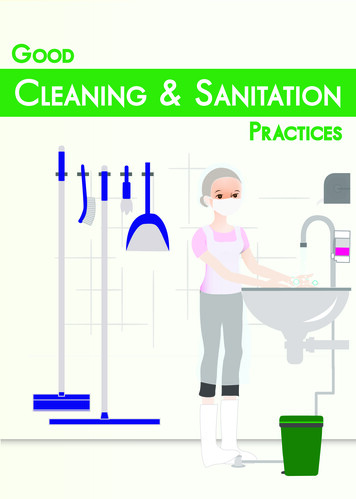
Transcription
C LEAN I N G & S AN ITATIO N
C O NTENTThis publication provides a set of guidelines on good cleaning and sanitation practices for food operators andfood handlers. To manage and reduce the risk of food-borne illnesses, a comprehensive and effectivefood safety management system should be adopted.INTRODUCTIONWhy are Cleaning and Sanitising Important?3Difference between Cleaning and Sanitising4CLEANING & SANITATION PROGRAMMEComponents of a Good Cleaning and Sanitation Programme5Recommended Frequency of Cleaning and Sanitation6Basic Steps for Cleaning and Sanitation7Factors Affecting Cleaning and Sanitising Efficacy8
CLEANING TOOLSRecommended Features of Cleaning Tools10HAND-WASHING FACILITIESWhy is Hand-Washing Important?13Components of Hand-Washing Station148 Hand-Washing Steps15INTERESTING FACTS16DOOGNOIOTTAE Practices A N I TI DSanitationU andTips on GCleaning17S&GSNEICNITACLEP R ACSUMMARY
IntroductionWhy are Cleaning and Sanitising Important?Cleaning and sanitising are important to food safety as many food poisoning casesare associated with inadequate and ineffective sanitation. Generally, surfaces ofequipment, food preparation tables and utensils that come into direct contact withfood should be washed, sanitised and air-dried.Cleaning and sanitation of food establishments are important for the followingreasons:To prevent food poisoning resultingfrom cross contamination between foodcontact surfaces and food.To minimise food wastage due to foodcontamination.To ensure cleanliness of premises at alltimes and create a more pleasant workenvironment.3
IntroductionDifference between cleaning and sanitisingCleaning is the complete removal of dirt and food waste using physical meansand appropriate detergent under recommended conditions.BeforeAfterSanitising is the reduction of the number of microorganisms to safe levels.4
Cleaning & Sanitation ProgrammeComponents of a Good Cleaning and SanitationProgrammeA good cleaning and sanitation programme should be conscientiously carried out:(b) Assign specificpersonnel forspecific task.(a) Identify areas,equipment anditems to be cleanedand sanitised.5(c) Establishmethod, procedureand schedule forcleaning andsanitation.(d) Monitorand verify foreffectiveness.Document step (a)to (d)
Cleaning & Sanitation ProgrammeRecommended Frequency of Cleaning andSanitationAreas identifiedRecommended minimum frequencyWeeklyMonthlyDaily (orafteroperation)General areasFloor and wall next to preparation areaDoorsWindows, ceilings, overhead fixtures(e.g. lighting covers and fans)Production area1Food processing equipmentFood containers, crockery and utensils1Food preparation table1Sinks, taps, gullies2 and drainsExhaust hood, flue and ventilation systemsPersonal hygiene facilitiesHand-washing sink and surrounding area1Toilets1Storage areaRefrigerator/chiller/freezer units and drystorage area which include:Floors & wallsFood containersPalletsRacksInterior & exterior refrigeration fansDelivery transportInterior cabin of delivery truck1Requires sanitising after cleaning2Grease traps are to be maintainedregularly by engaging NEA-licensedgeneral waste collectors.Always Practise:Spot it, Clean it!NowLater6
Cleaning & Sanitation ProgrammeBasic Steps for Cleaning and SanitationStep 1 : pre-rinsePre-rinse to remove the debris fromthe surface, which allows cleaningand sanitising to be carried out moreeffectively.Step 2 : wash surfaces withappropriate cleaning solutionThis can be done by soaking andscrubbing, spraying, foaming or highpressure cleaning.Step 3 : flush/rinse the cleaning compounD froM surfacesIt is important that all food remnants and cleaningcompounds are removed as they would interferewith the sanitising solution and render itineffective.Step 4 : SANITIsEApply sanitising solution, hot water orsteam.7Step 5 : flush/rinse off thesanitising solution(if required)
Cleaning & Sanitation ProgrammeFactors Affecting CLEANING AND SANITISINGEFFICACYcontact timeThere should be adequate contact timebetween the cleaning or sanitising solutionand the surface to be cleaned.temperature of cleaning and sanitising solutionCleaning is more effectivewhen using warm cleaningsolution as the bondsbetween the soil and thesurface are weakened.Hot water ( 77 C)or steam can also beused to sanitise thecontact surfaces.8
Cleaning & Sanitation ProgrammeSTRENGTH APPLIED DURING CLEANINGAdequate strength when appliedappropriately to the contact surfaces,can remove the dirt effectively withoutdamaging the surfaces.TYPE AND CONCENTRATION OFCLEANING AND SANITISING SOLUTIONThe type of cleaning solution used willdepend on the type of food waste.The final concentration of the cleaning andsanitising solution should be diluted asrecommended by the manufacturer.9
Cleaning ToolsRecommended Features of Cleaning ToolsColour-codedVegetables Processing AreaGeneral CleaningMeat Processing AreaSeafood Processing AreaColour-coded cleaning tools enable food handlers to differentiate the tools to beused in different areas of the food establishment. This is to minimisecross-contamination.10
