)Open issues andaction planNomination.APQP Kick offSupplierReadinessProject Schedulein SupplyOneAPQP orVIN PTSAPQP Kick Workbook to ZFAPQPKick offMeetingPreparationAPQP Kick-offMeeting Output:Understanding ofproject targetsAgreed projectscheduleOn-site milestonemeetings timelineAgreed Sub-SupplierReadiness processAPQP deliverablesDefined action plansfor open itemsAPQP Execution . SOPStatusTracking &Updates(SupplyOneAPQP or VINPTS)StatusTracking &Updates(SupplyOneAPQP or VINPTS) MilestoneMeetingsOutput:Review of projecttimingReview of theremaining openitemsParts statusStatus of SubSupplier ReadinessProcessRelease Final ProjectMeeting(optional)Output:Successful closure ofthe SupplierReadiness ProjectSummarization oflessons learned
72.1 Roles in Readiness ProjectAs a successful SOP depends on many varied factors,Supplier Readiness requires the expertise of a crossfunctional team involving representatives both from supplier and ZF side. The supplier is expected to providesupport and the appropriate resources to the ZF Supplier Readiness team.2.2 Tools & GuidelinesThere are a number of available tools provided by ZF toassist and guide the supplier through the Supplier Readiness process.Quality Directive QD83The guiding document that outlines the general ZF supplier quality requirements, expectations and processesis the Quality Assurance Directive for Purchased Items,also known as QD83. ZF Group’s standard AdvancedProduct Quality Planning (APQP) is a core element ofSupplier Readiness and is outlined in this publication.Basic Technical WorkbookThe Basic Technical Workbook is a document that shallbe completed prior to the Technical Review Meeting. Itcontains the following elements: Basic Data Sheet (mandatory): information about theproject itself, the milestones and the involved parties. Feasibility study (mandatory): already sent out withthe RFQ. Compliance Matrix (mandatory for high and mediumrisk components): confirmation of feasibility for allitems on the drawing. Sub-Supplier Tree (for high risk components andupon request by ZF): risk assessment for completesupply chain (see Chapter 3.4).A tutorial for working with the Basic Technical Workbook is available upon request.ZF Template for Risk Assessment (VDA MaturityLevel Assurance)This template should be used as standard for evaluationof risks along the supply chain; equivalent templates canalso be accepted.Supplier Readiness ChecklistZF provides a Supplier Readiness Checklist (appendix4.1) to guide the supplier through the process steps ofSupplier Readiness. This checklist will be provided tothe supplier during the Technical Review prior to nomination.ZF Supplier Communication PortalsThe APQP phase of the Supplier Readiness process ismanaged through the electronic communication platforms of ZF, SupplyOn (eAPQP) and VIN (PTS). Suppliers selected for this process will be required to utilizethese tools to track and report the status of the agreedproject milestones.
8Supplier Readiness DirectiveSupplier Readiness Process3 Supplier Readiness ProcessPurpose of the Supplier Readiness Process is to ensure a flawlesslaunch into serial production.3.1 Technical ReviewAfter determination of the components of increased risk, ZF schedules ameeting with the respective suppliers in order to discuss the identified focuspoints. The Basic Technical Workbook will be reviewed and completed inthe Technical Review and pre-development measures will be addressed anddocumented. The output of this meeting shall be a feasibility check, anaction plan in order to close identified gaps and the supplier’s commitmentto the ZF Supplier Readiness process.A completed technical review with an approval from ZF is required for asupplier to be considered for sourcing.3.2 APQP Kick-off MeetingThe APQP Kick-Off meeting is the official start of the APQP executionbetween ZF and the nominated supplier.Meeting PreparationThe APQP Kick-off meeting will be organized by ZF and can be held at thesupplier or at a ZF location. The supplier shall be given advance notice ofthe meeting to allow for adequate preparation. The invitation to this meetingshall be sent by ZF to the supplier and will contain an agenda and thenecessary templates.The following table outlines ZF’s expectations to the supplier with regards tothat preparation:Preparation bySupplierProject OrganizationPart IntroductionMachine and ProcessPlanning Cross-functional team defined Team members’ responsibilitiesdefined Escalation Path defined DFMEA (initial, when applicable) PFMEA (initial) Understanding about part andprocess (derived from releaseddrawings & specifications) Measurement & TestingEquipment Concept (initial) Manufacturing Equipment &Tooling Concept (initial)Identified Items / Actions fromTechnical Review (FeasibilityStudy & Compliance Matrix) Closed action itemsSub-Supplier Readiness Detailed sub-supplier informationProject ScheduleConditions for Process Release Open tasks Initial Project and MilestonePlanning Necessary documentation defined
