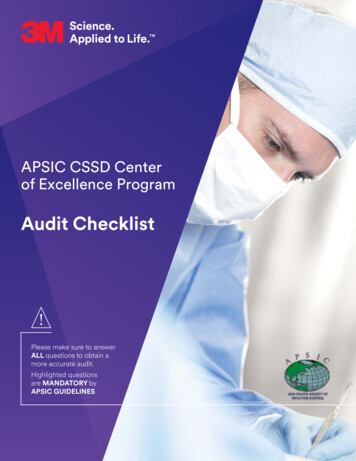
Transcription
APSIC CSSD Centerof Excellence ProgramAudit Checklist!Please make sure to answerALL questions to obtain amore accurate audit.Highlighted questionsare MANDATORY byAPSIC GUIDELINES
Audit ChecklistTable of Contents 2SECTION A: Handling, Collection and Transportof Contaminated Instruments (pages 3-4)SECTION B: Cleaning and Decontamination Processes (pages 5-7)SECTION C: Instrumentation Inspection, Preparation and Packaging (pages 8-11)SECTION D: Sterilisation and Monitoring (pages 12-17)SECTION E: Sterile Storage and Distribution (pages 18-20)SECTION F: Documentation (pages 21-22)SECTION G: Facility Design (pages 23-25)SECTION H: Considerations (pages 26-27)Expert Feedback (page 28)Summary Scores (page 29)
APSIC CSSD Center of Excellence Program Audit ChecklistSECTION A:Handling, Collection and Transport of Contaminated InstrumentsQuestion 1:Reusable items separated from waste atpoint of useNot separatedPartial separationClear separationQuestion 2:Contaminated disposable items are discardedappropriately (including sharps)Not discarded appropriatelyPartial complianceDiscarded appropriately all the timeQuestion 3:Gross soil is removed from instruments at pointof use if immediate transportation not possibleNot removedRemoved sometimesRemoved all the timeQuestion 4:Soiled items should be kept moist(moist towel, enzyme foam or spray product)Items are dryPartially moistMoist all the timeQuestion 5:Secured, dedicated containers are providedfor soiled instrumentsNot availableSometimesAll the timeQuestion 6:Use of puncture resistant, leak-proof containersfor soiled itemsNot availableSometimesAll the timeQuestion 7:Soiled items must be contained duringtransportationNot evidentAttempts madeDone all the time3SECTION A: HANDLING, COLLECTION AND TRANSPORT OF CONTAMINATED INSTRUMENTS continues
APSIC CSSD Center of Excellence Program Audit ChecklistSECTION A:Handling, Collection and Transport of Contaminated Instruments (continued)Question 8:Transportation of soiled instruments avoidshigh (public) traffic areasNot evidentAttempts madeDone all the timeQuestion 9:Transportation carts should be covered andshould prevent items from falling over or offNot doneOccasionally doneDone all the timeQuestion 10:Dedicated elevators (or lifts) with directaccess to decontamination areaNot availableDedicated but not used asplanned all the timeDedicated and used asplanned all the timeQuestion 11:Policy and procedure in place fortransportation of contaminated itemsbetween buildings, if applicableNot availablePolicy exists but not followedPolicy exists and compliedwith all the timeTOTAL:SECTION A:Handling,Collection andTransport ofContaminatedInstruments0 / 160 pointsMANDATORY ITEMS MARKED:0 / 100 (5 items)I completed all questions in this sectionespecially the MANDATORY (highlighted) items.Yes4 Return to Table of ContentsNoProceed to Next Section
APSIC CSSD Center of Excellence Program Audit ChecklistSECTION B:Cleaning and Decontamination ProcessesQuestion 1:Written policies and procedures in place forall cleaning and decontamination processesBoth not availableOne is availableBoth are availableQuestion 2:Instrumentation is disassembled (accordingto manufacturer’s instructions) to expose allsurfaces for cleaningNot doneDone occasionallyDone all the timeQuestion 3:Rigid container systems disassembledaccording to manufacturer instructions(filters, valves and interior baskets)Not doneDone occasionallyDone all the timeQuestion 4:Cleaning agents are used according tomanufacturer’s instructions (dilution andtemperature, etc.)Not doneDone occasionallyDone all the timeQuestion 5:Appropriate manual and mechanical cleaningmethods are used according to manufacturer’sinstructions and IFU’s are accessible todecontamination staffQuestion 6:Appropriate personal protective equipment(PPE) are usedNot doneDone occasionallyDone all the timeNot evidentOccasionally practicedDone all the timeQuestion 7:Appropriate brushes/cleaning implementsdesigned for use on medical devicesare usedNot doneDone occasionallyDone all the time5SECTION B: CLEANING AND DECONTAMINATION PROCESSES continues