Cleaning ToolsSPECIFICALLY DESIGNED FOR DIFFERENT EQUIPMENT ANDAPPLIANCESCleaning tools which are too abrasive can cause scratches to susceptible foodcontact surfaces. This would increase the risk of bacteria attaching to the scratchesand contaminating food products if not sanitised properly.Use suitable cleaning tools to clean the different types of surfaces.Examples:Brushes with stiff bristles for cleaningsurfaces with tough stains.Brushes with softer bristles to cleanpowdered, dusty surfaces or thingsthat may be susceptible to scratching.Pads are commonly used for cleaningutensils due to their soft and flexiblenature.11
Cleaning Toolsdurable and chemical resistantChoose brushes of good durability as there is a riskof physical contamination if the bristles fall outeasily.CHEMICAL RESISTANCECleaning tools should be made of syntheticmaterials that will not be damaged by cleaningchemicals.Always maintain cleaning toolsin a clean and hygienic conditionRe-usable cloths must be cleaned andsanitised regularly. Replace the cloths withnew ones when necessary.Wet cleaning tools (e.g. mops) should berinsed, washed and sanitised after use.They should be properly dried before storingin a designated place.12
Hand-washing FacilitiesWHY IS HAND-WASHING IMPORTANT?Proper hand-washing is vital in preventing contamination of food by the hands offood handlers. Harmful bacteria and viruses present on the hands of food handlersare reduced by proper hand-washing techniques.Food handlers should wash their hands and wrists immediately:Before engaging infood preparation.After blowing the nose,sneezing or coughing.After using the toilet.When changing tasks.(e.g. when switching between handlingraw and ready-to-eat food to preventcross-contamination)13After engaging in dutiesthat contaminate the hands.(e.g. cleaning duties, disposing trash andhandling money)
Hand-washing FacilitiesCOMPONENTS OF HAND-WASHING STATION432211The taps should preferably be hands-free (e.g. pedal, knee or elbow operated) toprevent the cleaned hands from touching any parts of the hand-washing facilitywhich might result in cross-contamination.2Foot-operated refuse bin3Liquid soap4Disposable paper towels14
Hand-washing Facilities8 Hand-washing steps182Wet hands with clean,running water and applysoap. Rub palms togetherto make lather.Rinse and dry your handswith paper towel.Between the fingers.73Practise the 8hand-washing stepsfor at least20 seconds.Back of your hands.Wrists645FingernailsThumbsBack of fingers.15
Interesting Factsdo you know?Cross-contamination may occur if high-pressure cleaning is used when there is anon-going food processing. This is due to the dispersion of the dirt and bacteria intothe air which might fall back onto the food or work surfaces. Hence, high-pressurecleaning should not be carried out when there is preparation of food.An average hand harbours more than 1000 bacteria per centimetre square. Washinghands thoroughly with soap and water can reduce the amount of bacteria present.Unwashed HandsAfter cold water rinseAfter 20 seconds of 8hand-washing steps usingwater and soap.16
SummaryTIPS ON CLEANING AND SANITATION PRACTICESEstablish a cleaning andsanitation programme andfollow conscientiously.Establish a cleaning and sanitation schedule for thefollowing areas:Floor, wall, doors, windows, ceiling and overhead fixturesFood preparation tables and processing equipmentFood containers, crockery and utensilsExhaust hood, flue and ventilation systemsSinks, taps, gullies and drainsToilets and hand-washing facilitiesStorage areas (e.g. dry store, chiller and freezer)Interior cabin of delivery trucksImprove the efficacy of cleaning andsanitation by considering:Dilution factorTemperatureContact timeStrength applied during cleaning17
SummaryUse cleaning tools that are:Colour-coded to enable users to differentiate thetools to be used in different areas of the foodestablishmentSpecifically designed for different types ofequipment and appliancesDurable and chemical-resistantEasily maintained in a clean and hygienic conditionHand-washing facilities are equippedwith hands-free water tap, liquid soap,disposable paper hand towel andfoot-operated refuse bin.Food handlers should practise the 8hand-washing steps to clean their handsand wrists.18
www.ava.gov.sgwww.nea.gov.sg5 MAXWELL ROAD, #18-00 TOWER BLOCK40 SCOTTS ROAD, #13-00 ENVIRONMENT BUILDINGMND COMPLEX, SINGAPORE 069110SINGAPORE 228231TEL: 6325 7625FAX: 6220 6068TEL: 1800 2255 632 FAX: 6235 2611
Cleaning & Sanitation Programme Pre-rinse to remove the debris from the surface, which allows cleaning and sanitising to be carried out more effectively. Step 1 : pre-rinse This can be done by soaking and scrubbing, spraying, foaming or high pressure cleaning. Step 2 : wash surfaces with appropriate cleaning solution Step 5 : flush/rinse off the