9Meeting OutputThe expected results of the Kick-off meeting are as follows: Clear understanding of all project targets Agreed project schedule On-site milestone meeting timeline to realize the APQP process,including the integration of the sub-supplier readiness process APQP deliverables Open issue list / action plan Finalization of prioritized sub-supplier structure by updating the SubSupplier Tree with risk categorization.3.3Supplier Readiness Project Status TrackingThe preferred tools for status monitoring of the Supplier Readiness projectare the SupplyOn Project Management module (eAPQP) or VIN (PTS).SupplyOn (eAPQP) or VIN (PTS)The Supplier Readiness project is set up by the Supplier Readiness Manager(ZF Program SDE) in SupplyOn. For suppliers to Division A, APQP will betracked through VIN PTS. Suppliers selected for this process will be requiredto utilize these tools to track and report the status of the project. After eachgate, the work packages will be rated (red, yellow, green) and the ratingresults will be shown in SupplyOn or VIN (PTS) as project status. The projectmembers will be notified automatically by email about status changes ofwork packages.According to the status of work packages, the following measures may betaken per the below chart:Status in SupplyOn/VINRedYellowGreenStatus Tracking Measures(Frequency depends on problem) Status report from supplier Telephone conference Additional on-site visit Status report from supplier Telephone conference No special measures – regularcheck at SR milestone meetingsMilestone MeetingsWithin the Kick-off meeting, milestone meetings and their frequency aredefined to achieve the APQP requirements.Key points of the milestone meetings are: Review project timing Review and resolve any remaining open issuesSupplierReadiness ProjectStatus Tracking
10Supplier Readiness DirectiveSupplier Readiness Process Parts review Sub-supplier Readiness Factory visitChange ManagementDesign changes influence the Supplier Readiness Process in that differentmeasures or process steps may need to be reviewed or repeated. Designchanges will be monitored within the status tracking process. A newfeasibility check is required for each new drawing release.3.4 Sub-Supplier ReadinessResponsibility for sub-supplier APQP remains the responsibility of the directsupplier to ZF. However, the Sub-Supplier Readiness Process helps definerisk and ZF may require additional activities to be carried out to minimiserisk. ZF will identify when the Sub Supplier Readiness process is required.SupplierReadiness ProcessSub-Supplier Readiness ProcessZF InternalRiskAnalysisTechnicalReview (withSuppliers onShort b-SupplierManagement ProcessAPQPKick offMeetingincludingSub-SupplierDevelopment of a Sub-SupplierTree and the correspondingSupplier Risk AssessmentVerification ofSub-SupplierriskassesementPPAPReleaseStart ofProductionReporting on progress in Sub-Supplier APQPProcessAgreedAPQP/PPAPplan fürSub-Suppliers(based on riskassesement)Actionplan/follow-upof sub-tierandZF involvementThe starting point of the Sub-Supplier Readiness process is the Sub-SupplierTree including risk classification, which determines the risk of each subsupplier and creates the critical paths within the Sub-Supplier Tree.Upcoming tasks include identifying and eliminating weaknesses in thesupply chain. In addition it is necessary to track and document sub-supplierstatus and report to ZF on a regular basis. Based on the reporting, ZF mayrequire additional actions (e.g. joint supplier meetings, visits or audits).The ZF supplier remains fully responsible for the performance of the subsupplier, this includes directed suppliers.3.5 Run@RateRun@Rate is a capacity measurement under volume production conditionsthat, at the time of implementation, assists in verifying that the production
11processes of a supplier are capable of supplying products in the agreedvolume and quantity. This process takes into account productionequipment, employees, tools and logistics processes.The Run@Rate must be applied at the bottleneck of the process chain. It isconsidered to be successfully passed if the contracted peak volume over lifetime is verified with production of the required quantity and quality andthere are no significant deviations in the production process. It isconditionally passed if the peak volume in the first 12 months after SOP isverified with production of the required quantity and quality and an agreedcapacity plan with ZF commodity buyer to cover peak volume is available.The supplier is requested to do a self-assessment. However, ZF may decideto execute the assessment on-site at the supplier.3.6 Project Closure and Process ReleaseA formal process release at the end of the APQP is mandatory (e.g. VDA6.3or Launch Readiness Audit). The requirements for the process release willbe communicated to the supplier during the APQP Kick-off meeting.ZF and the supplier may agree to schedule a final project meeting.The aim of this meeting is to evaluate the Supplier Readiness project. Afterthe final project meeting, both ZF and the supplier will have a confirmationof the successful closure of the Supplier Readiness project documented inthe meeting minutes. Lessons learned will likewise be summarized forfurther development.
12Supplier Readiness DirectiveAppendix4 Appendix4.1ChecklistSupplier Readiness ChecklistProject Nr.1.01.11.21.31.42.0Supplier ReadinessPhases/tasksDetailed check of feasibility studyincl. Compliance MatrixAction plan f
4.1 Checklist 13. 5 1.1 Index of Terms APQP Advanced Product Quality Planning BoM Bill of Material PEP Product Evolution Process PPAP Production Part Approval Process PTS Program Tracking System RFQ Request for Quotation SDB Sourcing Decision Board SDE Supplier Development Engineer SOP Start of Production VIN Vendor Information Network. 6 Supplier Readiness Directive Introduction to