APSIC CSSD Center of Excellence Program Audit ChecklistSECTION B:Cleaning and Decontamination Processes (continued)Question 8:Brushes/cleaning implements are eitherdisposable or if reusable, are decontaminatedat least dailyNot evidentDecontaminated irregularlyDecontaminated at least dailyQuestion 9:Monitoring of mechanical cleaning equipmentshould be done upon installation and then weekly(preferably daily) and recordedNot doneDone on installation but notmonitored subsequentlyDone on installation and monitoredwith documentation weekly/dailyQuestion 10:Appropriate manual and mechanical rinsingmethods are understood and are done accordingto manufacturer’s instructionsStaffs are unaware of theseSome understood and compliedAll understood and compliedQuestion 11:Cleaning agent (enzymatic cleaner) shouldbe compatible with the medical device tobe cleanedNo evidence of compatibilitySome are compatibleAll are compatibleQuestion 12:Chemical for disinfectants and terminal sterilisationare used according to manufacturer’s instructionsNot donePartial complianceFull complianceQuestion 13:Ultrasonic cleaner solution is changed at specifiedfrequency or sooner if neededNo frequency setFrequency set but not compliedFrequency set and compliedSECTION B: CLEANING AND DECONTAMINATION PROCESSES continues 6
APSIC CSSD Center of Excellence Program Audit ChecklistSECTION B:Cleaning and Decontamination Processes (continued)Question 14:Final rinse in washer disinfector is donewith treated water (deionized, distilled,or RO water)Final rinse with untreated waterFinal rinse with treated waterTOTAL:SECTION B:Cleaning andDecontaminationProcesses0 / 180 pointsMANDATORY ITEMS MARKED:0 / 80 (4 items)I completed all questions in this sectionespecially the MANDATORY (highlighted) items.Yes7 Return to Table of ContentsNoProceed to Next Section
APSIC CSSD Center of Excellence Program Audit ChecklistSECTION C:Instrumentation Inspection, Preparation and PackagingInstrument inspectionQuestion 1:Ensure instruments are cleaned and driedbefore packagingNot evidentPartial complianceFull complianceQuestion 2:Inspect instruments for flaws or damage.Check for rust, pitting, corrosion, burrs, nicks,cracks, chipping of plated surfaces. Lightedmagnifying glass available for instrumentinspection.Question 3:Cleaning verification by users should includevisual inspection combined with otherverification methods (ATP) that allowassessment of instrument surfacesand channelQuestion 4:Instruments:– Cutting edges are sharp– Moving parts move freely, without sticking– Instruments needing repair are taken outof service for repair or replacementQuestion 5:Follow MDMs instructions for instrumentsrequiring lubrication after cleaning or priorto sterilisationLighted magnifying glassnot availableOccasional inspection withlighted magnifying glass doneInspection done with lightedmagnifying glass for all instrumentsOnly visual inspectionOther verification methods includedbut without fixed schedule and planOther verification method includedwith fixed schedule and planNot evidentDone occasionallyDone all the timeNot evidentDone occasionallyDone all the timeSECTION C: INSTRUMENTATION INSPECTION, PREPARATION AND PACKAGING continues 8
APSIC CSSD Center of Excellence Program Audit ChecklistSECTION C:Instrumentation Inspection, Preparation and Packaging (continued)Preparation and assemblyQuestion 6:Delicate/sharp instruments are protected whilebeing handled/assembled for sterilisation (mayuse special holders, tip guards, or foam sleeves)– Tip protectors should be sterilant-permeableQuestion 7:Instruments that open (e.g. scissors, haemostats)are held in unlocked, open positionsNot evidentDone occasionallyDone all the timeNot evidentDone occasionallyDone all the timeQuestion 8:Multi-part instruments are disassembledprior to sterilisation, ensuring all parts areeasily accessed for aseptic assemblyNot evidentDone occasionallyDone all the timeQuestion 9:Lumened devices:– Remove stylets/plugs, such as catheters,needles, tubings– Moistening of the lumen may berecommended; consult device manufacturerQuestion 10:Complex instruments (eg, air-powered,endoscopes, having lumens or channels)are prepared according to written IFU fromdevice manufacturerQuestion 11:Non-linting absorbent material may be placedin trays to help facilitate drying. Tray liners orother absorbent materials may be used toalleviate drying problems.Not evidentDone occasionallyDone all the timeNot evidentDone occasionallyDone all the timeNot evidentDone occasionallyDone all the timeSECTION C: INSTRUMENTATION INSPECTION, PREPARATION AND PACKAGING: Preparation and assembly continues 9
APSIC CSSD Center of Excellence Program Audit ChecklistSECTION C:Instrumentation Inspection, Preparation and Packaging (continued)Preparation and assembly (continued)Question 12:Basins:– Graduated basins should differ in diameterby one inch– Use non-linting absorbent material betweennested basins– Wrapped basin sets should not exceed 3kg (7 lbs)Question 13:Containerized instrument sets do notexceed 11kg (25 lbs)Not evidentDone occasionallyDone all the timeNot evidentOccasionally complyFull compliance all the timePackagingQuestion 14:Packaging materials are held for a min. of 2 hrs.prior to use at room temp (21 F-24 F) and at arelative humidity ranging from 30-60%. [This isneeded to permit steam sterilisation and preventsuperheating.]Question 15:Packaging materials are examined regularlyfor defects (i.e. holes, warn spots, stains)Not evidentOne factor complied withBoth factors complied withNot evidentDone occasionallyDone all the timeQuestion 16:Wrappers should be kept snug, but not wrappedtoo tightly or strike-through could occurNot evidentDone occasionallyDone all the timeQuestion 17:Paper/plastic pouches:– Labeling is done on plastic side only– Double peel pouch only if pouch isvalidated for this use10No labelingLabeling but not on plastic sideLabeling on plastic sideSECTION C: INSTRUMENTATION INSPECTION, PREPARATION AND PACKAGING: Packaging continues
APSIC CSSD Center of Excellence Program Audit ChecklistSECTION C:Instrumentation Inspection, Preparation and Packaging (continued)Packaging (continued)Question 18:Wrapped packs:– Write only on indicator tape or affixed labelsNo labelingLabeling done inappropriatelyLabeling on indicator tape oraffixed labelsQuestion 19:Perforated, wire-mesh-bottom trays, and rigidorganizing trays are inspected prior to each useto ensure there are no sharp edges, nicks, orloose wire-meshQuestion 20:Tape (other than sterilisation indicator tape)should not be used to secure packages, norshould safety pins, ropes, paper clips, staples,or other sharp objectsQuestion 21:Validation test to be done for heat sealerat set frequencyNot evidentDone occasionallyDone all the timeNot evidentDone occasionallyDone all the timeNot doneFrequency set but not followedFrequency set and followedTOTAL:SECTION C:InstrumentationInspection,Preparationand Packaging0 / 260 pointsMANDATORY ITEMS MARKED:0 / 100 (5 items)I completed all questions in this sectionespecially the MANDATORY (highlighted) items.Yes11 Return to Table of ContentsNoProceed to Next Section
APSIC CSSD Center of Excellence Program Audit ChecklistSECTION D:Sterilisation and MonitoringFollow manufacturers’ guidelinesQuestion 1:Steriliser manufacturers:– Written instructions for cycle parametersare availableNot availableSome are availableAvailable for all sterilisersQuestion 2:Rigid container manufacturers:– Instructions for cycle parametersare followedNot evidentDone occasionallyDone all the timeQuestion 3:Medical device manufacturers:– Written instructions for sterilisation cycleparameters are available/accessible for itemsto be sterilised, including loaner setsLoading the steriliserNot availableAvailable but not easily accessibleAvailable and easily accessible(follow steriliser manufacturers’ written instructions)Question 4:Group together similar items requiring samecycle parametersNot evidentDone occasionallyDone all the timeQuestion 5:Steriliser cart:–A llow space between packs–D o not overload–P ackages should not touch chamber wallsNot evidentOverloading seen occasionallyComplied with all the timeSECTION D: STERILISATION AND MONITORING: Loading the steriliser continues 12
APSIC CSSD Center of Excellence Program Audit ChecklistSECTION D:Sterilisation and Monitoring (continued)Loading the sterilizer (continued)Question 6:Mixed loads:– Place metal items on the loading cart belowtextiles and paper-plastic pouches (to preventcondensate from dripping onto lower packs)Question 7:Solid-bottom pans, bowls, and trays are tiltedon edge and oriented in the same directionNot evidentDone occasionallyDone all the timeNot evidentDone occasionallyDone all the timeQuestion 8: Paper-plastic pouches:– Use baskets to facilitate placing poucheson edgeNot evidentDone occasionallyDone all the timeQuestion 9:Rigid containers:– Stacking could interfere with air evacuation;follow container’s manufacturer’s instructionsNot evidentDone occasionallyDone all the timeUnloading the steriliserQuestion 10:Open steriliser door properly– Door may be opened slightly at the endof the cycle (for some time) prior toremoving the loadQuestion 11:Load contents:–T here should be no visible signs of liquid, orwater droplets. (Wet items are consideredcontaminated even if not touched.)Not evidentDone occasionallyDone all the timeNot evidentWetness seen occasionallyDry for all itemsSECTION D: STERILISATION AND MONITORING: Unloading the steriliser continues 13
APSIC CSSD Center of Excellence Program Audit ChecklistSECTION D:Sterilisation and Monitoring (continued)Unloading the sterilizer (continued)Question 12:Sterilised items remain on the cart to cool fora minimum of 30 minutes, and
Audit Checklist Please make sure to answer ALL questions to obtain a more accurate audit. Highlighted questions are MANDATORY by APSIC GUIDELINES! Audit Checklist Table of Contents 2. 3 Not removed Removed sometimes Removed all the time Question 1: Reusable items separated from waste at point of use Not separated Partial separation Clear separation Question 2: Contaminated disposable